- Ventilation
- Posted
Air-tight case
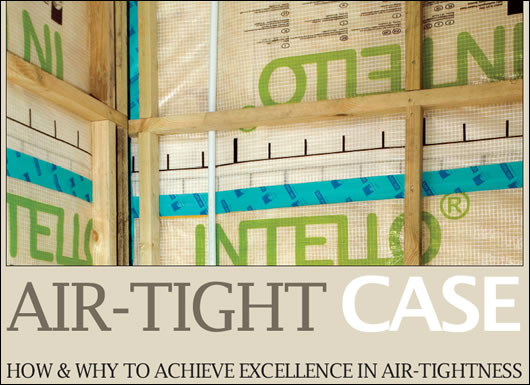
Air-tightness is a key factor in any low energy build, but is often overlooked in comparison to energy sources and insulation. Lenny Antonelli examines how air-tightness is achieved in buildings, from design stage down to the final sealing.
Andreas Schmidt likens air-tightness to a good wind-proof jacket. “If I’m wearing a wool jumper on a windy day, the wind will blow right through it. If I put on a wind or rain jacket and zip it up, then the wool insulation can do its job properly. It’s the same with a building. You might have insulation in your house, but you’ll still be cold if the wind is penetrating.” Schmidt is the Irish representative of Swiss air-tightness specialists SIGA, who entered the Irish market in November last year. “The idea is to keep all the warm air inside the building and all the cold air outside, to prevent draughts and high heating bills,” he says.
Air-tightness - essentially meaning the elimination of draughts - is crucial to reducing energy demand in buildings. Chris Montague of Building Envelope Technologies, who provide a range of air-tightness services to the Irish construction industry, says there are two steps to achieving it: “achieving air-tightness is 50 per cent design and specification, and 50 per cent construction quality. You can have a great design for air-tightness but if it's not put together correctly it won't succeed. Likewise, no matter how good the build quality is, the design has to be right.”
The first step is simply deciding how air-tight you want your building to be, Montague says. “You can go as low as passive standards or you can build something that simply meets the building regulations, depending on your target energy consumption.” Air-tightness of 0.6 air changes per hour (ACH) at 50 Pascals (Pa) pressure is required for passive house certification, though it’s common for new Irish buildings to be as high as 10-15ACH at 50 Pa.
Air changes per hour is just one of many units for measuring air-tightness - the other most common being air permeability, which is measured in cubic metres per hour per square metre of external envelope area (m3/hr/m2). Air changes per hour is the accepted metric for measuring air-tightness in many continental European countries, while air permeability emanates from the UK, and is used to express the air-tightness requirement for new homes under the recently changed Part L of the Building Regulations.
For typical dwellings it is reasonable to assume only a marginal difference between ACH and air permeability results, according to Niall Crosson of Ecological Building Systems. “A house achieving an air permeability of 10m3/hr/m2 at 50Pa could be assumed to have an ACH at 50 Pa of say, 9. This can change dramatically with more complex building forms.” As a rule of thumb, Crosson asserts, the ACH or air permeability at 50 Pa can be divided by 20 for non-complex building forms to estimate air change rates under normal conditions. “There is a methodology for calculating a more exact figure, but it’s not necessary for conventional dwellings”.
New homes must now achieve a result of 10m3/hrs/m2 at 50 Pa or better, as per the reference house in the technical guidance documents of Part L of the building regulations, which furthermore make measuring air permeability mandatory by means of blower door testing. However, the latest revision stipulates that new homes must consume 40 per cent less energy than this reference house, though builders have the discretion as to how exactly this target is met – and can choose how to claw back the necessary reductions by going beyond the minimum requirements in everything from added insulation, to renewable energy or high efficiency boilers, to improved air-tightness. Because sealing a building during construction involves relatively little or no cost - at least down to an air permability of about six or seven m3/hr/m2 at 50 Pa - it is one of the most cost effective ways of making large strides towards compliance.
Chris Montague continues: “When you’ve decided on your target energy consumption, you then have to consider all the various components of the building to make sure they will satisfy the level of performance you want.”
A crucial step in designing an air-tight building is introducing an air-tight barrier - essentially a continuous air-tight layer that runs around the building. “In your plans, if you can follow an air-tight line around the house without interruptions, you’ve done a good job with your design,” Andreas Schmidt says. “But if there’s an interruption in your line, the builder can’t build air-tight. If nobody thought about how to connect the air-tight membrane to a window or skylight at the design stage, how will the builder be able to do it?”
Niall Crosson of Ecological Building Systems elaborates on the air-tight barrier. “It’s typically the line that separates the heated conditioned air inside from the cool unconditioned air outside. If I take my plans and draw a line continuously around the perimeter, wherever I have to lift my pen off the sheet of paper, wherever there’s a break, that’s where we need to find a solution.” Ecological Building Systems was established in 2000 as a division of the MacCann & Byrne group, specialising in green building products, including the Pro Clima intelligent air-tight system and a range of natural insulation materials.
So, physically speaking, what exactly is an air-tight barrier? In some cases, it simply means ensuring all of the normal construction components are fitted and sealed properly to prevent air leakage. In other instances, a special air-tight membrane should be introduced to the construction.
Niall Crosson elaborates: “In masonry build, wet plaster is very reliable as an air-tight layer. But you need to plaster all areas, even if they're not exposed. I’ve seen block buildings fail air-tightness tests because they haven’t plastered unseen areas like behind toilets and sinks, and behind suspended ceilings. In the majority of cases a membrane is not required for masonry build, but it’s critical the plaster runs completely around the external envelope.”
“In lightweight construction, such as timber or steel frame, a membrane is a core part of ensuring air-tightness. You have to appreciate the importance of allowing the moisture to dry out particularly in timber frame or timber elements of block construction, and this is where breathability is key. Using an intelligent air-tight membrane greatly increases drying capacity.”
Ecological Building systems supply an intelligent membrane that regulates the diffusion of moisture through the air barrier (vapour control layer, or VCL). “Our membrane acts as an air barrier and intelligent vapour check rather than solely focusing on air-tightness,” Niall Crosson says. “It allows building components to dry out rapidly in the event that moisture penetrates into the building envelope. In winter months it prevents vapour from getting in, while in the summer it becomes up to fifty times more vapour open and allows it diffuse out. You may never need an intelligent membrane, but in the event of the unforeseen on site or over the life of the building it increases your drying levels.”
Do particular building materials or systems have an advantage when it comes to air-tightness? “The BER assessment presumes that timber frame is inherently more air-tight than masonry,” Chris Montague says, “and some anecdotal evidence says that timber frame houses are generally more air-tight. But that’s not the case in our experience. A masonry house is relatively straightforward structurally. If you consider that in relation to a timber frame house, which will have a vapour control membrane and many joints, the timber frame is a lot more complicated. It’s much easier to mess up with a timber frame build than masonry. That said, timber frame houses can be very air-tight.”
If reducing carbon emissions is the principle aim though, concrete block is probably not the best option. Cement production currently accounts for five per cent of global man-made carbon emissions, though ground granulated blastfurnace slag, a lower carbon alternative derived from steel industry wastes, is abundantly available in Ireland thanks to the impressive growth of Dublin-based supplier Ecocem, in particular. And while timber-frame building might not be as structurally simple as masonry, it does lend itself to pre-fabrication in factory, which allows for precision building and strict quality control. Chris Montague is convinced that ‘system’ building makes it easier to achieve high levels of air-tightness.
“The system builds we’ve tested have performed very well,” he says. “You don’t have to reinvent the wheel every time you reach an interface, as it will have been dealt with already.” Indeed, most super air-tight buildings in Ireland are constructed using a closed-panel timber frame system, in which insulation is precisely fitted to the timber panels during pre-fabrication.
Indeed, as recent case study articles in Construct Ireland have suggested, some closed panel timber frame homes are achieving superlative levels of air-tightness. A house in Malahide (1 ) built by the German company Project Oecotop achieved an air permability of 0.37m3/hr/m2 at 50 Pa whilst the two Botanic Homes passive houses (2)in County Carlow achieved 0.4ACH at 50 Pa. In terms of masonry, the ground breaking Easton News affordable housing development (3)in Kildare showed that with the right attention to detail in design and on site, full-fill cavity wall construction can achieve air permeability as low as 2.26m3/hr/m3 at 50 Pa.
SIGA’s Andreas Schmidt doesn’t believe any particular type of building has an air-tightness advantage. “There’s really no difference. If you bring the right detail from design stage to construction, it doesn’t matter what building material you use.”
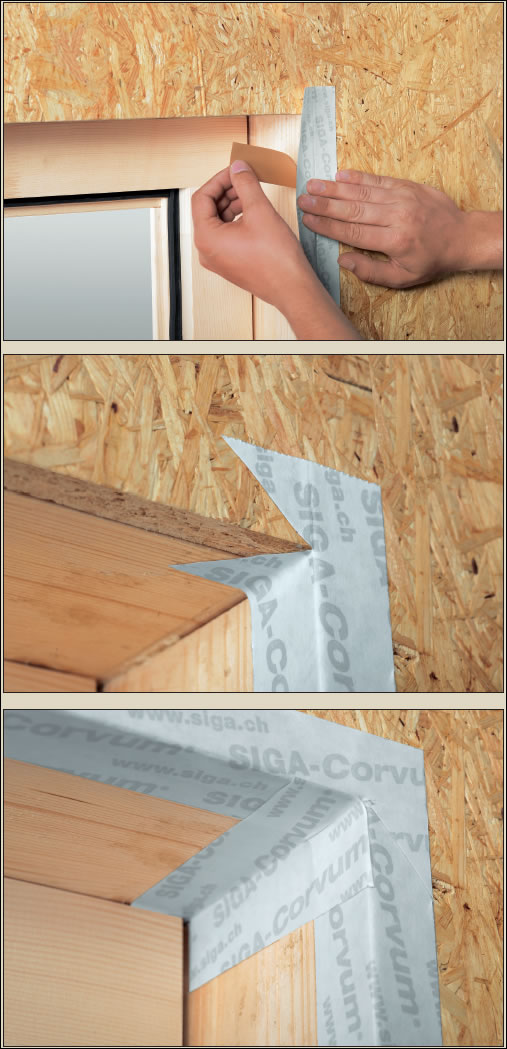
A step-by-step guide to using proprietary tapes to seal outside corners
From an air-tightness perspective, the shape of a building is arguably as important as the materials from which it is constructed. “The simpler the shape of the building, and the simpler the geometry and the less junctions, the better it will be in terms of air-tightness,” Chris Montague says. “You can’t make every building simple, but it really does pay enormous dividends if the designers keep that principle in mind, and tries to rationalise and simplify things.”
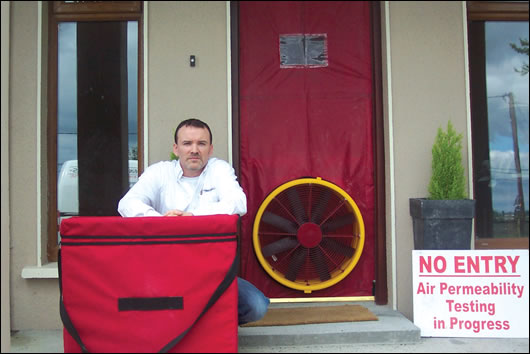
Pat Kyne of PK Energy Controls next to a blower-door
Niall Crosson emphasises the importance of simple design: “To achieve the best results we recommend trying to make the design as uncomplicated and straightforward as possible. Things like bay windows are very difficult to seal for air-tightness. You're adding on multiples of man hours by trying to seal them tightly.”
While ‘complex’ designs featuring bay windows, L shapes and angular projections may be popular, this doesn’t lend itself to lowering energy demand. Simple shapes are inherently more sustainable – they require less material to build, reduce the surface area through which heat can escape from the building, and reduce the number of intersections and joints where air leakage is possible. Perhaps more imagination is needed to marry simple shapes with innovative design and appealing aesthetics.
Of course getting the design right is just the first step towards air-tightness - implementing it is the next. “Picking your builders and making sure they’re trained is perhaps the most import thing,” Andreas Schmidt says. “If the builders just get the (sealing) product, they might be lost.” Both SIGA and Ecological Building Systems run air-tightness courses and seminars for those in the building trade, and both companies also offer on-site consultation.
So what are the most common points of air infiltration and leakage in buildings? All of the experts Construct Ireland spoke to offered a similar list: Doors and windows, skylights, service penetrations, overlaps between sheets of VCL, and junctions between the VCL and the building. Both SIGA and Ecological Building Systems sell a range of specialist air-tight tapes and adhesives designed to seal specific problem areas.
Niall Crosson explains Ecological Building System’s whole house air-tight system: “The Pro Clima intelligent air-tight system focuses on windows, floor joists, service penetrations and continuous sealing of the vapour control layer. For literally almost every detail there’s a specialist solution. Durability and health are vital; you need a system that will last the life of the building without emitting any harmful volatile organic compounds (VOCs). Studies have shown that gaps in the VCL can reduce insulation performance by up to 4.8 times, therefore a durable seal is critical.”
“We manufacture all of our own tapes and adhesives,” says SIGA’s Andreas Schmidt. “We don’t use any solvents, residential poisons or toxins. We work with this stuff every day so we want it to be healthy. Products with solvents and high boiling points also dry out much faster and become more brittle over time. Also, it’s very important for us to test the products not only in the lab, but on the building site under real conditions. We have long-term experiments running on site, as well as tests in the lab. Many of our products are patented.” After Schmidt spoke to Construct Ireland, he offered us an impromptu demonstration of SIGA’s air-tight products, and some basic installation training, from the back of his car on a miserably wet day along Dublin’s Ormond Quay. Despite the soaking rain, everything was impressively sticky.
According to Pat Kyne of PK Energy Controls, specialists in air-tightness testing, Irish buildings have a number of common air-tightness flaws. “The issues vary from building type to building type,” he says. “The worst case is typically the dormer bungalow. The warm roof area of the dormer bungalow is parallel with a crawl space that runs around the perimeter that is ventilated through the eaves. When the wind picks up you've got positive pressure on the windward side of the house, the wind blows over the roof and you get a negative pressure on the opposite side. The air will move and take the path of least resistance.”
“It enters the crawl space, hits the wall, moves down into the floor void that runs underneath the bedrooms, and from there it can go anywhere. This can causes a lot of air currents under the floor. It's a widespread problem, and you get an average of about eight to twelve air changes per hour at 50 pascals in a dormer. If you go downstairs and remove a recess light fitting, you'll feel the air moving at a very high velocity across the floor void. The effectiveness of any insulation in the floor void is dramatically reduced.” Kyne says that introducing a vapour control layer is the most effective way of solving this problem.
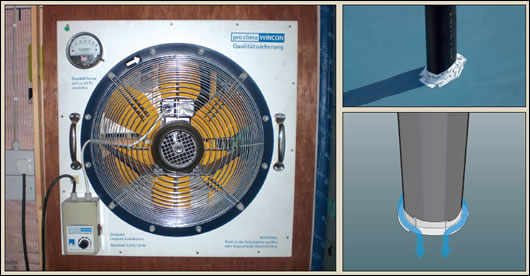
(clockwork from left) the Pro Clima Wincon, the ‘air-tightness spirit level’; wind-tight sealing of a round penetration; note the overlapping layers of tape to allow water run-off
Typical two storey masonry houses also face common problems. Kyne continues: “The most common problem here is also in the floor void. Joists run across the width of the house where they are butted into the wall, where they usually rest on the inner leaf of the cavity wall. The most common method is to butter up around the joists with mortar, but if they aren’t sealed up correctly any air free in the cavity can get into the floor void, and the problem is especially bad with partial fill cavity walls.” Kyne suggests filling the cavity to help remedy the problem if refurbishing, but recommends sealing the joists to the block properly during construction – or preferably resting them on hangers.
“A full fill cavity wall gives a much better performance than a half or partial fill,” he says. “After it's pumped and the bond on the bead is set, you get a minute leakage at 50 Pascals. In terms of air-tightness in a masonry house, full fill is the way to go.”
“If the boards aren't tied to the cavity, it makes the problem worse. You can see the joists on the infrared camera - they look like blue fingers streaming in from the cavity wall. I've tested houses that use the conventional method of supporting the joists in the inner leaf of the cavity wall, and they have an average of about eight air changes per hour at 50 Pa. However I've tested a house where the joists rest on hangers, and it got a result of about five air changes per hour.”
Kyne also cites ducts supplying extract fans and wall vents as places where air can leak easily if proper sealing is not in place. He stresses that it’s much easier to seal tricky areas during the build then to solve problems retrospectively – emphasising the importance of air-tightness in the design. During construction, gaps between door and window frames and the building can be sealed up, joists can be sealed properly to the block-work or vapour control layer (or designed to rest on hangers) and service penetrations can be easily taped up. All of these tasks became more difficult once the build is complete. Hence Kyne recommends blower door tests at both first fix stage and on completion to ensure any breaches haven’t occurred after first fix.
According to a SIGA energy calculator, basic attention to air-tightness can result in significant energy savings. The calculator estimates that, over a 200 day heating period, a house with eight air changes per hour and a 100m2 base, heated with oil to 20oC, will cost e4127 to heat, while an equivalent house with three air changes per hour will cost e1548 to heat.
Andreas Schmidt says that while attention to air-tightness inside is crucial, wind-tightness is also important. Wind-tightness is similar in concept, but refers to the external envelope of the building. If cold air can penetrate through to the vapour control layer, it lowers the temperature of the VCL. This causes the warm internal air to cool down when it hits the membrane, and condensation can occur, leading to mould and building damage.
“If cold wind and rain can penetrate your house you won't get the U-values you want,” Schmidt adds. “Take a skylight for example - it should be air-tight on the inside and windtight on the outside. If you stop all movement of air in the construction the insulation performs much better. If cold wind and rain can enter the building, then your structure can rot. It's important both sides are really tight.”
Once a building is sealed, testing it is the next step. Blower door tests – in which a fan mounted on a door is used to pressurise or depressurise the building – are the most common, along with infrared thermography.
“We highly recommend that a test is done when the vapour control layer is still visible,” Andreas Schmidt says. “You can then take a short piece of tape and repair any faults, but if the plasterboard is on then you’re in trouble.” Chris Montague stresses the importance of ensuring the person carrying out a blower door test is suitably experienced.
Ecological Building Systems provide an air-tightness quality control unit, the Pro Clima WINCON, a basic testing unit that allows builders to perform simple air-tightness quality assessments on site. “It’s basically a fan mounted on a wooden frame with a pressure gauge,” Niall Crosson says. “Prior to finishing, the builder can depressurise or pressurise the building very quickly and identify and seal leaks at any stage of the building process. It gives the builder more control instead of having to rely on the final blower door test. It doesn’t replace the blower door test but it helps to increase awareness on site.”
Despite the central role air-tightness has to play in low energy building, extreme levels of air-tightness aren’t favoured by all in the green building community, due to the assumption that they necessitate the use of mechanical ventilation heat recovery (MVHR) systems in order to maintain a healthy indoor atmosphere. Some green builders prefer to avoid super air-tight standards and the energy demand of MVHR systems, while still building well-insulated structures that are naturally ventilated and fuelled by low or zero carbon sources. It’s worth noting that MVHR energy consumption is coming down as MVHR manufacturers switch to low wattage fans and motors whilst improving the efficiency of their heat exchangers. MVHR and high levels of air tightness generally go hand in hand - Pat Kyne recommends a minimum air-tightness level of three ACH at 50 Pascals in order to make MVHR effective. “It think it will become the standard, that every house is built air-tight with MVHR,” he says.
Air-tightness was hardly thought of on building sites a few years ago, but things are quickly changing. “There's a massive change in awareness,” Andreas Schmidt says. “That's not just because of the building regulations, but because builders now have to deliver more quality. People buying a house want to get quality for their money. With oil prices rising, people are looking for safe energy. The Irish market is still behind, but there are so many people who are interested in air-tightness and want to build better, and that’s the amazing part for me.” Pat Kyne adds: “If there is a design for air-tightness, the contractor should appoint one guy on each site to look after air-tightness. I think that might be starting to happen now.”
Chris Montague agrees that awareness levels are improving, and believes that the Irish building sector is learning quickly. “Designing and constructing an air-tight building is a bit like riding a bike. The first time you’ll fall off, the second time you’ll be a bit wobbly, but the third or fourth time you’ll know what to look out for, and then you’re on your way.”
1 Walsh, Jason ‘Vorsprung durch Oeko-technik ’, Construct Ireland Issue 12 Volume 3
2 Antonelli, Lenny ‘Passive attack ’, Construct Ireland Issue 2 Volume 4
3 Stuart, Jay ‘Out of the Ordinary ’, Construct Ireland Issue 9 Volume 3
Related items
-
Why airtightness, moisture and ventilation matter for passive house
-
Airtight delight
-
Partel’s airtight membranes now certified for passive house construction
-
ProAir pioneers with EPDs for ventilation systems
-
Mass timber masterwork
-
Partel obtains EPDs for airtight membranes
-
Let’s bring ventilation in from the cold
-
45,000 more Irish homes face radon risk, new maps reveal
-
ProAir retooling for the future
-
Manhattan modular apartments feature Wraptite membrane
-
Ecological launch Inventer decentralised ventilation
-
Poor ventilation a Covid risk in 40 per cent of classrooms, study finds