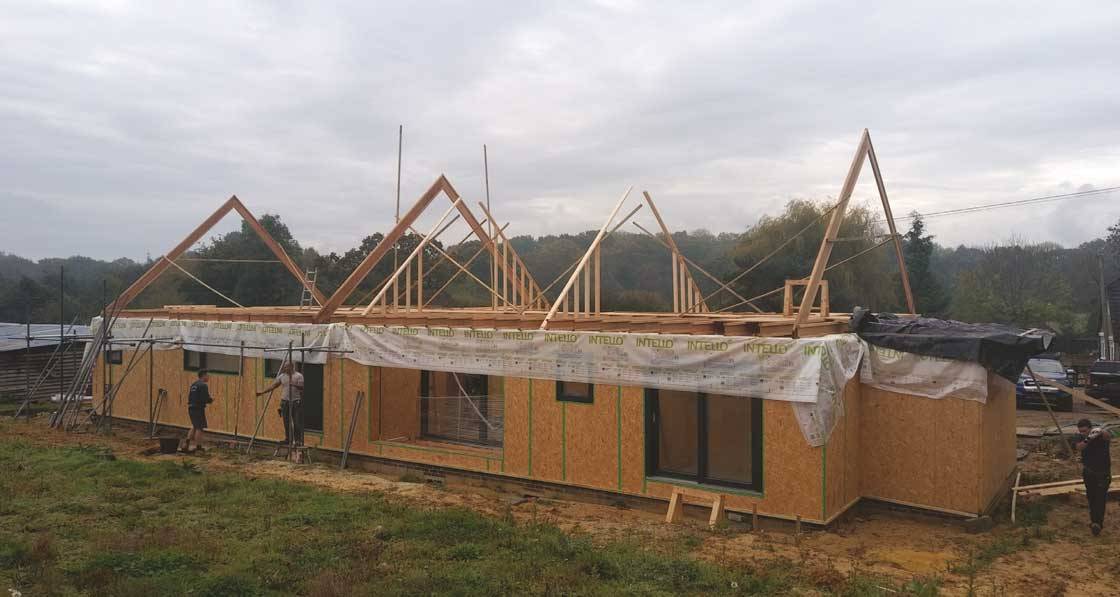
- Blogs
- Posted
Is procurement stifling natural building materials?
Is the very nature of the way that construction products are bought and sold limiting the wider proliferation of natural and sustainable materials?
This article was originally published in issue 30 of Passive House Plus magazine. Want immediate access to all back issues and exclusive extra content? Click here to subscribe for as little as €10, or click here to receive the next issue free of charge
While those in the green building sector may be informed about a diverse array of natural and ecological products, many of these have struggled to penetrate the mainstream market, which tends to rely on the same materials over and over again, like concrete and synthetic insulants.
“The uptake of natural insulation products is limited by the current systems of procurement,” says Will Kirkman of leading sustainable building materials supplier Ecomerchant.
“There is often a presumption that if an architect or self-builder wants to specify something, that everything is readily available. But how easy is it really for a specifier to get the products and materials they are looking for?”
Kirkman pointed out that mineral wool, polyurethane rigid board and polystyrene foams make up over 95% of the approximately £900 million annual total of UK insulation sales.
“The very ubiquitous nature of just a few insulation products creates the artificial impression that these are the only ones on the market,” he said. “The big builder’s merchants, for example, usually don’t stock natural insulation materials on the shop floor — so they can appear to be invisible.”
He likened this representation of choice to going into a supermarket and finding only white bread on the bread aisle — perhaps of various different types and from different manufacturers, but just white bread nonetheless. “If all you ever saw is white bread, that’s the bread you would buy,” he says.
Kirkman says this is compounded by the fact that building regulations only measure thermal performance, meaning natural materials are often overlooked by specifiers as too expensive because they are compared with plastic insulants on U-value alone.
Cultural mindsets
This point is echoed by passive house architect Jae Cotterell, one of the developers of the PH15 build system from Passivhaus Homes. PH15 is a passive house suitable timber-frame system that uses natural insulants like woodfibre and sheep wool insulation.
“Education is an enormous part of it,” Cotterell says. “If you only look at U-value, clearly the woodfibre isn’t going to perform as well as Celotex [for the same thickness].”
But there are a host of other factors that often aren’t considered when insulation is specified — these include embodied energy, carbon sequestration, decrement delay, breathability and so on.
“The negative perhaps of using a system like PH15 is that you have a thicker wall, but the advantage is you have something that addresses building biology as well as building physics.”
Cotterell also believes there is a perception, at least in the mainstream industry, that some of these natural materials carry greater risk, making the industry very slow to move away from the systems and materials they are used to.
One example is the perception that woodfibre insulation might be a fire risk, because wood is typically seen as a fuel. “Wood fibre is actually incredibly robust under fire,” Cotterell says. “The timber industry have a big job to do to deal with that cultural mindset.”
Clearly, new lines of communication are needed between those specifying building materials and those supplying sustainable alternatives. Kirkman points out that an expert supplier like Ecomerchant, who cover a huge breadth of sustainable building products, is often engaged too late in the procurement process to be able to offer advice on material choice. Typically an architect will have specified a particular product, and the contractor will then approach Ecomerchant looking for it. But if an expert supplier is engaged earlier, Kirkman says, it can offer advice on the best products and systems to use for a particular application.
It points to an issue that Passive House Plus repeatedly hears from those in the sustainable building sector: the need for a much more collaborative approach to procurement in order to deliver high quality, sustainable buildings — as opposed to the traditional approach, which is based purely on price, and which encourages cost-cutting and the worst kind of ‘value engineering’.
Indeed, Passive House Plus frequently hears about the need for designers and contractors to work together collaboratively from the early stages of a project — but perhaps there is a strong argument that expert merchants have a role to play in that process, too. Passive House Plus plans to return to the issue of procurement, and to cover it in more depth, in upcoming issues.