- Design Approaches
- Posted
All systems go
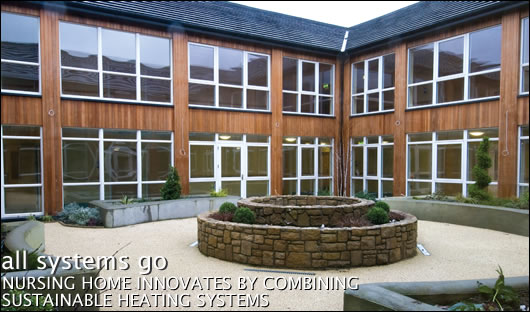
Some buildings, by their nature, tend to have larger energy requirements. Occupied around the clock, with occupants who feel the cold, nursing homes are a case in point. John Hearne visited a north Dublin building where a range of different sustainable technologies operate in tandem to deliver the residents’ heating and hot water requirementsA new nursing home in Castleknock, County Dublin combines a solar system, air to water heat pumps, a micro-CHP unit and condensing gas boilers to deliver one of the most cost-effective heating and hot water solutions for a facility of this kind you’re ever likely to see. Energy savings in the order of 40 per cent are expected from a system whose ingenuity lies not in any one technology but in a minutely engineered synthesis of four separate systems.
Elm Green Nursing Home is a three storey, 100-bed facility which includes 15 staff apartments and 27 independent living units linked by a glazed corridor to the main structure. The building itself, though it incorporates a reasonably beefed-up insulation spec, is of largely conventional construction. A steel frame on the ground floor supports a concrete deck on the first floor – this to facilitate underfloor heating – while all other structures are timber frame. A U-value in the walls of 0.25W/m2K is achieved through a combination of rigid polyurethane and fibreglass, while a figure of 0.16W/m2K in the roofs comes courtesy of 350mm of cross-laid rock wool. There’s also low energy lighting throughout. Billy Malone of BEM Electrical, who designed the lighting specification, explains that all internal lights are 2D high frequency fittings, varying in intensity between 16W and 38W. Motion sensors control operation in circulation areas. Externally, 100W fittings are controlled through photocells and timeclocks.
The real story however is in the plant-room, and a heating system that was designed and built by mechanical services engineer, Paul Lynch. “You’ve a solar heating system, you’ve a micro-CHP, you’ve gas boilers and you’ve six heat-pumps, and they’re all integrated together,” he explains. “Basically, we have certain criteria we have to meet. We have to heat the nursing home with underfloor heating, we’ve to heat the 27 apartments and we have to heat the staff quarters, so we have a substantial heat requirement.” The bulk of that heat is carried to occupants via 4,700m2 of underfloor heating in the ground and first floor slabs of the main building, supplied by long-established heating technology company Henco Ireland, a Blackrock-based company who also offer renewable energy systems. The secondary heat load to the apartments and staff quarters is carried by radiators. Each of these solutions was primarily chosen to reflect the particular kind of use to which each space is put, Lynch explains. “I put radiators into the staff quarters, for a start because it’s timber frame construction, and it would have been a bit difficult at the time to put in underfloor heating, but it’s mainly from a response point of view, in the sense that, the staff are not going to be up there all day. What you really want is when they come in that they can flick the switch, or set the timer. There’s a time-clock for each apartment, all the rads are thermostatically controlled and there’s also a valve in the plant room that’s weather compensated.”
The usage profile of the nursing home itself also dictated the combination of underfloor and heat-pumps. “We’re driving the underfloor heating all the time through the heat pumps, but we’re only bringing it up to about 30 degrees to maximise the COP (estimated at between 3.5 and 4 at that temperature). And it’s efficient because the building is a 365 day building,” Lynch says. “You never have a peak demand; there’s a constant call for heat. This solution is ideal for the likes of prisons, hospitals and nursing homes. Normally, when we’re designing a system, say an office or a warehouse, you have to have huge boiler capacity so that on a Monday morning, you can bring the place up to temperature quickly, but here, you don’t need the same kilowatt capacity because demand is flat.” The heating load is demand led. Thermostats in each of the zones in the nursing home call for heat as required, and within the plant room, the system responds incrementally, calling on more heating and circulation power as it’s needed. The six 28kW Dimplex heat-pumps, which were supplied by Geothermal Solar in Kildare, operate in cascade, minimising current drawdown. A series of inverter or variable speed pumps in the plant-room each control four underfloor heating manifolds. As zones heat up and require less heat to maintain temperature, each manifold shuts down, sending a signal back to the inverter pump that less power is now necessary. In this way, power scales up and down in smaller increments, giving greater control over heat distribution and power output. “Your normal scenario in a heating situation,” says Lynch, “is your pump is driving all the time. If you have 100 radiators, what happens is, as the rads shut down, the pump is still cranking as hard as ever, so you end up actually getting noise in your pipes. Here, as the building comes up to temperature, the pumps go to sleep, they crank back down to the minimum flow rate, and as demand flow rate increases, they drive up.”
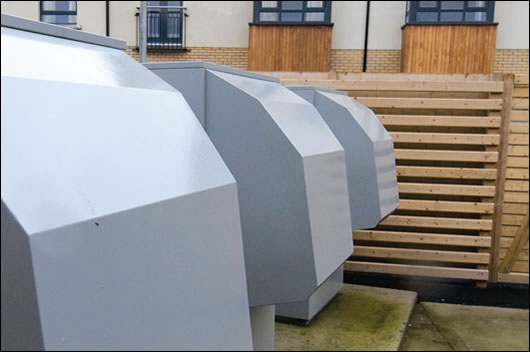
The courtyard of Elm Green, a new nursing home in Castleknock which combines heat pumps
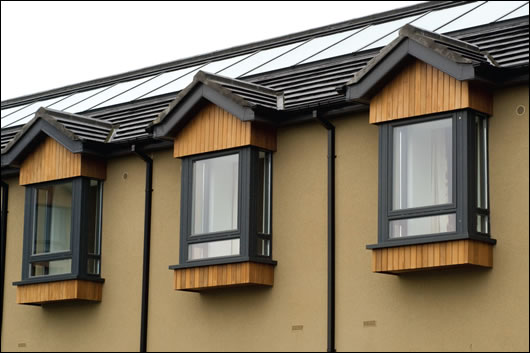
Solar panels
In a nursing home situation, good backup is vital. In Elm Green, if the heat-pumps go into fault mode, the first line of defense is the micro-CHP unit, followed by the condensing gas boilers. Combined heat and power, or cogeneration, is the simultaneous generation of heat and power from the same piece of equipment. In much the same way as a car’s fan heater captures heat from the engine, CHP captures heat that is usually wasted in the power generation process and makes use of it to heat water, resulting in very high running efficiencies and energy savings. “There are sensors on the heat-pumps and on the heat-pump controllers,” says Lynch. “If they sense the temperature isn’t what it should be, an alarm rings in the software, it makes a decision and opens a solenoid valve, then the CHP and the boilers will start dumping low pressure hot water into the heat-pump water.” Because the heat-pumps operate at low temperature and boilers operate at high temperature, Lynch has split the system to effectively provide two heating systems in one, with 80 degree water on one side and 40 degree water on the other. The CHP system takes precedence over the condensing gas boilers, but if it cannot bring the spaces to temperature, the controls system will automatically call for help from the boilers, which are also set in cascade and will come on in sequence as required.
These are Heatmaster HM85TC units, capable of condensing in both space and hot water modes. “Each modulates between 16.5kW and 85kW,” Derek Fitzpatrick of supplier Pumpwise explains. “So they can ramp up and down, and will fire at different modes depending on the output required.”
While the heat-pumps take the lead in providing space heating to the underfloor system, the CHP is first called on to provide heat for the radiators in the apartments and staff quarters. Meanwhile, the solar system takes priority on hot water. Also supplied by Geothermal Solar, the twenty flat plate panels are mounted on the front roof of the building to take full advantage of the southerly orientation. Covering a surface area of 40m2, the panels deliver a combined output of 36kW. “In the summer time,” says Lynch, “the system takes about four hours to bring 2,500l of water up to 60 degrees.”
The panels feed a pre-heat tank in the plant room, with the CHP again taking the back-up role when the solar can’t provide what’s required and the condensing gas boilers as before providing the last line of defence. On the cold and cloudy January day we visited, the solar panels were only delivering 16 degrees to the tank, prompting a call on the CHP unit. In order to eliminate the risk of legionella, the water must be kept at 60 degrees. This water is routed from the preheat tank through the gas boilers, but if that minimum has been reached in the tank, the water simply passes through without firing the boilers.
The micro-CHP is a Dachs system made by Senertec in Germany and supplied and installed in Ireland by Kinviro. In Elm Green, the system is running as part of SEI’s ongoing micro-CHP pilot, and all aspects of its performance are being monitored at five second intervals. As part of that pilot, the unit has also been fitted with an external heat exchanger which preheats the water going into the system using any residual exhaust heat. “After we pick up the residual heat from the exhaust,” Frank Daly of Kinviro explains, “it goes into the generator and we collect the heat there.” Most big generators are air cooled, blowing off the heat as it’s generated, but the Dachs system is water cooled. “The water comes out of the alternator, then it goes into the guts of the engine where it picks up heat from the lube oil and the engine jacket, then from there, it goes back out through the exhaust gas heat exchanger and the whole process starts again.” By collecting residual heat from all parts of the unit, the system achieves an efficiency rating in the order of 99 per cent. “It gives 5.5kW of electrical power,” says Daly. “Though it doesn’t sound like a lot, it would look after the bulk of the electricity requirements of the boiler house, which is the guts of the electrical load of the building.” This power feeds seamlessly into the distribution board of the building, thereby reducing the facility’s reliance on mains electricity. “In an application like this it would be very rare that the base-load would drop below the output of the micro-CHP. If it did, what would happen is this would continue to run but you’d send surplus power out onto the grid.” In addition to the 5.5kW of electrical power, the system provides between 12.5kW and 14.8kW of thermal output.
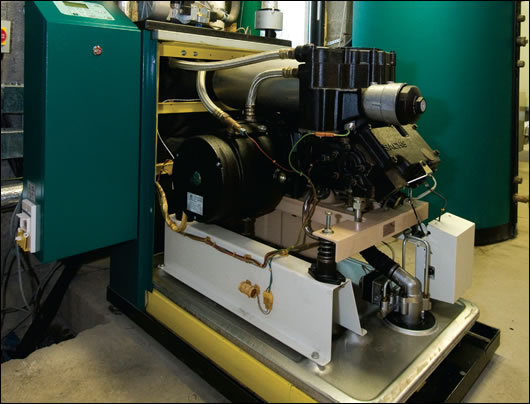
A micro-CHP unit – seen here with its case off
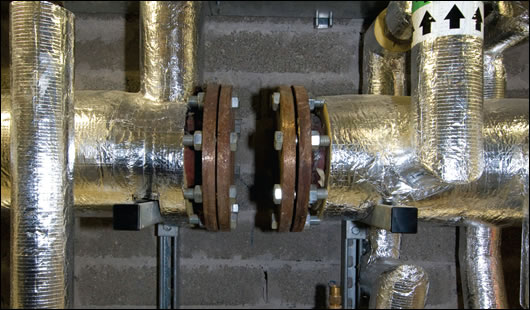
The heating system is split to effectively provide two systems in one, with 40 degree water available in one section (to the left) and 80 degree water in the other (to the right)
The administration involved in micro-CHP installations has been substantially simplified in recent years. At one point, the ESB required a highly detailed and lengthy compliance process before it would sanction the connection of a unit like that in Elm Green to the building’s distribution board. “It’s been vastly improved,” says Frank Daly. “They’ve really pulled out the stops there. As long as ESB is satisfied the technology is certified as being compliant with their grid connection criteria, it’s a simple inform and fit procedure; basically a single page form where we tell them what the technology is and where it’s installed.” The unit is also much quieter than you would expect from a single cylinder, four stroke engine. Set on springs and surrounded by a padded cabinet, it produces 52 decibels at one metre – by comparison, speech measures around 50 dBA. The system feeds heat directly to a buffer tank, using a thermostatic pump to prevent the ingress of cold water. “In times of low thermal demand you can store the heat in there. In terms of high thermal demand there’s 750l of hot water waiting.”
When it comes to CHP, getting the sizing right is vital. “The Dachs CHP is used to do the base-load,” says Daly, “which is the thermal demand that’s there year round, and then the boilers kick in to meet any load above that. You should always size a CHP for the base-load. Over-sizing a CHP can result in wasted heat because you have to blow off the heat to keep it running…Any nursing home that has 30 beds or more should consider a micro-CHP because it’s ideally suited given the constant demand for heating and hot water. There’s always someone on duty and the lights are always on, so there’s always an electrical demand as well.”
The importance of sizing is also something that Niall Leonard of TR Controls is keen to emphasise. He designed and programmed the plant-room’s highly sophisticated controls system. “If the CHP was too big or the solar or the boilers were too small, the whole thing would degenerate into a mess. To get the CHP to run 24/7 with as little extra fuel as possible is a fine art. It’s the same with the solar and the gas; size is everything, size matters. And we’re not wasting money on big capital outlay. There are six heat-pumps there and they’re sized to deliver just what we want most of the year. If they were too big, there would have been too much capital outlay. If they were too small we’d have to supplement them with the boiler. Sizing on everything is critical.”
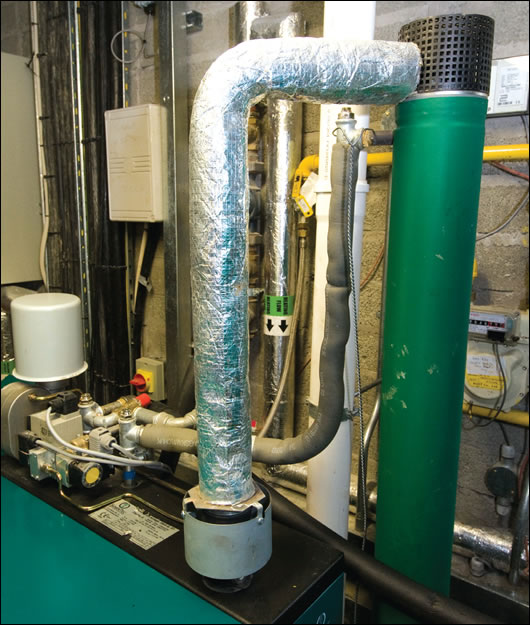
A CHP unit has also been fitted with an external heat exchanger which preheats the water going into the system
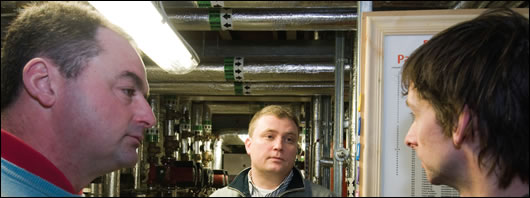
Mechanical services engineer Paul Lynch and Frank Daly of Kinviro discussing the heating system with John Hearne
As is the controls system that brings the technologies together. Built and supplied by Cylon Controls, and programmed by TR Controls, the system takes four disparate pieces of kit and automates their operation to optimise the building’s energy demand. “We manufacture the hardware and the software,” says Stephen Carroll of Cylon Controls, “but it comes out in a format that it must be told what to do.” This is Niall Leonard’s job. He explains that the system itself is comprised of a series of intelligent control devices which take inputs from a series of sensors installed at key points throughout the heating system. “I sat down with Paul and we looked at what he wanted to do in terms of the heating and the systems…We went through the various scenarios and built up a detailed description of what we wanted to do, and that lead us into what points we wanted to monitor, so we’ve a sensor on the solar tank, we’ve a sensor on this header, a sensor on that header and so on, then each sensor was mapped onto a drawing. Next we write the logic…If this value is greater than that, add it to that, plus that, minus that, turn on that: it’s pure logic. It starts out as completely empty, free architecture, then if you can describe it we can put it in.” Commissioning then becomes an elaborate process of working through every possible mechanical scenario to establish that the system is working as it should. “One of the differences in this site,” says Stephen Carroll, “is that Paul and Niall have sat down and really worked the system, whereas traditionally you get a main contractor building a building for an unidentified end user, and this type of equipment is put in as a generic specification. But it’s a kind of a fit-and-forget scenario…This is an example of where everything is maximised and everything is optimised.”
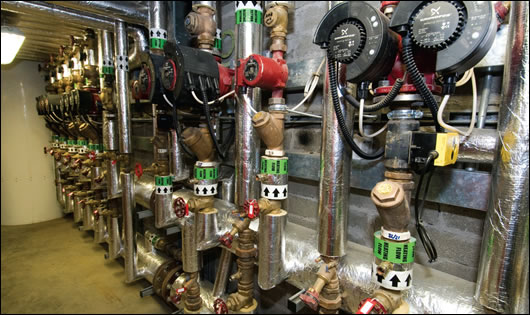
A view of some of the system’s pumps and pipes, with the preheat tank in the background
Once the sensors and logic circuits have been set up, the next stage is to develop an onscreen graphical representation of the entire system in real time. TR Controls take pictures of the system in the plant-room, bring them home and develop a windows based operational interface which fully describes everything taking place within the system. The controls system is then networked into the building, so that a PC can be plugged in anywhere and the system accessed and viewed. The layout is highly intuitive, with graphical representations of everything: the boilers, heat pumps, CHP and solar the headers and manifolds, complete with temperature readings. You can follow the energy trail through the system, click on the different heating zones and monitor thermostats. “It’s meant to be an automatic system.” says Leonard. “That means that we have to design it so that no manual intervention is necessary. We should be able to lock this door and go away knowing that the heating is going to come on at the required time to the required temperature.” If there’s a problem, an SMS or an email detailing the specific nature of that problem is sent automatically to the person responsible. Cylon Controls can go further than this, is the client so demands, by offering a remotely managed option, whereby the building will be managed centrally by your offsite energy arrangement bureau, thus ensuring all plant and equipment controlled by the BMS is managed and optimised by trained personnel.
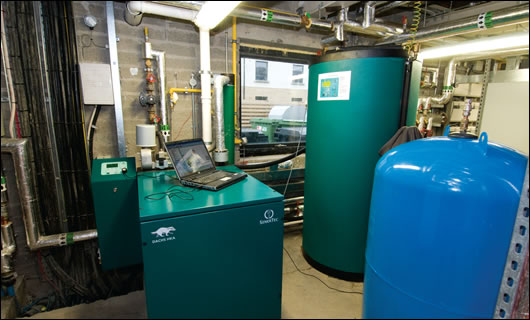
The CHP unit with the external casing fitted
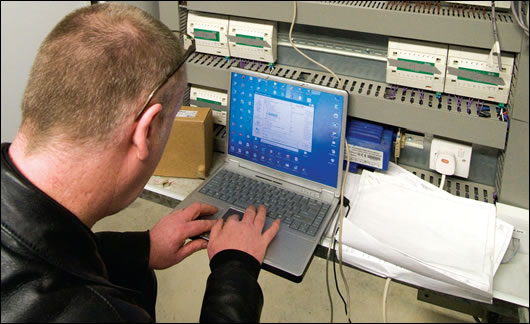
Niall Leonard of TR Controls programming the crucially important controls system
Though the heating system in Elm Green has the potential to deliver huge savings on traditional heating systems, it takes the controls system to realise that potential. Take the hot water for example. Under regulations, this must be delivered in the tap to the end user at 55 degrees. On the day we visited, the onscreen graphic showed that the water in the taps stood at 55.8 degrees, just 0.8 degrees above the minimum. “The control is that tight,” says Leonard. “For every degree we’re out, we’re wasting money. We have to spend the money it costs to get 55 degrees, but 56 is a waste.”
Meters on the systems and subsystems are currently a work in progress. Once the base-load is established, the building manager can experiment with temperatures and monitor the impact on comfort and fuel usage. While the system is designed to work without manual intervention, some monitoring is necessary. “Energy usage in buildings typically creeps up over the years,” says Niall Leonard. “People get sloppy and plant gets left on, or timers get turned off. The building manager has to constantly refer back to his baseline, saying ‘this is what it was. I should be able to hold it to this’. We do a lot of maintenance and maintenance basically means going in and putting it the way it was from day one, when it was new.”
As the building works through its first winter and occupancy begins to rise, that baseline is slowly being established. Further improvements are also being considered. Heat recovery in the laundry room is in the pipeline, while Lynch is also looking at the possibility of installing a small heat-pump in the plant room to capture residual heat there. “We’re aiming to get energy usage as low as it can go,” he says. “It’s very much a work in progress.”
Selected project details
Developer/contractor: KMD Properties
M&E design/build: Paul Lynch Mechanical Services
Electrical contractor: BEM Electrical
Build system: Kingspan Century
Additional insulation: Fingal Insulations
Micro-CHP: Kinviro
Heat pumps & solar: Geothermal Solar
Underfloor heating: Henco Ireland
Condensing boilers: Pumpwise
BMS: Cylon Controls
BMS programming: TR Controls
- Articles
- Design Approaches
- All systems go
- Heating
- underfloor
- Dachs CHP
- micro chp
- condensing gas boiler
Related items
-
Ecomerchant now stocking Herschel Infrared heating products
-
Panasonic welcomes new Green Homes Grant
-
Steeply sustainable - Low carbon passive design wonder on impossible Cork site
-
Focus on whole build systems, not products - NBT
-
Marc O'Riain: The golden age of solar water heating
-
International - Issue 29
-
Internet of Things dominates ISH 2019
-
Passive Wexford bungalow with a hint of the exotic
-
Heat Merchants announces €4m expansion, 75 jobs & CO2 pledge
-
The House of Tomorrow, 1933
-
1948: The Dover Sun House
-
The dazzling Dalkey home with a hidden agenda