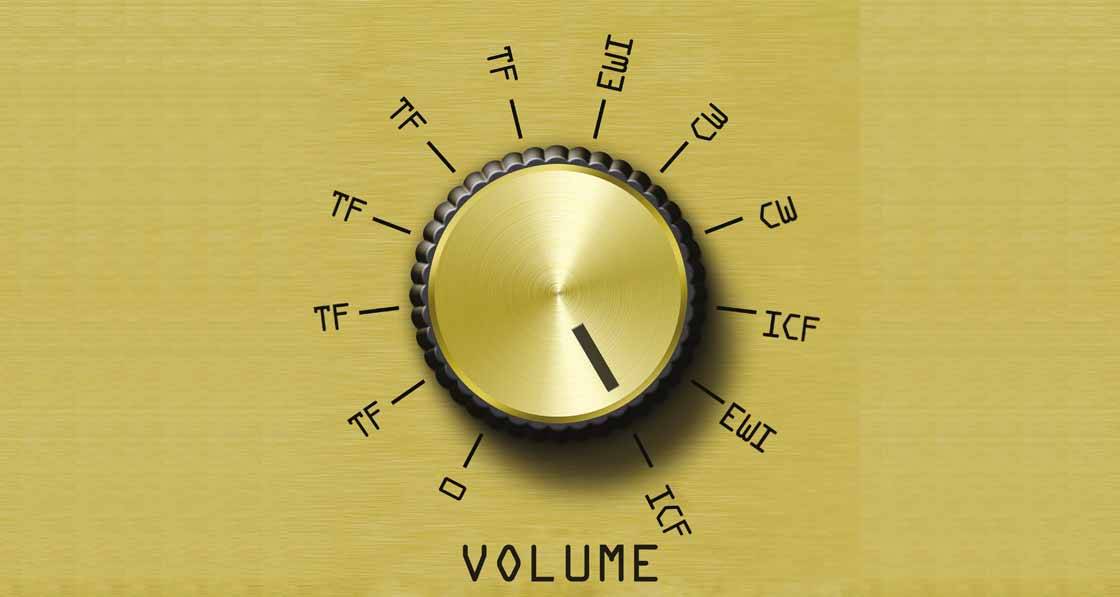
- Insight
- Posted
Up to 11
In issue 38 of Passive House Plus we published an in-depth assessment comparing the build specs including five wall types to a typical Irish house. To enable the industry to fairly compare a broader range of build options, we now expand that analysis with the addition of four timber frame wall types and two insulated concrete formwork systems
This article was originally published in issue 41 of Passive House Plus magazine. Want immediate access to all back issues and exclusive extra content? Click here to subscribe for as little as €15, or click here to receive the next issue free of charge
Issue 38 of Passive House Plus included an article, Six of one, which took a typical Irish house type and analysed the embodied carbon required to build it – assessing a number of variables for wall types and foundations. The house design in question – a 76 m2 end-of-terrace unit provided by Cork City Council – was assessed using the PHribbon embodied carbon calculation tool, in a collaboration between the Passive House Association of Ireland (PHAI), which funded the work, and the Association for Environment Conscious Building (AECB).
The analysis included cradle-to-grave calculations for wall types including cavity walls (with rendered block or brick externally), externally insulated blockwork (with either render or brick slip) and an I-beam timber frame wall with cellulose insulation and a render board. While these calculations were an important start – an opportunity to compare apples with apples by assessing the same house against different build approaches – it took in a comparatively small number of variants. The PHAI and AECB therefore agreed to make the calculations available to any third parties who wish to assess other variants against the house type, provided they agree to share the results for further dissemination.
The Irish Timber Frame Manufacturers Association (ITFMA) has taken the opportunity to assess four additional timber frame wall variants against the house type – essentially including timber frame with a fire-rated plaster board and either mineral wool or PIR insulation, and in both cases either rendered block or a recycled glass render board and render system. The ITFMA commissioned sustainable building consultant John Butler to produce a report on the different wall type variants – along with an insulating concrete formwork (ICF) system – and provided draft results to Passive House Plus for this article.
The wall build-ups were calculated to a U-value of 0.18, the backstop for walls under Ireland’s 2019 Technical Guidance Document for Part L of the building regulations, and the five build-ups from the earlier PHAI/ AECB analysis were adapted to meet the same U-value, to enable fairer comparison. For this article, Passive House Plus commissioned further analysis to evolve the ICF analysis into two scenarios – including high and low embodied carbon variants.
At the risk of death by tables, the 11 variants are included here, to show the build-ups in each case. While the full ITFMA report will assess wall build-ups to achieve U-values of 0.18 and 0.15, for this article only values of 0.18 were used. Eleven variants may also be a lot to take onboard in one article – let alone 22. As the embodied carbon explainer on p75 reveals, building life cycle assessments typically include three modules – A (cradle to practical completion), B (use phase, typically excluding operational energy and water use) and C (end of life). In this case, two sections of modules have been omitted. Modules A5 and C1 – which respectively deal with emissions released via construction (e.g. onsite activity) and demolition (at end of life), are typically calculated based on the project cost, based on default figures.
In the absence of specific costs for the various wall build-ups, these aspects were omitted. Consideration was given to excluding emissions from transporting the materials from factory gate to site (A4) from the calculations for this article, in part due to the difficulty in accurately calculating transport distances for concrete products, in the absence of environmental product declarations (EPDs) for many specific products. (For instance, in the case of a concrete block this would involve speculating on where the cement, sand and aggregate were sourced, calculating distance, freight type – and how heavily laden the vehicle is, including return trips – to and from the blockwork manufacturer, and calculating the ratio of each material used). In the end, transport default data from the RICS whole life carbon methodology was used, which suggests default distances for locally, nationally, and mainland Europe manufactured products of 50, 300 and 1,500 km by road, and points to UK government data for emissions from a range of road freight scenarios.
Where a material was Irish-made – as most materials in the analysis are – it was assumed to travel 300 km nationally by articulated truck, and 50 km locally by rigid truck. With the exception of the OSB and cellulose insulation, the timber and timber-based products were assumed to be from mainland Europe, along with the mineral wool insulation, render board system, EWI silicone render and the adhesive for the EWI brick slip system.
Based on 2021 UK averages, the local journeys appear to be circa 50 per cent laden trucks, due to consideration of return journeys, which are presumably largely empty for local trips. This means that the 50 km local trips are effectively assumed to be from depots circa 25 km from the site. The 300 km national and 1,500 km European journeys assume roughly 75 per cent laden artics, reflecting a reduced likelihood of empty return journeys.
The timber frame variants tended to include more materials from continental Europe, but this doesn’t come with a significant embodied carbon penalty via transport, due to the lighter material weight compared to concrete products. By way of example, option 5, the I-beam timber frame system with cellulose, generally assumes timber and timber-based products from Sweden, with the exception of Irish-made cellulose and OSB. Much of the imported structural timber used in Ireland comes direct from the south of Sweden by relatively low carbon sea freight, but as the article supposes 1,500 km truck journeys were instead made, with an extra 50 km locally to deliver to site, it would have added 326 kg CO2e, compared to 86 kg based on 300 km national and 50 km local transport.
Given the lack of EPDs for Irish concrete blocks, figures for a medium density block from the British Precast Association were used, albeit with national transport assumptions. Also, the concrete mix calculations for the ICF system were done prior to the Cement Manufacturers of Ireland obtaining an EPD for CEM I, and were therefore instead based on an averaged portland cement EPD by the UK’s Mineral Products Association. This meant the cement had a value of 846 kg CO2e/tonne, compared to CMI’s values of 723 kg CO2e/ tonne for CEM I, or 698 kg for CEM II. If the calculations were redone, it’s likely the ICF worst case would have reduced by over one tonne of CO2e.
A 50-year building design life was assumed, as per the EU Level(s) sustainable building framework. The render board and render system used for three of the timber frame variants was assumed to last for the lifespan of the building – though as the EPD for the system makes clear, this assumption is dependent on the quality of installation, taking account of rainproof connections to other buildings or building parts. Similarly, the silicon render system used on the two ICF variants and on the rendered EWI system were also considered to last for the life of the building, although the EPD in this case listed a design life for the outer layers of the system of 25 to 50 years, depending on location, construction and material quality, while also recommending repainting after 15 to 20 years. Repainting and retouching of render systems was omitted in all scenarios, including the sand/cement render, which was assumed to have a 30-year lifespan. Interior painting and repainting were omitted in all cases. Had a 60-year lifespan been assumed instead, as per the UK RICS methodology, the results may have differed in some cases – depending on what assumptions are made about component lifespan.
The five timber frame variants posted the lowest embodied carbon scores, both in terms of the module A (cradle to practical completion) results, and the A-C (cradle-to-grave) results. Wall type 5 – the I-beam timber frame wall with cellulose insulation and a render board – is the clear winner at 4.1 tonnes from A-C. This wall type is also the only variant where more CO2 is sequestered in the walls at the point of practical completion than was released in the manufacture and transport of the wall materials to site. It’s important to note that this sequestered CO2 is assumed to be released at the end of the 50-year design life in the life cycle assessment (LCA), but if the walls were to last in excess of 100 years, this CO2 would remain sequestered for that time. Planners permitting, greater reductions still could potentially be achieved by use of lower embodied carbon external cladding, such as charred timber cladding – which can offer the dual benefit of low upfront emissions and 100-year plus lifespans.
The second and third best results go to two timber frame walls with render board finishes, wall type 7 and 9, with the mineral wool/PIR insulated version (5.0 tonnes) scoring better than the PIR-only variant (5.2 tonnes). Wall type 6 – timber frame with mineral wool/PIR and blocker outer – comes in at 6.4 tonnes, while wall type 8, 8 – a PIR insulated timber frame wall with rendered block cladding – comes in at 6.6 tonnes. One point to note here: the timber frame variants 7-9 benefit significantly from the very low emissivity levels assumed for the foil-faced PIR insulation and foil-faced VCLs and membranes, where these materials were facing unventilated cavities, in line with ISO 6946:2017. This meant significantly reduced insulation thicknesses are required to achieve the 0.18 U-value backstop. The cavity wall variants also benefited from this emissivity – with the foil facing on the PIR facing into unventilated cavities.
Sixth place and the best result for a concrete- based system goes to wall type 3, the block on flat with EPS external insulation and silicone render, which at 8.2 tonnes adds over a tonne compared to the worst performing timber frame variant – and double the score of wall type 5.
Rendered cavity wall (wall type 1) comes in seventh at 8.9 tonnes, with brick-clad cavity wall (wall type 2) at 9.8 tonnes – reflecting the high embodied carbon of brick manufacturing. The low embodied carbon variant of ICF (wall type 11) comes in ninth at 9.9 tonnes, followed by the brickslip-clad externally insulated block variant (wall type 4) at 10 tonnes. The clear outlier from these 11 wall types is the higher embodied carbon variant of (wall type 10) bringing up the rear at 15 tonnes. There are a couple of important observations here. The first is that the brick or brickslip clad variants fare significantly worse than their rendered equivalents. Note that brick or brick slip options were not considered for the ICF or timber frame variants. The fairest comparison therefore is arguably between the rendered versions of all wall types, including systems with rendered block-clad outer leafs, rendered EWI, and renderboard systems.
Secondly, the ICF variants – and to a lesser extent the other concrete-based variants – are to a fairly large extent affected by the assumptions around transport distance: 1.48 and 1.56 tonnes of CO2e are estimated for transporting concrete to site in the low embodied carbon and high embodied carbon ICF variants respectively, assuming 300 km by artic and 50 km by rigid trucks. While these distances may look less far-fetched given that the figures are based on round trips, over a tonne of CO2e is associated with the artic journeys specifically. An ICF project near a cement manufacturer’s factory gate would stand to achieve significant reductions.
It’s also important not to take these results out of context, notwithstanding the fact that this article is focused on embodied carbon alone, and ignoring other considerations. External walls can represent a significant proportion of a building’s total embodied carbon, but there are other building elements which may have similar or greater impacts in some cases. The extraordinarily high results for an admittedly unusually large solar PV roof in the case study on p69 are a case in point.
Passive House Plus intends to add other build specs to this comparison in future issues, and invites other parties to put forward their build specs for publication. But while analysis like this may serve as useful guidance to inform design specifications, it’s imperative that building designers start either commissioning building LCA consultants or using building LCA tools for themselves – and at the earliest possible stages in the design, in order to inform the specification – and focus the minds of suppliers to find ways to reduce the embodied carbon of their solutions.