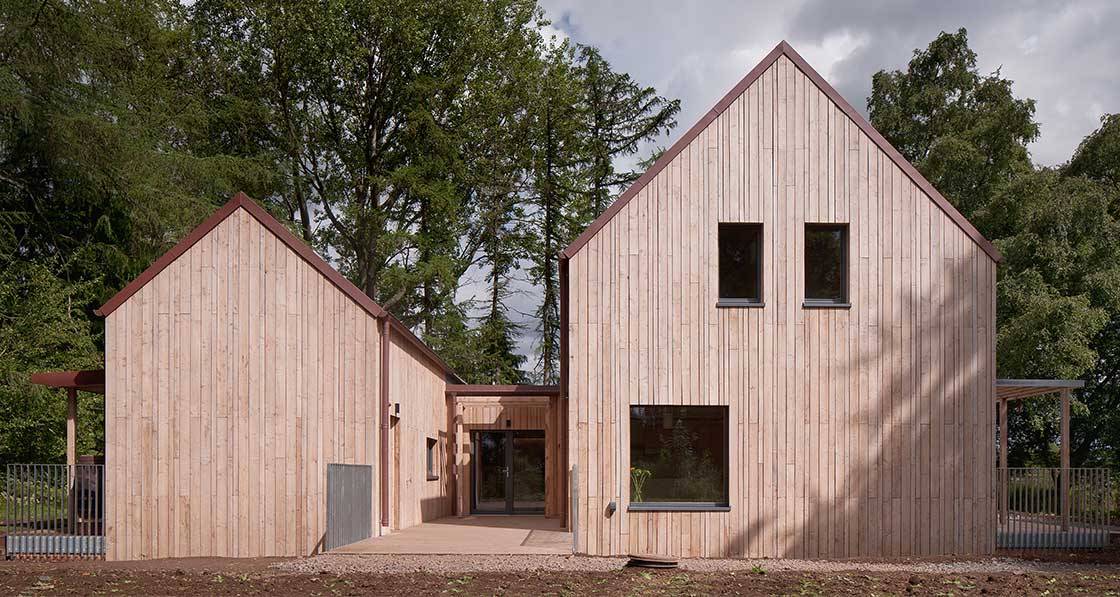
- New build
- Posted
Living proof
Sometimes a building comes along that does almost too much. Passive house stalwarts Kirsty Maguire Architects’ latest opus is an award-winning architectural, engineering, and sustainability feat – which asks questions not just about how we build, but how we live.
Click here for project specs and suppliers
Method: Timber frame, screw piles, bio-based materials, heat pump
Location: Dundee
Standard: Passive house classic
Heating cost: £20 per month space heating cost, between two households.
See 'In detail' panel for more information.
The many projects I have covered in my 15 years writing for Passive House Plus share certain traits in common: extremely low energy use, airtightness, technical innovation, and rigorous attention to detail. Many were also low in embodied carbon, or prioritised bio-based and natural materials.
But every so often a project comes along that goes beyond technical and environmental ambition, to ask deep questions about how we use buildings, and reimagine how this relationship might look.
So it is with The Seed, a new passive house on the edge of Dundee which picked up the Supreme Award and Best New Home Award at the Dundee Institute of Architects 2023.
Built with a timber frame that is insulated with cellulose, and almost completely shunning the use of cement and concrete, the house is designed to be lived in by two families.
There was a really interesting discussion exploring a way for two families to live together.
The project was the vision of Karoline Hardt, who is from Germany but studied at St Andrews, before moving to Leeds, where she became inspired by the city’s cohousing developments. Cohousing is a form of intentional community, where people have private living quarters but share facilities such as guest bedrooms, gardens, laundry, even cars. A space for shared meals is common too, though homes generally have private kitchens as well.
When Karoline started looking to buy a home of her own, she wanted to take these principles and apply them to a smaller project, to create a home and garden that could be shared by two families.
“I read a lot of cohousing literature and case studies, mostly from Scandinavia,” she says. “But this was going to be something very different — how do you translate the principles of cohousing projects of 30 to 50 households, plus one common house, into a project of one house for two families? That was really tricky.” Her initial motivation was to reduce consumption and share resources – the washing machine, the hoover, simple things. “All the cohousing people I knew in Leeds were ecologically minded,” she says.
A big garden to grow food and make space for nature was integral to her vision, but it was hard to find a house with a decent sized garden within her budget in Glasgow, where she was living. So, she cast her eye further afield, and eventually bought a 1950s house with a one-acre garden on the western edge of Dundee. “Under the floorboards, there was 50 cm of air, then the soil. It was dusty and damp. I can’t believe I lived there for three years, it was very unhealthy,” she says.
Initially, the plan was for a deep retrofit. Karoline was interested in passive house, having been familiar with the concept from Germany, and she found Kirsty Maguire Architects (KMA), who specialise in passive house design and are based just across the Firth of Tay, in Newport-on-Tay.
Kirsty and Karoline looked at ways to upgrade the house, but the changes Karoline envisaged were significant, and the building was in such a poor state of repair that it would have been hard to retain much of the existing house. So, they made the decision to knock and rebuild.
Of course, demolish-and-rebuild usually results in a higher carbon footprint than retrofit. But it did give Karoline the opportunity to develop a purpose-built dwelling that is quite unique, being designed as it is around the concept of sharing resources.
“The ecological impact of renovation would have been smaller,” Karoline says, “but I think in this case it maybe was acceptable to build from scratch, because it allowed us to have our two families together, side by side.”
The finished house features a mix of private and communal spaces. Downstairs, the dwelling is divided in half, with two separate kitchen-and-living spaces, each with a sliding timber door that leads out to the communal, central hallway.
One of these kitchen-and-living spaces is for Karoline and her partner Carolina, while the other is for their friend Daniel and his daughter Emilia, who they share the house with. Between them, the two families have developed a simple language for communicating whether they would like to socialise or not. A fully open sliding door means, ‘we would love you to come in’. A closed door is a request for a privacy. A half-open door says, ‘come in if you would like to’.
The broad and bright communal hallway was designed as a meeting place and social hub. It has built in seating, and a covered porch at one end that is pleasant for sitting out on mild days. “We might all meet in the hallway and then start talking, so we end up hanging out in the hallway,” Karoline says. The back section of the house, which faces north, is just one-storey. It has a shared office that can double as a guest bedroom — a material and carbon efficient use of space — plus a sauna, accessed from the rear deck of the house, and a shower room. Upstairs there are three bedrooms, a washroom and shower room.
Outside, the garden is bordered on all sides by mature trees — beeches, Scots pines, birches, black poplars, ash, spruce, and Norway maple. In fact, the entire garden is covered by a tree preservation order. So many tree roots snake across the site that it restricted the area in which the new house could be built.
We might all meet in the hallway and start talking, so we end up hanging out in the hallway.
From the outset, the residents of The Seed set about creating an edible forest garden, applying the principles of permaculture. They have planted apple trees, pears, plums, cherries, hazels and chestnuts. They have also put in vegetable beds and have plans to build a greenhouse with windows salvaged from the old house, and to create a swimming pond, for people and wildlife.
They have given space to a local woman to keep bees, while Daniel, who home-educates his daughter, participates in a weekly meet up that Karoline hosts for home-educating parents and their children, who use the outdoor space to learn new skills and play in nature.
“The children are helping to design the garden,” Karoline says. “Their design brief is to make the garden more playful. Our big project this year is building the treehouses that the children asked for and designed.”
“I wanted to make it a social garden, not just a social house,” she says, “for the garden to be a space where people can create together. It’s a private garden but we are creating something that is communal. We are trying to make something communal within structures that are not communal, in the official sense.”
The Seed is also proud of its diversity: all its adult residents are immigrants, two are people of colour, two are queer women. “This is important for us,” Karoline says. “Here, four usually minoritised groups are in the majority, and we have found that this changes things. We interact differently, talk about different things, understand different things. The Seed is like a respite from the dominant culture.”
-
The foundation consists of a suspended timber floor constructed on galvanized steel screw pile foundations The foundation consists of a suspended timber floor constructed on galvanized steel screw pile foundations
-
Andrew McCullough of Thermal Image UK using a smoke pencil to look for leakage during the blower door test Andrew McCullough of Thermal Image UK using a smoke pencil to look for leakage during the blower door test
-
Heating is provided by a Daikin Altherma 3 air-to-water heat pump Heating is provided by a Daikin Altherma 3 air-to-water heat pump
-
The garden is filled with mature trees and covered by a tree preservation order The garden is filled with mature trees and covered by a tree preservation order
-
The foundation consists of a suspended timber floor constructed on galvanized steel screw pile foundations The foundation consists of a suspended timber floor constructed on galvanized steel screw pile foundations
-
The foundation consists of a suspended timber floor constructed on galvanized steel screw pile foundations The foundation consists of a suspended timber floor constructed on galvanized steel screw pile foundations
-
The foundation consists of a suspended timber floor constructed on galvanized steel screw pile foundations The foundation consists of a suspended timber floor constructed on galvanized steel screw pile foundations
-
Installation of the suspended timber floor, which is insulated with cellulose and sits on a truss lattice of timber beams that is ventilated underneath Installation of the suspended timber floor, which is insulated with cellulose and sits on a truss lattice of timber beams that is ventilated underneath
-
Smartply Airtight OSB with airtightness taping at seams Smartply Airtight OSB with airtightness taping at seams
-
Brick from taken down house used for gabions Brick from taken down house used for gabions
-
Pro Clima Extoseal Encors weatherproof and watertight sealing tape around windows Pro Clima Extoseal Encors weatherproof and watertight sealing tape around windows
-
Blower door airtightness test underway Blower door airtightness test underway
https://mail.passive.ie/magazine/new-build/living-proof#sigProId50b677693b
In my time writing for Passive House Plus, we have covered many projects with deeply impressive fabric performance, energy demand and airtightness. But as with most of the building sector, we have always evaluated these buildings based on the amount of energy they consume per square metre of floor area. Meaning that someone can build a very large house, consuming far more resources than necessary, and still meet standards such as passive house, or the RIBA Climate Challenge (Ed.: the RIAI, to their credit, have set a more stringent embodied carbon target for homes of more than 133 m2 or smaller low density rural homes). A growing number of voices now argue that we need a robust way to measure energy use and embodied carbon per person too, as well as per square metre.
The Seed does challenge perceived wisdom about how much we need to live with. Does every home need a separate guest bedroom, for example? Its own laundry, tools, and other facilities? What else might we share if we lived closer together, while building community at the same time?
This writer lives with his wife in in a small cohousing project within a wider intentional community, Cloughjordan Ecovillage. Moving here has been one of the most rewarding decisions of my life, and it is now hard to imagine living any other way. It has opened my eyes to the extent to which community has been eroded from our societies, its critical role in climate and environmental action largely forgotten. Which is why projects like The Seed are so inspiring and illuminating.
This article was originally published in issue 47 of Passive House Plus magazine. Want immediate access to all back issues and exclusive extra content? Click here to subscribe for as little as €15, or click here to receive the next issue free of charge
Cohousing aside, The Seed is also deeply impressive in terms of thermal and environmental performance. It was certified as a passive house just before this magazine went to print — all the more remarkable given that its H shape means it has a large surface area from which heat can escape, and given its foundation type – more on which later.
It was built with a prefabricated timber frame system from Eden Insulation in Cumbria, and insulated with cellulose and wood fibre, with airtightness provide by Smartply Airtight OSB. And it boasts a superb airtightness result of 0.19 air changes per hour.
But it is in the detailed thought given to embodied carbon and materials where The Seed really excels. Karoline developed the project with her ex-partner, and his desire to avoid the use of cement and concrete led to some innovative design decisions. Early on, KMA and the project engineer, Narro, produced a report looking at potential alternatives to concrete foundations.
KMA also evaluated the embodied carbon of the different options. A limecrete foundation was considered, but Karoline was keen to have large windows, and there was more chance of these shifting over time on limecrete.
Then Narro came across No More Digging, a Dundee-based supplier of screw piles and ground screws – large steel screws that are secured into the ground to provide a stable foundation. Steel industry progress on commercialising net zero carbon steel notwithstanding, steel is typically a highly carbon intensive material, and far higher than even concrete, pound for pound. Analysis by embodied carbon expert John Butler indicated circa 180 tonnes worth of concrete would be required to build a strip foundation for a development of this nature, including the foundation for the decking. This compares to circa five tonnes of screw piles, and roughly one-third of a tonne of concrete grout. Maguire had hoped to eschew concrete altogether, but a high-water table mitigated against this, meaning the use of concrete grout – which main contractor Billy Ferguson reckons added up to less than a cubic meter of concrete – to protect the steel.
At The Seed, the suspended timber floor is insulated with cellulose and sits on a truss lattice of timber beams that is ventilated underneath. This lattice in turn sits on the screw piles, which are anchored into the earth – which also means the site could be easily restored to a green field site, once this building reaches its eventual end of life, hopefully several hundred years from now. Brick salvaged from the old house forms the upper layer of earth here, while salvaged brick was also used to form the gabions for the retaining wall (in order to create a ventilated, suspended timber floor without raising the level of the house too much, it was necessary to dig down).
“There is a lot of really beautiful work underneath the building,” Kirsty says, praising Billy Ferguson and Paul Gordon of contractor Alpha Contracts for this.
Karoline says that building something innovative came with riskes as well as rewards: “It was a huge responsibility because I always wanted to make the perfect decision,” she says. “But I learned there is no such thing as the perfect decision. Because even if you find the right material, is it available in the UK? Are the skills available to install it?”
With a portfolio of ambitious ecological and low environmental impact projects under their belt, KMA are no stranger to exploring new architectural ideas, and Kirsty says that even though the project was innovative, her team approached it methodically. “We managed risk very carefully and gave Karoline deliverable options which were extremely well researched and low risk at each stage.”
She continues: “Karoline’s vision was this cohousing type living arrangement, and part of this project was exploring what that meant for her, to deliver the bigger picture she envisioned for the site.”
“There was a really interesting discussion about what cohousing meant, what would work. It was really just exploring a way for two families to live together. Karoline brought different voices into the design process along the way, and the fact the space would work for a range of different people, rather than just one set of people, is really interesting.”
Ultimately, The Seed hits impressive environmental benchmarks — passive house certified, low embodied carbon, an obsession with reusing materials — but it is as much about creating a space for community and nature as the building itself.
Kirsty says: “To Karoline, it’s a woodland garden that happens to have a house in it.”
Selected project details
Client: Karoline Hardt
Architect: Kirsty Maguire Architect Ltd
M&E engineer: Max Fordham
MVHR: Paul Heat Recovery
Civil/structural engineer: Narros
Energy consultant: Kirsty Maguire Architect Ltd
Main contractor: Alpha Contracts
Mechanical contractor: Alpha Services
Airtightness tester/consultant: Thermal Image UK
Passive house certifier: Ingo Theobalt
Build system, wall, roof and floor insulation: Eden Insulation
Thermal breaks: Compacfoam, via 21° (formerly Green Building Store)
Airtightness products: Ecological Building Systems/Medite Smartply
Windows and doors: 21° (formerly Green Building Store)
Roof lights: Velux
Landscaping: Client and Alpha
Primary space heating system supplier: Alpha
Rainwater harvesting: Alpha
Embodied carbon
Passive House Plus commissioned embodied carbon calculations from John Butler Sustainable Building Consultancy, which included a comparison of the house’s innovative screw pile foundations against two other options more typically seen in these pages: an insulated foundation system, and a strip foundation. More on that below.
The scope was generally as per the RICS 2023 whole life carbon assessment standard, and included specialist groundworks, substructure, superstructure, floor, wall and ceiling finishes, building services, fittings, furnishings, and equipment – excluding kitchen appliances – and external works. Where environmental product declarations (EPDs) could not be identified for a given material, EPDs for similar products were used, or default data from the ICE database. Default transport assumptions were taken in general from RICS 2017, with one notable exception being the reused materials from the site.
When assessed against the 2030 RIBA Climate Challenge target of 625 kg CO2e/m2 - which does not include external works - the cradle to grave score for this building came to 582 kg CO2e/m2, comfortably beating the target. Arguably, the building is better than this total looks. At 176 m2, with a design to accommodate two households, it uses considerably fewer resources than it would have if separate homes had been built.
Then there’s the perennial issue of the treatment of timber in life cycle assessment calculations – an issue which is amplified in a building like this, which is timber to the bone. By the point of practical completion on the home, 408 kg CO2e/m2 had been emitted into the atmosphere, translating to 88.3 tonnes of CO2e. But given the use of timber and wood-based products to build the floors, walls, roof, thermal envelope and finishes, the building sequesters an awful lot of CO2e too – 441 kg CO2e/m2 (95.5 tonnes), meaning as it stands, the building actually sequesters more CO2 than was emitted to build it.
But this is where care is required, to avoid the risk of encouraging a drive to deforest our way to saving the world. A better solution than attempting to compensate for upfront emissions with sequestered emissions is to avoid releasing emissions in the first place. To that end, the upfront carbon rating scale set by the Low Energy Transformation Initiative (LETI) is useful, in that it sets ratings for upfront emissions, without deducting sequestered CO2. At 408 kg CO2e m2, this building achieves a B rating. To get to an A, it would need to fall under 350 kg CO2e/m2.
So where are the upfront carbon hotspots? Remarkably, the biggest cradle to factory gate total for any single material came from the screw piles, at 13.8 tonnes CO2e, with the zinc roof cladding coming second at 7 tonnes. Screw piles are essentially extended ground screws, and previous analysis published in this magazine on ground screw foundations indicated the technology’s potential for significant embodied carbon savings. However, this analysis did not have the benefit of actual EPDs for screw piles, instead relying on default data for recycled steel.
While no EPD was available for the brand of screw piles used in the building, Passive House Plus and Butler found EPDs for two other ground screw brands and took an average of the two to apply a value for the building. Meanwhile, data on an insulated foundation system was used for comparison, alongside a traditional strip foundation with PIR insulation – albeit with rule of thumb information derived from other projects in both cases, rather than a full foundation design.
When considered in the context of the whole building, the comparison indicates that switching from the suspended timber floor on screw piles to an insulated foundation system would actually have reduced the building’s embodied carbon totals. The LETI upfront carbon score reduced from 408 to 401 kg CO2e/m2, while the strip foundation variant would have increased the total to 447 kg CO2e/m2. The insulated foundation system also reduced the cradle to grave score from 582 to 576 kg CO2e/m2, compared to an increase to 619 kg CO2e/m2 for the strip foundation variant.
One other significant factor which counted against the screw piles in this case was building regulations at the time. 5.1m and 6.1m screw piles were used at The Seed. John Butler has worked on other projects with ground screws of half this length, and refers to a current project by Grain Architecture with 1.6m screws.
“We wanted quite a lot of ventilation under the building to keep the timbers dry,” says Kirsty Maguire, who adds that if the project were starting now, changes in building regulations would have enabled substantially shorter piles. “Under the new regs, if you have an even surface, with hardcore layer and DPM – which we do – you can have a 150mm gap to the suspended timber floor.
At the time the regs only mentioned a concrete capping to the solum. We had to err on the side of caution and go for a larger gap, because we were avoiding concrete and minimising any petrochemical materials.”
It is worth emphasising that the foundation comparison results are only indicative, and that the subject warrants further exploration, with fully quantified and specified foundation designs. But what makes these results even more startling is that conventional CEM I-based concrete was assumed. Given the commercialisation of low carbon steel manufacturing approaches, it may only be a matter of time before a ground screw manufacturer turns to technologies such as electric arc furnace-made steel and obtains an EPD to verify the low embodied carbon score. Or it may be that other low carbon foundation options emerge. But a key point emerges: rules of thumb are of limited value in embodied carbon. Actual calculation, based on the most accurate data possible, is essential.
In detail
Development type: Co-living house for two families.
Building type: Two-storey timber frame house (176.8 m2 TFA)
Site type & location: Brownfield – replacement house, Dundee
Completion date: July 2023
Budget: Confidential
Passive house certification: Passive house classic certified
Space heating demand (PHPP): 20 kWh/m2/yr
Heat load (PHPP): 10 W/m2
Primary energy renewable (PHPP): 34 kWh/m2/yr
Heat loss form factor (PHPP): 4.0
Overheating (PHPP): 0 per cent of year above 25 C
Number of occupants: 3 adults, 1 child
Environmental assessment method: n/a
Airtightness (at 50 Pascals): 0.20 ACH
Measured energy consumption: Not yet available
Heating costs: Calculated space heating costs of £20 per month, based on the PHPP space heating demand of 23 kWh/m2/yr, an estimated seasonal COP of 3.5 for space heating, and a 2024 Scottish electricity tariff of £0.24p from powercompare.co.uk
Embodied carbon
Cradle to grave score: 582 kg CO2e/m2 GIA, meeting the RIBA 2030 Climate Challenge target Upfront carbon: 408 kg CO2e/m2 GIA – excluding sequestered CO2 – meeting LETI band B Thermal bridging: Timber kit fully designed to avoid thermal bridges by good junction design and working with supplier – Eden Insulation – OSM kit which is designed with this in mind. All junctions addressed this throughout. Cladding is lightweight rainscreen.
Ground floor: Suspended timber floor constructed on galvanized steel screw pile foundations. Brick from old taken down house used for gabions and top layer of earth under house, recycled rubble backfilled behind gabions, minimum 600 mm ventilation gap; timber foundation beam on top of screw piles; 12 mm Elka strong board; 360 mm cellulose-insulated timber floor; 22 mm Caberdeck, 22 mm oak floor finish. U-value: 0.115 W/m2K
Walls (inside to out): 13 mm Fermacell; service void with 40 mm wood fibre insulation; 12.5 mm Smartply airtight board; 360 mm celluloseinsulated timber frame wall in layers of 39 mm, 282 mm and 39 mm; 22 mm Multiplex top; ventilated cavity; Russwood rough sawn Scottish larch open-jointed cladding pre-treated with SiOO:X original. U-value: 0.99 W/m2K
Roof: Principally pitched roof, but with flat roof section linking two-storey and single-storey sections. (Inside to out): 13 mm Fermacell; service void with 40 mm wood fibre insulation; 12 mm Smartply Airtight board; 360 mm celluloseinsulated timber frame wall in layers of 39 mm, 282 mm and 39 mm; 22 mm Multiplex top, vented cavity with timber battens, 18mm plywood, membrane, zinc. U-value: 0.10 W/m2K
Windows and external doors: timber framed Ultra (now GBS98) windows. Average G-value: 0.51. Average U-value: 0.93 W/m2K
Roof windows: Velux passive house certified roof lights. G-value: 0.34. U-value: 0.81 W/m2K
Heating system: Daikin Altherma 3 air-to-water heat pump with low temperature radiators.
Ventilation: Zehnder Comfoair Q350
Water: Low flow fixtures, rainwater harvesting using recycled whisky barrels.
Electricity: No PV. No battery. Car charger ready but no cars in household, bike-based household with bike shed not garage. Bike charging points at bike shed.
Sustainable materials: Timber frame, cellulose/ wood fibre insulation, Fermacell board, clay plaster, reused materials from house, root protection then reused here and, on another site, screw piles, almost entirely omitted cement, Scottish larch cladding, timber flooring, zinc roofing and rainwater pipes. Recycled/reused furniture. Unbleached materials in blinds. Avoided MDF in kitchen and bathroom specifications.