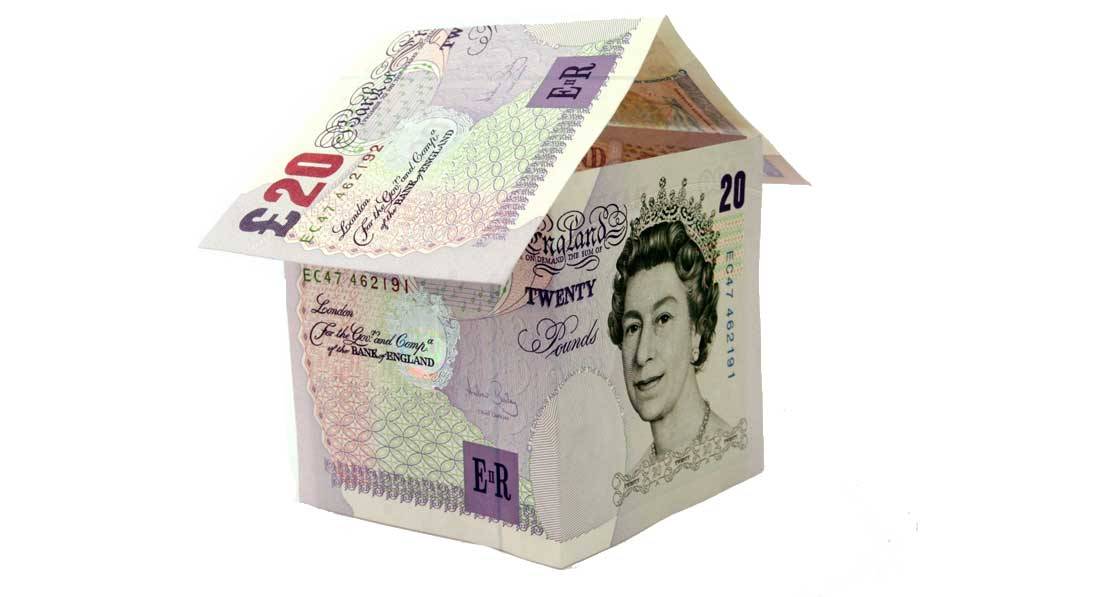
- General
- Posted
Passive house costs falling, new study finds
New research published by the Passivhaus Trust has shown that the real-terms cost of building to the passive house standard has fallen since the previous study four years ago.
This article was originally published in issue 32 of Passive House Plus magazine. Want immediate access to all back issues and exclusive extra content? Click here to subscribe for as little as €10, or click here to receive the next issue free of charge
A “best-practice” passive house social residential project might now be achieved at a cost uplift of 8% over a nonpassive equivalent – and some projects are already achieving lower costs even than this.
The Trust’s latest research examined cost data from just over a dozen passive house residential developments ranging in size from less than five to over 70 units. Most were constructed for social landlords, with a minority for private sale.
The Trust analysed contract pricing information by element where this was available and found a range of extra-over costs. The Trust was able to identify factors that were associated with lower extra-over costs, including simple form, modest glazing, and an experienced team – in particular, experienced clients.
Taking an ‘ideal’ project based on these extra-over costs, it was calculated that the full extra cost of passive house, to include, structure, insulation, glazing, airtightness, building services, site supervision, airtight testing and certification, could be around £115/m2. This is around 8% of the average cost for similar-sized social housing projects in a relatively cost-neutral UK region, as calculated by Taunton-based cost consultants Baker Ruff Hannon.
The project also analysed the full build costs for the projects where this was available. Here a clear trend of cost reduction was seen in the latest costs, versus the costs collected by the Trust in 2015 (costs were corrected for inflation to enable more meaningful comparisons).
While costs of the more expensive projects in each survey were similar, in those in the lower-cost end of their cohort, prices showed a distinct drop.
A similar trend was reported by a single client, Exeter City Living, who have now completed or tendered for 10 passive house projects since their first in 2010. Over the course of several “generations” of procurement, learnings have been fed back in, to simplify and de-risk the projects, resulting in a real terms fall in construction costs of around 20% in that period.
The researchers spoke to a number of designers and contractors in the course of the research, who gave further insights into the way they had controlled costs, and also, the benefits they had been able to gain in their own companies as a result of what they had learned.
One contractor who built two successive passive house projects for the same client, using the same system, told the Trust how experience from their first build had fed back into the second: “For the first project, we had to do remedial work after the air tests on a number of units. We identified some weak points and changed some aspects of the construction for the second project, and had modifications made by our system supplier.
“On our next project, all the units passed first time. The whole build has gone a lot more smoothly.” On another project the quality assurance (QA) process adopted by the contractor led to a significant drop in defects, and now informs all their builds: “Defects and legacy are so frustrating for a contractor – you lose a lot of money and tie good people down going back to sort stuff out. The (QA) sign-off process has been a good lesson and reaped rewards in our business. It has been a good learning process for us.”