- Passive Housing
- Posted
Restoring order
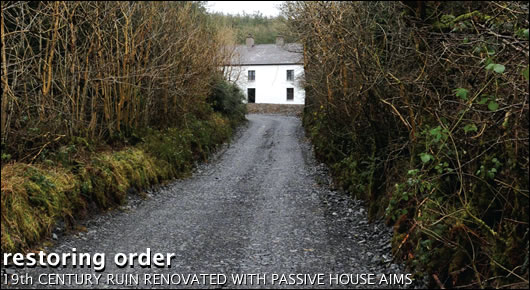
Turning a ruined farm house into a usable dwelling has been a dream for decades, but can an age-old structure really be brought-up to the cutting edge of energy efficiency? Architect Frank Cooney has found a way with a ruin in Cavan currently undergoing renovation. Jason Walsh visited the site to find out more.
The Irish countryside is littered with derelict houses, tumbledown ruins whose destiny seems to be to slowly decay until all that is left is a pile of rubble. It doesn’t have to be so, as an architect in County Cavan has proved by turning an aging, roofless stone ruin into an eco-house that gives even the most cutting-edge of sustainable new builds a run for their money.
Starting again
A foundation-less, two-storey detached rubble stone building in Bailieborough, County Cavan does sound like an unlikely candidate for the description ‘energy efficient house’. Picturesque? Certainly. Efficient? Hardly. However, through the use of computer modelling, a desire to reduce embodied energy and make use of natural materials, along with attention to detail on the building fabric and primary energy system, that is just what has been achieved – a re-build that has turned a wreck into a home.
Owned by Frank Cooney and Patricia McCaffrey, the three-bedroom building is to become a family home. Why would an architect re-build a ruin? In part to prove a point, that any building can be significantly improved, but also because of a belief that traditional buildings have a lot to teach us – and plenty to offer us too.
Cooney, who worked on the design on the early 1990s of the Green Building in Dublin’s Temple Bar, has long felt that an environmentally-sound building should start with the simple things: get the fabric right and the rest will follow.
In the case of this house, however, Cooney also looked into traditional settlement patterns: why were small-holdings laid out the way they were? He explains that houses were often oriented east-west to maximise heat-gain and avoid overheating, while shelter was provided by trees and the ambient outdoor temperature moderated by creating a courtyard. Cooney was able to make use of all of these existing features while also applying what he felt was appropriate technology to bring this 19th century house well beyond modern building regulations.
The first engineers that Cooney contacted, who were not chosen to work on the job, saw the problem of making the house habitable in a purely technological fashion: “They suggested a deep bore hole and heat pump,” said Cooney. “We said, ‘first let’s see how far we can push the building – we have an east-west orientation, a sheltered courtyard and a thermally massive structure.’”
For Cooney, however, it’s all about the building fabric: “We said, ‘if we can achieve a [wall] U-value of 0.15 what does that do for us?’ With really high insulation levels we can keep the heat we gain. Then we looked at an air-tightness membrane, and we looked at blocking the chimney. Initially we proposed supply-air windows but moved away from those – they weren’t doing a lot for us.
“We looked at passive solar gain, having a large window on the southern elevation, so we modelled what that would do for us. We found that we were getting fifteen to sixteen degrees Celsius in summer and autumn without heating, so we proceeded from there.
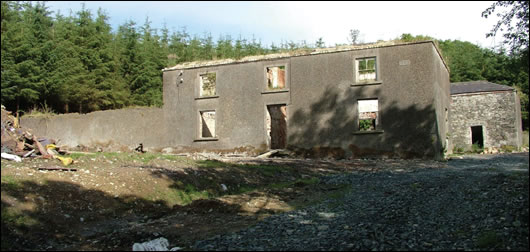
The 19th century ruin which architect Frank Cooney chose to transform into a modern eco house
High levels of insulation are key to the house’s design: “For 300 days of the year, the house’s temperature doesn’t drop below fourteen degrees Celsius [in computer modelling],” he said.
Knowing that the house already had thermal mass in the form of massive stone walls, Cooney sought out a way of beefing-up the thermal performance. The answer came in the form of the house’s primary insulation material – Brillux supplied by Greenspan Products.
Brillux is an exterior insulation finish system – insulation that is fitted to the exterior of a building.
“We recommend external insulation for [both] new-build and old-build,” said Greenspan’s managing director Mike Cregan. “If you’re building a house, hotel or apartment block using masonry the most effective way of insulating that building is on the outside. If you insulate on the inside not only do you reduce floor-space, but you probably will not achieve anything close to the U-value that you will with external insulation. You also run the risk of condensation occurring behind your insulation, within the wall. External insulation is the more efficient way of insulating – you stop the cold and damp getting in to the wall in the first place. This creates a warm wall effect within the building. Also, external insulation is probably the only way of completely eliminating cold bridging in a building”.
According to Cregan, the typical consumer is not yet aware of the benefits – or possibly even the existence – of external wall insulation: “People should be made aware of the possibility – they don't know about it, they're just dry-lining. Because you’re working on the outside you can put more insulation on. You can bring a house from 60–70 years ago up to modern day standards and beyond,” he said. “It also has the advantage of causing no disruption within the building. For instance, if you dry-line, not only do you lose space, but your home becomes a construction site, and you have to factor in the extra costs of additional trades for rewiring electrics, moving radiators and skirting, and so on”.
On the exterior of the house is a lime render. The lime was supplied by County Carlow’s Tradtional Lime Company: “Our main business was recycled and traditional build materials but drifted into lime and mortars for conservations, restorations and eco-building,” said the firm’s Ed Byrne. “Generally traditional hydraulic lime was always used for building and external renders. Internally it's not really important which is used, hydraulic or non-hydraulic, though non-hydraulic has a much slower setting time.”
According to Byrne, one of the key advantages of hydraulic lime renders is breathability: “In a traditional house you don't have a cavity wall so you need breathability. Hydraulic lime is the original intelligent membrane, it resists the ingress of water but is totally breathable. Water comes into a house as water but it goes out as vapour. It's resistant to water but vapour permeable.”

On the exterior of the house is a lime render, which improves the breathability of the building
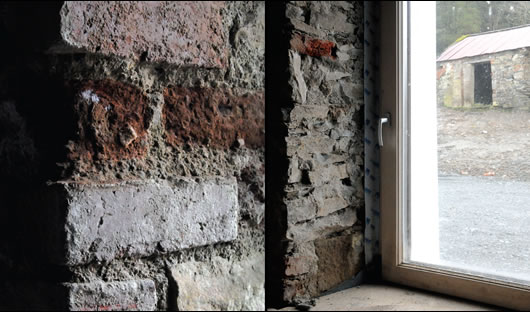
(left) The large stone walls of the house provide good thermal mass; (right) the house’s windows are all triple-glazed units supplied by Optiwin
For Byrne, not only does this meet today’s needs, but it also offers time-honoured guarantees that may not be available with other products: “One of the problems I find with intelligent membranes is: they work well, but I would wonder if they continue to work as well after long periods of time?”
The house also has many additional features, each designed to contribute to reducing its energy footprint, from Eco-joists that allow services to travel without interruption to the building fabric, recycled slates used for the roof, a reed bed to naturally process wastewater, a simple passive stack effect between the main hallway downstairs and the upstairs landing, warm roof insulation and of course, good glazing: the house’s windows are triple-glazed units from Optiwin achieving a U-value of 0.8 W/m2 K and, overall, the house achieves an A2 building energy rating (BER) and is built to passive house standards: “It’s the first re-build we’re aware of in Ireland that is being done to both passive house and A2 BER standards,” said Cooney.
The roof consists of slates externally on top of a breathable felt, over-sized rafters filled with 300 millimeters of rockwool insulation, an Intello air-tightness membrane from Ecological Building Systems and an insulated board from Gypsum Industries.
Aside from the insulation, air-tightness was a key issue. Cooney is happy with the results: “Results from Ecological Building Systems, and this is without the concrete floor being fitted yet, show an air permeability of two [2m3/hr/m2 at 50Pa]. Current building regulations call for a maximum of ten.”
A rainwater harvesting system is also planned, but has not as yet been fitted.
Work on the re-build commenced in October 2007. For main contractor, Patsy Carolan of Carolan Construction much was new on the job: “A lot more work was involved – it was certainly harder to do. It would be slower than a new build and you have to sequence it differently,” he said.
According to Cooney, when it came to heating systems, the decision was easy to make given enough information: “Our computer models were doing well for us having decided to optimise primary heat. We looked at solar for hot water because we knew it worked well. We found that in January and February we had our biggest heating demand – eleven kilowatts of energy, five for space heating and six for hot water. We asked how that compares with a standard two to three bedroom house – those have 20 kilowatt boilers.
“Affordability was an issue,” said Cooney. “I don’t like the word ‘payback’– my idea is to make eco-architecture attractive to the public so we need to make it financially sensible. We looked at wood pellet and wood chip boilers, we looked at heat pumps, rejecting them [heat pumps] because of the use of electrical energy. We were concerned about wood pellet because of the technology and the cost of the fuel. We looked at a deep bore hole and eliminated it on the basis of capital cost.”
In the end, the house’s energy demands were met in an innovative way. The principle contributor to both space and water heating is solar energy: “The main thing we did was put in 12.5 square metres of solar panels,” said Joe Martin of Solar Energy North East.
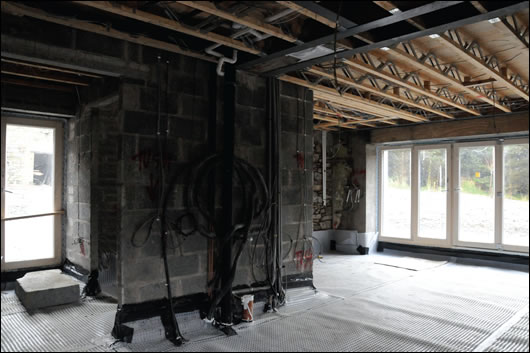
Eco-joists were installed to allow services to travel without interruption to the building fabric
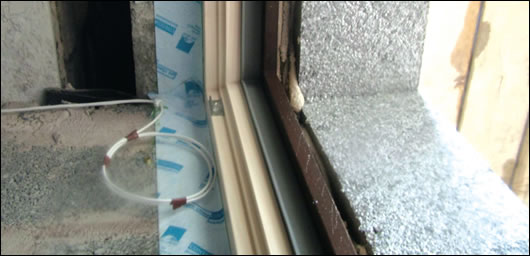
External insulation was fitted to the walls to dramatically increase the thermal performance
The solar collectors Solar Energy North East supplied are flat plates units manufactured by German company MP-Tech, and distributed in Ireland by solar pioneers Solaris through their network or partners, of which Solar Energy North East is one.
Martin is adamant that flat plate collectors are underrated and should be specified more frequently: “I have a strong preference for flat plates,” he said. “In my view the advantage of tubes is oversold.”
In Martin’s view the variation in quality with tubes is much bigger than that with flat plates and the pros and cons of the two systems make them equal: “Metre-for-metre the tube wins, but system-for-system the two systems are equal. A good quality tube has a twelve to fifteen year life expectancy whereas a flat plate has a life of 40 years without maintenance.
“Tubes are vulnerable to breakage – any impact is magnified because of the vacuum. You also have a disposal issue,” he said.
Martin says he does supply evacuated tube systems and recommends them for particular circumstances: “Tubes make sense when space is a factor.”
The heat from the solar panels is used to heat water – a thousand litres of water – which is then used to meet domestic hot water requirements as well as feed through the underfloor heating system.
The bath Cooney and McCaffrey chose is a 400 litre ceramic unit so without such a large capacity it would be impossible to fill. What is remarkable is that the hot water system has been designed to do just this without the need to introduce an electrical immersion heater or other source of heating.
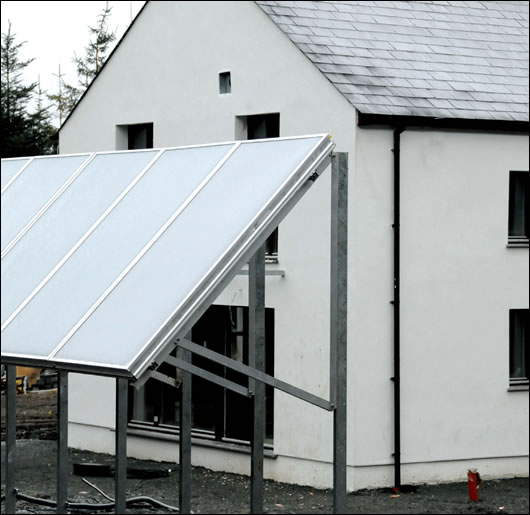
The principle contributor to space and water heating is solar energy, with 12.5 square metres of flat plate solar panels installed

the Enervent HRV unit which will be used to ventilate and distribute heat evenly around the building
This thousand litres of water is stored in a giant buffer tank on the first floor and is circulated through the house’s underfloor heating system. A freshwater heat exchanger allows clean water to be used for domestic hot water at a rate of 40 litres per minute.
Martin explained how he designed the system: “If we were to do hot water only, we could say that three panels would cater for four people, as a rule of thumb. With this house, which might not be in constant use, I felt that using solar for domestic hot water alone wasn’t the best use so we decided to use the solar to supplement the space heating. This meant doubling the solar collector area but this doesn’t double the cost, adding around 30 per cent.”
In addition to the solar, a 14.9 kilowatt Evolution II ‘thermo-chimney’ stove with a back-boiler, also supplied by Solaris, is to be located on the ground floor. “It’s very high efficiency,” said Martin, “85 per cent efficient.”
12.5 kilowatts of energy from the boiler are used to heat the water with the remainder going directly into the room. This low energy output directly into the space is by design, as direct radiant space heating is considered to be less desirable and less controllable than providing space heating through a buffer tank.
The stove’s primary fuel is unprocessed wood, sourced locally, though it can burn other fuels such as peat, if required.
The stove does not qualify as a ‘gasification’ system. Martin says that this is mostly an oversight in legislation: “In Germany the larger gasification boilers are not favoured by the government,” he said. “The thinking is that a 60 kilowatt boiler reduces the need for insulation [resulting in poorer houses and increased inefficiency].
“The stove, the solar and the insulation should all be working in concert,” he said. “Sustainable Energy Ireland recognises that we need to stop plumbers oversizing boilers.”
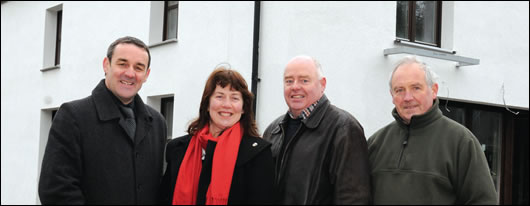
Frank Cooney, Patricia McCaffrey, Joe Martin and Patsy Carolan
The ‘cooler’ water at the bottom of the buffer tank is preheated by the solar coil. The water is then fully heated by the stove during the winter period and this water is then used for both the underfloor heating, and also to providing domestic hot water through the fresh water heat exchanger.
“The most efficient way to store energy is in water,” said Martin.
Finally, heat-recovery ventilation (HRV) is used to both distribute heat evenly throughout the building and ventilate. For this purpose, Solar Energy North East supplied an Enervent unit: “People effectively heat their houses with the back doors open – that’s what all of those ventilation pipes amount to.”
Whatever approach one takes to achieving sustainable architecture, there is no doubt that Cooney has proved that an old building is no excuse. If a tumbledown stone building can be made as remarkable as this building, surely there is an imperative to get to work on the rest of Ireland’s housing stock – most of which already has roofs and foundations and is easier to work with than this project.
Selected project details
Client: Frank Cooney & Patricia McCaffrey
Architect: Cooney Architects
Mechanical and electrical engineering: IN2 Engineering Design Partnership
Main contractor: Carolan Construction
Civil and structural engineering: Tim Murphy Structural Design
Mechanical contractor: Edward Carolan
External insulation and render: Greenspan Products
Solar and wood stove: Solar Energy North East
Lime renders: The Traditional Lime Company
Air-tightness products: Ecological Building Systems
HRV: Enervent Ireland
- Articles
- Passive Housing
- Restoring order
- embodied energy
- passive
- Brillux
- Greenspan
- lime
- Traditional Lime Company
- Gypsum
- evacuated tube
- solar panels
Related items
-
Solar panels to receive VAT drop in aim to boost uptake
-
Podcast: what we've learned from 20 years in green building mags
-
New embodied carbon rules for large London projects
-
Coasting home - Beautifully designed Hampshire home breezes past passive standard
-
Ecological brings Lime Green plasters to Ireland
-
Achieving NZEB event in Cork hears of embodied carbon plans
-
Diasen thermal lime plaster features on RTE renovation
-
Ecological take double honours at SEAI Energy Show
-
Material impacts
-
Ireland’s largest solar PV project completed in Kilkenny
-
Airtightness - the sleeping giant of energy efficiency
-
Striking London building catches the eye as well as the sun