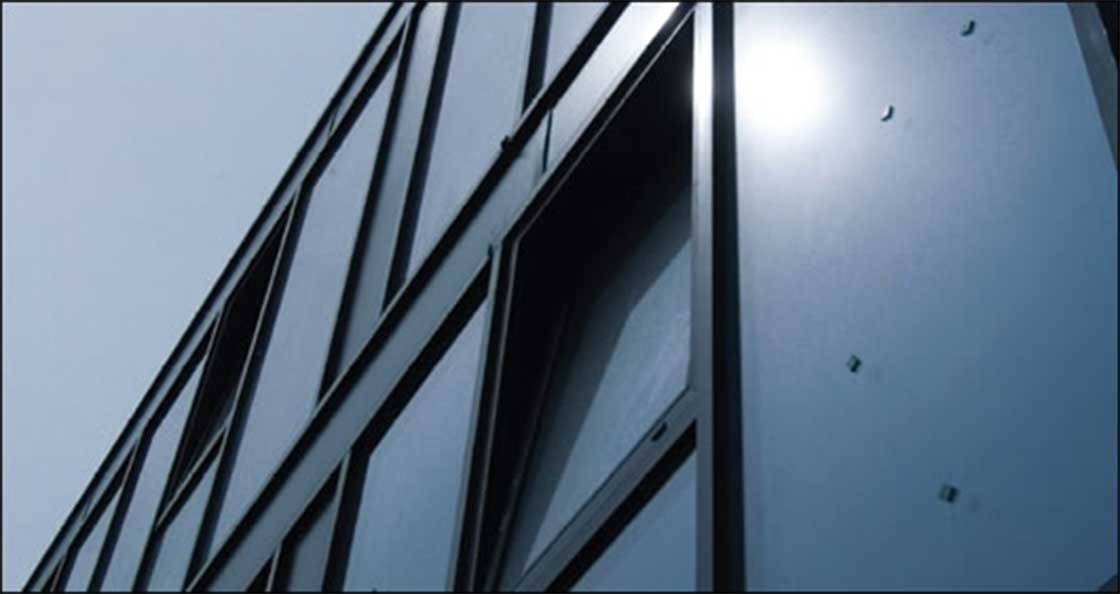
- Design Approaches
- Posted
Mixed Signals
As Construct Ireland goes to press, what is anticipated to be one of the lowest energy buildings in Ireland's recent history is nearing completion. John Hearne visited the site to find out how a combination of design ingenuity and modern technology is set to deliver stunning results.
A new mixed-use development on Forster Street in Galway promises to be among the most energy efficient in the country. Incorporating a range of sustainable innovations, stakeholders aim to deliver a building that will dramatically exceed conventional building standards.
Chris Croly is a director of environmental engineering with energy consultants on the project, Building Design Partnership (BDP). "Detailed design dynamic simulations undertaken by BDP have shown that the estimated energy usage for heating purposes is only 6kWh/m2/yr and the total energy use, inclusive of end user equipment is likely to be in the order of 40kWh/m2/yr, resulting in one of the lowest energy buildings in the country. The design team will be monitoring the building's energy use during its first two years of operation and it will be interesting to see the results." It certainly will. Forster Street is a mixed development, and as such there are no definitive energy benchmarks that can be applied. Comparisons are available however, says Croly. "CIBSE (the Chartered Institution of Building Services Engineers) guide F provides various benchmarks for buildings constructed to 'good practice' standards and an area weighted calculation implies that the energy use of this type of development if built to good practice standards would be in the order of 110kWh/m2/yr."
Since the owner first approached Peter Keavney of the Galway Energy Agency eight years ago, energy conservation has informed all elements of the design and construction process. "It's an excellent project," says Keavney. "Part of our scope was to target passive design techniques, so we set up the specification for target U-values and the fabric insulation levels." Energy consultant at the concept stage, Keavney brought Heffernan and Associates Architects of Barna, Co. Galway into the project. MD David Heffernan has a long history of driving sustainability in Irish commercial and domestic design. In Forster Street, he met a particular challenge. Wedged between two existing buildings, limitations in height, space and orientation reduced the suite of technologies available to the team. Heffernan is keen to stress however that the starting point for the project was not the active technologies that have also been included but the passive elements. "If you get the basic things right, like orientation, insulation, infiltration, and ventilation, you're cutting 50% of potential running costs straight away. Then you add the active measures like solar panels, the boreholes and the heat pump."
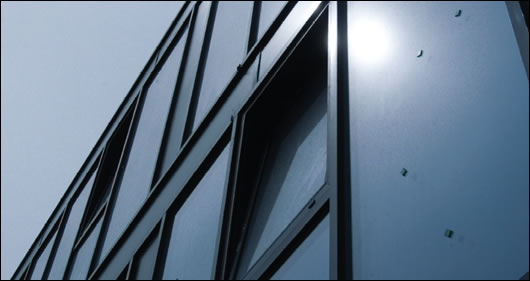
Visually, the most striking element of the design is the façade. A triple-glazed curtain wall designed by Hodgins Architectural Facades, faces south east onto Forster Street, allowing ample scope for passive solar gain
A triple-glazed curtain wall provided and constructed by Hodgins Architectural Facades, it faces south east onto Forster Street, allowing ample scope for passive solar gain during the early morning when it is most beneficial. Thermal modelling by BDP suggested that a glazing solar transmittance of 50% would optimise the building's solar performance; delivering sufficient useful solar gain to reduce the need for further energy sources, yet reducing both glare and the risk of over-heating. "The glass solar transmittance is controlled by a layer on the inner pane of glass." Diarmuid Hynes of Heffernan & Associates explains. "It's low-e glass on the inner-most pane, with the transmittance film on the outside of the inner pane. The units are filled with Argon gas, to control the level of heat gain and to insulate the units to achieve a U-value of 1.0." That U-value refers to the entire unit; for the glass in isolation, the value comes in at 0.7.
With highly insulated glazing comprising a substantial portion of the building's external envelope, the design team decided to continue in that vein by installing significant levels of insulation on the outside of the structure. Sandwiched between the two adjoining buildings, both north and south gables are constructed of 100mm block work. On the outside of the blocks, there are two layers of 70mm Kingspan TW53, a rigid urethane insulation with a thermal conductivity of between 0.026 and 0.028 "Outside that," Hynes continues, "we've a radon barrier as a water proof membrane. On the outside of that again, there's a geotextile system and any vapour that builds up will run down into a French drain, a land drain that runs all the way across the perimeter, under the slab, so any water, any vapour that builds up between us and next door runs down the geotextile…It's gathered up by the French or land drain and fed into the surface water system." Another double layer of TW53 runs below the slab while in the roof, a tapered insulation product, Kingspan TR26 joins up with the insulation in the walls. "In a traditional build, you would have your 300mm cavity wall with your insulation in between." Hynes explains. "In this building, the glazing is the insulation on the outside of the curtain walling system. The TW53 forms your insulation on the North East and South West Gables and that connects then with the insulation under the slab and outside the envelope. It's like wrapping the entire thing in bubble wrap to keep it warm, so all the insulation is on the outside, it's under rather than over the slab, it's outside the walls rather than inside the walls and it's above the roof structure, all the insulation meets to create a thermal envelope." One of the advantages of externalising the insulation lies in the fact that you can then use the concrete mass as a thermal store. "You're using the floor slab as a battery or heat store. If you insulate on top of the floor slab, you're isolating it thermally from your heating, but if you keep it within the building and the insulation's on the outside, you've got a concrete shell. That then slows the heating and cooling and the concrete becomes a thermal store. The other significant value of this insulation method is that it removes thermal bridges from the structure and we detailed every junction in the building to design out thermal bridges"
The building may be mistaken for having a large glazed façade that produces a larger heat loss than necessary but it must be remembered that the building is sandwiched between two other structures that provide perfect insulation to tow of the facades and it is therefore important to maximise light transmission from the remaining facades.
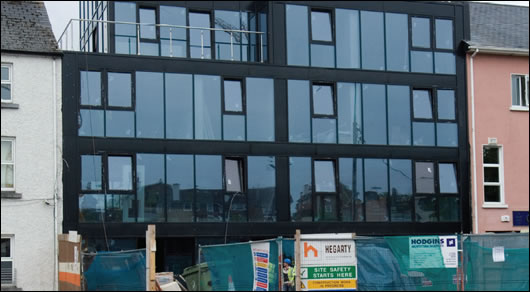
The new development at Forster Street is wedged between two buildings, a challenge which resulted in a design that makes the most of natural light where available
Within the building, design and fabric feed directly into how the development will ultimately be used. Each unit is thermally broken. Actis Multi Foil insulation, with an advertised U value of 0.2 separates each floor from the one below it. "All we want this to do." says Hynes, "is to stop heat transfer from one unit to the next, so if the occupants upstairs are gone away during the winter and the occupants downstairs have their heating on full, that the heat doesn't dissipate to the floors above or below. We are effectively thermally separating each apartment." Particular thought has also gone into the energy requirements of the common spaces; stairwells, hallways and corridors. "You'll see a lot of older buildings heating and even overheating stairwells and corridors where there's no habitable space. It's a total waste of energy," continues Hynes. The main stairwell is situated at the back of the building, on the 'cold side' of the construction. It requires no heat, but traditional building methods cannot prevent cold bridging occurring between the heated and unheated parts of a structure. A new product called 'Isokorb' from German company Schock gets round the problem. "It's a system whereby the reinforcing steel travels through a sheet of insulation. The rebar is arranged in such a way that it doesn't cause a cold bridge, but it's still structurally binding the two sides of the structure together. It's got blocks in it every now and again to stop any bending moments from one slab to the other. They are tied together with the Isokorb but it's thermally broken. We don't have to heat the stairwell at all, so it brings the overall heat load requirments for the building right down."
Sealing the external envelope was the next step. "The most important feature in the design of a low energy building is the prevention of air leakage." says Chris Croly of BDP. "The design target for building air leakage has been set at 3m3/m2/yr." Achieving that level of air-tightness on a building of this nature required a lot of thought and a high level of on-site training and discussion. "We used the main building elements to form the air seal." Croly explains. "In this case, the majority of the building is a glazed framing system, so the design team discussed air tightness in detail with the system supplier and in particular how all joints would be sealed. Once the framing is secure, the main areas of concern were the joints with the roof and the floor, as well as the main doors. Air tight design is largely common sense, we sat down as a team and identified where air leakage was most likely to occur and what could be done to minimise it. The same process was carried out with the builder on site. We met with him and outlined the importance of making sure that everyone on site understood that it's an air tight building." Periodic inspections combine with continuous on-site liaison with contractors to ensure that the high levels of air-tightness aspired to are achieved.
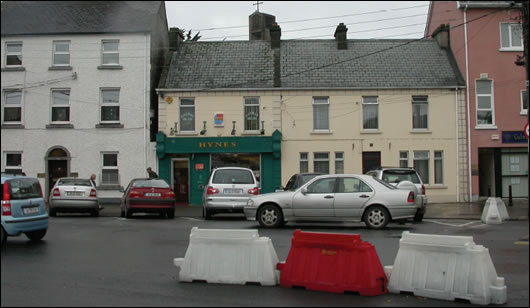
The buildings originally on the site were demolished to make way for the new development
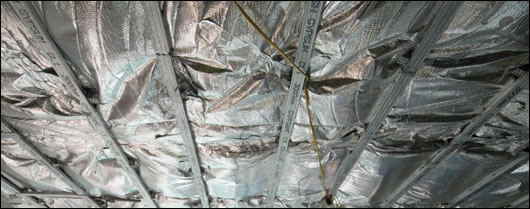
Actis Multi Foil insulation, with an advertised U-value of 0.2, separates each floor from the one below it. "All we want this to do," says Hynes, "is to stop heat transfer from one unit to the next, so if the guy upstairs is gone away during the winter and the guy downstairs has his heating on full, that it doesn't go upstairs."
A highly sealed domestic building can benefits from mechanical ventilation during winter to supply background fresh air. In Forster Street, this works in tandem with a high efficiency heat exchanger. "Mechanical supplies are particularly beneficial in the bedrooms," says Croly. "We'd have concerns that if we relied purely on the occupants to open the windows, they might not get an adequate supply of fresh air due to concerns over draughts and noise (particularly in this city centre location) that lead them to close windows, particularly at night when they're asleep, so mechanical ventilation with heat recovery was installed to provide a minimum level of background fresh air. The energy usage of the fans is balanced by the heat energy recovered so the use of a mechanical system does not result in a net increase in energy, while offering a guaranteed level of fresh air.
"As part of the full building simulations we carried out an exercise to study the relative energy and cost savings of the mechanical ventilation system over a natural ventilation system," says Croly. "The results showed that in cost terms (when filter replacement costs are included) there was no significant net saving through the installation of the mechanical ventilation system but there was a slight reduction in carbon dioxide emissions associated with energy usage with the mechanical option. The comfort provided by the mechanical option is however the most important reason for its inclusion and there is no associated energy penalty.
The three air handling units in the building are Vent Axia Air Minder 290 systems from the Aervent Group. Dave Cussen of the company explains that in addition to potential energy savings, the system ensures a high level of air quality throughout the building. "The fact that there's continuous extract and continuous supply reduces condensation in bathrooms, prevents mould growth, it prevents black lines around bath and shower, it prevents mildew on your walls inside and condensation on your windows…The fact that there's a filter in it reduces dust particles and dust mites in your house. Also, a big factor - on Forster Street this is a huge thing - the fact that you've continuous ventilation means you don't have to have window vents or wall vents, which means that you have a very high reduction in noise from outside. Basically the noise ingress through the ducting system is practically nil. There'd be more noise through a closed window." Boasting an efficiency rating of 90%, low noise motors and automatic controls, the system includes a 'night-time set-back' feature which allows the unit to be 'set-back' to a very low speed to facilitate energy savings. In addition, the unit carries a fan-specific power of 0.8, Cussen explains. "Fan specific power is very important, it's watts per litre per second. The system assists with achieving a good result when a DEAP calculation is performed, andthe HRV will therefore help you with your energy rating."
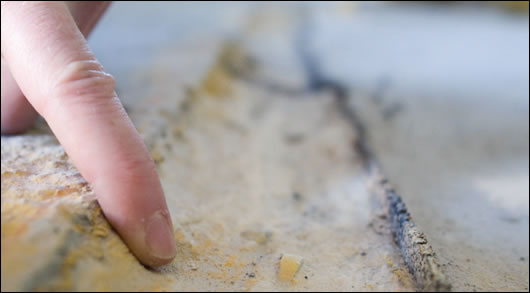
Insulation covering the Isokorb system, which prevents cold bridging between the occupied and landlord areas
While the building will take most of its heat through occupancy and passive solar gains, a heat source is still required. "A low energy building," says Chris Croly of BDP, "constructed to these standards does not require any heating energy when it is occupied but a heating system is still needed to bring the building up to temperature after a period without use. For example, in the office areas, a small amount of heating will be required to bring the building back up to temperature first thing in the morning before occupation." The underfloor heating system installed is powered by a small, closed-loop vertical bore heat pump. Three 135m holes bored into the ground beneath the building house the vertical array which is hooked up to two small heat pumps, supplied by Dunstar. "The efficiency of a heat pump increases significantly as its flow temperature decreases." says Croly. "Due to the low heat load of the building, a lower than normal flow temperature has been set for the heat pump, maximising its efficiency. The main heating pumps are specified with variable speed drives that automatically reduce pumping energy to match the building's load profile. BDP have carefully designed the controls system to distribute heat only when required and each space has local temperature controls." As Peter Keavney points out, this is the first community heating system installed in Galway.
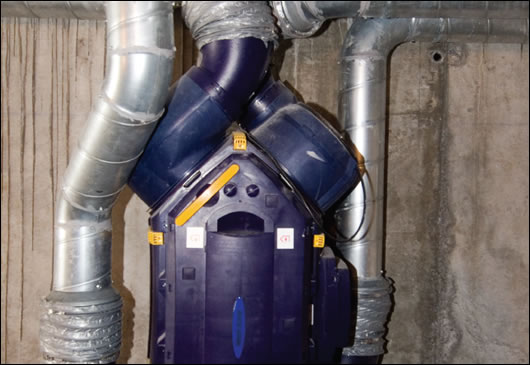
Boasting an efficiency rating of 90%, low noise motors and automatic controls, the Vent Axia Air Minder heat recovery ventilation system includes a 'night-time set-back' feature which allows the unit to be 'set-back' to a very low speed to facilitate energy savings
With passive solar gain providing most of the space heating requirements, a solar array on the roof of the building will look after more than 65% of the building's hot-water needs. Flat plate, high efficiency panels from Arcon in Denmark are provided and as Construct Ireland goes to press, are to be fitted by Irish Arcon agent Nivektron. Kevin Noone of the company says that design specification necessitated lower profile panels than those typically used on commercial installations. "Height restrictions, that's really why. They have got anti-reflex prismatic glass, they have got Teflon coatings on them, the integrated pipe = system, they're the same standard that I always use. They're more low profile, they're going to be less than 1m high off the roof level, and that's really why we've gone down that route." The pumps used have been modulated to facilitate reduced flow for lower temperatures, thereby increasing efficiency, while monitoring equipment has been installed to keep an eye on the performance of the array.
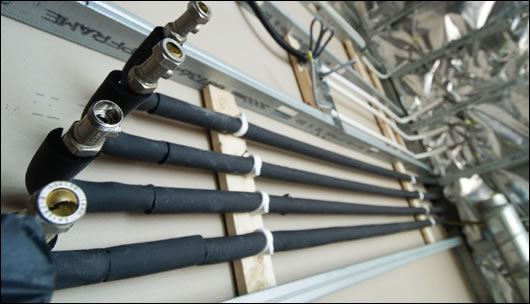
Insulated pipework distributes heated water from the group heating system throughout the building
Because all nine units rely on one centralised source of hot water, the plumbing has to be adapted to recognise that. "A secondary return loop is provided to comply with legionella legislation, but this continuous hot water circulation has the added benefit of ensuring that hot water will always be available to all outlets, reducing water wastage that is associated with running taps warm in domestic buildings," Diarmuid Hynes of Heffernan & Associates explains. "If I'm on the top level and I turn on my tap, I'm not waiting half an hour for the water to come all the way up to me. The hot water's waiting just below the sink because it's on a loop." With the bulk of hot water coming from the solar array, a small condensing gas boiler, supplied by RVR in Kenmare provides the necessary back up. "As the solar panels will generate a large amount of hot water during the summer, more than is required by the building, it is necessary to deal with the excess heat. The first stage is to use local blending valves on all outlets and this allows the water temperature in the cylinder to rise slightly higher than it normally would without loosing any useful solar heat. The second stage is to dump excess heat into the under floor heating system where it is dissipated although this will be a very rare necessity."
The building's low energy spec also extends to water use. Conventional developments of this size would typically require a pumped hot and cold water system. In Forster street, the design team opted instead for a gravity fed system. This option dramatically reduces consumption because the water is no longer pressurised but requires careful selection of fittings. David Armstrong of BDP continues. "The building also contains several other water conservation measures. We have dual flush systems, low flow taps, low flow shower head units, body-form baths, and percussion taps in public and office areas to prevent taps being left on. We've significantly reduced the amount of water that the units would potentially use." He points out too that these technologies are no longer difficult to source or install. "Basically all of these are off-the-shelf items, they're easily replaceable, and easily maintained. That's the beauty of the whole thing. If you do have a problem, you don't have to spend a fortune on maintenance, you don't have to go looking for exotic parts, they're all there to be picked up."
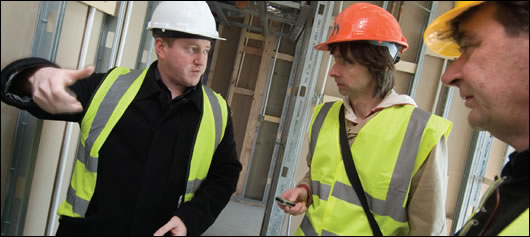
Diarmuid Hynes (left) and David Heffernan, founder of HAA (right) explaining the intricacies of the building to Construct Ireland's John Hearne (centre)
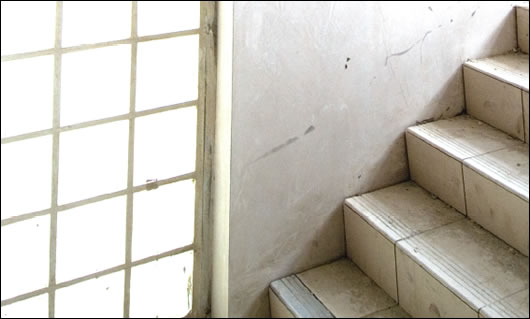
1 hour fire rated glass blocks bring natural light into the stairwells, thus reducing the need for electrical lighting
Daylight is everywhere in the building, even in places you would never expect to find it. "We've installed skytubes in some of the ensuites." says Diarmuid Hynes. "They're rooms within a room in the middle of the building, so they're nowhere near external windows, but we've still managed to get in natural light." Similarly, one hour fire-rated glass blocks in the stairwells obviate the need for artificial light by allowing greater transmission of natural light. Where it is required, all fittings are low energy and where possible, they're strictly controlled. All common areas are illuminated with 28 watt CFLs with motion detectors, while individual areas - stairwells, corridors, entrance halls - are monitored by separate infra-red sensors so all are not lit simultaneously. The apartments feature a combination of CFLs and LED based down-lighters. "LV feature down-lighters are often used in domestic buildings without understanding the energy implications." says Chris Croly. "They are notoriously inefficient and convert the majority of the electricity they consume into heat. The Forster street development uses LED based down-lighters where feature lighting is required. These fittings have only recently become available on the market and are continuously improving." The power output on conventional down-lighters is 50 Watts. On LED based down-lighters, it's approximately 2Watts.
To encourage energy efficient lamp replacement by future tenants of the building, a number of the apartments feature light fittings that can only = take CFL bulbs. For safety reasons, Chris Murphy of electrical contractor Tim Kelly Electrical explains that back up switching is required in areas with motion and daylight detectors. "You have to provide override switching in the unlikely event that things go wrong,…If you come into the corridor and the light doesn't come on, you can turn it on yourself, but what happens normally with the standard light switch is that people turn on the light and they walk away and the light is left on behind them forever. These ones go off after a predetermined amount of time." Apart from 49 watt fluorescent lighting in the kitchen and plant-room, the highest output for any lighting fixture in the building is 28 watts.
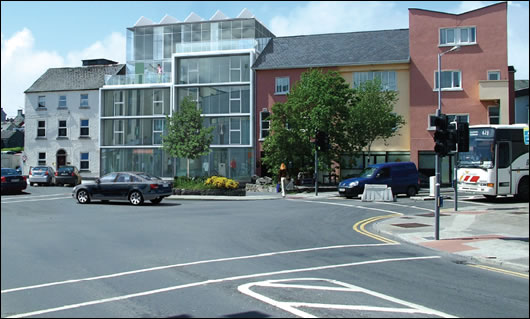
A computer rendering by Proviz reveals the attractive façade that the finished building will present
Given the array and interdependence of technologies in the building, intelligent control is essential in bringing the whole package together and making it work for the people who have had no role in the design and build stages - the occupants. "It's one building with lots of different occupants in it." says Chris Croly. "It's important that we're not relying on the occupants to tell the control system what it needs to do, that we're not reliant on people turning the heating off when they're not there, so the controls are intelligent. They sense the load. If the controls realise that the building has no load, they will automatically shut the building down. We've tried to minimise the amount of controls that people have to interface with. We have simple switches and simple controls so they won't see the building management system behind it. These are literally switches on the wall and timers on the heating." Additionally, he acknowledges the need for some interaction between the designers and the end-users. "We'll be leaving them with a leaflet explaining how the building works and what to do, but hopefully we'll also have the opportunity to sit down with them and have a users meeting to explain how it all works too. The building's developer plans to use one of the retail units. He will have a permanent presence in the building and will be a contact point for the fostering of this low energy community."
Indeed, an important element of this building is the integration of several types of accommodation into a single, mixed use low energy building. In theory an occupant of a low energy apartment could work in the low energy office below and purchase their groceries in the low energy shop below. If this were to be the case, this landmark building could offer a blueprint for sustainable living that extends far beyond its admittedly excellent energy performance. l
Selected project team members:
Architect: Heffernan & Associates
M & E Consultant: BDP
Energy consultant: Galway Energy Agency
Building contractor: PJ Hegarty
Electrical contractor: Tim Kelly Electrical
Glazing: Hodgins Architectural Facades
Insulation: Kingspan & Ecoquilt
Heat recovery ventilation: Aervent Group
Glass blocks: Roadstone
Solar panels: Nivektron
Heat pump: Dunstar
- Articles
- Design Approaches
- Mixed Signals
- mixed use development
- Galway
- building envelope
- urethane insulation
- heat pumps
- heat recovery ventilation
Related items
-
Grant integrated heating packages installed for 61 homes in Rathdrum
-
Lung disease patient: Zehnder MVHR “the best thing I’ve ever had”
-
ProAir MVHR unit achieves up to 95% efficiency
-
Zehnder launches MVHR system for tight spaces
-
Offaly new build installs Grant integrated heating package
-
Is it okay to retrofit heat pumps before building fabric?
-
Hevac launches hot water heat pump with green refrigerant
-
Viessmann launch two new compact heat pumps
-
Mitsubishi heat pumps 6-7 times lower CO2 than condensing gas boilers
-
Top 5 questions about specifying structural thermal breaks
-
Major new grants for retrofit & insulation announced
-
Daikin launches new Altherma 3 R heat pumps