- Timber
- Posted
21st century Victorian
Just outside the quiet rural town of Templepatrick, County Antrim, located ten miles north of Belfast, is a timber frame house that sets new standards for comfort and, the owners hope, sustainability. Jason Walsh visited the house and found a traditional aesthetic that belies its ultra modern sustainability features
Looks can be deceiving. The home of Neil and Kyra Orr, an imposing edifice in the County Antrim countryside, does look like what it is. And yet it doesn’t. What it does look like is a sizeable, comfortable, three storey home ideally suited to family life. What is doesn’t look like – but most certainly is – is a sustainable timber-frame building that features the best in insulation and makes use of renewable energy.
On finding out about the owners, things become a little more clear: Neil Orr is himself well-versed in sustainable building as head of timber frame house manufacturers Advanced Timbercraft (update: the company rebranded as Kudos several years after this article was published), also based in County Antrim. Sustainability is a key concern for the firm – not only is it dedicated to building high quality and efficient homes, it also concerns itself with the material which is used to build in the first place: “We want to remove all treatment from the timber,” he says. “We use FSC-certified spruce sourced in Scandinavia.” Advanced Timbercraft also promotes natural insulation products, though it does, of course, supply a range of other materials. The company employs seven manufacturing staff and two dedicated air-tightness and insulation fitters.
The staff are certainly kept busy in today’s changing market: 2007 saw Advanced Timbercraft manufacture 21 houses and 2006 saw 35. No Kingspan Century, to be sure, but not an insignificant feat for a family business in a market that has traditionally been hostile to change: “Output depends on the square footage,” says Orr, “one [in 2007] was equivalent to four houses.”
So, given his background, it is unsurprising that Orr decided to build his own house, timber frame of course.
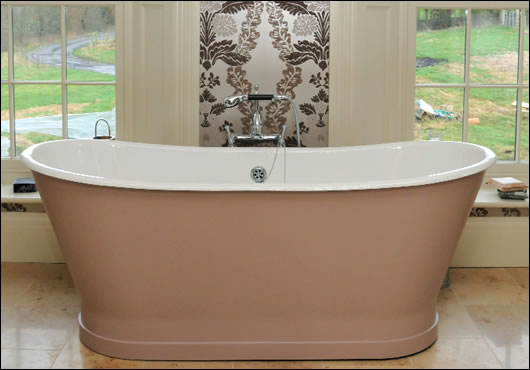
In terms of aesthetics, the Orr’s house does not suggest its innovative construction, instead showing many period-style features, as seen in the bathroom
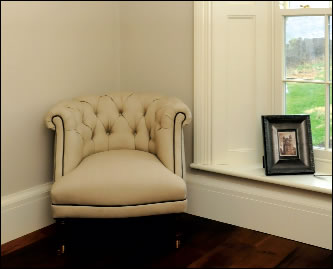
Building the dream
The 4,500 square feet (418 square metres), three storey, detached building not far from Templepatrick, County Antrim, is the culmination of months of planning – and years of dreaming. Orr and his wife Kyra wanted a period-style Victorian home influenced by the traditional three storey terrace.
Of course, the north of Ireland’s famously restrictive rural planning laws were an issue that had to be faced. The first hurdle that the couple faced was that one of the main aspects of their urban-inspired home – having three storeys – was going to prove difficult.
“My ideal home is a Victorian terrace but I want to live in the countryside,” says Orr – not a sentiment that was likely to have pleased the planners.
The solution involved some creative thinking. Instead of building a normal three storey building, Orr settled for a two storey with a 40 degree pitch in the roof. Put simply, this meant that what would otherwise be attic space was immediately available for use resulting in a house that meets planning requirements by being two storey but is functionally a three storey building.
“Public planning policies in rural areas prevent roof heights above a certain level – the majority of houses are [really] a storey and a half or a storey and three quarters,” he says.
Construction work on the property started in December 2006 and lasted twelve weeks. Advanced Timbercraft’s factory fitted insulated panels were brought on site and hand-assembled.
Orr says he feels a duty to be as sustainable as possible but realises that this intention must be balanced against costs, needs and desires: “We found ourselves facing a dilemma over what to do – [we wanted to achieve] high levels [of sustainability] at a reasonable price. In many respects it was the most difficult job we’ve ever done.”
In terms of improving the building’s thermal performance, Orr went a long way, using a 50 millimetre layer of high density polystyrene external insulation and Climacell celluslose insulation between the studs, supplied by Ecological Building Systems of Athboy, County Meath. The cellulose insulation is of varying depths, 140 millimetres at its shallowest, 280 millimetres at its deepest.
The u-value of the walls averages at 0.14 W/m2K.
The external blockwork features a 50 millimetre cavity with oriented strand board and breather membrane.
A 38 millimetre service duct located behind internal plasterboard assures that no unnecessary breaks were made in the house’s air-tight envelope.
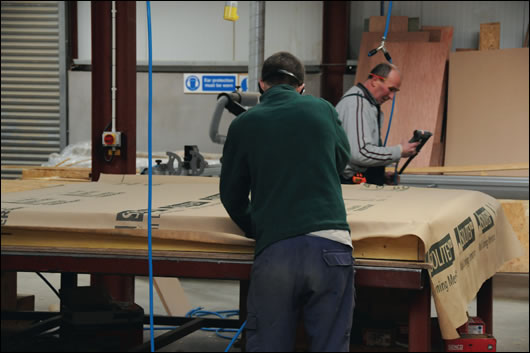
Factory fitting of Solitex, one of the Pro Clima products supplied by Ecological Building Systems, which were used to seal the house
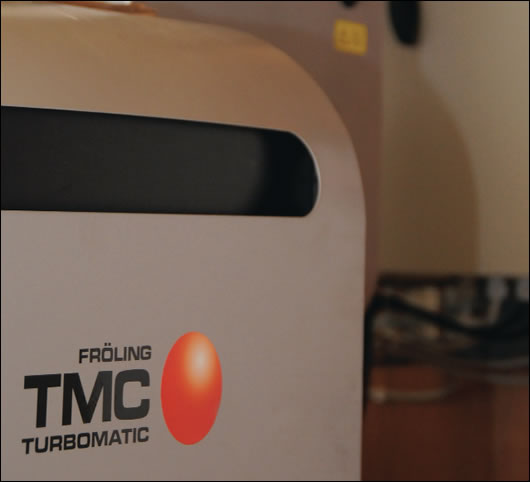
The principle heating system for the house is the Fröling Turbomatic, a wood chip boiler that supplies a 250 litre buffer tank
“Air-tightness is critical,” says Orr. “We built a house eleven years ago, a conventional two storey home and seven years ago we put a timber frame extension on it. There’s no comparison between the two.”
The house was sealed with the Pro Clima range of products supplied by Ecological Building Systems.
The Orrs were, at the time of writing, expecting a blower door air-tightness test to be performed by Commercial Connections from Crossgar, County Down.
Orr notes one interesting aspect of air-tightness in the home: “In an air-tight house you really notice any drafts.
“I can’t stress enough the importance of air-tightness. I think it’s the single most important thing. From an insulation point of view, if you install fibre glass well it will still insulate well if you air-tighten the house. With cellulose there’s the additional environmental benefit and the insulation is much better.”
The roof is also well insulated: “It’s very similar to the walls,” explains Orr. “It has nine inches (226.6 millimetres) of cellulose insulation. Instead of polystyrene we used Kingspan insulation. It’s maybe not as sustainable as we would have liked but nobody is coming up with better insulation to keep at current widths.
The floors are also well-insulated with seven inches (177.8 millimetres) of material, two layers of polyurethane and polystyrene from Xtratherm. Finally, a service duct on the first floor is insulated with 40 millimetres of Thermohemp insulation, also supplied by Ecological Building Systems.
Of course, despite the extremely high build quality and attention to thermal energy and the building’s envelope, the building remains a large one, something that some might view as ‘unsustainable’. Ultimately, though, large houses are going to be built, as are even larger commercial and industrial buildings, and it therefore makes sense to build them as sustainably as possible.
Size is not the only compromise with sustainability. The Orrs wanted heritage sash windows in keeping with the house’s design. The mahogony window frames were supplied by Hayburn Wood Products but, in keeping with the intention of energy conservation, the glazing is double-glazed low-e K glass from Pilkington.
Energising
The principal water and space heating system for the house is a wood chip burner and boiler. The boiler is a Fröling Turbomatic 35 kilowatt system that supplies a 250 litre buffer tank. This hot water heats the home via an underfloor heating system on the ground floor and conventional radiators on the two upper floors. The boiler comes on at 58 degrees and had been running for a total of 493 hours between installation and Construct Ireland’s visit – equivalent to just twenty days across a total of three months.
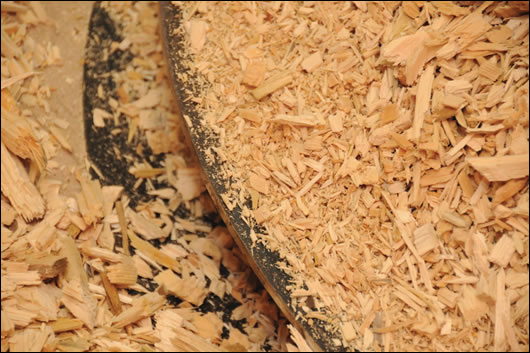
he wood chip fuel for the boiler, which heats the home via an underfloor system and conventional radiators
The boiler, burner, underfloor heating system and radiators were supplied and installed by Powertech based in Carrickmore, County Tyrone. The company’s Francis Martin explains: “When you’re using a heat pump you can’t use conventional radiators [because] going above 40 degrees with geothermal is too inefficient. With wood it’s different. Wood is good to burn at 70 to 80 degrees so it’s easier for traditional plumbing,” he says.
Martin explains that the key to success with such a system is knowledgeable plumbers: “Where it differs from traditional plumbing is that it requires proper controls. It’s plumbed for maximum efficiency and the plumber needs to install control valves.”
The underfloor system, guaranteed for 50 years, has spaces of between 50 and 200 millimetres between the pipes, which are themselves 17 millimetres in diameter. The density of the pipework depends, simply, on the volume of the room to be heated: “In a double-height area you’d need more pipes – it’s a cubic metre calculation.”
The heating system, both the underfloor and the radiators, are properly zoned for maximum efficiency: “A manifold distributes the [hot] water to each room,” explains Martin. “There’s a programmable digital clock in each room to control it.” By doing this, areas of the house can not only be set to individual temperatures according to personal comfort levels but overall efficiency is increased as there is no need to continually heat infrequently used areas.
In terms of fuel costs, Martin says that the wood chip system is a winner: “If you have an oil burner and you work out the cost at 37 pence per gallon, a wood pellet boiler should be roughly half of that. Wood chip could be as low as ten per cent.”
He does note, however, that a supply of high quality fuel is important: “In many cases we would say around fifty per cent due to the need for consistency [in moisture levels in the wood chip].”
Orr does use waste wood from manufacturing to heat the Advanced Timbercraft office but isn’t tempted to mass produce his own fuel for his home: “It would cost £14 to £15,000 (e18,500–e19,800) to buy a wood-chipper. I buy wood chip for £20 a tonne. We have a log burner in the office.
“That boiler would be capable of heating five or six houses,” he says. Indeed, Martin notes that one developer he is working with is currently thinking in terms of five kilowatts per house – a figure much lower that the 35 kilowatt system Orr is using.
Martin is adamant that no matter how good a renewable energy system is – and he’s clearly proud of the wood chip system supplied to Orr – that it will only be as good as the building it goes into: “It’s a huge mistake to put in renewable energy only to waste it,” he says. “That house is fantastic. It’s an example of over-specification.”
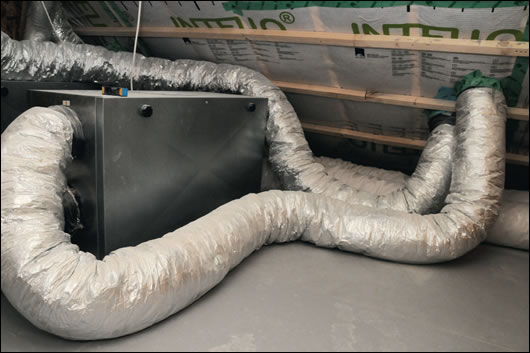
In addition to the wood chip, the house also includes two HRV units which work in tandem to improve both efficiency and comfort
In fact, Martin is quite clearly taken with Advanced Timbercraft’s house generally, telling Construct Ireland: “What Advanced Timbercraft do which is different to most people is to put on the rafters and seal them with two inches of Kingspan insulation. Between the rafters they put in cellulose – that means that they get a u-value equivalent to twelve inches of fibreglass. It’s also totally sealed, so it’s efficient and effective.”
Action Renewabes, the north’s equivalent agency to Sustainable Energy Ireland, did contribute £3,600 (e4,765) toward the wood pellet system. The grant scheme awards half of the cost of a renewable system up to a maximum of £3,600.
In addition to the wood chip for space and water heating the house also includes heat recovery ventilation, supplied by home ventilation specialists Homecare based in Donaghmore, County Tyrone. “We installed two systems,” says Homecare’s Gareth Fitzsimons. “Both Villavent HRV units.”
Again, this over-specification is related to both efficiency and comfort: “The reason for two systems rather than one was to allow for the zoning of the ventilation,” he says. “We also installed a Sach central vacuum [cleaning] system. Both systems are primarily involved in keeping a healthy indoor environment.
“The second reason is that they complement each other – the installation of the two systems takes place at the same time and follows the same ducting line,” he says.
Fitzsimons says that a single system would have sufficed but by using two in tandem, control is improved: “We could have put in one single unit but you’d be putting in fresh air all over the house. The zoning is an efficiency and comfort issue.”
The specific systems in use are Villavent VM2s, a two rotary wheel heat exchanger. Each is able to support a kitchen and up to six additional wet rooms and apparently has a heat exchange efficiency of up to 90 per cent. Villavent systems are designed and manufactured in Norway, a country with decades of experience with heat recovery ventilation. Villavent itself has been in business for over 35 years. The VM2 unit is listed in the SAP Appendix Q database.
Fitzsimons puts the VM2’s performance in real world situations at 80 per cent: “There are so many variables. With some units you hear figures like 97 per cent heat recovery – that just doesn’t happen. At 80 per cent efficiency if it’s twenty degrees inside and zero degrees outside you get heat recovery of sixteen degrees.”
Fitzsimons says that proper ventilation strategies are increasingly important in sustainable homes: “The market we’re involved in is interested in conservation of the heat in the home [and] this increases the need for proper ventilation. Up to 35-40 per cent of the total cost of self-building can be mechanical and electrical systems [and] as houses become better insulated and air-tight better ventilation is required.
“The sexy subjects – solar panels and so on – are undoubtedly good technologies but they’re vote winners for the government. Conserve the energy first and then look at downsizing heating.”
He also notes that the traditional Irish ventilation strategy is not only unsuited to sustainable building, but also simply not very good: “Infiltration is uncontrolled ventilation,” he says.
“Our model fits wells with quality timber frame homes. It takes the place of the ‘naturally’ leaky house – you’re controlling the amount of odoured, stale air that leaves the building and bringing in the same amount of filtered air. The two streams come through the unit [without mixing] so the natural thing to do is take as much heat as possible from the stale air and transfer it to the clean air.”
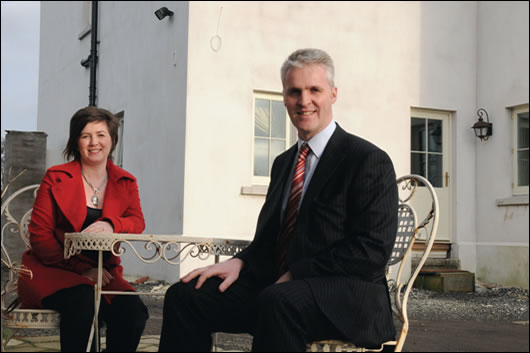
The clients, Neil and Kyra Orr, relaxing in their front courtyard, are able to reflect on a job well done
Once installed, the system left very little visible trace of its existence: “Visually, all you’ve got in the house is that each of the wet rooms has a CD-sized ceiling vent. Out of those, high humidity air will be continually extracted. The fresh air is supplied into other inhabited rooms.”
From a health and well-being perspective, the Villavent system includes an EU-7 grade British Allergy Foundation approved pollen filter: “If there are inhabitants in the house with asthma this is ideal,” says Fitzsimons.”The system filters the air coming in and keeps the relative humidity down – this is not conducive to dust mites breeding. It will also help hayfever sufferers,” he says.
Happy home
Orr freely admits that in building the house of their dreams his family had to make choices, compromises perhaps, but ultimately they are more than happy with the results. If only the attention to air-tightness and insulation was to become commonplace in similar buildings then the typical rural house in Ireland, north and south, would be greatly improved.
“The difference between this house and our last is like day and night, white and black,” he says. Indeed, Orr is clearly not afraid to put his money where his mouth is: “I’m passionate about timber frame not only because I sell it but because I live in it. We used to spend a lot of time convincing people that it was a normal method of construction, now people are interested.”
Orr does recognise, however, that despite the growing demand for air-tight, well-insulated timber frame houses, not everyone is onboard for the right reasons: “Developers simply want to do things to building control level.” Nonetheless, improvements are improvements, regardless of the ultimate motivation behind them.
In this regard, over-specified though it is, Orr’s house sets down a marker for sustainable rural housing. As always, the proof is in the pudding: “We’ve never felt cold,” he says. They’re not likely to either.
Project details
Client: Neil & Kyra Orr
Timber frame: Advanced Timber Craft
Air-tightness and natural insulation:
Ecological Building Systems
Additional insulation: Kingspan & Xtratherm
Wood chip boiler: Powertech
Heat recovery ventilation: Homecare
- Articles
- timber
- Advanced Timbercraft
- Templepatrick
- timber frame
- Climacell
- cellulose
- insulation
- Pro Clima
- Fröling Turbomatic
- Kingspan
Related items
-
Ireland’s first 3D printed homes insulated with clay foam
-
Timber in construction group holds first meeting
-
Unilin Ireland launches embodied carbon report
-
Up to 11
-
It's a lovely house to live in now
-
Mass timber consultation: have your say by 21 April to change the rules
-
Ecological launches Retro EcoWall for internal wall insulation
-
We Build Eco flat pack timber frame partnership gathers pace
-
Xtratherm name changes to Unilin
-
Ecological Building Systems launch Retro EcoWall for internal wall insulation
-
Mass timber masterwork
-
Kore launches low carbon EPS