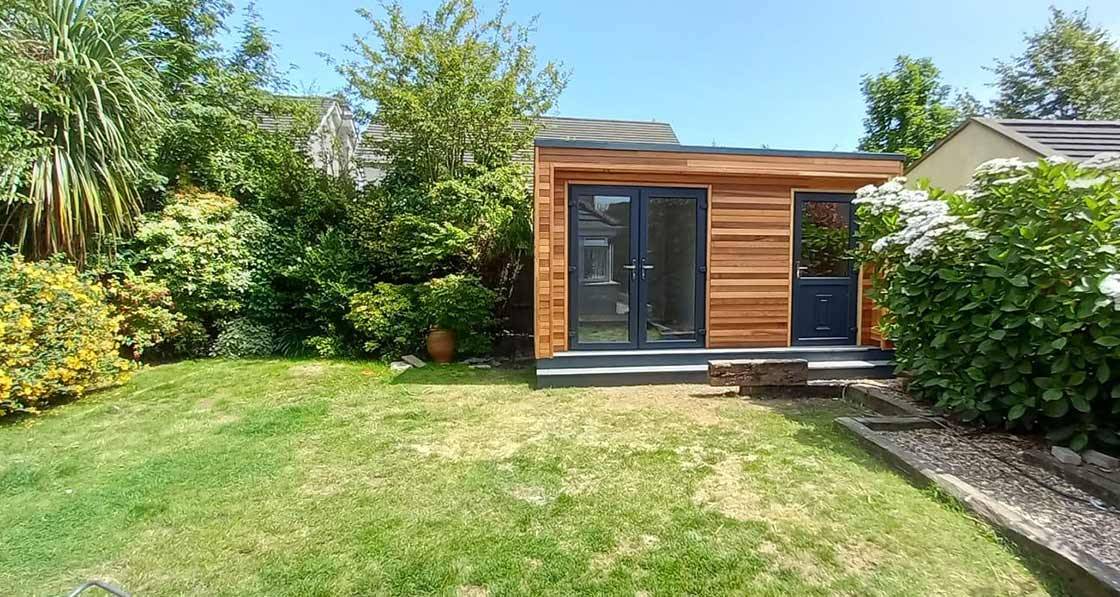
- Marketplace
- Posted
Low carbon, cement free carbon rooms being built in Cork
A garden room built by Cork-based Blue Mountain Garden Rooms has a significantly lower carbon footprint when compared to an equivalent log cabin with a concrete base, or to a block-built log cabin with a concrete base, a recent analysis has found.
This article was originally published in issue 42 of Passive House Plus magazine. Want immediate access to all back issues and exclusive extra content? Click here to subscribe for as little as €15, or click here to receive the next issue free of charge
The EcoPOD from Blue Mountain Garden Rooms has a gross embodied carbon of 1,660 kg CO2e (kilograms of CO2 equivalent), compared to 2,230 kg CO2e for the log-built cabin with concrete base, and 3,710 kg CO2e for the block-built cabin.
This is before carbon stored in the timber is subtracted, giving a net carbon footprint for the EcoPOD at the point of practical completion of -2,244 kg CO2e, compared to 14 kg CO2e for the log cabin, and 3,071 kg CO2e for the block-built structure.
This analysis mainly used carbon factors from the ICE Database v 2.0, as well as some environmental product declarations (EPDs), and assessed materials from bills of quantities, so principally covered the ‘cradle to factory gate’ period of the building life cycle. The analysis was funded by Cork City Local Enterprise Office under the Green for Micro scheme, and was conducted by sustainability consultancy Sustineo.
“As Ireland is now delivering buildings with the highest possible energy ratings, focus must shift to the embodied carbon of construction materials,” said Sustineo MD Raoul Empey. “In terms of greenhouse gas emissions reduction, embodied carbon has generally become the most significant impact of a building’s whole life cycle carbon impact.
Blue Mountain is a small sustainable timber frame fabrication company that erects and builds garden rooms and house extensions. “We focus on carbon neutral building materials and low-impact building methodologies,” said the company’s Conor McManus.
McManus said that the company has a strong focus on eliminating construction waste. “Our waste management strategy starts with the materials and methodologies we choose to build with, after that our priority is to keep waste to a minimum,” he said.
“Our timber carcass can be disassembled at end of life and reused. Our cellulose insulation is made locally here in Cork from recycled newspaper by Ecocel,” he added. The company’s garden rooms are all manufactured off site in Cork.
Blue Mountain Garden Rooms has also completely eliminated the use of cement and concrete from its builds, and installs its garden rooms on ground screws from Stop Digging Ireland. “Our pile system can be removed and reused at the end of a building’s life, unlike a concrete base,” McManus said.
He added that very little ground is broken with this practice with minimal disruption to soil and site.
The company uses only FSC and PEFC certified timber, and specifies Irish timber as much as possible, though McManus says it can be difficult to guarantee Irish timber at the moment due to supply chain challenges. He added: “We believe longevity is crucial to sustainable building and therefore choose durable materials to build structures that will last. Our external cedar cladding has a life expectancy of forty years while our membranes and tapes have a life expectancy of one hundred years.
“We feel a key component of sustainability is simplicity and replicability, and to this end we feel that our model and building methodology not only meets best practice criteria within the Irish construction sector, but is easily replicated with the materials and skills available.” The company has a close relationship with Dublin-based garden room manufacturer Rooms Outside, with which it shares best practice methodologies for designing and building sustainable garden rooms.
“Our goal for next year is to fit, as standard, environmentally friendly Marmoleum floor covering,” McManus added. “We would hope too, in the future, to change our internal finish which will completely remove the use of clean water out of the build process. We see this as our biggest, but not unsurmountable challenge. We have almost totally eliminated the wet-trades from the build and associated use of processed water. The only area now using clean water is the skim finish internally.”
According to Raoul Empey, recent progress on embodied carbon calculation mean it should be a standard part of construction projects of all shapes and sizes. “With advances in software, such analyses have become simpler and are really available to all design teams,” he said. “It’s up to those developing the client brief to build in carbon efficient design at the outset, and it is wonderful to see that demonstration of environmental credentials is not just reserved to large construction companies. Blue Mountain EcoPODs shows that it is also possible for smaller companies to build structures that align with our net zero goals in that more carbon is stored in the building materials used than was emitted in their manufacture.”
For more information, please visit https://www.bluemountaingardenrooms.ie
Related items
-
Grant’s Aerona R290: A next-gen heat pump designed for the Irish climate
-
Historic Dublin building retrofitted with cutting edge insulation
-
Proctor gains ground with Scottish passive schools
-
Heat pump and EV charger combo promises smart energy use
-
Unipipe celebrates 25-year NIBE partnership with new high-efficiency heat pumps
-
Full EPD Certification for Pro Clima airtightness and windtightness products