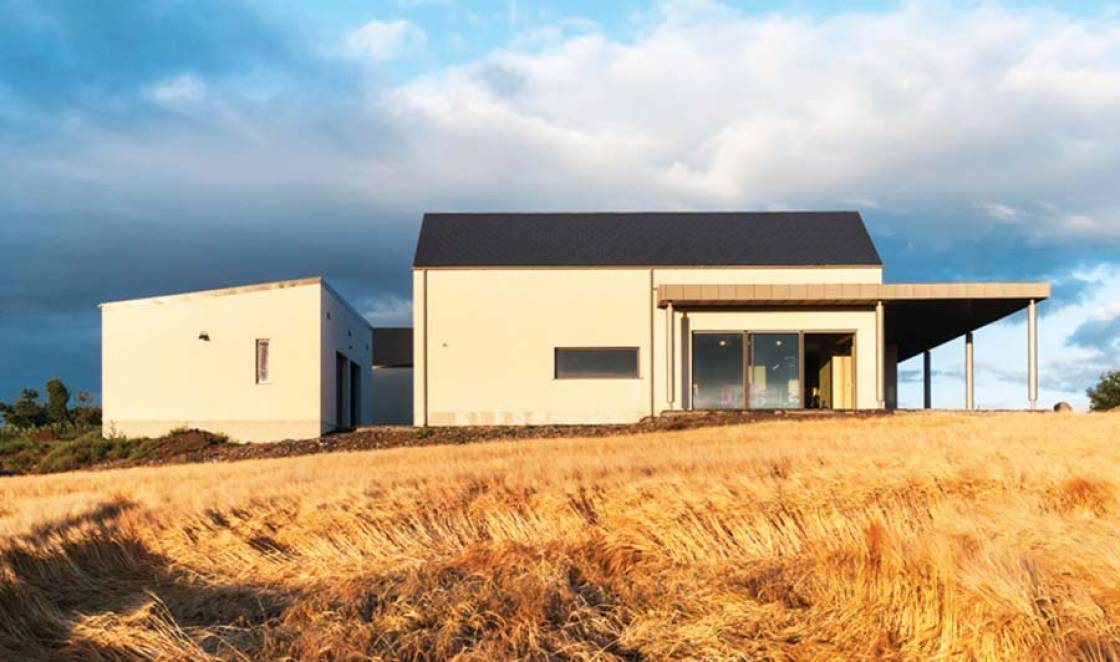
- Passive Housing
- Posted
Rise of the passive house
It could be a reflex response to the shockingly poor construction standards that came to define Ireland’s boom years, but the world’s leading low energy building standard is starting to thrive in Ireland. As the several case studies following this article reveal, a groundswell of Irish clients, designers, contractors and manufacturers are starting to recognise the opportunities available in becoming early adopters of a standard destined for exponential global growth
Irish passive house pioneer Tomás O'Leary has called for at least one Irish local authority to make the ultra low energy passive house building standard a minimum requirement for all new build.
"We could generate fantastic enterprise out of the passive house standard if somebody had the imagination to introduce at an official level," he says.
O'Leary has called for at least one local authority to follow the example Fingal County Council set in 2005, when it introduced requirements for energy efficiency and renewable energy in new domestic dwellings – requirements that were well ahead of national standards at the time.
"What I'm calling for is some far sighted local authority out there to grab this by the scruff of the neck," he says. O'Leary says such a move would help make Ireland an international pioneer in low energy construction.
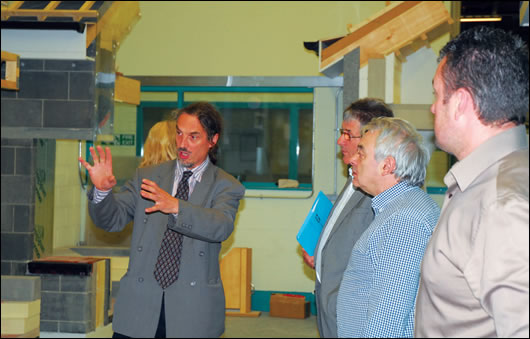
MosArt’s Art McCormack describes the minutiae of passive house at the FÁS passive house tradespeople course in Finglas
For those unfamiliar with it, passive house (or passivhaus) is a German standard of energy efficiency in buildings. Despite the name, it applies to all buildings - not just housing. If a building is certified as passive, it's essentially so well insulated and airtight that it doesn't require conventional central heating. Instead it’s mechanical heating needs can be met mainly through heat recovery ventilation, which extracts heat from outgoing stale air and uses it to pre-heat incoming fresh air.
In order to meet the standard set by the German-based Passive House Institute, a building must meet strict criteria: for example it must either have a space heating demand of less than 15 KwH/m2/yr or a heat load of 10 W/m2, while its airtightness can be no more than 0.6 air changes per hour at 50 pascals pressure.
O'Leary built the first certified passive house in Ireland, and indeed in all of the English speaking world, in 2004. He has since become renowned as Ireland's leading passive house guru. O'Leary first heard about the passive house concept at SEAI's See the Light conference in 2002.
"I was sitting in the auditorium listening to this Swedish architect talking about passive house," he says. "And I actually left my seat and phoned my wife and said, 'we're going to build a passive house.'"
Since then Ireland has become a global centre of passive house design and construction. “Passive house is easy to adapt and very cost-effective to build in Ireland’s relatively mild climate, a fact that has helped Ireland to become one of the first nations with a strong and dedicated passive house community,” says physicist Wolfgang Feist of the Passive House Institute, and one of the standard’s originators. “Since Tomás O’Leary built the first Irish passive house, Ireland has made big steps in using passive house for sustainable development and has even played a role in the standard’s further development in a variety of refurbishments, as well as with the construction of the first passive house supermarket [Tesc
o in Tramore, Co Waterford].”
The Passive House Association of Ireland is also celebrating its first year in existence. The association is a representative body for all those in the passive house construction industry, and is actively seeking interested parties to get involved. “Passive house design is one of the few areas of construction that defies the current economic times,” says its chairman, architect Martin Murray of Martin Murray Architects. “We believe that passive house design offers great prospects for international marketing, job creation and job protection, and at present Ireland is undoubtedly a market leader within the international passive house community.”
Ireland now has the second highest number of certified passive house designers in the world. "I'm really proud of that achievement," says O’Leary, whose Passive House Academy trains designers. "My hope is that these people [certified designers] will benefit in terms of their job prospects."
O'Leary and his team at the academy have also just helped the FÁS training centre in Finglas, north Dublin, devise the world's first passive house craftsmen course, which will be approved by the Passive House Institute and aimed at tradespeople.
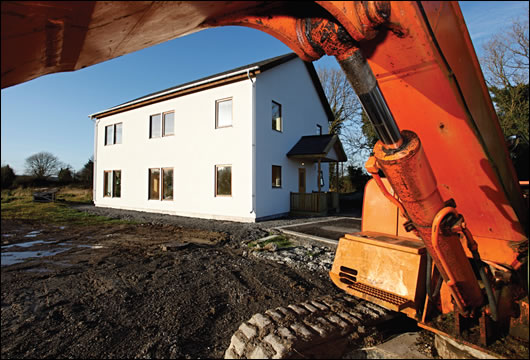
an uncertified passive house by Galway-based Scandinavian Homes in Cloughjordan, Co Tipperary
"It's been recognised that we need to start training up the builders in parallel with the architects," O'Leary says. "FÁS had a massive insight and foresight to develop that.
FÁS is currently running its first pilot of the course, which will be divided into two parts: one that deals with the building envelope, and one that's focused on mechanical and electrical components.
Martin Carroll of the FÁS training centre in Finglas says they grew interested in green building when the construction downturn hit. As well as the new passive house course, it's also led to them developing courses in solar photovoltaic and wind energy.
"We thought, why not be out there at the front? Why not be leading some of this stuff rather than chasing?" Carroll says. "The passive house was a vehicle to solve two things: to bring us up into the latest building technology, and to develop our own instructors in this green area."
"We hope they can all get work in Ireland," he says of the course participants. "That would be FÁS 's aim, but at the same time if people have to leave the country to find work, these kinds of skills should be an extra bonus to them."
Ireland's status as a passive house pioneer is underlined by the fact that the Passive House Academy is now delivering courses for passive house designers in the US, as well as certifying US buildings.
"There's a lot of expertise and knowhow here in Ireland," Tomás O'Leary says. "I think even for a small business like ourselves, it's not beyond us to think about exporting our knowhow, exporting our services. I'd say the front edge of Irish construction is 20 years ahead of mainstream construction in the US."
O'Leary is convinced the passive house standard can drive serious R&D and employment in Ireland, but stresses that its full potential can only be realised with support from the government.
"The main reason I think we should be going for passive house in Ireland is that it would give us a massive edge," he says.
He points to Irish window manufacturer Munster Joinery's launch of their Passive House Institute certified PassiV Future Proof window as one example. "You have a very large employer of 2,000 people who see passive house as the only game in town," O'Leary says.
Munster Joinery have now been followed by two other companies manufacturing Passive House Institute certified windows in Ireland under licence: Ambiwood, who are manufacturing Optiwin windows, and SmartWin.
Galway-based heat recovery ventilation manufacture Pro Air has also told Construct Ireland it is upgrading its systems to make them eligible for certification by the Passive House Institute. Meanwhile, a wide range of Irish timber frame manufacturers are now offering passive standard homes, including the likes of A-Frame, Advanced Timbercraft, Dempsey Timber Engineering, Eco Timber Frame, Greenhus, Keenan Timber Frame, Kilbroney, Kingspan Century, MBC Timber Frame Ltd, Scandinavian Homes, Shoalwater Timber Frame and SIP Energy Homes.
"I think passive house is reaching a tipping point in Ireland," O'Leary says. "We have institutions and bodies like Tesco, Irish Rail, the Department of Education, UCD, FÁS – all of these are now buying into passive house and building passive house."
One question frequently raised is how much extra it costs to hit the passive house standard compared to conventional build. Figures from 5% extra and up are frequently mentioned, but Tomás O'Leary is convinced that anyone determined to keep the cost down can make going passive "as affordable as possible".
He expects the cost of building to the passive standard to fall in the near future. "It's no longer just the one-off house in the countryside," he says. "I'm actually in no doubt that you can design out a lot of the extra expense. I think you're going to notice in the next 12 to 24 months that the extra cost of passive house will come down considerably." He says that as more passive house components are manufactured in Ireland, costs will fall.
Ireland, and indeed the world, is full of green building standards: from BER and LEED to the Code for Sustainable Homes, the Living Building Challenge, Super E and more. Indeed, critics of passive house point out that the standard takes no consideration of whether the materials used in a building are green or not - just how much energy the building uses. So why should it become arguably the most popular green building standard, at least in Ireland?
Wolfgang Feist attributes the popularity of passive house to a variety factors, such as the fact that passive is an open standard anyone can aspire to, and that it tackles common household problems relating to energy consumption, air quality and comfort. “Some 20 years of experience showing that the standard is reliable, long lasting, sustainable and well accepted by persons using the buildings,” he says.
Tomás O’Leary adds: "People are still captivated by the passive house concept. They're looking for comfort, they're interested in air quality. One of the main things is that it's actually proven. I don't know what a B1 house is like, or what a C1 house is like, but I know what a passive house is like and I know what to expect. It's a very simple concept, it applies to every part of the world and to every building."
Passive projects – past, present and future
Such is the rise in passive house construction in Ireland – with the number of certified passive projects growing every week – that attempting to exhaustively document this activity seems like an impossible task. This issue of Construct Ireland alone features thirteen buildings that have been, or are close to being, certified, and a further five that are going for the new passive house standard for retrofit, Ener PHit. And the level of activity in the passive sector is so great there were many projects we had to leave out of this issue, including two masonry projects insulated externally with Rockwool: one detached house built by self-builder Brendan Murphy in Macroom, Co Cork, plus a large extension to a nursing home in Celbridge.
Cooney Architects are currently up to wall plate level on an externally insulated house in Navan which has been put through PHPP and designed to surpass the passive house requirements, and the client may choose to go for certification.
Miles Sampson Architects are six months from completion of a cavity wall house in Ennis that will be going for certification. Sampson also has a project in for planning permission with GreenTec Ecological Homes in Craughwell that’s aiming for certified passive, low carbon construction and energy plus standard. “I have several other projects where the clients will either go passive or near passive,” says Sampson.
Mannion Passive House Builders Ltd, who have built certified passive houses in Athenry and Oranmore, have completed a development of two semi-ds in Salthill in May which has been submitted for certification, and the company has another project on site in Limerick which will be completed in June next year. “We’ve seen a big rise in interest,” says Cyril Mannion. “90% of people who contact us are interested in getting certified. It seems to be mainly because they know they’re getting a good quality product.”
Galway-based passive and low energy pioneer Lars Pettersson of Scandinavian Homes has seen a significant demand for his approach to passive building since building his passive show house in Moycullen in 2005. “I think we have 27 houses which could be certified – they’re under 10w/m2 and they’re sufficiently airtight.” Two that have been airtightness tested – Declan Cunningham’s house in Limerick and Anthony and Elaine Kelly’s two-storey house in Cloughjordan – came in under the threshold at 0.27 and 0.56 air changes per hour respectively. Scandinavian Homes currently have a nine-strong Irish crew on site in the Swedish town of Lysekil, retrofitting an 1860s building to passive standards.
The Department of Education is currently on site with two passive house schools, one in Moynalty, Co Meath, and the other in Powerscourt, Co Wicklow. Both should be completed in 2012, and were built with single leaf masonry walls and external insulation. The department's senior engineer, John Dolan, told Construct Ireland the passive schools were being built as part of the department's energy research programme, and that they would help the department figure out the extent to which passive principles can be incorporated into wider school design. “The schools are also intended to act as a "life learning tool to pupils and staff and the wider community," he says.
The Wain Morehead Architects designed passive house in Carrigaline, that featured in issue seven volume five of Construct Ireland recently gained certification. Eco Timber Frame, whose highly airtight closed panel system was critical in achieving the onerous airtightness target, are currently building a passive house in Waterford that’s achieved an impressive 0.3 air changes per hour airtightness figure. Other certified passive houses that featured previously in Construct Ireland include Tomás O’Leary’s own house, a Botanic Homes house in Killerig, Co Carlow, Michael Bennett Group’s passive show house in Rosslare, and Tesco’s eco store in Tramore.
Integrated Energy are consulting on Stephen O’Rourke’s externally insulated passive house in Portlaoise, which will also be submitted for certification. According to Archie O’Donnell of Integrated Energy, O’Rourke’s approach has influenced two other passive projects currently on site.
MosArt have two wide cavity wall houses in Roundwood currently on site which are being built to passive house specs but the clients may choose not to certify. Bob Ryan of MosArt, who are accredited to certify passive houses in Ireland – told Construct Ireland that while a complete list is unavailable, umpteen projects around the country come to mind. Ryan told Construct Ireland of twenty six houses going through the certification process currently, and another ten buildings built to passive standards but not going for passive certification. With building regulations pushing clients towards passive house thermal performance levels, there may be countless more passive projects waiting to come out of the woodwork.
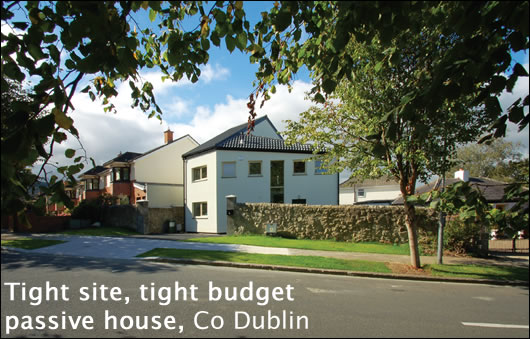
Éasca approved architect Paul McNally of The Passivhaus Architecture Company faced some unique challenges when it came to building a passive timber frame house in Ballinteer, Co Dublin — not only was the site tight, the budget was too.
“There was no money to spend on extraordinary finishes or any grand architectural gestures, we really had to go with a very simple design,” he says.
This meant occasionally sacrificing natural materials for more conventional alternatives. “We used PVC windows which some people might criticize as being an un-ecological selection,” he says. “That allows us to bring the project in on budget.” Nonetheless, the windows by Munster Joinery – who extrude PVC from a greener polymer than the old lead-based industry standard and recycle PVC mostly for cavity closers for the UK market – are certified by the Passive House Institute for their excellent energy performance.
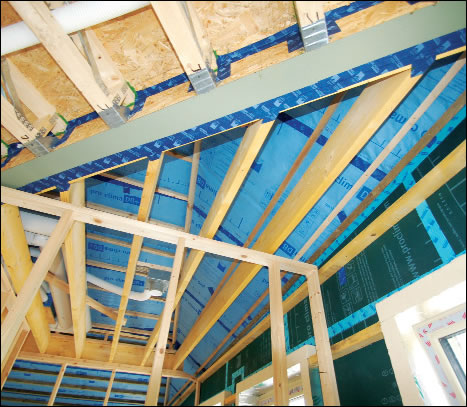
A pro clima vapour barrier and airtight membrane was installed to boost the airtightness
Dempsey Timber Engineering built the house’s timber frame, which is insulated with cellulose in the studs, Rockwool in the service cavity and Gutex Ultratherm woodfibre board — supplied by Ecological Building Systems — outside the stud. The roof features 350mm of Rockwool insulation and a further 80mm of Kingspan Aerobord Platinum EPS insulation.
The house has just gained passive house certification. The first airtightness test had failed to produce the required 0.6 air changes per hour — McNally says this was because the OSB used as part of the timber frame structure was thinner than intended, and thus more permeable to air. An airtightness membrane was then installed.
“We took the decision to put an extra layer on the inside to make sure they achieved the result,” says Stephen Duffy of Mount Carrick Environmental. The most recent airtightness test produced a result of 0.3 air changes per hour. “We knew airtightness could only be achieved by making a conscious effort at the beginning to incorporate the air layer into the structure of the building,” Duffy says. The Éasca approved contractor also supplied and installed Kingspan Thermomax solar collectors at the house.
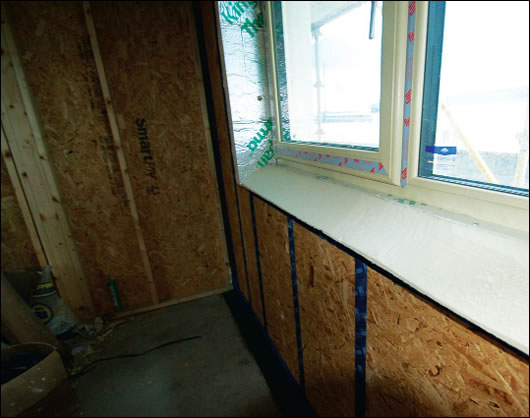
Munster Joinery Future Proof PassiV windows installed with PIR insulation surround
When it came to building their own home, energy efficiency was always a priority for homeowner Kevin Davenport and his wife Aisling, who moved in this July. “We lived abroad for a long time, and we just knew we didn’t want to build like any other Irish house. We’ve lived in too many bad Irish houses,” says Kevin. “We have two cats who will not leave this house, whereas before they would go off all the time. They’re just constantly in the house. It’s a good sign if the cats like it, I think.” Building from scratch also allowed the couple to purpose-build the house around the needs of their son, who has special needs.
"I suppose there is an impression that these are things that rich people do,” Kevin says of building a passive house. “But we had our budget, and I think it just shows it's not a vanity project. We're normal people and we're just choosing to build a house this way because ultimately we'll save the money, and for environmental reasons as well, from an ethical point of view.”
Selected project details
Architect: Paul McNally Ecological Architecture now The Passivhaus Architecture Company
Contractor: Mount Carrick Environmental
Timber frame: Dempsey Timber Engineering
Civil & structural engineering: Tanner Structural Designs
Windows: Munster Joinery
Doors: Ecoglaze
Airtightness products & Gutex Ultratherm: Ecological Building systems
Floor insulation: Aerobord Supergrund
Window surround insulation: Kingspan
Heat recovery ventilation: Pure Renewable Energy
Mechanical contractor: Real Energy
Airtightness testing: QR Energy Rating Systems
Windows and doors: Munster Joinery & Ecoglaze
External cladding: Greenspan
Rainwater harvesting: Rainharvesting Ireland
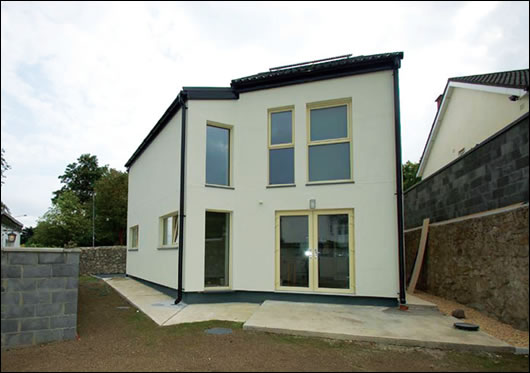
The house is situated on a very tight site
Project overview:
Building type: 136 square metre detached two-storey timber frame house with warm attic construction.
Location: Ballinteer, Dublin 18
Completion date: June 2011
Budget: Construction cost €1,600 per square metre plus vat, excluding costs associated with site preparation and completion, drainage, services connections etc
Passive house certification: certified
Space heating demand (PHPP): 13kWh/m2/year
Heat load (PHPP): 8 W/m2
Airtightness: 0.46 air changes per hour at 50 pascals pressure
BER: A3 (45.77 kWh/m2/yr)
Ground floor: Supergrund ground floor slab. 50% GGBS 100mm concrete on 300mm EPS.
U-value: 0.112 W/m2K
Walls: Greenspan Aquapanel rendered cement board externally on treated battens to ventilated cavity, 80mm Gutex Ultratherm wood fibre insulation on 200mm timber frame with cellulose insulation, 9mm smartply racking board, pro clima Intello vapour check and airtightness system with pro clima tape and grommets, 70mm service cavity with Rockwool insulation and painted plasterboard wall linings.
U-value: 0.118W/m2K
Roof: Forticrete rooftile on battens and counter-battens, on pro clima Solitex breather membrane, on 80mm Aerobord Platinum EPS insulation, on Medite Smartply racking board, on 300mm joists with full-flll Rockwool insulation, on pro clima Intello vapour barrier and airtight membrane, on 50mm service cavity with Rockwool fill and plaster ceilings.
U-value: 0.085 W/m2K
Windows: Munster Joinery PassiV Future Proof PVC windows, soft coat low-e glass, Argon gas filling. U-value ranges from 0.78 to 0.94 W/m2K. Each window installed in 90mm Kingspan Thermabate PIR insulation surround. Passive House Institute certified.
Door: Internorm Selection door
U-value = 0.79 W/m2K. Passive House Institute certified
Heating system: Victrix 23.6 kW modulating condensing gas boiler for space heating and DHW support. Distributed in Variotherm wall panels and underfloor panels. Kingspan Thermomax solar evacuated tubes
Ventilation: Paul Novus 300MVH heat recovery ventilation system with a certified efficiency of 93%
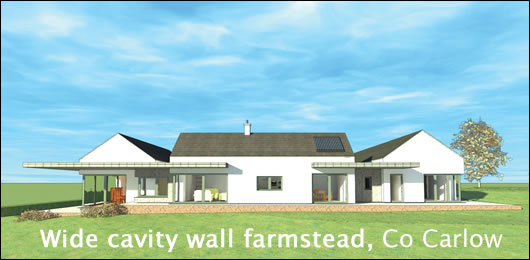
Building a passive house needn’t mean a boxy design and unconventional building methods — Tony Holden’s new house in Tullow, Co Carlow proves meeting the standard is feasible with plain old cavity wall construction and traditional Irish design.
Building a passive house needn’t mean a boxy design and unconventional building methods — Tony Holden’s new house in Tullow, Co Carlow proves meeting the standard is feasible with plain old cavity wall construction and traditional Irish design.
Holden says his main motivation for going passive was quality — he saw passive certification as a guarantee his would be well built. "It's not that I'm a green fanatic," he says. "The main reason I'm building a passive house is that it's a quality control stick. It's a standard I can test. I've got good metrics to ensure my house is as it's supposed to be."
He plans to get the house certified by the Passive House Institute as soon as possible. "That's everyone's final destination on the job," he says. "It's not something we're going to leave on the long finger for a year or two."
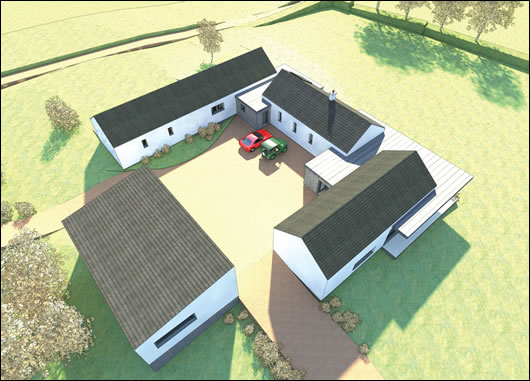
The house is constructed in four sections, evoking a traditional farmstead
He was open to different construction methods, and sought tenders for cavity wall, timber frame, and single leaf concrete block construction. But the cavity wall always came back cheapest. "I wouldn't have built a passive house if it was going to cost me too much," he says. The wall cavity features 300mm of Korefill bonded bead insulation, with 500mm Isover Metac insulation in the roof. All windows and doors are Passive House Institute certified Pazen Premium Maxi units.
“The design of the house wasn't ideal for hitting the passive house standard,” says Tracey Sludds of architects OLS. “The client stipulated from the start that the design should take precedence over the building's performance. Albeit that we wanted to reach the passive house standard, he was not willing to sacrifice or compromise on the overall aesthetic of the house.”
Sludds says the house’s U shape proved a challenge to reaching the passive house standard. “Not only does it look like a traditional Irish farmstead but the design could only achieve the passive house standard in Ireland's milder climate. This house design would not reach the standard if it was in central Europe."
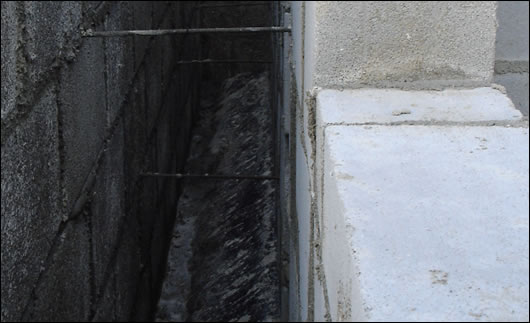
The building pushes the boundaries of cavity wall construction – a 300mm wide insulation void with Ancon Teploties reducing cold bridging
Selected project details
Client: Tony & Siobhan Holden
Architect: OLS Architects
Civil / structural engineer: Peter Bolger Consulting
Main contractor: American Timber Frame Houses
Wall & floor insulation: Kore Insulation
Airtightness products, roof insulation & additional wall insulation: Isover
Windows and doors: Pazen Ireland
Airtightness tester: Integrated Energy
Project overview:
Building type : 295 square metre detached stepped single-storey house, with a wine cellar attached and a workshop detached. The build method is infill cavity construction with timber A-frame pitched roof.
Location: Tullow, Co Carlow
Completion date: September 2011
Passive house certification: pre-submission
Space heating demand (PHPP): 15 kWh/m2/yr
Heat load (PHPP): 10 W/ m2
Airtightness: target 0.30 air changes per hour at 50 pascals pressure. Initial airtight test is due to be carried out on the shell and core in two weeks. Due to the building design, location and climate constraints, this house requires a more onerous air tightness level than standard passive houses. While the passive house limit is 0.6 air changes per hour at 50 pascal pressure, this house must achieve a better value of 0.3.
BER: Pending
Ground floor: Viking insulated concrete raft foundation, insulated with 400mm of EPS Kore insulation with Rhinoplast Ultra Radon barrier.
U-value: 0.09 W/m2K
Walls: 15mm Weber render to 100mm Cemex dense block external leaf, 300mm cavity filled with Korefill bonded bead insulation with Ancon basalt Teplotie wall ties, 150mm Quinn-Lite Aircrete block to inner leaf, with Gypsum Airtite Quiet parge coat, 75mm insulated service cavity, vapour barrier, 12.5mm Gypsum plasterboard with skim finish.
U-value: 0.09 W/m2K
Pitched Roofs: Capco fibre cement slates externally on treated timber battens/counter battens, followed underneath by breathable roofing underlay, to DTE timber roof truss, with 500mm Metac insulation between joists, Vario vapour barrier, 18mm taped & sealed Smartply OSB, 150mm uninsulated service cavity, 12.5mm Gypsum plasterboard ceiling with skim finish.
U-value: 0.08 W/m2K
Flat Roofs: VMZinc Plus Quartz zinc standing seam externally, followed underneath by breathable roofing underlay, on WBP plywood support, on treated timber fillet battens to create fall and ventilation, on 250mm treated timber joists/counter joists in-filled with Metac insulation followed underneath by Vario vapour barrier, 18mm taped & sealed Smartply OSB, 150mm uninsulated service cavity, 12.5mm Gypsum plasterboard ceiling.
U-value: 0.08 W/m2K
Windows: Pazen Premium Maxi triple-glazed aluminium-clad Eucalyptus hardwood windows, with argon filling and an overall U-value of 0.77 W/m2K
Heating: back-up heat source via a heater battery mounted in line with the supply air duct from the heat recovery ventilation unit. The system is currently under review.
Ventilation: Paul Novus 300 heat recovery ventilation system — Passive House Institute certified to have heat recovery rate of 93%, and an electrical efficiency of 0.24 Wh/m3
Green materials: Pazen Eucalyptus hardwood windows, Isover recycled glass mineral wool roof insulation, reclaimed oak timber plank flooring, Tretford eco backed carpet, Dulux zero VOC eco paint, all roof timbers from PEFC certified sources.
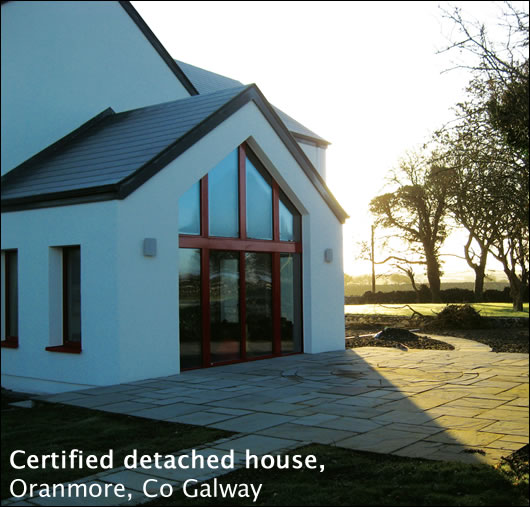
Galway-based Mannion Passive House Builders are steadily building a reputation as one of the country's foremost passive house contractors. The company finished its latest project — in Oranmore, Co Galway — earlier this summer.
"It has been certified [by the Passive House Institute] but I won't have the cert in my hand until 6 September," says Cyril Mannion of Mannion Passive House Builders.
A fairly typical two-storey detached rural Irish home, the house’s walls were constructed with concrete block and 250mm of Atlas EPS external insulation. The roof features 500mm of cellulose insulation, while the ground floor boasts 300mm of EPS. The windows are Optiwin triple-glazed aluminium-clad larch units with argon filling. The house also has a Paul Thermos 300DC heat recovery ventilation system, which is certified by the Passive House Institute to have a heat recovery rate of 89%.
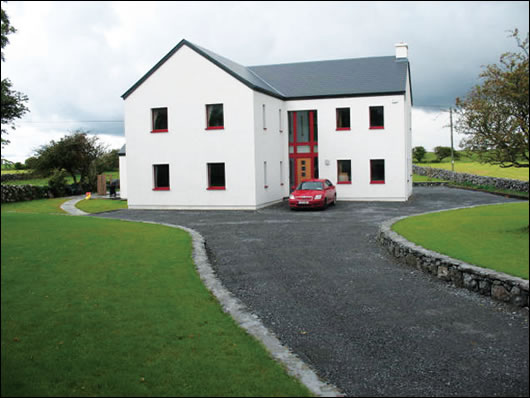
The house’s heavily externally insulated exterior give it a substantial feel. Optiwin triple glazed larch windows were used throughout, with an overall U-value of 0.85 W/m2K
A 92% efficient Grant Vortex condensing oil boiler also features. Mannion says that during the cold snap last winter the boiler "came on every three days for only twenty minutes." Though it was freezing cold on Christmas Day, the combination of bright sunshine, a full house and a hot oven meant the occupants had to open windows to cool down inside.
Passive House Builders have also completed a passive house project nearby in Athenry, Co Galway. "You hear a lot of people talking about passive house round and about," Mannion says. "It is catching on. Unfortunately people are still coming to us a little late [in the design stage]. I mean it's never too late, but if you come earlier, there are savings to be made."
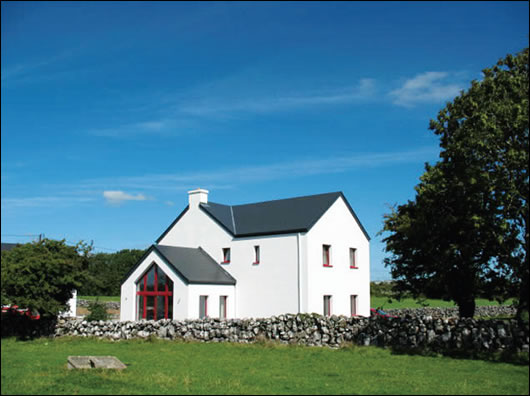
Selected project details
Contractor: Mannion Passive House Builders
Architect: Shane Hanniffy & Associates
Windows: Optiwin
Heat recovery ventilation: Pure Renewable Energy
Oil boiler: Grant Engineering
Mechanical contractor: Pro Air
Airtightness testing: Energy Matters
Floor insulation: Aerobord
Airtightness products: Siga
Project overview:
Building type : Detached two story dwelling house, 240 square metres approximately, built using masonry and external insulation
Location: Oranmore, Co Galway
Completion date: June 2010
Budget: €300,000
Passive house certification: certified
Space heating demand (PHPP): 15 kWh/m2/year
Heat load (PHPP): 10 W/m2
BER: B1 (74.6 kWh/m2/yr)
Airtightness: 0.54 air changes per hour at 50 pascals pressure
Ground floor: Insulated raft foundation with 300mm EPS insulation.
U-value: 0.11 W/m2K
Walls: masonry build with 250mm of external insulation.
U-value: 0.11 W/m2K
Roof: standard cut roof with 500mm of cellulose insulation, membrane taped & sealed, 50 mm uninsulated service cavity, 12.5mm plasterboard ceiling.
U-value: 0.10 W/m2K
Windows: Optiwin triple-glazed aluminium-clad larch windows, with argon filling and an overall U-value of 0.85 W/m2K
Heating system: 92% efficient Grant Vortex condensing oil boiler supplying underfloor heating and 300 litre buffer tank, plus 30 Joule solar vacuum tubes supplying separate 300 litre domestic hot water tank
Ventilation: Paul Thermos 300DC heat recovery ventilation system — Passive House Institute certified to have heat recovery rate of 89%
Green materials: cellulose insulation, all timber FSC certified sources, 55% GGBS cement
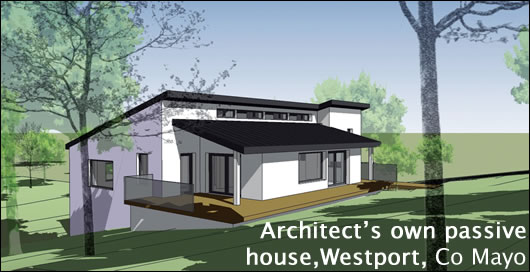
One thing about passive house that’s frequently debated is the price — how much extra does it cost compared to conventional build to go passive? Figures of between zero and 20% are frequently thrown about, though it’s usually stressed that with the extraordinarily low heating costs, any extra outlay can be recouped.
Trying to make a passive house as affordable as possible, one Mayo-based architect decided to build her own to the passive House standard.
“We’ve got Oak Barn Construction to do the main structural aspect but we’re basically finishing it off ourselves in order to manage the high specification within our budget,” says Cuala McGann of McGann Scahill Architects.
“I’ve been interested in the passive house standard for quite some time, and being a certified passive house designer, I’m seeing this as an opportunity to put it into practice,” she adds.
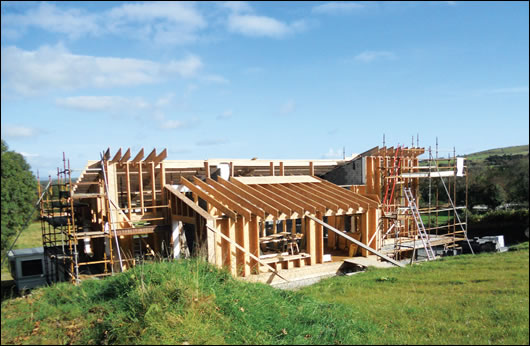
The stick built timber frame structure
McGann says it’s difficult to know how much extra aiming for passive will add to the final cost of the project. “When I finish this exercise I’ll be able to put it in exact numerical form,” she says.
She reckons that if one stays true to the spirit of the passive house standard by not installing a conventional central heating system, going passive shouldn’t cost more than 5% extra.
McGann chose the stick-built timber frame system from local contractor Oak Barn for the project. “We were basically looking to go with a breathable construction, and we wanted to work with Oak Barn Construction,” she says.
“She wanted to have her own house as passive, partly to show clients that you can achieve this,” says Oak Barn’s Willie McDonagh. The company stick-built the timber frame structure with I-beams. “The advantage of that was that we were able to get wider walls [meaning more insulation], and less cold bridging.”
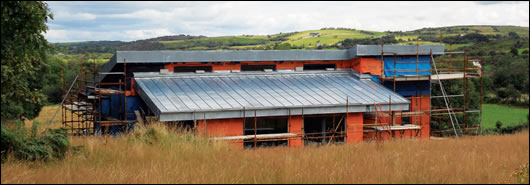
Natural zinc roofing
The walls of the house feature 160mm of Gutex woodfibre insulation externally, with 300mm of cellulose between the studs and an insulated 100mm service cavity. The roof includes 360mm of cellulose plus 170mm of woodfibre insulation in the service zone. Optiwin triple-glazed Passive House Institute certified windows also feature throughout.
“That’ll be the highest spec that we have worked to,” Willie McDonagh says. “The walls were massive but it wasn’t difficult to work with.”
McGann plans to get the house certified by the Passive House Institute. She says that this project has been “good in terms of professional experience.” She adds: “We’re using it as an opportunity to apply the passive house standard to an architectural design.”
Selected project details
Client: Cuala McGann & Olivier Bauduin
Architect: McGann Scahill Architects
Civil / structural engineer: Structural Design Services
Main contractor: Oak Barn Construction
Wall insulation, roof insulation & airtightness products: Ecological Building Systems
Windows and doors: Optiwin
Mechanical & electrical contractor: Ecowest
Project overview:
Building type : 204 square metre detached two-storey timber frame house
Location: Westport, Co Mayo
Completion date: under construction 2011
Passive house certification: pre-submission
Space heating demand (PHPP): pending
Heat load (PHPP): pending
Airtightness: max. 0.60 air changes per hour at 50 pascals pressure
BER: pending
Ground floor: raft foundation insulated with 200mm Kingspan insulation under-slab, 35mm insulation over-slab.
U-value: 0.12 W/m2K
Walls: stick-built I-Joist timber frame: render finish on render carrier board on treated SW battens on Solitex facade membrane, 160mm woodfibre board, 302mm timber I-joists fully filled with cellulose insulation, 18mm taped and sealed OSB, 100mm insulated service cavity and 12mm plaster carrier board internally.
U-value: 0.07 W/m2K
Roof: natural zinc finish on 18mm OSB on 50x35 treated SW battens on Solitex-Mento breathable roofing membrane, on 35mm Gutex-Multiplex woodfibre insulation, on 360mm timber I-joists fully filled with cellulose insulation, 18mm taped & sealed OSB, 170mm woodfibre insulation service zone, plastered finish.
U-value: 0.07 W/m2K
Windows: Optiwin triple-glazed aluminium-clad timber windows, with argon filling and an overall U-value of 0.73 W/m2K
Heating system: wood insert stove (pending) supplying heating coil on HRV and 300L buffer tank, plus solar vacuum tubes (pending) supplying separate 300L domestic hot water tank
Ventilation: heat recovery ventilation system (pending) - Passive House Institute certified to have heat recovery rate of 92%
Green materials: timber frame, cellulose insulation, woodfibre insulations, 50% GGBS cement, rainwater harvesting system & water conserving fittings (both pending)
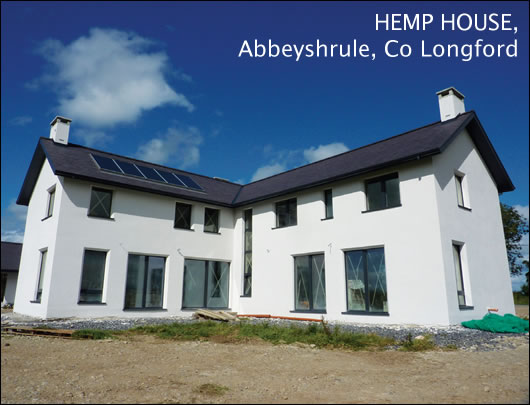
One ambitious self-builder in Co Longford is doing much of the construction work for his passive house — and he's doing it with a highly ecological hemp lime and timber frame system. "I'm doing nearly everything," says James Byrne, a mechanical engineer by trade. "I'm doing most of the technical stuff, it's a baptism of fire."
Byrne is building the house using the Tradical Hemcrete hemp-lime system from UK-based Lime Technologies. The walls of the house feature a timber frame — built by Meath-based A-Frame — with 600mm of the Tradical mix. Byrne has installed the hemp-lime himself, having mixed it on site and poured it into timber shuttering he made. Once one layer has dried he removes the shuttering, places it on top of the dried hemp lime mix below, and pours the next layer. Byrne first constructed a garage with the Tradical system to make sure he got the mix right.
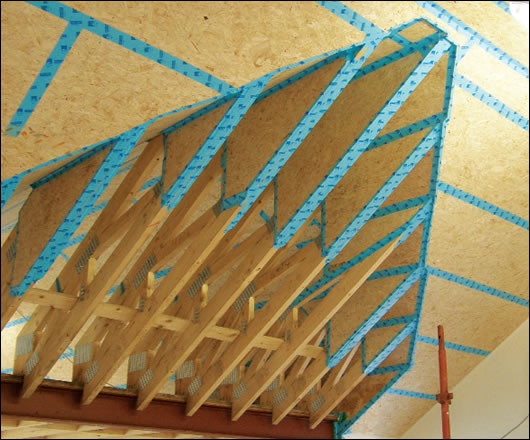
Meticulous airtight roof detailing
"The wall build is breathable," Byrne says. Wet plastering on the inside of the walls serves as the airtightness layer — the most recent blower door test produced a result of 0.53 air changes per hour. The house also features low carbon GGBS cement in its foundation and 12.5 square metres of flat plate solar panels.
Conor Doherty of timber framers A-Frame says the only difference between hemp-lime and conventional timber frame was calculating the loads and weights.“It’s really just the engineering – that’s the only difference,” he says.
“The other thing is the truss design we did,” he says. “It’s a double rafter, it’s a vaulted truss. It’s the first time we’ve done it like that. We need that depth to get 400mm of insulation.”
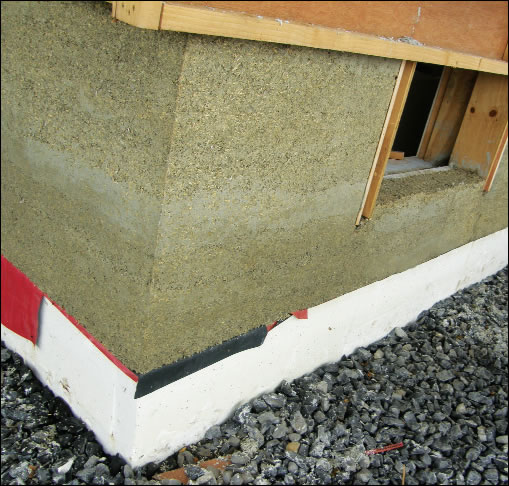
The first pour advancing
Architect Zeno Winkens —who also has straw bale and poroton builds in the Wexford area to his list of credits — designed the building. "I looked into it a good bit and I'm quite pleased with it," Winkens says of hemp-lime construction. "I'd definitely do another one."
Selected Project Details
Architect: Winkens Architecture
Civil engineer: Carraig Consulting
Airtightness testing: Green Build
Timber frame: A-Frame
Hemp-lime system: Lime Technology
Heat recovery ventilation: Pure Renewable Energy
Cellulose insulation: Warmcel, installed by Cosycel
Windows: Optiwin
Floor insulation: Airpacks
Airtightness products: Proline Hardware
Solar thermal: GoSolar
Stove: Kildress Plumbing Suppliers
Foundations: Viking House
Reed bed: Herr Ltd
Project overview:
Building type : 335 square metre detached two-storey Tradical Hemcrete house
Location: Abbeyshrule, Co Longford
Completion date: October, 2011
Budget: €400,000
Passive house certification: pre submission
Space heating demand (PHPP): 15 kWh/m2/year
Heat load (PHPP): 10 W/m2
BER: pending
Airtightness: 0.53 air changes per hour at 50 pascals pressure (initial test result)
Ground floor: insulated ring beam (passive slab from Viking House) with 300mm platinum EPS100. U-value: 0.096 W/m2K
Walls: factory-built 38x140mm@600 centres timber frame with 2mm Baumit SEP02 render externally, followed inside by 15mm Baumit FL68 base coat, 450mm Tradical Hemcrete, 9mm Resistant Multi-Pro Magnesium Silicate board, 4mm Baumit MC55W and 2mm Baumit KG30 skim coat internally. U-value: 0.131 W/m2K, (manufacturer’s figure) / 0.155 W/m2K (Passive House Institute figure). The reason for this discrepancy is that Tradical Hemcrete is not a rated material, so the institute adds 20% to the lambda value
Roof: Bangor Blue slates externally on 50x35 battens/counter battens, followed underneath by 18mm Hunton Undertak bitumen impregnated woodfibre sarking board, 450mm parallel chord roof truss filled with cellulose insulation, 18mm taped & sealed OSB3, 125mm uninsulated service cavity, 10mm fermacell ceiling. U-value: 0.093 W/m2K
Windows: Optiwin Alu2Wood triple-glazed aluminium-clad windows, with argon filling and an overall U-value of 0.78 W/m2K
Heating system: 78% efficient ESSE wood-fired cooker and five SolvisCala solar thermal collectors supplying 950L SolvisMax thermal store supplying air battery heater and bathroom wall heating
Ventilation: Paul Santos 370DC heat recovery ventilation system — Passive House Institute certified to have heat recovery rate of 84% / EN 308 certified efficiency of 92.7%
Green materials: Tradical Hemcrete, Resistant Multi-Pro Magnesium Silicate board, Fermacell dry lining board, cellulose insulation, 40% GGBS cement, Biofa paints
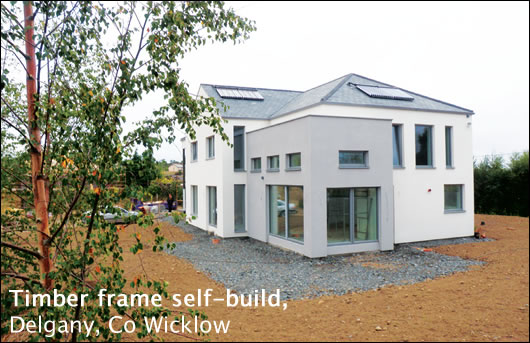
Justin O'Keeffe and his wife spent years watching the development of the passive house in Ireland before deciding to build one for themselves in Delgany, Co Wicklow.
"I've been a subscriber to Construct Ireland for years," O'Keeffe says. "I remember seeing photos of Tomás O'Leary's house [the first passive house in Ireland] when it was being built."
O’Keeffe decided to build passive because he sees the standard as a guarantee of quality: "It's the most measurable standard out there, it's field tested."
But he reckons there's a penalty in terms of cost — about 15 to 20% extra, he estimates. "But once you do it, the running costs are dramatically lower,” he says.
O'Keeffe — now a certified passive house designer himself — chose a timber frame system from Kilbroney Timber Frame for the build. The walls feature two separate studs, each filled with fibreglass batts — one 90mm, the other 150mm — and separated by an empty cavity to eliminate thermal bridging. “Making sure the two walls weren’t touching was extremely important,” says Mark Cooper of Kilbroney Timber Frame.
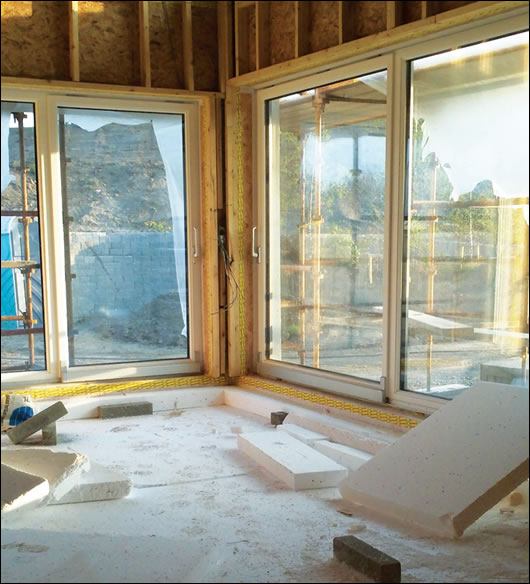
400mm of EPS insulation being installed in the floor
The service cavity in the walls boasts another 100mm of fibreglass, while the roof features a total of 305mm of fibreglass plus 80mm of rigid Kingspan insulation. OSB board serves as the airtight layer in the walls, while a Siga Majpell membrane feature in the roof. “We’ve made the building windtight as well as airtight,” Cooper says.
The house is heated by an air-to-water heat exchanger in the heat recovery ventilation, which collects heat from a hot water cylinder that's fed by both the solar collectors and a gas boiler. Pazen Ireland supplied the house’s Passive House Institute certified triple-glazed windows.
O'Keeffe is planning to move in in September, having managed the project and done much of the labour himself. "We've self-built because you get that better attention to detail, and the quality standard you build to is your own quality standard. When you're self-building you go and get the right materials, you go and get the right people, and then you watch to make sure it's done."
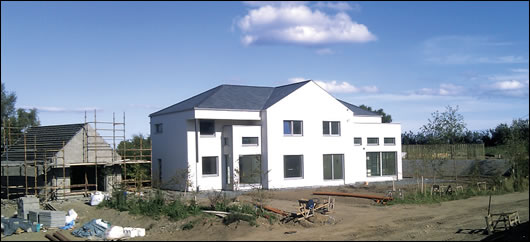
Sun catches the monocouche rendered façade
An airtightness test produced a result of 0.58 air changes per hour. "It's such a large house, there's a lot of surface area. Your surface area to volume ratio probably isn't as favourable as a simpler design would be,” says Ann-Marie Fallon, passive house consultant on the project. “Achieving airtightness of 0.6 would probably be more of a challenge with a house of this scale than with something more compact or simple in shape."
Baker Insulation supplied and installed most of the insulation and airtightness products on the job. "Justin was a guy who knew what he wanted and what the result had to be," says the company's Mark Baker, who adds that he sees more and more ambitious homeowners driving an energy efficiency agenda now than during the building boom.
Baker Insulation’s final payment was dependent on the house achieving the required airtightness result. "We got it, and for us it was a great satisfaction," he says.
Selected project details
Client: Justin O’Keeffe & Nikki Evans
Civil/structural engineer: Donnolly Troy Associates
Energy consultant: Ann-Marie Fallon
Mechanical contractor: M&P White Plumbing Services
Electrical contractor: Marathon Electrical
Airtightness tester: 2Eva.ie
Build system supplier: Kilbroney Timberframes
Insulation & airtightness installer: Baker Insulation
Windows and doors: Pazen Ireland
Airtightness products: Siga
Condensing boiler & solar thermal: RVR
Heat recovery ventilation: BEAM Central Systems
Cladding supplier: REP Ltd
Roof lights: Velux
Lighting: Smartlight
Rainwater harvesting: Carlow Precast Concrete
Project overview:
Building type: 350 square metre detached two-storey timber frame house
Location: Wicklow
Completion date: September 2011
Passive house certification: pre-submission
Space heating demand (PHPP): 12 kWh/m2/year
Heat load (PHPP): 10 W/m2
Airtightness: n50 of 0.58 air changes per hour at 50 pascals pressure & depressurisation to EN13829
BER: pending
Ground floor: raft foundation insulated with 400mm EPS.
U-value: 0.10 W/m2K
Walls: Kilbroney Timberframes double factory-built timber frames with Parex Lanko monocouche system, treated battens and ventilated external cavity and facade membrane on 9mm Panelvent. Followed inside by 90mm stud, thermal break, 150mm stud – all completely filled with fibreglass batts, 18mm Smarptly OSB3 as the airtight layer sealed with airtightness tapes, 100mm service cavity insulated with fibreglass batts.
U-value: 0.1 W/m2K
Roof: warm roof construction. Capco natural slates on battens/counter battens, followed underneath by breathable roofing underlay on 9mm Panelvent, 220mm timber joists filled with fibreglass batts, 175mm rafters with fibreglass batts, Majpell airtight layer, 80mm insulated service cavity with Kingspan rigid insulation, 12.5mm plasterboard ceiling.
U-value: 0.1 W/m2K
Windows: Pazen premium maxi triple-glazed alu-clad eucalyptus windows, with argon filling, Passive House Institute certified and an overall U-value of 0.77 W/m2K.
Heating system: Victrix condensing gas boiler & 12m2 of Calpak Solar Vacuum Tube Panels feeding a 1000L TiSun Proclean stratified tank.
Ventilation: Dantherm HCH8 counter-flow heat recovery ventilation system — Passive House Institute certified to have heat recovery rate of 83%. Includes in line water-to-air duct heater & summer bypass
Green materials: 10,000L precast rainwater tank, water treated for domestic use
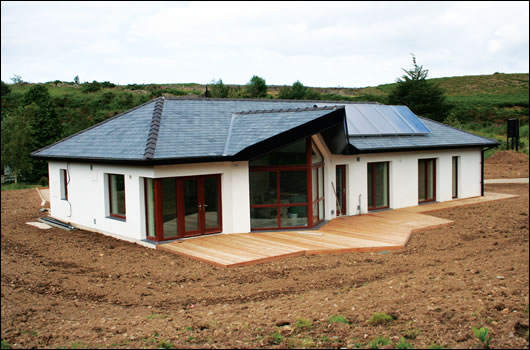
Leontine Binchy was inspired to build a passive house by her time living in Germany. “The houses are just so well insulated there,” she says. “You’d generally be warm enough in a t-shirt and shorts in the middle of winter.”
She heard Irish passive house guru Tomás O’Leary speaking on the radio one morning, and her interest was piqued. “We read up on it, and it seemed to make sense,” she says.
She was just in the process of moving into her new passive bungalow in Enniskerry, Co Wicklow when Construct Ireland spoke to her.
MBC Timber Frame supplied the build system used for the house, which was designed by leading passive house architects MosArt. The walls feature a 100mm stud insulated with Isover Metac glasswool insulation, with taped and sealed 12mm OSB board outside the stud forming the airtight layer, and a further 200mm of platinum EPS insulation outside the OSB. “It's like a blanket wrapped around the house with 300mm of insulation,” Peter Crossan of contractor Stanhurst Limited says of the build-up.
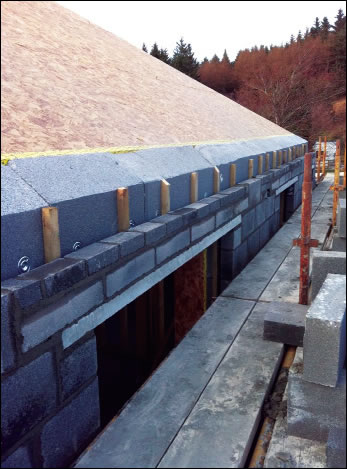
200mm Platinum EPS external insulation cut level with the roof pitch
Putting the airtight layer outside the main stud, which is also the service cavity, means it can’t be accidentally punctured from inside the house, Crossan explains.
The roof features an almost identical insulation spec as the walls, while the house features the Viking House insulation raft foundation system, which is certified by the Passive House Institute. The house also boasts Passive House Institute certified triple-glazed Future Proof windows from Munster Joinery.

Siga tapes applied to the OSB
The house has two other innovative technologies from Viking House. The first is two duct-free fine wire (FiWi) copper heat recovery ventilation systems.
O’Loughlin told Construct Ireland that he’s started the process of getting the units certified by the Passive House Institute. “The initial testing is showing that it’s one of the most efficient HRV units out there,” he claims.
He explains how the units work: “The air flows in and out through wires and the two air streams don’t mix, but the temperature is transferred through the copper wire. There’s about 20km of copper wire in each heat exchanger. There’s a huge surface area. We’re getting excellent return air temperatures and they’re delivering excellent air quality.”
“The fact that the copper wire is so conductive and the wires are so fine allows the heat exchanger to be so compact,” he says. “There’s also no issue with having to clean ductwork.”
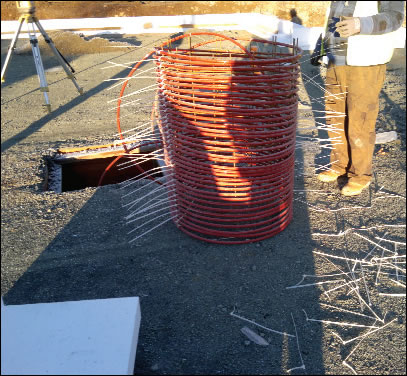
Coiled pipe for storing solar hot water in the Viking House floor slab
Another Viking House technology used on the project is a 90 square metre solar slab of sand and gravel under the building that inter-seasonally stores hot water produced by the 12 square metre array of evacuated tubes, releasing the heat slowly to heat the house over the winter. The slab sits above the main layer of insulation in the foundations in order to minimise heat loss.
Selected project details
Architect: MosArt
Main contractor: Stanhurst
Civil / structural engineer: Tanner Structural Design
Build system supplier: MBC Timber Frame
Quantity surveyor: Brian Gubbins
Windows and doors: Munster Joinery
Wall insulation, floor insulation: Airpacks
Solar thermal supplier: Kingspan Renewables
Roof insulation: Isover
Mechanical contractor, underfloor heating, heating controls & rainwater harvesting: Aqualex
Passive house consultant, main OSB, solar slab & heat recovery ventilation: Viking House
Airtightness products: SIGA
Airtightness tester: 2Eva.ie
Screeds: Fast Floor Screeds
Electrical contractor & lighting controls: 3G Electrical
Project overview:
Building type : 165 square metre, detached single-storey timber frame dwelling
Location: Enniskerry, County Wicklow
Completion date: August, 2011
Budget: €300,000
Passive house certification: pending
Space heating demand (PHPP): 14 kWh/m2/year
Heat load (PHPP): 10 W/m2
Airtightness: 0.56 air changes per hour at 50 pascals pressure
BER: B1 (78.68 kWh/m2/yr)
Ground floor: Viking House insulated raft foundation system with 300mm EPS insulation, 500mm compacted hardcore with solar slab heating pipes, 150mm concrete floor slab, 100mm EPS insulation, underfloor heating pipes in 75mm concrete floor screed.
U-value: 0.084 W/m2K
Walls: 100mm concrete blockwork with render finish externally, 50mm ventilated cavity, 200mm platinum polystyrene insulation mechanically fixed to 12mm OSB board taped and sealed to form airtight seal, fixed to 100mm factory-built timber frame with 100mm Isover Metac insulation fitted between timber studs, 12.5mm plasterboard and 3mm skim finish to internal.
U-value: 0.117 W/m2K
Roof: natural roof slates externally on 50x35mm battens and counter battens, followed underneath by breathable roofing underlay, 200mm platinum polystyrene insulation mechanically fixed to 12mm OSB board taped and sealed to form airtight seal, fixed to 175mm factory-built timber roof trusses with 100mm Isover Metac insulation fitted between timber rafters, insulated on the slope.
U-value: 0.118 W/m2K
Windows: Munster Joinery PassiV Future Proof triple-glazed, argon-filled, timber eco passive windows and doors.
Overall U-value of 0.80 W/m2K
Heating system: Viking House solar slab connected to 12m2 of evacuated tubes solar panels on roof, buffer tank with immersion back-up and underfloor heating pipes in concrete floor screed.
Ventilation: Viking House fine wire heat recovery ventilation system
Electricity: standard connection with night rate electricity supply
Green materials: timber cladding used externally, natural roof slates, OSB 3 used throughout, timber windows and doors
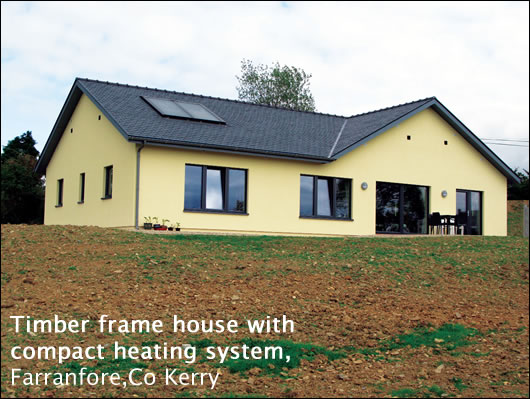
The passive house concept appealed to John O'Sullivan the first time he came across it. "I liked the idea from the point of view of comfort and the lifestyle," he says. "It struck a chord with me."
That was two years ago, and O'Sullivan has been reading Construct Ireland ever since as he has embarked on a construction journey that saw him move into his new passive house outside Farranfore, Co Kerry two months ago. He's even a certified passive house designer now.
O'Sullivan chose leading low energy timber framers Shoalwater for the project. "I've seen timber frame in Europe. It's there 200 or 300 years and the buildings are still standing," he says. "I thought the construction method was just much more effective.”
The walls of his house feature 80mm of Gutex woodfibre board, plus a total of 270mm of cellulose insulation. The roof features 450mm of cellulose, while the ground floor is insulated with 320mm of Kingspan Kooltherm insulation. “John was very motivated and decisive,” says Shoalwater’s Donal Mullins. “If the people on board are as motivated as you, you generally don’t get any problems.”
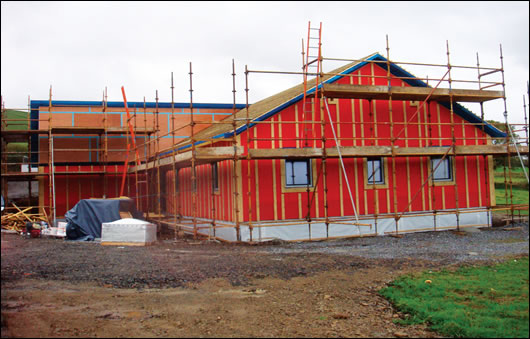
The battened walls ready for Aquapanel cement fibre board cladding
Windows are Pazen Premium Maxi Passive House Institute certified triple-glazed units, made with eucalyptus hardwood and clad in aluminium. Nilan Ireland supplied the house's heating system, a Passive House Institute certified Nilan P Compact heat pump, the first installed in Ireland. The unit extracts energy from the exhaust air in the house and uses it to heat both domestic hot water and fresh incoming air. The system also features a geothermal element, though this has yet to be used.
Nilan's Maurice Falvey points out that while standalone heat recovery ventilation will dump exhaust heat to the outdoors once the desired indoor temperature has been reached, the Nilan Compact instead uses this energy to heat domestic hot water. The unit is supplemented by two Wikora flat plat solar collectors. To test the performance of the ventilation and monitor indoor air quality in a passive house, both humidity and carbon dioxide levels in the house are being measured on an ongoing basis.
Stephen Young of Young Design Build, energy consultants on the project, said the house will go for full passive certification. "That was the goal from the start,” he says.
Young points out that because the Passive House Institute certification of the Nilan unit is not recognised by SEAI – meaning default values for its efficiency must be entered when calculating whether the house complies with Part L of the building regulations – solar panels were required in order to meet the renewables requirement in the regs.
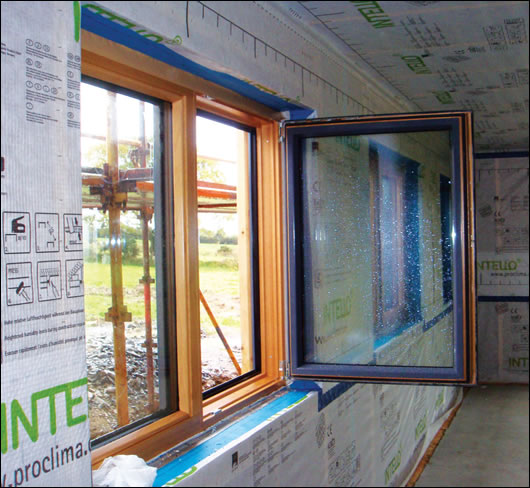
Premium Maxi Passive House Institute certified windows and Pro Clima airtightness system
O'Sullivan had just moved in as Construct Ireland went to print. The house hasn’t been tested by the winter cold yet, but nonetheless his verdict is emphatic: "There's no comparison from the point of view of lifestyle and quality of environment."
Selected project details
Client & project management: John O'Sullivan
Main contractor: Self-build with assistance from Donnie O'Shea
Build system supplier: Shoalwater Timber Frame
Insulation & airtightness products: Ecological Building Systems
Floor insulation: Kingspan
Insulation contractor: Clioma House
Windows and doors: Pazen Ireland
Mechanical contractor / boiler & heat pump supplier: Nilan Ireland
Solar thermal supplier: Wikora
Airtightness tester: Greenbuild
Energy consultant: Young Design Build
Project overview:
Building type : 185 square metre detached single-storey timber frame house
Location: Scart, Farranfore, Co Kerry
Completion date: June 2011
Passive house certification: pre-submission
Space heating demand (PHPP): pending
Heat load (PHPP): pending
Airtightness: 0.56 air changes per hour at 50 pascals pressure
BER: pending
Ground floor: strip foundation with rising Quinnlite blockwork, externally insulated with Aerofloor insulation to reduce thermal bridging. Concrete screed insulated with 320mm Kingspan Kooltherm insulation above concrete slab.
U-value: 0.064 W/m2K
Walls: factory-built timber frame with thin coat render to 12.5mm Greenspan Aquapanel cement board, followed inside by 38x90mm treated battens, 80mm Gutex ultratherm insulation, 9.2mm Panelvent sheathing board, 220mm cellulose-filled timber stud, airtightness membrane, 50mm service cavity insulated with Thermo-Hemp insulation, and 15mm Fermacell plasterboard internally.
U-value: 0.133 W/m2K
Roof: Gallagas natural (Spanish) slate externally on 50x35mm battens, followed underneath by breathable roofing underlay, 450mm cellulose insulation to attic space, truss roof, airtightness membrane, 50x38mm uninsulated service cavity, 10mm Fermacell plasterboard ceiling.
U-value: 0.96 W/m2K
Windows: Premium Maxi Passive House Institute certified windows by Pazen – triple-glazed alu-clad eucalyptus hardwood windows, with argon filling.
Overall U-value: 0.74 W/m2K for all windows and doors
Heating system: Nilan VP18 JVP Compact Passive House Institute certified heat pump unit with an integral 180 hot water tank, supplemented by two Wikora Wikosun 2340Ti flat plate solar collectors supplying separate 300L buffer tanks. The collectors have been successfully integrated with the Nilan system by having a hot water draw-off coil through the solar buffer tank feeding into the Nilan unit. On a hot day when the solar buffer tank has been heated sufficiently by the solar panels, the heat pumps aren’t required for heating water
Ventilation: the Nilan heat pump also provides heat recovery ventilation
Green materials: timber frame, cellulose insulation, Gutex ultratherm insulation, Thermo-Hemp insulation, Fermacell plasterboard, FSC certified eucalyptus hardwood windows
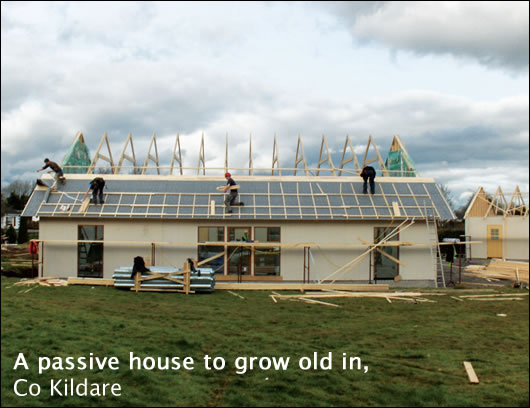
When Micheál Byrne started to research building his own passive house a few years ago, he had no idea it would lead him to become a certified passive house designer.
"I educated myself on passive house and the upshot of it was that when I was going to builders and talking about passive house, I ended up knowing an awful lot more about it than they did," he says.
"I have no background in construction at all, nil," he states emphatically. "To my thinking it's an advantage. I have no connection to the old ways of constructing a traditional house. The only thing I know is passive house."
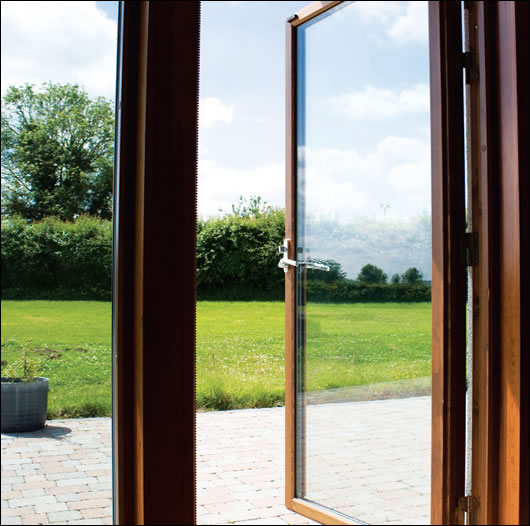
Tanumsföster triple glazed windows achieve a U-value of 0.92 W/m2K and a G-value of 61%
Micheál's company Passive Developments Ltd now offers consultancy and education on the passive house standard, in adding to construction itself. Micheál wasn't able to get planning permission for his own house, so he chose different clients for his first building project: a house for his parents. The house is designed so the couple can live entirely on the first floor should they ever become incapacitated.
Micheál chose a timber frame system from veteran Galway passive house builder Scandinavian Homes for the project. "What do you want to end up with? You want a comfortable low energy house,” he says. “When you pull the door and close it at night, it won't really matter if it's timber frame or not."
The walls of the house feature 215mm of Paroc mineral wool insulation, while the roof is insulated with a total of 400mm of Warmcel blown cellulose, and the ground floor with 280mm of expanded polystyrene. The house's heating system is quite minimalist: there's electric underfloor heating in two bathrooms and a utility room, and two vacuum tube solar collectors feature too.
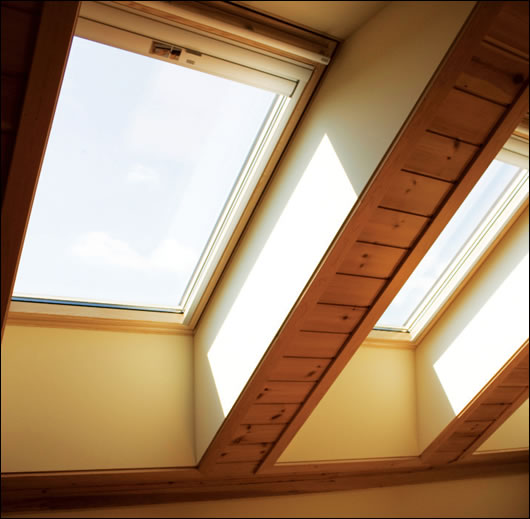
Micheál is hopeful the house will achieve Passive House Institute certification, but there are still some niggly issues to be resolved. Because the house's REC Temovex heat recovery ventilation system isn't certified by the Passive House Institute, a default value for its efficiency must be entered in PHPP. This means the house’s calculated space heating demand is 18 kWh/m2/yr rather than the required 15 kWh.
But the house can still achieve certification by meeting the Passive House's Institute's other key demand for space heating: a maximum heat load of 10 watts per square metre. Micheál says he’s working with the Passive House Institute to get it certified on this basis. Irrespective, Micheál has been considering other routes to come within the 15kWh threshold too: installing an approved HRV system for example, or cutting down a tree that's overshadowing the house and reducing solar gain.
But Micheál is also keen to avoid these options, and is confident it will get certified based on its calculated heat load in PHPP. "It would be interesting if we could get it certified without using any Passive House Institute certified products," he says.
He says people often ask his dad if he misses having an open fire — usually absent in airtight passive buildings — in his new house. "He got used to it quite quickly," Micheál says. "In this house it's never cold — so you never go looking for a fire."
Selected project details
Client: Maura & Michael Byrne
Architect, build system supplier & passive ventilation supplier: Scandinavian Homes
PHPP consultant: Peter H Lohr
Main contractor, energy consultant & project management: Passive Development
Civil / structural engineer: McGuinness Engineering Services
Wall insulation: Paroc
Roof insulation: Abbey Insulation
Floor insulation & underfloor heating supplier: Rostaff Developments
Windows and doors: Tanumsföster
Airtightness products: Siga
Airtightness tester: Energy Matters
Solar thermal supplier: Energy 4 U
Fit-out, flooring & roofing: Francis Day
Groundwork, drainage, paving & planting: Bernard Fitzsimons
Project overview:
Building type : 241 square metre detached, dormer, single family house
Location: Newtown, Rathangan, Co. Kildare
Completion date: July 2008
Budget: €313,000
Passive house certification: pending
Space heating demand (PHPP): 18 kWh/m2/year
Heat load (PHPP): 10 W/m2
Airtightness: 0.55 air changes per hour at 50 pascals pressure
BER: pending
Ground floor: 22mm floating solid pine floorboards/15mm stone tiles, 2 mm corkmat (080), 120mm power floated concrete, 280mm of expanded polystyrene (WLG 035) with 75mm of expanded polysturene and 60mm polyurethane insulation around the circumference, 1.5m depth broken stones on geotextile.
U-value: 0,109 W/m2K
Walls: internal plaster board (13mm), 70mm Paroc wool (WLG 033) stud 45x70mm, internal plaster board (13mm), airtight membrane, 145mm Paroc stud 45x145mm, Masonite K-board 9 (wind stopper), air gap 28mm, silicate exterior plaster (2mm) on fibre-enforced silicate board, 13mm (Bluclad)
Roof: concrete rooftiles on 28mm battens and 22mm counterbattens, roofing felt, 17mm timber sarking on rooftrusses spaced at 1.2m with double top-chord to break cold bridge, 400mm blown Warmcel (WLG 030) insulation with 22mm air gap above, vapour barrier, 17mm pine timber ceiling boards.
U-value: 0.09 W/m2K
Windows: Tanumsföster triple glazing.
U-value: 0,92 W/m2K and G-value: 61%
Heating system: electric floor heating installed in concrete in two bathrooms and the utility room downstairs. Two 12 CPC vacuum solar collector (4.4m) connected to a 300L dual coil solar cylinder. An electrical immersion heater is built in to the tank for top-up in winter.
Ventilation: REC Temovex 400 balanced ventilation system with heat recovery; 160-125-100 mm spiro duct system with rubber-sealed connections.
Electricity: 116 kWh/(m2a) total demand on heating installation, domestic hot water, household electricity and auxiliary electricity calculated according to PHPP
Green materials: Warmcel and Paroc
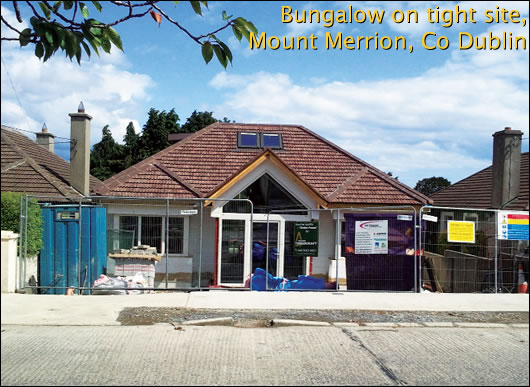
Architectural technician Des Crabbe took over the management of this passive house for clients Niall and Monica Walshe after a previous architect had completed drawings. "These guys were adamant they wanted a passive house," Crabbe says.
The project is Crabbe's first passive building. "It's a bungalow at the front and you don't really see the contemporary two-storey structure at the back,” he says.
Crabbe says that convincing the planners to let him knock the existing house on site and build new was a challenge — the local authority was keen to see the dwelling renovated instead. But once he compiled a report demonstrating the energy performance of the proposed passive house, they were convinced.
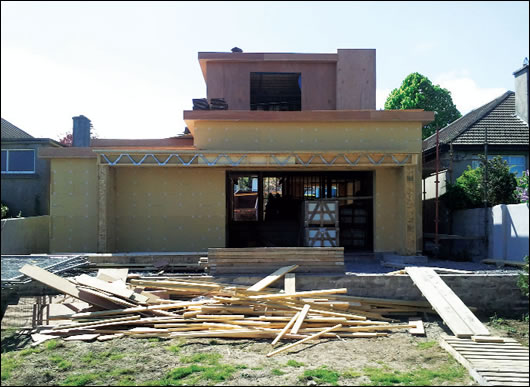
Gutex Thermowall external insulation
Advanced Timbercraft (who have since rebranded as Kudos) supplied the house's timber frame system, with natural insulation and airtightness products by Ecological Building Systems. “He wanted to create the lowest energy house in Ireland,” Advanced Timbercraft’s Neil Orr says of homeowner Niall Walshe. “Niall was very steadfast in his agenda.”
The house features a high tech KNX building automation system that controls everything from heating and lighting to security and home entertainment systems. If curtains are closed in a bedroom during the day and someone flicks a light switch, the system KNX will even open the curtains rather than turn on a light.

Thermo-Hemp service cavity insulation
Heating for space and water is provided by a Daikin air source heat pump and four square metres of Daikin solar panels. "He doesn't need a big heat load, he just needs some background heat," says Ollie McPhillips of Pure Renewable Energy, mechanical contractor on the project.
McPhillips says choosing a heat pump and solar system from the same company made integration of the two simple. "The way the whole control system is done, you don't have to be trying to patch up different systems.”
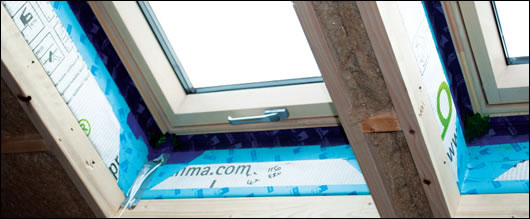
Fakro airtight roof lights
Selected project details
Architect: OA Studios
Build system supplier: Advanced Timbercraft (since rebranded as Kudos)
Civil / structural engineer: Fahy & Fitzpatrick Engineers
Main contractor: Halton Construction
Airtightness & insulation products: Ecological Building Systems
Airtightness tester: Greenbuild
Windows and doors: Internorm
Heating system supplier: Pure Renewable Energy
Energy consultant: Passivate
Lighting: Light4Living
Heating & lighting controls: IDAS Ltd
Rainwater harvesting: Watersource
Roof lights: Tradecraft Building Products
Electrical contractor: JR Healy Electrical
Project overview:
Building type: 256 square metre single-storey bungalow styled dwelling to the front south elevation with pitched A-roof. Two-storey contemporary styled dwelling to the rear north elevation with Alkor flat roof sections.
Location: Mount Merrion, Co Dublin
Completion date: November 2011
Passive house certification: pre-submission
Space heating demand (PHPP): 11 kWh/m2/year
Heat load (PHPP): 7 W/m2
Airtightness: 0.53 air changes per hour at 50 Pa
BER: pending
Ground floor: 500mm high Supergrund ‘F’ external wall profile (ringbeam). Internal retaining walls formed with Q7 Quinnlite insulated blocks. Floor build-up is 100mm concrete slab with reinforcing mesh, on 400mm EPS100 insulation, on 50mm stone blinding (3-8mm stone), on monarflex Radon DPM barrier c/w sump and vent pipes by Neoflex, on 250mm well compacted hardcore (18-35mm hardcore).
U-value: 0.075 W/m2K
Walls: 80mm Gutex Thermowall external insulation with Stucco render, 241mm lightweight I-beam Advanced Timbercraft timber frame structure with Daemstatt cellulose insulation, 18mm OSB sheeting, pro clima DA Membrane forming airtightness layer taped and sealed with pro clima airtightness tapes glues and accessories, 89mm service cavity with hemp insulation and 12.5mm Gypsum plasterboard.
U-value: 0.093 W/m2K
Pitched roofs: re-used existing tiles on 50x25mm soft wood treated timber battens at 250c/c, on counter battens, on Solitex breathable high performance felt, on 70mm foilbacked PUR insulation, fixed to 175x44mm rafters at 400c/c with cellulose insulation between pumped to 55kg/m3, on Intello membrane, on 89mm service void with hemp insulation between, on 12.5mm Gypsum plasterboard.
U-value: 0.122 W/m2K
Flat Roofs: standing seam Alkor membrane, on 18mm WBP plywood, on firring pieces all to achieve 1:80 fall to gutter valley, on battens, on Solitex high performance breathable membrane, on 70mm foil backed PUR insulation, on 175x44mm rafters at 400c/c with cellulose insulation between pumped to 30kg/m3 between rafters, on Intello airtight membrane, on 50mm battens to form service void with hemp insulation between, on 12.5mm Gypsum plasterboard.
U-value of 0.128 W/m2K
Windows: Passive House Institute certified Internorm triple-glazed alu-clad windows with a thermally broken painted spruce timber frame. Argon-filled cavities with low emissivity glass.
Overall U-value: 0.71 W/m2K
Rooflights: 7 triple-glazed Fakro FTT U6 Thermo rooflights with class 4 airtightness level, warm TGI spacers, Krypton-filled cavities.
Overall U-value: 0.81 W/m2K
Heating system: Daikin Altherma 11Kw split system – a high temperature air to water heat pump with 50L system buffer and a COP of 3.08 at 7C in to produce hot water at 55C, two Daikin flat panel solar collectors 2.6 m2 each with 300L hot water storage tank and 3Kw back-up immersion element. Heat distribution is by four 1kW towel radiators in the bathroom and en-suites plus one radiator at north end of the building on each floor. All integrated and programmable through KNX energy management system.
Ventilation: Paul Novus 300 Passive House Institute certified heat recovery ventilation system of minimum 90% efficiency, interfaced through KNX control LCD panels.
Green materials: woodfibre, cellulose and hemp insulation
Other green credentials: 4,800L Carat rainwater harvesting tank with multiple filter packages allowing rainwater to be used throughout the house including drinking and showers. KNX intelligent building home automation and energy management system. Guaranteed energy savings of 60% throughout the home with light, ventilation, shading and heating. Low voltage LED lights to be used throughout house with dimmer control and motion sensors integrated into the KNX control / interface