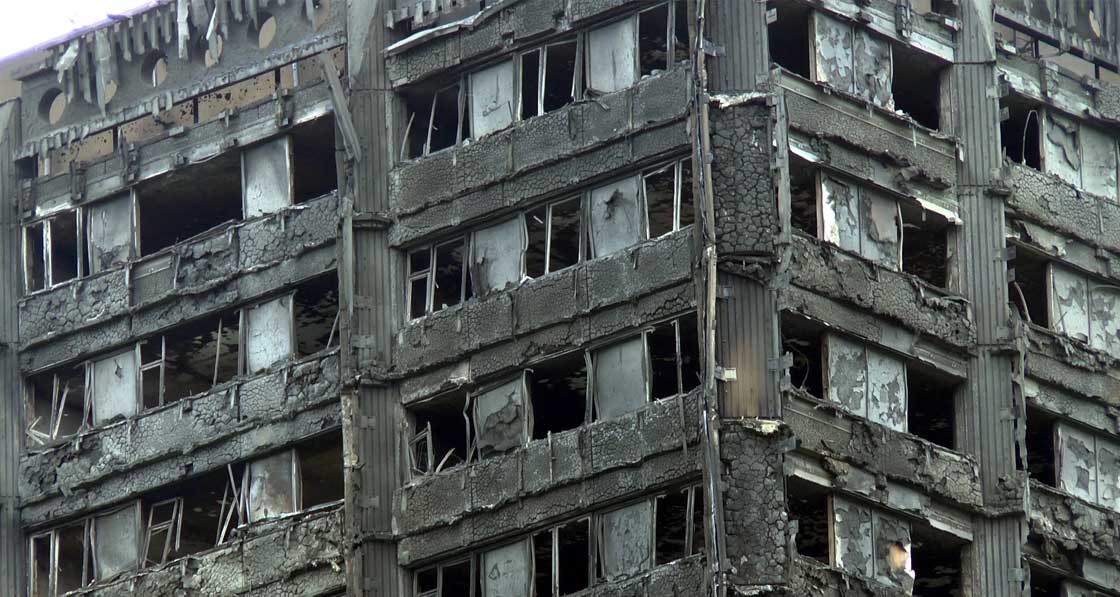
- Blogs
- Posted
Why construction contracts must change in light of Grenfell
Design-and-build contracts have become increasingly common in construction, a trend that must be reversed in light of the Grenfell Tower fire if we are to deliver safe and high quality buildings, says quantity surveyor Michael McCarthy.
This article was originally published in issue 23 of Passive House Plus magazine. Want immediate access to all back issues and exclusive extra content? Click here to subscribe for as little as €10, or click here to receive the next issue free of charge
When the Grenfell Tower tragedy struck on 14 June, people around the world looked on in horror at the building ablaze on their TV screens.
In one of the wealthiest boroughs in one of the wealthiest countries in the world, at least 80 helpless residents died for the sake of a cost-cutting decision that saved a relatively small amount of money.
In a recent article in the Guardian (4 September 2017), the new head of the RIBA, Ben Derbyshire, identified one of the main weaknesses that led to the Grenfell Tower tragedy. Namely, the side-lining of the architect’s role in the design process through the use of design-and-build (D&B) contracts, in which a main contractor is appointed to both design and construct the project, rather than an architect or engineer leading the design processes.
In such contracts, the lead contractor will often sub-contract design work to an architecture or engineering practice, but that firm may not have the same level of design control or involvement as in a contract where the design is controlled by the client.
The growth in the use of D&B contracts has often little to do with the design component that a contractor is to undertake and more to do with the transfer of risk. A key feature of D&B contacts is the substitution of one type of material for another, often cheaper, in a process commonly referred to as ‘value engineering’.
Value engineering should be a process of finding cost savings by getting a building or elements of a building to provide the same functionality and quality for less cost. It should be carried out at design development stage in conjunction with all the stakeholders and the design team.
However, it has become corrupted to mean substituting one type of material for a cheaper one at a later stage of the design process. Value engineering, as we now know it, should never substitute a material for one of lower quality. This is simply changing the specification. In the case of Grenfell, this was done by the project quantity surveyor at the behest of the client, Kensington & Chelsea Tenant Management Organisation (KCTMO). One crucial ‘value engineering’ decision made was the reduction in the cladding specification from fire resistant zinc cladding to aluminium cladding with a flammable core, saving £293,368 in the process (Robert Booth, the Guardian, 6 July 2017).
How design-and-build should work When a D&B project goes to tender, there should be a detailed employer’s requirements document, which is a performance specification a contractor is to achieve. How this is achieved is often left to the contractor. The design should typically be 30% to 50% developed, allowing the contractor to complete the design.
The instances where D&B should be used are when there is a pressing time schedule that does not allow for complete design development or in repeat generic design where there is a choice of systems. In reality, D&B is being used more widely than this, often because it is a convenient method of risk transfer.
Many D&B tenders often are 80% to 90% designed at tender stage. Up to tender stage, the design team is under the control of the client, so the contractor has to ‘guess’ at the un-designed portion. Only after tender is the design team ‘novated’ across to the contractor. In this instance, contractors have little influence on the design in reality. They have to assess the cost risk of the remaining 10-20% and allow for it in their tender. This leaves much of the remainder of design decisions to be mainly choice of product.
Because D&B tenders involve contractors producing their own bills of quantities (BOQs), it transfers the measurement and quantification risk to the contractor. It also allows contractors to make calculated risk assessments on delivery and methodology.
The downside is that every contractor bidding for the project must now produce their own BOQ, adding considerably to overall costs of tendering for the industry. This loss of quantification control also leads to a reduction in budgetary control on the part of quantity surveyors, as the D&B contractor now produces and controls the quantification process.
Taking back control in the 5D BIM age This need not be the case anymore. The advent of BIM and better cost management methods make it possible to allow architects and design teams to regain the control that they have lost due to D&B contracts.
‘5D’ is the prefix that denotes the use of BIM for cost management. It is an underused power house of information that can revolutionise cost management and consequently, quality control.
Combining 5D BIM with the ‘New Rules of Measurement’ (NRM), published by RICS, makes this even more powerful. The NRM suite is a far superior method of measurement than either the old SMM7 in the UK and ARM4 in Ireland. In fact, NRM is a whole life cycle cost management system that has benefit to asset operators far beyond completion date.
By using 5D BIM methodologies, QS practices can offer real time implications of design changes and help designers and clients to find the optimal balance of quality, size and cost. Forms of contract can be devised or amended in order to get the balance of cost, risk, quality and responsibility right.
For architects to take back control of the design and specification, there also needs to be control and certainty of costs. Cost and design control go hand in hand. In order to avoid the mistakes of the past, architects should regain their rightful place as the lead position on projects. To do that, methods of cost management, procurement and the appropriate allocation of risk in each circumstance must be reassessed.
D&B contracts have their place, but their current level of use, in my view, should be reconsidered. The full facts of what happened in the Grenfell Tower tragedy have yet to be concluded. What we do know is that greater design team control and autonomy on all aspects of projects will mitigate and prevent the kinds of decisions that led to this disaster. By fully using the tools and methodologies that are now at our disposal in a collaborative way, everyone’s need for safety, quality and viability can be met.