Move on up
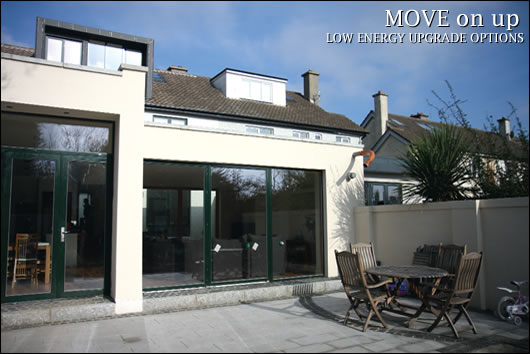
High energy prices and growing public eco awareness is leading to a situation where people are giving existing homes energy upgrades on an unprecedented scale. Two recently renovated houses in Dublin are at the extremes of how even the most difficult existing dwellings can be made greener, as Jason Walsh reveals.
In an ideal world we could all live in energy efficient homes and reap the benefits: lower bills, improvements in comfort and well-being and contributing to a greener society, but this vision does not reflect the reality of Irish housing today. Standards have clearly been improving in recent years and some new Irish homes are close to the European cutting edge, but that doesn’t tell the whole story.
Indeed, Construct Ireland regularly features newly-built houses constructed to the highest standards – excellent buildings, in many cases, and ones that make for ideal homes, but how many of us really live in passive houses or A-rated apartments? How many of us even live in new buildings at all? After all, so many of the improvements in energy use that we read about are predicated on building from scratch. There is an alternative, though: refurbishment.
At a time when the housing market is in severe decline it makes more sense than ever to refurbish rather than buy. Anyone who puts their house on the market right now is likely to be offered significantly less than they would just a year ago and, in some cases, may even find they have difficulty finding a buyer – a clear motivation for refurbishing.
Moreover, there just aren’t as many new houses as there have been. In a report issued in October 2007, the Central Bank estimated that 2008 would see 65,000 housing completions – a figure that is backed-up by the Economic and Social Research Institute (ERSI) think tank. This is by no means an insignificant number, but it certainly represents a steep decline from the 2006 peak of 93,419. The Construction Industry Federation (CIF), meanwhile, estimates an even lower figure of 45,000 for 2008. It is obvious that the construction industry is already nervous about the prospects for new build developments, something that is likely to be exacerbated by the so-called ‘credit crunch’ resulting from the fallout of the sub-prime mortgage crisis in the United States and Britain.
Economics aren’t everything of course. There are also sound practical, geographical and even ecological reasons for refurbishing a house with energy use in mind.
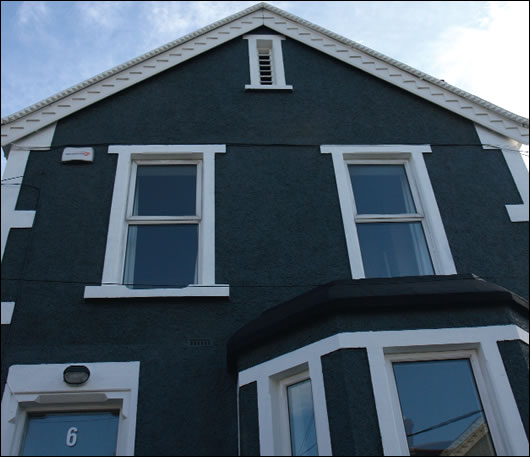
The title picture is a view from the back garden of Michael Bredican’s house in Clontarf, and the façade (above) of Fionna Fox and Bernard McCabe’s Smithfield house, two distinctly different existing homes where distinctly different solutions were taken to improve energy performance and reduce carbon emissions
Firstly, housebuilding does not necessarily occur where there is demand, particularly in urban areas. Secondly, many houses have historic and aesthetic features that owners are seeking and would not therefore be interested in new buildings.
More concretely, it has been estimated that up to 80 per cent of existing Irish housing stock could significantly benefit from, at a minimum, improved insulation. Given that Irish housing has, on the whole, not been designed with energy use in mind despite rising fuel costs there are two options: wholesale demolition and rebuilding – which is both impractical and unsustainable – or refurbishment.
The simple issue of comfort, and the attendant spectre of fuel poverty, should also not be ignored. Interestingly, a British government study found that only 25 per cent of homes in the UK met the official standard temperatures – 21 degrees Celsius in the living room and eighteen degrees Celsius in other areas. The minimum desirable temperatures from a health perspective are eighteen and sixteen degrees respectively. The British government found that when the outside temperature dropped to four degrees 50 per cent of owner-occupied houses in England failed to meet these minimum standards. Worse still, the figures for council houses that failed under these circumstances was 62 per cent. Even more alarmingly, this figure shot up to a staggering 95 per cent in private rented apartments. It shouldn’t be forgotten that, with the exception of the imminent change to Part L, standards are higher in the UK than here in Ireland.
From a purely environmental standpoint improvements to housing stock also make perfect sense. An Environmental Protection Agency (EPA) report, Ireland’s Greenhouse Gas Emissions in 2006, indicates that energy use in Irish housing accounted for 7,289.87 kilotonnes of CO2 emissions, a figure virtually unchanged since 1990 which saw 7,350.38 kilotonnes. While lower than other sector such as agriculture (19,309.07 kilotonnes), industry and commerce (12,031.58) and transportation (13,718.94), there is clearly room for significant reductions in the production of greenhouse gasses in the residential sector.
Finally, there is the reality that refurbishment is already going on – new kitchens, windows and doors and extensions loom large in our house-obsessed culture and if the work is already being done, why not throw energy use into the mix?
What is to be done?
Obviously there are significant constraints on what can be done to upgrade a building’s performance, after all, unlike building from scratch renovating a house does not present a clean slate. However, thinking about things fully, we never really have a totally free hand – there are always restrictions, whether imposed by budget, planning issues, site size, access and so on.
The first thing to do is to consider the building fabric. Many would-be renovators jump both feet-first into renewable energy sources – a situation that has recently been exacerbated by a generous grants regime – and while using renewables is to be commended, it shouldn’t be the first consideration. Issues of insulation and air-tightness should be considered before buying solar panels, heat pumps and all – what is the point of changing space heating systems, even to ones with lower fuel consumption or carbon emissions, if significant amounts of heat are lost anyway?
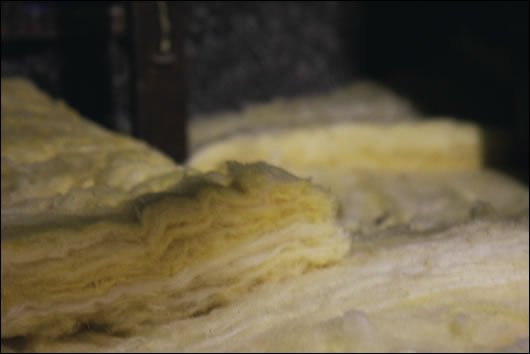
Loft insulation at Fionna Fox and Bernard McCabe’s house, a vital factor in improving the energy efficiency of a house. There is little point in changing heating systems and installing renewables if significant amounts of heat are being lost through the building fabric
The very first thing that should be done, if it hasn’t already, is to insulate the loft – heat rises and significant amounts are therefore lost through un-insulated or poorly insulated roof-spaces. A range of high-quality natural materials from hemp to sheep wool are now regularly used, typically for loft insulation in refurbs, often for health reasons. After that there is the issue of the wall insulation – if the house is old enough there may not be any at all, nor may there be a cavity to install any in. In this case dry-lining or external so-called ‘outsulation’ are recommended. Even if you have acavity wall house, has it been insulated, and how good is that insulation? Is the cavity wide enough to pump-fill the wall with bonded bead cavity wall insulation? With all insulation, should you trade better U-values for higher embodied energy? Or is it better to do the opposite? The list of options can seem endless.
Glazing is, of course, another important consideration and double-glazing is obviously a must, if possible. Beware, however, not all windows are equal. Low-e glass is obviously preferable but it’s also vital to consider the U-value of the overall window unit, not just the glazing. Paradoxically, the larger the window is, the better its overall U-value will be due to the greater glass to frame ratio, but use of a larger window can reduce the overall fabric U-value, as it’s easier to achieve better U-values with walls. Window installation is also important, particularly with regard to air-tightness.
More and more houses being constructed in Ireland today are being designed and built with air-tightness in mind, thus reducing leakage. The amount of air that can infiltrate or exfiltrate a building is, in fact, a good indicator of how well a building is built in the first place. True air-tightness can be difficult, and expensive, to achieve in refurbishment but there are always ways to improve. Even modest but easy measures to make a house more air-tight can be taken, from simply making use of draught excluders to inserting a chimney balloon into an open fire grate – when it’s not lit obviously. Perhaps that open fire should be removed altogether?
Renewables, however, can play a very important role and once the building fabric is up to scratch there are many options to be considered from solar panels – both thermal, for producing hot water, and photovoltaic, for generating electricity – to biomass boilers heated by wood chip, pellet or other eco friendly fuels, heat pumps, wind power and so on. Even the humble gas boiler can be a good investment. Although natural gas is not a renewable or carbon-free fuel, high-efficiency condensing boilers are a vast improvement on the traditional boilers used in many dwellings.
Then there is the issue of how to distribute the heat. Traditional radiators are notoriously inefficient, requiring a high surface temperature. Underfloor heating or more technically advanced radiators that do not rely on high surface temperatures will make significant savings in terms of both cost and carbon emissions. Alternatively, heat-recovery ventilation can also be used to both ventilate a home as well as heat it, although its efficient operation depends on achieving good levels of air-tightness.
Finally, low energy A-rated appliances will make a significant impact on both carbon emissions and household bills but remember, they aren’t a panacea – an energy efficient oven is still an oven.
The key question in refurbishing a home to bring it up to modern energy efficiency standards is value: will the work pay for itself in savings and how long will that take? Making a rash decision could result in a costly mistake
If all of the above seems daunting, or even downright terrifying, don’t worry – many have been there before you and here are two case studies that represent different approaches to improving existing houses.
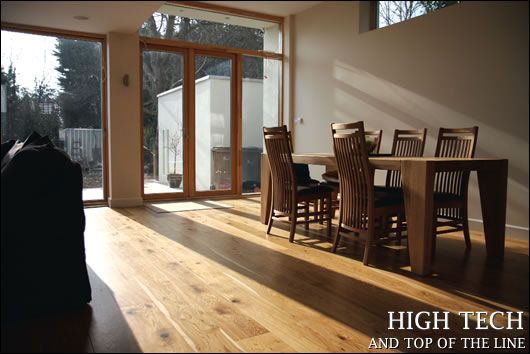
Michael Bredican doesn’t do things by half. The Dublin-based builder has recently moved into a 250 square metre (including an extension), four bedroom, 60-year old block built semi-detached house that he has completely refurbished to bring up to today’s expectations in energy efficiency. Unlike most energy upgraders, Bredican has not taken a piecemeal approach to meeting – or indeed reducing – the building’s energy needs. Instead he has gone the whole hog. Bredican’s house in Clontarf includes thermal solar panels, a deep bore heat pump, a condensing gas boiler, underfloor heating and heat recovery ventilation. It also makes use of a variety of techniques to reduce energy need including rockwool insulation, a metal stud from Kingspan and dry lining.
Of course Bredican, being a builder himself, knows what he’s doing: “I’ve been in the building industry for a long time now,” he said. “I have a degree in construction economics [and] last year I did a course in renewable energy technology which gave me access to a range of people.” Bredican, clearly a committed eco-builder, has been reading Construct Ireland for some time: "It's been useful for helping me understand the various technologies and techniques that I wanted to put into practice in this house."
On the question of overkill Bredican is unrepentant: “I wanted to implement as much as possible of it. I’m going to use it as a flagship for my own work,” he says. “I’ve put my money where my mouth is.”
The first question was how to improve the building fabric, both of the existing house and of the new extension that Bredican was adding. The existing building itself consists of 250mm solid block walls, somewhat limiting the options. In this part of the building Bredican installed a 50mm metal stud from Kingspan with a rockwool board supplied by the appropriately named Dublin firm U-Value Insulation. The new extension, a 50mm cavity wall, also sees rockwool and was subsequently dry-lined. In-situ U-values are, unfortunately, not available.
Bredican also attempted to improve the air-tightness of the house: “We’ve sealed-up the attic space, even the crawlspaces. Every part of the house is sealed-up as much as possible [but] I’ve yet to have a blower door test done.”
The existing windows were replaced with double glazed, argon filled, low e-coated Harmon Vinduer windows. These aluminium clad windows have a U-value of 0.9w/m2K and were also used in the extension.

A bore hole was used for the geothermal energy, due to lack of space, which despite being only two metres wide, is 180 metres deep
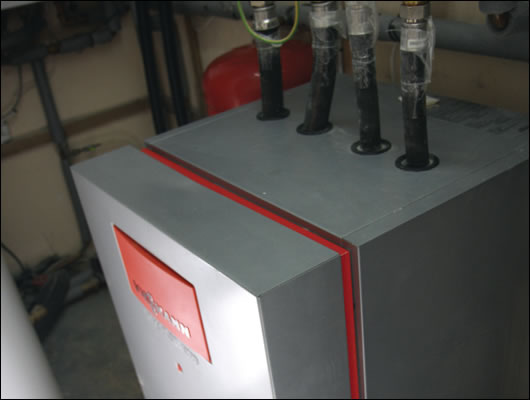
The heat pump, a Viessmann Vitocal 300 supplied by Precision Heating, only provides the space heating of the building, and doesn’t heat the water, to maximise its efficiency
Bredican bought the house in 2006: “I got feedback that it was in a good location for a [bore hole] heat pump from Michael Dineen at Groundsource. We had a lot of water – it was almost a well.
Being situated not only in an urban area, but also on a site that was already built dictated the source for the geothermal energy. For a start, a standard ground source heat pump with a large array of horizontal plumbing was out due to a lack of space – it was bore hole or nothing: “I needed it to be in the back garden – at two metres wide it’s the smallest you can go,” says Bredican. Despite being only two metres wide, the bore hole is 180 metres deep.
The geothermal system was designed by Groundsource of Slane, County Meath. The company’s Michael Dineen explains: “You don’t know what you’ll get until you actually drill. Certain areas are suited, others aren’t.”
The system that Dineen provided uses closed loops, meaning the water continually recirculates through the system, in this case at a rate of about 3.5 cubic litres per hour. The average temperature of the incoming water is 12 – 13 degrees Celsius.
“You have two plate exchangers,” says Dineen, “the refrigerant gas is released in a low pressure circuit and it goes to minus 25 or 30 degrees. That’s passed through a plate exchanger and the gas extracts the heat from the water, usually taking it to about 40 degrees. The compressor pressurises the gas that goes through another plate exchanger that has the hot water for the underfloor heating – the gas can reach 60 to 70 degrees.
“The water temperature is managed via the weather compensator,” says Dineen, noting that this improves efficiency.
The system is rated as a having a COP of 5:1: “For every kilowatt of electricity used to work the heat pump and compressor, you’re getting five out of the ground.”
Dineen cautions against installing geothermal heating without fully considering it, stating that a good source is essential: “A heat pump is only as efficient as the collector,” he says. “You go to trade shows and they’ll tell you how efficient their heat pumps are but it’s no good if the collector is not done properly. Water is your medium – it’s transferring heat from the element, which is rock. Sand or gravel [in the case of ground source heat pumps] is too dry. Even a bog is no good – a bog has no movement [of water].”
The heat pump Bredican used is a Viessmann Vitocal 300 that outputs up to 10.8 kW per hour and was supplied by Precision Heating. The company’s Alan Hogan explains: “The 100 range models are, to Viessmann, a basic technology. 200 is equivalent to an S-class Mercedes and 300 is the top of the range.”
“We used a weather-compensated heat pump – the system measures the temperature in the buffer tank, making sure it’s at the correct temperature.” The objective of this is to have the system modulate according to the heat loss in the building and the outside temperature.
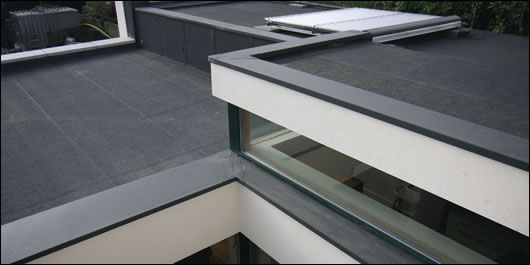
The evacuated tube solar collectors supply between 45 and 50 per cent of the house’s hot water over the course of the year
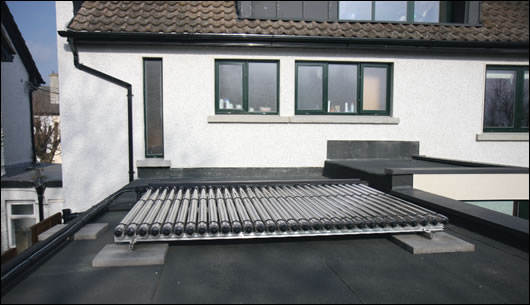
Hogan explains that although the heat pump could have supplied hot water for the building it was decided not to pursue this for reasons of efficiency. “We wanted the heat pump to do the baseload [space heating] of the building and not heat the water because if you make a heat pump work harder you will lower its COP.
“We sized the heat pump on the basis that 90 per cent of the year the building would need 10 kW. The [Viessmann condensing gas] boiler monitors the temperature and comes on and assists the heat pump when necessary. The boiler is always in [the more efficient] condensing mode when it’s on.”
Continuing his car analogy, Hogan compares the system to the famous Honda Civic IMA hybrid car: “It’s as if it has two engines. The heat pump will take care of the trickle load of the building. The boiler only ever comes on when the [outdoor] temperature is lower than one degree.”
For domestic hot water, the building uses a combination of thermal solar panels and gas. “The thing about comfort in the home is that people don’t notice one or two degrees in air temperature but they do notice if there’s not sufficient hot water. So, if the solar can’t heat the hot water, the boiler comes on at the times it’s set to.”
The evacuated tube solar collectors – three square metres in total also from Viessmann UK – supply between 45 and 50 per cent of the house’s hot water over the course of the year.
Water is collected in a 300 litre twin coil tank. “Consuming 160 litres of hot water per day expected hot water demand is 3,400 kW hours annually. We’re producing [around] 1,840 kw hours by solar – approximately 49 per cent [of demand]. This amounts to reductions in CO2 emissions of 400 kilograms annually from the solar alone.”
The ability of the solar to meet hot water demand obviously fluctuates according to seasonal weather. Most generation occurs outside of the winter months, peaking in July at approximately 90 per cent, while from January to March it drops to below 35 per cent. Speaking to Bredican on a day in early February, Construct Ireland was informed that the solar system was producing water at 25 degrees.
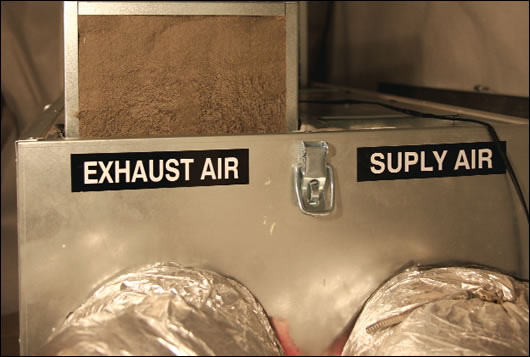
The house also features a HRV unit, the LTR 3 from Enervent, which is used for ventilation and air filtration
In addition to the solar, geothermal and gas, Bredican’s house also features heat-recovery ventilation, specifically the LTR 3 from Enervent: “When I was researching the heat recovery I wanted low noise and a small unit,” he says. “I [also] wanted a filtered unit.”
The LTR 3 features four speed regulation, an on/off-switch for the heat recovery and the models with electrical heaters include regulation of the heating.
The LTR 3’s fan power is 130 watts while E-designated models include a built-in 500 watt electrical heater with a capillary thermostat and EP-designated models include a built-in 500 W electrical heater with a Pulser Triac controller and a duct temperature sensor. Bredican does not use the system for heating, instead concentrating purely on ventilation and air filtration.
“I can use it to get heat but I’ve never used it for that [so far],” he explains. On the ventilation front, the device has revealed a slightly disturbing fact: how poor air quality is in any home: “I can’t get over how dirty the filter gets – filthy, they get black.” Clearly the machine is doing its job.
Overall, between the improvements to the building’s fabric and the high-performance, low energy systems added, Bredican declares the project a success: “I’ve found the house is a hell of a lot easier to live in than the last one I lived in. It’s so comfortable,” he says.
Some would say Bredican’s project is overkill, going much further than most people would ever contemplate, in particular in terms of the heating systems. His reasons for doing so are also unique to him as a builder. Nevertheless, as an upgrade, the work on the dwelling shows what can be done and it is of course encouraging that a builder, albeit one already committed to sustainable development, would take measures to reduce energy demand and meet that demand through renewables and efficient energy sources when working on his own home – truly, this old house is a sign of the changing times.
“When you buy a mobile phone or computer you want it to keep up with the times,” says Bredican. “When it comes to a house I wanted it to be as sustainable and future-proof as possible. Today I met two architects and clients. One had seen the house and wanted to replicate what we’ve done here.”
Upgrading a home’s energy performance is a personal act – after all, the owner must first decide to do it but, more importantly, the scale of the work to be done will depend on a range of individual factors including the budget available, the nature of the building being worked on, and even its location.
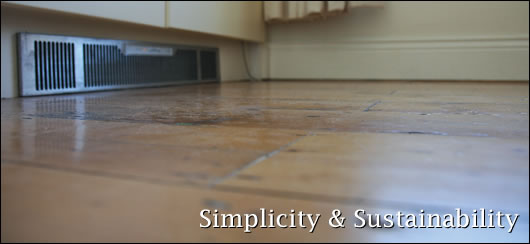
Couple Bernard McCabe and Fionna Fox renovated their 1,350 square feet (125.4 square metres) home in Grangegorman near Dublin’s Four Courts in September 2007. Like an increasing number of their contemporaries the two young professionals, a pharmacist and solicitor respectively, focussed not only on aesthetics and indulgence but also on the environmental impact of their home, improving the comfort level as a result.
The building, a century old character-filled three bedroom end-terrace was far from ideal from an energy perspective and McCabe and Fox experienced some trials during the refurbishment but the result has been worth it: “The process was very natural,” says Bernard McCabe, “we wanted to make the house as ecological as possible seeing as we were doing the whole thing [refurbishment] anyway.”
The original plan called for an extension but after attending a meeting at the Cultivate centre in Dublin’s Temple Bar the couple decided against it: “We didn’t need the space and we’d need to heat it,” says Fionna Fox.
Energy consumption was something that was already on the couple’s minds, having bought the house in January 2006 and lived in it since then: “The house was dark and cold and the oil-fired central heating cost a bomb – everything was falling down basically,” she says.
McCabe concurs: “It needed stripping back.”
In any eco-construction project the key thing to get right is the building fabric. Of course, although this always a challenge, it poses greater difficulties when working with a pre-existing building, particularly older buildings which were often constructed with little thought given to energy use. For Fox and McCabe the key issue was insulation but it turned out that the previous occupants had given the couple a helping hand: “A lot of the house is concrete,” says McCabe. “It was [already] dry-lined on top of that – six inches.”
“The whole place had already been dry-lined,” agrees Fox, but the couple didn’t stop there: “We used glass wool in the attic – double the recommended amount.” Indeed, 40 centimetres of glass wool was used to insulate the attic floor.
Additionally, Actis multi foil insulation sourced from Dublin’s U-Value Insulation was installed above the joists at ground floor level, just below the wooden floor. “The foil insulation is there to insulate the floor as well as possible,” says McCabe.
The party wall that divides the end-terrace building from the building next door was fitted with 3/4 of a foot (0.29 metres) of sound proofing plasterboard, mainly to reduce noise but it also has some additional value as insulation.
Life’s a gas
Unfortunately for McCabe and Fox, renewable energy was not an option. The house’s chimney obscured the sunlight, making solar panels impractical and the couple decided against a wood pellet boiler due to a lack of access and storage space. Given this scenario, the couple decided to install an efficient condensing gas boiler.
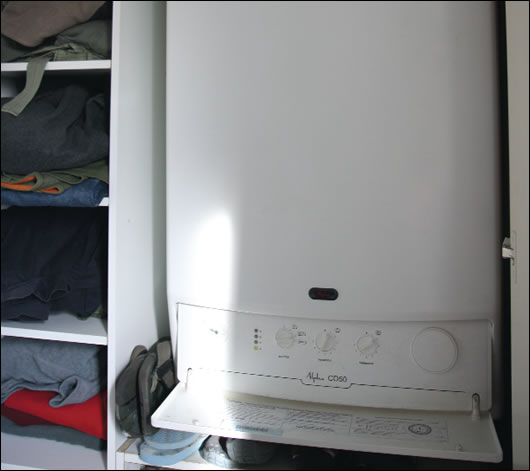
The couple decided to install an Alphatherm condensing combi boiler, with a Zenex GasSaver on top, which increases the efficiency of the boiler
“Between Barry [Gallagher, builder on the project] and Michael [Meehan, heating consultant] we worked out that we couldn’t do any of the renewable options,” says Fox. “Michael pointed out that, from an eco and energy point of view, you want to recover your money within ten years.
“That left us with gas as our only option. We got the most efficient gas boiler available and have aGasSaver on top.”
The boiler is an Alphatherm CD-50, a condensing combi boiler holding 50 litres of hot water. Combi boilers are used to eliminate the need to store hot water thus freeing-up space that would otherwise be used by a storage tank and also providing greater efficiency.
Energy consultant Michael Meehan of Ecosave explains how he became involved in the refurbishment and what was done: “I was referred by [sustainable design consultant] Jay Stuart. “Solar panels wouldn’t work – they just weren’t practical. Bernard and Fionna said to me that they’d had a lot of information from different people and it didn’t add up.”
And so, gas it was: “We stripped out the services and put in the combi boiler and Zenex GasSaver. The combi boiler heats incoming water directly while the GasSaver pre-heats the cold water [coming into the system] using the flue gas. These measures increase the efficiency of the boiler.”
Meehan says that the savings achieved by the GasSaver are due to the inefficient nature of domestic hot water systems. He also says that combi boilers have not seen significant use in Ireland due to poor plumbing techniques: “Victorian plumbing – the technology that is still being used comes from the Victorian era: a cold water storage tank in the attic and a domestic hot water tank. That technology is over 100 years old. The modern way to heat water is with heat exchangers and that’s what’s inside the boiler. You only use the amount of hot water you need,” he says. “The reason combis never got going in Ireland is our poor infra- structure, you need good water pressure.”
After all of the work on the new heating system the proof that it was worth the effort is in the running costs. McCabe and Fox’s first gas bill, covering the winter months of November to December 2007, came to just e167.81.
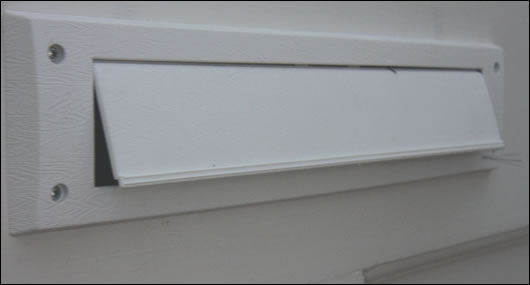
Draft excluders were fitted to all external doors, windows and the letterbox resulting in a notable reduction of heat loss
In order to fulfil the building’s space heating needs efficiently Meehan sourced and installed low energy hydronic heating terminals instead of radiators. Fox explains that the tiny devices, recessed into the wall, are an improvement on traditional radiators: “Instead of heating all of the hot water in a normal radiator it heats a cup full and then blows it out into the air.”
These are also zoned for greater control: “Upstairs and downstairs thermostats can be used independently,” says McCabe. They also have the additional benefit of being extremely low profile, effectively built-into the walls, and thus taking up effectively no space, one of the usual key selling points of underfloor heating.
In addition to the major work of insulating the house and installing a new space and water heating system, the couple also took a range of smaller measures to improve both the energy efficiency and environmental profile of their home.
The energy upgrade coincided with a more traditional refurbishment, part of which called for timber flooring. Bernard McCabe explains that ecology was part of the thinking here as well: “We used reclaimed pine – because it’s so old it’s quite tough.”
The little things that matter
The couple also shifted the attic entrance into a little-used spare bedroom and draft proofed it, thus further reducing the impact of drafts and cold air.
In order to stop heat from escaping up the chimney of the open fire Fox and McCabe purchased a chimney balloon. This simple inflatable e20 device is inserted into the chimney to block it up, creating a near air-tight seal. The only thing to remember is to take it out before lighting a fire.
Draft excluders were also fitted to all external doors, windows and the letterbox and have made a difference that the couple has noted.
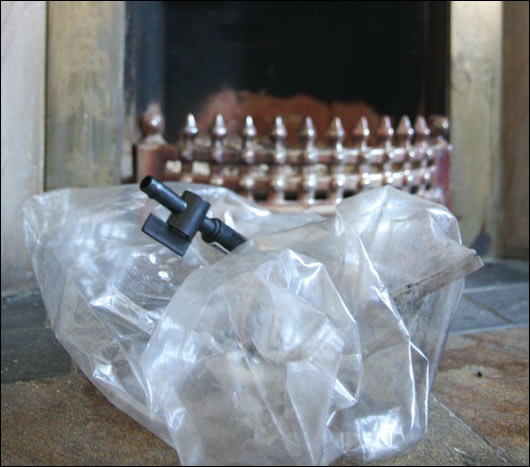
A chimney balloon, used to stop heat escaping up the chimney of the open fire
All electrical appliances used in the house are A+ rated and the couple have purchased an interesting device known as a ‘Centa Meter’ which monitors the amount of electricity used in the house, allowing them to know which appliances use more than others.
The house also makes use of rainwater harvesting – a 500 litre tank in total – to supply the washing machine, dishwasher and toilet. “Grey water is [also] harvested for the garden,” says McCabe.
Additionally, all lighting used in the house is low energy.
Finally, although the couple didn’t replace those of the building’s windows which were already double-glazed, they do plan on adding one extra touch to them to further improve their thermal performance: “We’ll be adding a film to the glazing to stop glare and bounce heat back, improving the u-value,” says Fox. On top of this, any of the glazing that was single-glazed has been replaced with argon-filled low-e ‘K glass’ from Pilkington. Argon-filled ‘K glass’, which has a typical U-value of 1.5, is well-regarded for its thermal performance and is, as a result, often used in unheated conservatories.
The final stage will be to install a wood burning stove which will reverse the 80/20 ratio associated with open fires where 80 per cent of heat currently escapes up the chimney.
Clearly Fox and McCabe have shown that even in difficult situations where renewables are not ideal a house can enjoy significant improvements to its energy use. The improvements to the building fabric when combined with the more efficient heating system and a gamut of smaller measures make for a much improved performance and on a scale that everyone can aspire to.
- Articles
- Sustainable Building Technology
- Move on up
- energy upgrade
- energy rating
- refurbish
- Alphatherm
- Enervent
Related items
-
EIB Group support new low-cost home energy upgrade scheme in Ireland
-
Retrokit tailors software platform for one-stop-shops
-
SEAI shifts focus to deep retrofitfit with conference & pilot scheme
-
Bristol deep retrofit proves worth with monitoring
-
A2 rated extension and upgrade, Co Cork
-
Cork home hits 94 percent heat reduction with Enerphit
-
Opinion
-
Thermal bridging
-
Isover awards
-
Carlow A1 upgrade
-
Zero waste
-
Clonakilty eco house