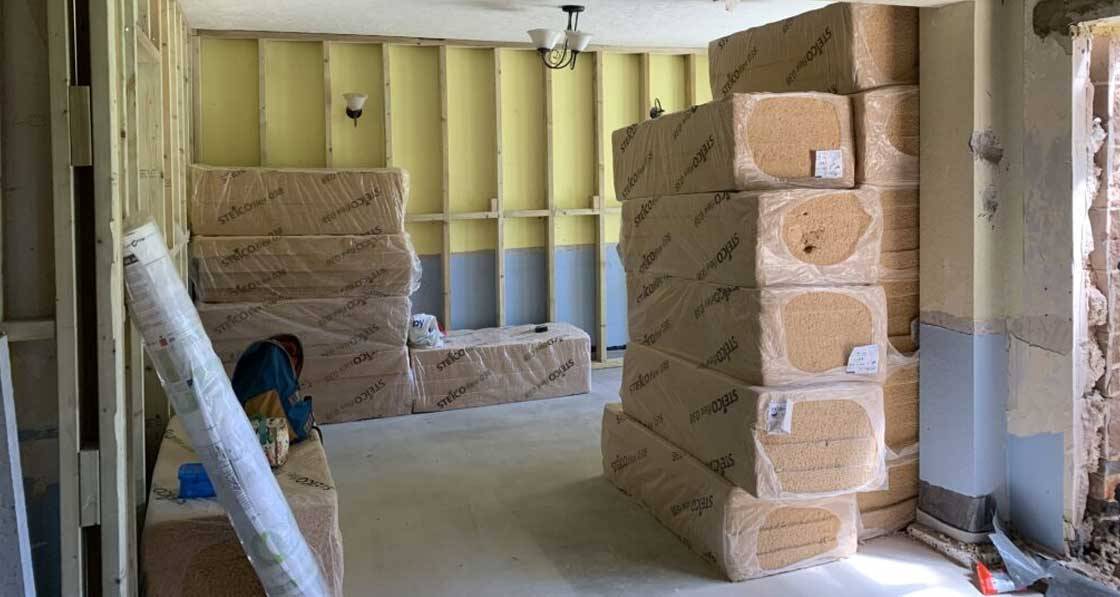
- Marketplace
- Posted
Building sector must take the lead on embodied carbon
This article was originally published in issue 39 of Passive House Plus magazine. Want immediate access to all back issues and exclusive extra content? Click here to subscribe for as little as €10, or click here to receive the next issue free of charge
That’s according to leading sustainable building supplier Ecomerchant and the Architects Climate Action Network (ACAN). “It’s tempting to think that there might be a council of despair and disappointment, but that most certainly isn’t the case within the industry itself…. There already exists a vast body of knowledge that has been built-up aimed at reducing industry’s reliance on fossil fuels,” write Ecomerchant and ACAN in a joint blog post published at www.ecomerchant.co.uk.
“Each individual, whether they be a homeowner, specifier, investor or construction professional, has the agency to make decisions to decrease embodied carbon,” write the authors. “After all, while operational emissions can be reduced over time with building energy efficiency renovations and the use of renewable energy, embodied carbon emissions are locked in place as soon as a building is built or refurbished.” The authors then present a range of steps that those in the industry can take to cut embodied carbon on their own projects. These include:
- Use materials that have low embodied carbon. Natural products, timber, wool, straw, hemp etc can act as a carbon store and are often manufactured using a low or renewable energy source.
- Optimising the life cycle impacts for anything less than a 60-year span is not worthwhile. The management and control of moisture in buildings is critical to their longevity. The building fabric is prone to decay if the structure becomes damp. Natural materials are breathable and offer a good solution to dealing with moisture.
- Build in flexibility. This may be addressed by creating a building that is either highly adaptable or with elements that can be reconfigured or reused.
- Think about real costs. Cheap now can be expensive later as you need to replace or repair more frequently, adding to your operational costs. Every time you replace or refurbish a material, you add carbon emissions to your building account. Invest in durable materials.
- Use multi-functional elements. For example, timber and straw modular systems can offer structure as well as excellent acoustic and thermal insulation,
- Value life cycle assessments (LCAs) and environmental product declarations (EPDs) for measuring the carbon footprint and environmental impact of buildings and their constituent materials.
To read the full article visit www.ecomerchant.co.uk.
Related items
-
Ecological Building Systems expands UK and Irish straw panel construction with EcoCocon deal
-
Focus on better buildings, not better spreadsheets
-
MBC offers total passive house envelope solutions
-
Historic Dublin building retrofitted with cutting edge insulation
-
Proctor gains ground with Scottish passive schools
-
Full EPD Certification for Pro Clima airtightness and windtightness products