- Passive Housing
- Posted
Hooray for Hollywood
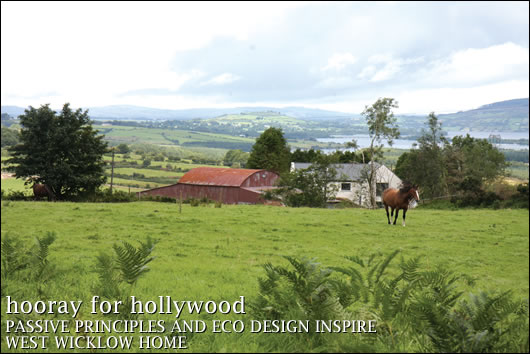
When residents of Hollywood solemnly and publicly state the need to combat climate change, it is easy to reject as self-righteous, opportunistic bleating. When it’s a resident of Hollywood, County Wicklow, and the environmental statement is in the form of a poroton-block house infused with sustainable features, it provokes an altogether different response, as Lenny Antonelli reveals.
Perched on a quiet hilltop just outside the village of Hollywood, County Wicklow is a house with a deceptive appearance. What looks like a vernacular, block-built structure is actually a poroton house that verges on passive standards. The vision of Colmán McSweeney and his wife Elaine, this two-storey, 2,800 square foot family home boasts a panoramic hilltop location and a host of green features.
Poroton – the industry term for terracotta block – is simply clay that has been fired to about 1000°C. Poroton blocks have numerous perforations, which reduce their weight while maintaining strength and increasing thermal resistance. Cavities in the block are filled with perlite - a type of volcanic ash. “They take volcanic ash and bake it,” Colmán McSweeney says. “It expands and forms a good insulator.”
The 425mm T8 poroton blocks, that Wexford company Formula Building Technology (FBT) supplied him, boast a U-value of 0.18 W/m2K before any render or plaster is added – putting them within touching distance of the 0.175 W/m2K wall U-value standard recommended by SEI’s recently published document, Passive homes: Guidelines for the design and construction of passive house dwellings in Ireland.
McSweeney says he chose poroton because, when compared with timber frame, he felt it was able to deliver exceptional energy performance at a better price. He picked local builder Darren Beehan for the job, even though Beehan hadn’t worked with poroton before. “I thought that it was such a simple system, why bother getting in a specialist? Why not just go with a local builder?” McSweeney was also keen to demonstrate that the skills of low energy building could be easily adapted. “Other local builders can replicate what we’ve done,” he says.
“I was sceptical at the start,” Beehan admits, “but it was great to get a run at something different. It keeps you on your toes. It’s a good system, and it’s fairly easy. The blocks are plastered with an insulating plaster supplied by FBT. The two storey structure went up in eight to ten days.” Beehan is currently pricing work for another poroton house.
Sheep wool insulation is installed in the attic. “The total depth is 300mm, which is 150mm in between the joists and 150mm across on top,” David Pierce of Sheepwool Insulation says. “That will have a U-value of 0.149 W/m2K. Typically nowadays you need a depth of 250mm to meet the building regulations U-value of 0.16 W/m2K, so this goes a bit further. ”
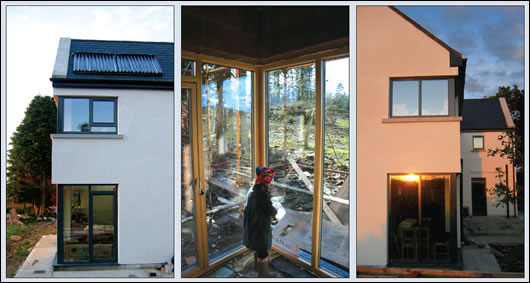
The glazed corner adds an interesting design feature
Though the house is plumbed for radiators, McSweeney hopes he won’t need to install them. Heating requirements are reduced by use of a Vortice HRU ECO 3 mechanical ventilation heat recovery (MVHR) system, with space heating produced by two Tonwerk masonry log stoves supplied by Frontier Energy.
The MVHR system works, in essence, like any other - extracting humid, stale air from kitchens, bathrooms and WCs and using it to heat fresh incoming air, which is then supplied to living rooms and bedrooms. “It provides a healthy comfortable living environment while retaining as much heat as possible within the dwelling,” says Niall O’Toole of ATC Electrical and Mechanical, who supplied the system.
The unit is SAP Appendix Q registered – a must for all good heat recovery systems, as without it a default efficiency must be entered into the DEAP software, which would have an adverse effect on the building energy rating. The HRU ECO 3 achieves efficiencies ranges from 86 to 93 per cent, subject to the number of wet rooms in the house. In this case ATC advised on optimal placing of the unit to ensure the best efficiency possible for the house. A stair ladder has been placed beside the unit to allow easy access for regular servicing. It is equipped with a summer by-pass feature that enables fresh air to enter the house without being pre-heated during the summer months. “This helps to cool the house down during the summer,” O’Toole adds.
“Heat recovery ventilation has come a long way in the last few years,” he says. “Better heat exchangers and low energy DC/EC motors mean that a higher percentage of the heat put into the house can be recovered at a much lower electrical consumption than before.”
Downstairs are the masonry log stoves, which supplement the MVHR system. Concrete acts as thermal mass in the stoves, absorbing heat and radiating it out slowly into the house. “You burn logs in it for an hour and a half and it radiates heat for up to eight hours,” McSweeney says. “The stoves heat up internally to about 1000oC, but you can touch the outside as it’s at about 60oC. It radiates very slowly.” “During the winter we’ll probably light the stove in the living room once or twice a day. When it’s really cold we’ll fall back on the one in the office. There won’t be draught exclusion under the door of the living room, so the heat can get out, and go up the stairs and drift into the bedrooms. The air coming in from the MVHR system will be about 18oC, so the stove will just boost the heat by that extra few degrees.” Ever eager to reduce the building’s carbon footprint, McSweeney ruled out wood pellets because of the embodied energy in their processing and transportation. He considered wood chips, but says he couldn’t find a suitably sized system at the right price. He’s currently bartering for fuel - he designed a local tree surgeon’s website in return for supply of timber.
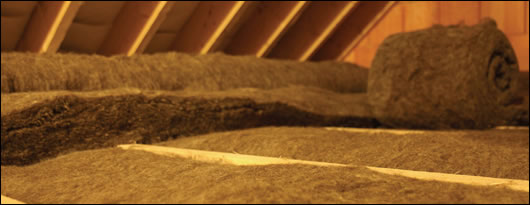
The cavities in the T8 poroton blocks are filled with perlite – a type of volcanic ash
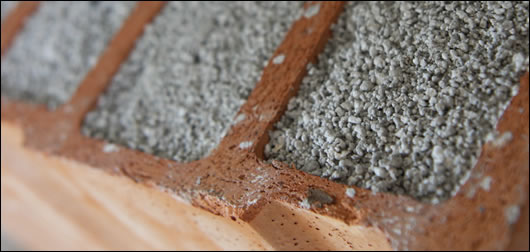
Sheep wool insulation is installed in the attic
An eight square metre Calpak vacuum tube solar array connected to a 500 litre TiSun Pro-Clean stratified tank cylinder will supply most of the house’s hot water. Those familiar with solar thermal technology might baulk at the size of the system. McSweeney explains: “The advice on solar panels was to go for a three square metre panel linked to a 200 litre tank, for a system that would provide 50 per cent of our hot water needs.”
“However that assumes a conventional heating system is in place. We opted instead for a 500 litre buffer tank linked to an eight square metre array, which should allow us to rely on solar for hot water from March to September or October. The buffer tank is so big that if we get two cloudy days, we won’t need any back-up heating. In June, July and August we expect to have a surplus of 200 to 300 litres of hot water a day - we might use it for a pool in the garden.”
What prompted McSweeney to choose vacuum tubes over flat plates? “The tubes mightn’t be as efficient as the panels at capturing heat in the middle of the summer,” he says, “but for low sun conditions you’ll get more out of the tubes then the panels.”
Des Flynn of RVR, the Kenmare-based heating company who supplied the solar thermal system, explains how it works. “The cylinder has a stratifier with a coil inside that is heated by the solar tubes. Hot water from the stratifier is loaded in at the top of the 500 litre cylinder. There’s a 45 litre capacity coil inside the cylinder, which is heated by the hot water that enters from the stratifier.”
McSweeney elaborates: “You get a system that prioritises hot water before space heating. First it fills up the hot water for domestic use, and then it starts filling up the buffer which could be used for central heating. Another major plus for us was how the TiSun cylinder addresses the issue of Legionella occurring, without having to unnecessarily heat the tank.”
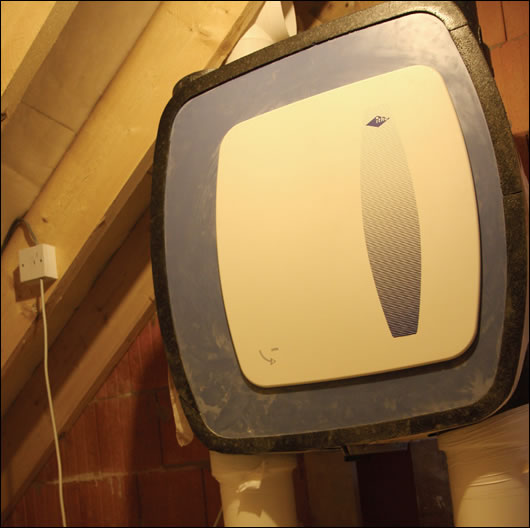
The Vortice HRU ECO 3 heat recovery ventilation system
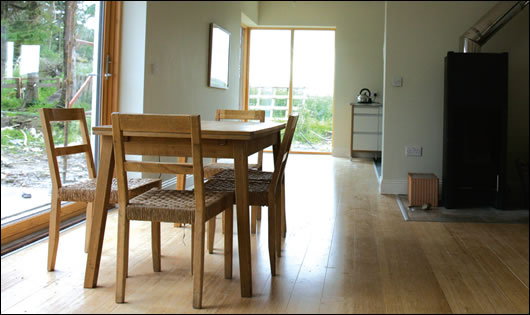
The open plan, bamboo-floored living room with Tonwerk masonry stove to right
Glazing is obviously crucial in any low energy build - most of the windows in the house are NorDan NTech passive windows, except for one sliding door and two French doors. “The sliding doors will lead out to a sunroom eventually,” McSweeney explains. “We don’t have the budget for the sunroom right now.” Once the sunroom is built though, the kitchen will sit behind three layers of glazing - hence why double instead of triple-glazed sliding doors were chosen.
The NTech passive units are timber-framed, triple glazed, and boast low e-coatings, warm edge spacer bars, two cavities with argon fill and most importantly, superb performance – NorDan quote an immensely impressive U-value of 0.7 W/m2K on the whole window including frame. The U-values for the double-glazed sliding living room door – also sourced from Nordan – and solid front door are 1.3 W/m2K and 1.0 W/m2K respectively.
The windows had not been commissioned prior to the first blower door test and consequently, although they performed well, the test did not reflect their optimum performance. NorDan’s John McMenamy explains: “It would be standard practice to install the windows during construction, and then when the building is complete, a service engineer would go and check all units to ensure that everything is operating correctly.”
“On the day of the second blower door test, two service engineers from Norway visited the site, one was an airtightness expert, and the other was from NorDan’s technical department. They found some minor issues – two of the window seals were slightly out of place, and two windows had the wrong type of receiver, so the window wasn’t closing in fully, though it was hard to spot that with the naked eye.”
The house got a result of six air changes per hour at 50 Pascals in the first blower door test. While a decent result, it wouldn’t make the house sufficiently airtight for the MVHR unit to operate at optimal levels. McSweeney explains the result: “The house wasn't prepared for the blower door test. We made no effort for airtightness because, being naive at the time, we didn't realise the importance. It was only after the test was done that the penny dropped. It hit me like a concrete block. We should have had a vapour membrane under the ceiling, but we didn’t. I suppose it’s a matter of learning as you go along.”
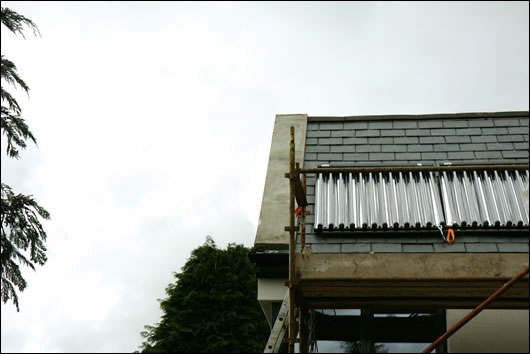
Calpax vacuum tube solar panels being installed
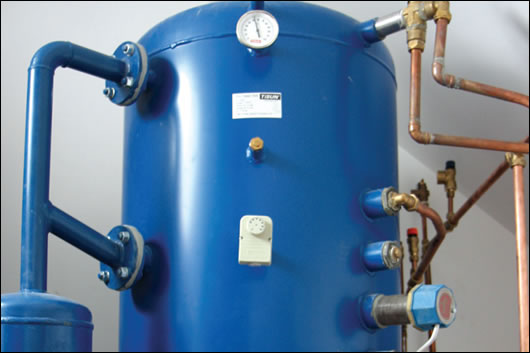
The 500 litre TiSun Pro-Clean stratified tank cylinder
McSweeney admits that lack of attention to airtightness was a mistake, but says he’s keen for others to learn from his oversights – one of the reasons he contacted Construct Ireland to publicise the project in the first place, having been encouraged to do so by another contributor to Construct Ireland’s online forum. Indeed, a dialogue with the Construct Ireland team affected the latter stages of the build in several unexpected ways. McSweeney says that articles in previous editions and discussions on the forum at ConstructIreland.ie had already been a source of much useful free advice, but the role of the magazine took on another dimension when he first contacted editor Jeff Colley in July to propose featuring the house.
According to McSweeney it was prompting from Construct Ireland that persuaded him to install the solar thermal system immediately rather than put it on the long finger, and he adds that the magazine’s imminent coverage of the house helped persuade him to choose sheep wool over rockwool for the attic insulation. McSweeney also credits Colley with urging him to test the building’s airtightness. “Without Construct Ireland’s input, the full extent of the importance of going airtight wouldn’t have been obvious. I was just interested in the BER, and Jeff Colley twisted my arm and encouraged me to go for thermal imaging and blower door testing which Gavin O’Sé of Greenbuild expertly did. If I wasn’t putting the build into the magazine, I would have just gone for a BER. The blower door test was key to the final lesson of learning the importance of airtightness.
“Also, even so late in the project, Ecological Building Systems and Sheep Wool Insulation were very helpful in fixing the airtightness.” he says. “And the people on the Construct Ireland forum have been a huge help in giving their knowledge and experience to any questions I asked. When I was looking into various poroton systems, one poster on the forum suggested I stick to the FBT system, due to its simple buildability, which lends itself to airtightness.”
Considering the lack of initial attention to airtightness, the first blower door test result is quite respectable. McSweeney attributes this to the simple wall structure – just poroton block and plaster – that minimises the number of potential joints for air leakage or infiltration. “Having said that the first test result could have been better had we been more prepared for it, as there were some obvious leaks from the attic back into the structure.”
Since the first test, the attic has been insulated and sealed, windows have been adjusted, and wall-floor junctions, door frames and service penetrations have been sealed using tapes and adhesives supplied by Sheep Wool Insulation. The second blower door test yielded an impressive 1.7 air changes per hour at 50 Pascals, though this doesn’t meet the passive house standard of 0.6 air change per hour.
If all goes well, McSweeney may soon be able to boast of having an A-rated house. “The house is coming out with a B1 BER at the minute,” says Greenbuild’s Gavin O’Sé, who performed the blower door and thermography tests, and conducted the BER assessment. However, O’Sé – whose pedigree includes carrying out the blower door tests on the Botanic Homes passive houses in Carlow featured in the previous edition of Construct Ireland – is convinced some simple adjustments can see the house achieve an A3. The downstairs utility room is accessible from the kitchen, but is bordered on the outside by the garage wall. Not considering the utility room or the hot press room above it to be part of his primary living space, McSweeney used a non-perlite filled poroton block with lower thermal performance for these areas.
“He didn’t realise that if a room is accessible from the main house, it has to be included in the BER assessment,” O’Sé adds. “I’ve recommended he massively increase the amount of insulation around the utility room and the hot press room above it, and I think he’s going to do that. He’s going to put insulated plasterboard outside the utility room on the garage side. In the hot press room upstairs there’s about 100ml of fibreglass but he’s going to double or triple that. He’s at about 79 kWh/m2/yr now, but these few changes in insulation combined with the new blower door test result should bring it to an A3 (between 50 and 75 kWh/m2/yr).”
McSweeney stresses that as with all masonry build systems, anyone considering using poroton should ensure that they have the right detailing to prevent the possibility of damp occurring. “However, unlike traditional cavity builds, the problems become immediately evident after rain, and can be swiftly rectified by cleaning up of details and use of bitumen in certain problem areas for external water tightness”. McSweeney also stresses that FBT have Agrément certificates which should cover the building for its lifespan.
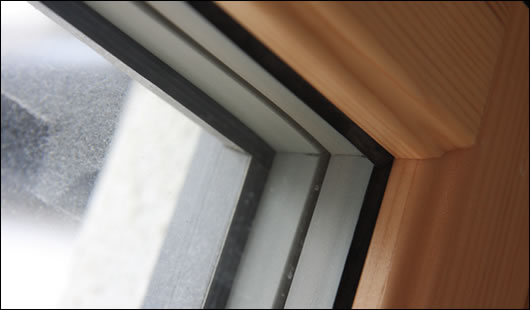
A close look at the cutting edge NorDan NTech triple glazed windows
With the house sitting on an elevated site and visible from a scenic approach route, McSweeney was eager for it to be in keeping with vernacular design. “We wanted to build something that was sympathetic to the vernacular Irish architectural style,” he says. “The Cork Planning Guide was a big help in this regard, in affirming our ideas on what would work well in a rural setting. Two summer holidays around the south east and rubbernecking every rural dwelling on the roads around Wicklow and Kildare helped us decide what we did and didn’t like.”
Of course, design was important from an energy as well an aesthetic perspective. “When you read up on passive architecture you read a lot about ‘deep’ houses”, he says, “where you have your bedrooms in the back of the house, because they don’t need to be as warm as the rest of the house. And then you have your living space in the sun. I just didn’t like the idea - I like the idea that you’re getting light in your bedrooms. The traditional Irish longform house lent itself to what we wanted to do.”
While ‘traditional’ and ‘vernacular’ might be read as ‘boring’ to some, McSweeney’s house is neither. Viewed from the back, the extensive kitchen glazing and sharp corners combined with the angles created by the house’s simple form give it an understated appeal. Viewed from a distance, it nestles easily into the hillside beside farm buildings, and is partially hidden by surrounding trees.
“We wanted a house with plenty of light and solar gain,” McSweeney adds. “This form of building isn’t optimised for a passive house, but it will be bright and we’ll be able to do without lighting for much of the day. I think it’s a good mix of traditional form with optimal solar gain, however in this regard we were fortunate with the orientation of the site.”
“There are only two rooms that don’t have access to the sun for much of the day. There’s the office downstairs, which should be warmed up a little by the equipment there, and will also get the morning light which should help to warm it up. Then there is the bedroom above that, which we may have to heat from the buffer tank with a small, low temperature radiator if winter temperatures in the room are uncomfortable.”
“The last piece of the jigsaw to be put in place is tree planting,” McSweeney says. “The fact that we had an existing dwelling on the site, meant that the trees which were planted afford us great shelter from the north winds. We’ll plant some fruit trees at the top of the garden to protect us from a vicious south-east wind that comes from the Wicklow Gap. We need to divert this wind with further planting so it doesn’t tunnel around the sides of the house and take heat away from the building. One thing that impressed me during the thermal imaging tests by Gavin O’Sé was how the sheltered areas of the external envelope were that bit warmer than the exposed surfaces. If we get the microclimate around the building correct with intelligent planting, we’ll save even more energy.”
With evident sincerity in his desire to build a genuinely low energy home, McSweeney has applied his green thinking extensively. “Everything we buy for the house is low energy and long life,” he says. “If we invest now we will have lower running costs, and given the way energy prices are going this was a wise choice. For example, we just got a larder fridge and chest freezer, and the watts consumed by both together are less than an A rated fridge freezer.” Sustainability was also a factor when it came to flooring. The kitchen floor is marmoleum, a natural substance made from linseed oil, wood flour, resin, limestone and jute, while the flooring upstairs and in the living area is bamboo - a fast growing plant that can be harvested frequently without threatening its natural ecosystem. CFL bulbs also feature prominently throughout the house.
While McSweeney’s new home certainly boasts a spectrum of sustainable features, the cynic might says that its size isn’t conducive to true low energy living. “Is our house a little big? Yes, I think so,” he admits. “However that is also with a view to the long term. The house should be big enough for our family’s needs for the next 30 to 40 years – thus the accessible bathroom beside the office so we can move in there when we become older and one of the children can take over the rest of the house with their family, if it suits. How many houses do you know of where the family extends the house because they have teenagers and need the space, only to discover that they have an empty house five or ten year later?”
McSweeney’s eagerness to embrace sustainable building is obvious - but where did his green inspiration stem from? “The low energy route was always in the back of our minds. When you’re living in a concrete house you realise what it costs to heat it. We were putting in 3,000 litres of oil a year into a tank to heat a 700 square foot house. We knew what bad building was about. If we put up a wardrobe in a corner, we got mould. We had mushrooms growing where the main house met the bathroom. We certainly knew all about what we didn’t want.”
It’s been a long road for McSweeney’s family, who had just moved into the house when Construct Ireland visited: “We started this nine years ago,” he says. “We moved into the cottage that was here, and the intention was always to extend. Then children arrived and that got in the way for a few years. We went to pre planning about three years ago.” It may have been a long journey, but now that his family can boast a bright, comfortable low energy home in such scenic location, nobody would question whether it was worth it.
Selected project details
Client: The McSweeney Family
Main contractor: Darren Beehan
Post construction energy assessment: Greenbuild
Build system: FBT
Windows & doors: NorDan Vinduer
Attic insulation: Sheep Wool Insulation
Solar system: RVR
MVHR: ATC Electrical & Mechanical
Masonry stoves: Frontier Energy
Marmoleum flooring: Forbo Ireland
Bamboo flooring: Bamboo flooring Company
- Articles
- Passive Housing
- Hooray for Hollywood
- Poroton
- mechanical ventilation heat recovery
- Calpak
- solar gain
- passive house
Related items
-
Hevac launches Airmaster decentralised MVHR for schools
-
Big picture - New Zealand rural passive home
-
Podcast: what we've learned from 20 years in green building mags
-
45,000 more Irish homes face radon risk, new maps reveal
-
Passive house 30 years on: qualified success or brilliant failure?
-
Above the curve - Limerick passive house showcases precision timber engineering
-
AirMaster’s flagship MVHR awarded passive house certification
-
Window-opening unreliable for ventilation, study finds
-
International passive house conference kicks off
-
CVC Direct launch MVHR add-on for space heating & cooling
-
NZEB’s effect on new home specs emerges
-
Iso Chemie Winframer gets BBA approval