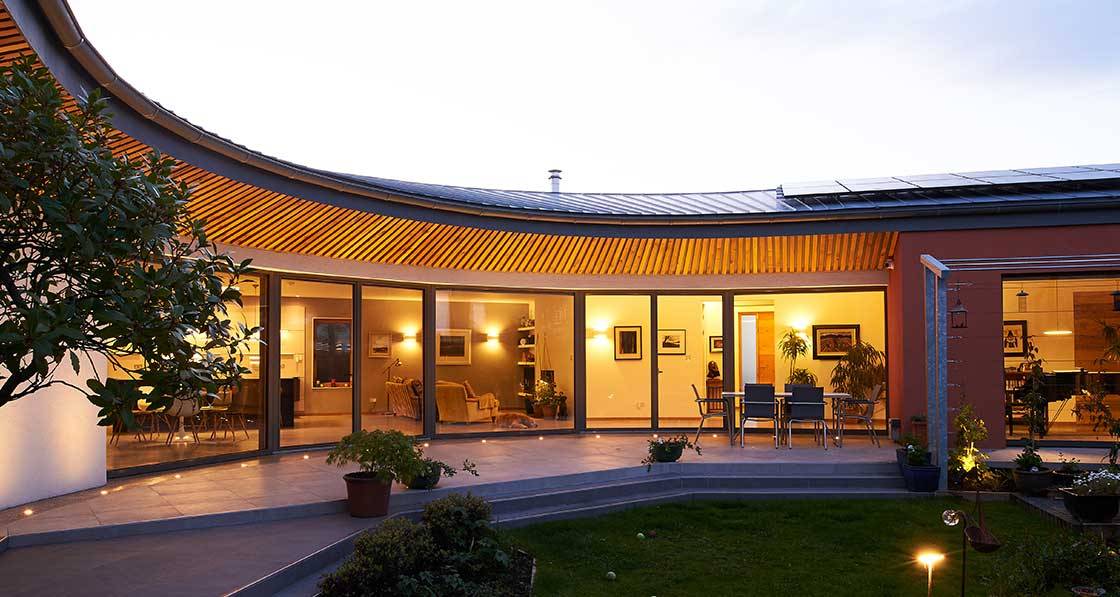
- New build
- Posted
Above the curve - Limerick passive house showcases precision timber engineering
Sometimes it takes the constraints of a challenging site to bring out the best possible design, and that was certainly the case for this Limerick City passive house, where the project team managed to deliver a unique, curving passive house in response to a tricky urban plot.
Click here for project specs and suppliers
€25 PER MONTH FOR SPACE HEATING & COOLING (Estimated, see ‘In detail’ for more)
Building: 223 m2 uncertified passive house
Build method: Timber frame
Location: Limerick, Ireland
Standard: Uncertified passive house
Designing a completely bespoke home on a tiny site in a very mature, built-up urban area is the kind of brief that many architects relish, not least the challenge of creating a distinctive form that functions brilliantly, while ensuring that it blends in aesthetically with neighbouring homes. Throw in the desire to build to the passive house standard, and you have quite the project.
But spend a bit of time taking in the sight of this really interesting, three-bed, single-storey dwelling in Limerick city — particularly the way in which almost the whole house orients towards its curved courtyard — and you can very quickly see why architect Barbara Carr (of local practice Studiomove Architects) and her client, John , are so pleased with it.
The new building has a bigger footprint than the original house that was demolished to make way for it, but it still blends in nicely. “The front of the house has very similar proportions to the bungalows that are there, and we didn’t want to do something that really jumped out,” Barbara says. “But inside it’s completely different. That’s why I called it the Tardis. When you come up, you can see that it’s different, but it really doesn’t shout out and I really loved that aspect of it. And then you come in the front door and there’s that sense of the sweep of the courtyard around the site that surprises you.”
The idea of wrapping the house around three sides of the site was adopted.
The Tardis certainly manages to maximise every one of the 220-odd square metres available to it, and while it butts up closely against neighbouring properties, being single storey means there is no risk of it overlooking adjacent homes.
A driving force behind the project was John and his wife’s previous experience of living in an early 20th century red-brick home. Although they really loved the house, with its period features, it was registered with the local heritage council and they felt that any attempts to insulate it would be severely restricted. Even with a 30 kW condensing boiler and heating zones, the house struggled to keep them warm in winter.
As an engineer, John had the idea of doing a self-build very firmly on his bucket list. He was in the fortunate position to be able to take some time off work to serve as the project manager and main contractor. When the opportunity arose to buy a house that came up for sale in the area, the couple decided to take the plunge, knocking down the original 1950s bungalow to create a clean slate for a new build.
“Initially all I knew was I wanted to build a warm house. That was the starting point. So, I researched what could be done, what’s out there and it kind of led me on to the whole concept of the passive house standard,“ says John.
The curved courtyard-facing rear façade comes together
“What I really liked about it, and this is from an engineering point of view... is that you could design and model the house up front and see how it would perform rather than coming up with a notional design and then hope it would work out.”
He undertook the passive house designer training course run by MosArt Architects in Wicklow (which Barbara also did), and also decided to do a lot of the work himself, particularly the mechanical and electrical, which allowed him to indulge in his enthusiasm for the latest in smart home automation technology from Loxone.
While it’s clear from the performance figures that the Tardis works as a passive house, it was agreed early on that the design wouldn’t be a slave to the standard. “We didn’t want to wind up with a box, basically, with the windows on the south,” says John. So, while a warm, comfortable home was the main aim, achieving the standard – with or without certification — was a nice-to-have rather than a must-have.
What made things tricky was the orientation. The original house faced south but straight onto a high, six metre high brick wall with an apartment block behind it. “We looked at it and thought ‘Oh, crikey’, Barbara says. “I mean, it’s a brilliant site in terms of its proximity to town and privacy, but the orientation then was really compromised by these things.”
The idea of wrapping the house around three sides of the site was adopted so that the house orients towards the courtyard garden rather than the back wall. So, while it’s not far off the L-shape form that John had suggested, “it embraces the garden rather than addressing the wall,” says Barbara. “We calculated that we’d get enough south light into the courtyard of the house in summertime, but had to play around with window sizes as the curved courtyard crept around to face north. We also reduced the high-level north and east-facing windows in size.”
Barbara says that because the form factor was not ideal for passive house — being single storey and spread out, there is a large surface area from which heat can escape — insulation and the orientation of windows was critical.
A number of different build systems were investigated, including structural insulated panels, insulated concrete formwork (ICF) and blockwork, but it was decided that a twinwalled timber frame would give the best detailing and, more importantly, would lend itself to the non-rectilinear shape of the house.
Indeed, there’s no doubting that the geometry added a layer of complexity to the build, particularly with regards to the roof. Although it’s a mono-pitch, there’s a lot going on with it.
It sweeps around in a curve, getting wider to accommodate high level windows above the kitchen and bathroom. All this, along with the curved courtyard window setting, generated a fair bit of “swearing” among the build team in its bid to make it all come together.
Given the prominence and importance of the view facing out into the courtyard, the choice of external doors and windows was an important one. John and Barbara chose an Austrian company called Josko and even visited the factory, where they fell in love with their internal Venetian doors, made of bog oak. “These add a real wow factor to the interior,” Barbara says. “They are extra high, flush-fitting, in great finishes and with a magnetic latch system. There was quite a bit of work getting them to fit correctly.”
It wasn’t in the plan, but they also opted to line the underside of zinc roof overhang in the courtyard with timber battens. It was felt that the view from inside out into the courtyard would look quite flat and dark with just the zinc roof overhang, and undermine the look of the beautiful timber windows. So, a joiner and his experienced father were commissioned to add matching battens, which they set using the radius of the curve of the building.
“It took time to get them looking right,” Barbara says. “But now it’s really beautiful. It’s warm and you can see it from inside. So, you’re looking at your timber windows from inside, and then you look up and you see these battens as well. It’s one of those things that wasn’t decided before. I think we all love it.”
On the foundation side of things, John liked the idea of an insulated raft foundation but the need to build up tight against the back wall effectively ruled that out, not to mention the – admittedly quite small – risk that an oil spill from the next door neighbour’s oil tank would damage the EPS of the insulated foundation. A standard raft foundation was installed instead.
This article was originally published in issue 38 of Passive House Plus magazine. Want immediate access to all back issues and exclusive extra content? Click here to subscribe for as little as €10, or click here to receive the next issue free of charge
The use of timber frame, supplied by Galway firm Long Life Structures, adds bonus points for a low carbon material, as does the cellulose insulation in the walls and roof.
“The roof was what attracted me to the project really,” says Emmet Nee of Long Life Structures. “I always love doing curved work, curved carpentry. We’ve gained a bit of a reputation for doing challenging houses like this.
“We see ourselves more as thermal envelope specialists rather than just timber frame suppliers. The good thing with timber frame is that the design stage of the drawings will show up any areas that require deep thinking, and that’s where you work it out. For this house we had to work out each individual roof rafter instead of doing one and repeating it 60 times.”
The twin wall system used on this project, with two cellulose-filled studs separated by another layer of cellulose, is the company’s standard build method for passive house projects, as it eliminates thermal bridging through the walls. The company also boasts an enviable record of achieving better than 0.6 air changes per hour on every house it has built to date.
“Airtightness doesn’t happen by accident, it has to be designed in,” Emmet says. “When we go to site we have our airtightness strategy honed in. The real challenge is when you’re erecting the frame — those are there areas you won’t be able to get to again. This is the reason we erect our own frames rather than sub-contract it out.”
John and his partner moved in a year ago, so they’ve experienced both a summer and a winter. “On the face of it, people think of passive houses as cheap to run and that’s it, but it’s actually a very, very comfortable house in terms of the constant temperature, with no drafts, and it’s a single zone temperature-wise throughout.”
Since they had their smart meter installed by ESB networks, John has been tinkering around with the Nilan air-to-water heating and ventilation system to see how it works best in combination with the 3.5 kW solar PV panel array and a 4.8 kW battery. “Traditionally you might have your day and night meter, but now you’ll have maybe three or four different rates over the course of 24 hours and so we’re looking at how we can maximise that capability with a PV,” he says.
The geometry added a layer of complexity to the build.
As an engineer used to project-managing more complex industrial projects, John very much enjoyed managing this build on a personal level. “One of the things that I found with building this house is that there was emotion involved. If you’re doing an industrial project, you have a specification, you’re not worried about colours or worried about would the client be happy with this or that and so on.”
“When people look at these Grand Design programmes and so on, they have no idea what’s going to happen in the background in terms of the complexity involved in it. The best thing I ever did was to do the passive designer course, to bring myself up to speed, you know, from selecting windows, to detailing, to minimising thermal bridges and so on. I’ve learned so much from it, it’s absolutely unreal.”
No doubt he enjoyed installing the state-ofthe- art smart home system that controls everything from lighting to blinds to heating. “He had great fun with that,” Barbara says. Personal joys aside, John is also clear on what the project has achieved and is actively considering applying for passive house certification.
“We pushed the envelope in terms of getting as close as you can to the passive standard without sacrificing aesthetics in an urban, built-up area.
1 & 2 Installation of the curved courtyard windows, triple glazed aluclad units from Josko; 3 timber cladding was fitted to the underside of the zinc roof overhang in the courtyard for aesthetic reasons; 4 Intello vapour control membrane and airtightness taping to ceiling; 5 the Nilan Compact P combines heat recovery ventilation along with air heating and cooling; 6 solar battery and Solis Hybrid inverter.
Selected project details
Architect: Studiomove Architects
Civil & structural engineering: Mike Boyce Consulting
M&E design: GEON
Timber frame & raft foundation: Long Life Structures
Quantity surveyor: Steadfast
Mechanical contractor: Paul Corcoran Plumbing & Heating
Electrical contractor: Deegan Contracts Limited
Airtightness test: Hession Energy
Cellulose insulation: Darmstadt, via Clíoma House
Wufi analysis: Ecological Building Systems
Airtightness products: Clíoma House
Windows & doors: Josko, via DG Windows & Doors
Space heating & ventilation: Nilan Ireland
Roof windows: Fakro
Blinds: Shade Tec
Cladding: Aquapanel, via Greenspan
Roofing: A & A Quinn Roofing
Polished concrete floor: Mapei, via Topcoat Systems
Landscape design: Manila Landscape Design
Home automation (Luxone): GEON
Lighting design: Wink
Embodied carbon
With a cradle to grave score of 483 kg CO2e/m2 GIA, this project beat the RIBA 2030 Climate Challenge target of 625 kg CO2e/m2 GIA, according to calculations by John Butler Sustainable Building Consultancy using PHribbon. While the revised RIBA methodology is aligned with LETI’s embodied carbon targets, it differs in a crucial regard: LETI excludes embodied carbon emissions from PV arrays, considering them as part of the electricity grid, effectively. Excluding the large PV array in this case would cause the figures to drop by a further 37 kg CO2/m2.
The calculations included a number of assumptions where necessary, in particular in the area of mechanical, electrical and plumbing services, where environmental product declarations (EPDs) remain rare.
Data from a French Product Environmental Passport for the heat pump which most closely resembled the compact unit installed was used, and data for stainless steel ductwork was used in the absence of polypropylene ductwork data. The analysis included interior and exterior finishes, sanitaryware and sinks, but not all fitted furniture, fixings and equipment. Default or comparable data was used in a number of other areas. Transport emissions were adjusted to provide rough approximations for given product types. No replacements were assumed for the fabric, and two replacements of the heat pump were assumed – albeit with inert refrigerants assumed – within the 60 year projected lifespan in the calculations.
A comparison between the as built external wall system and a notional cavity wall build up to the same specifications – with transport and construction emissions adjusted accordingly for those elements specifically – showed cradle to practical completion figures of 58 kg CO2e/m2 for the as built walls (including 30 kg CO2e/m2 for materials) versus 114 kg CO2e/m2 for the cavity wall comparison (including 93 kg CO2e/m2 for materials).
The complete building as built was compared to the same complete building built with cavity wall construction and with no GGBS substitution in the foundations. The cradle-to-grave figures increased from 483 to 563 kg CO2e/m2, while the as-built spec also included 150 kg CO2e of sequestered CO2 in the timber and timber-based products, whereas the alternative with cavity walls was estimated to include 83 kg of sequestered CO2e (both versions assumed the same timber and timber-based products used for internal walls and roof build up).
As ever, it is worth remembering that the module C emissions relate to the end of life at the building. The majority of the module C emissions relate to sequestered CO2 in the timber and timber-based products, and it is assumed that these emissions are released at the building’s end of life – with 75 per cent of timber assumed to be incinerated, and 25 per cent landfilled. Even if the timber was instead assumed to be recycled or reused, the sequestered emissions would move outside of the boundary conditions of the building life cycle assessment, and pass on to the next use. While this may give the appearance that a significant amount of CO2 is released into the atmosphere at the building’s end of life, it is possible that timber may remain sequestered in buildings for hundreds of years.
In detail
Building type: Detached 223 m2 timber frame house.
Location: Limerick City
Completion date: February 2020
Budget: Not disclosed
Passive house certification: Uncertified
Space heating demand: 18.44 kWh/m2/yr (PHPP)
Heat load: 9.73 W/m2 (PHPP)
Primary energy non-renewable: 65 kWh/m2/yr
Overheating: 10% (PHPP)
Number of occupants: 3
Energy performance coefficient (EPC): Pending
Carbon performance coefficient (CPC): Pending
BER: Not yet completed
Environmental assessment method: N/A
Measured energy consumption & energy bills: During 2020, the household electricity bill averaged €80 per month, for all space heating, hot water & electricity. However, John installed a solar PV array in September 2020, and a smart meter with varied electricity rates in April 2021. This already appears to be making a big difference in electricity consumption. For example, while the house consumed 1,645 kWh in May 2020, its projected energy consumption for May 2021 was just 370 kWh (as of May 25). For space heating & cooling only, taking the current Energia day rate (0.1565c), this property would have an estimated bill for space heating and cooling of €300 annually or €25 per month inclusive of VAT, but excluding standing charge and PSO levy. These figures are based on final energy demand (delivered energy) figures from the PER sheet of PHPP.
Airtightness: 0.5 ACH at 50 Pascals
Thermal bridging: Walls, pitched and flat roofs all in timber frame with cellulose insulation meant that the line of insulation was continuous from one plane to another. A twin wall timber frame system, 330 mm thick overall, helped to reduce thermal bridging. Psi values were taken as default 0.08 W/ mK, apart from the curved courtyard wall. The detail around a steel beam above the large window/door wall to the courtyard had a calculated psi value of 0.04 W/mK. Foundation/wall psi value was 0.01 W/mK. Ground floor: 150 mm thick reinforced concrete slab (grade C30/37) followed above by 280 mm Mannok Therm Floor PIR insulation, with ducting pipework for Nilan ventilation cut in, 75 mm screed containing pipework for underfloor heating. 12 mm grey Mapei Ultratop Terrazzo & Irish beech pebble polished concrete finish. U-value: 0.078 W/m2K
Walls: 20 mm Aquapanel exterior cement board, followed inside by 50 x 50 mm timber battens to create ventilated cavity, 22 mm timber sheeting and pro clima Solitex Humida Fronta Quattro wind-tight membrane, 89 x 38 mm outer leaf non-loadbearing stud at 600 c/c filled with Darmstadt Thermofloc cellulose insulation (0.037 W/mK), 100 mm layer of cellulose between inner and outer timber frame, 140 x 38 mm inner load bearing stud at 600 c/c filled with cellulose insulation, 12 mm Durelis Naturespan Vaporblock racking airtightness layer, 50 x 50 mm battens at 400 mm c/c to form service cavity, 12.5 mm Gypsum plasterboard and skim. U-value: 0.120 W/m2K
Roof: Zinc cladding with standing seams, followed inside by Alutrix vapour barrier, 18 mm penny gap boarding, 50 x 50 mm timber battens, 18 mm OSB sheeting, 300 mm deep timber I-beam rafter (at various centres due to radius of roof) filled with Darmstadt Thermofloc cellulose insulation, Intello Plus vapour control membrane, 50 x 50 mm battens at 400 mm c/c to form service cavity, 12.5 mm Gypsum plasterboard and skim. U-value: 0.116 W/m2K
Roof, flat: Fatra PVC membrane, followed beneath by 120 mm TR 26 PIR insulation board, vapour barrier, 18 mm plywood sheeting, timber firring pieces falling from 92 to 50 mm (1 in 80 fall), joists 170 x 44 mm with full fill cellulose insulation, Intello Plus vapour control membrane, 100 x 38 mm battens at 400 mm c/c to form service cavity, 15 mm gypsum plasterboard and skim. U-value: 0.105 W/m2K
Windows: Josko Platin Plus triple glazed aluclad timber windows. U-value: 0.82 W/m2K average for the project.
Roof windows: 2 x Fakro U8 triple glazed roof windows. U-value: 0.8 W/m2K
Heating system & Ventilation: Nilan Compact P XL (430 m3/hr) unit which combines heat recovery ventilation along with air heating and summer air cooling through the balanced ventilation ductwork. Passive House Institute certified. Effective heat recovery efficiency: 80% (PHi), calculated with PHPP, considering stated efficiency and installation. The Compact P is backed up with a Nilan air-to-water heat pump (Air9) which provides weather compensated hot water to zoned underfloor heating circuits. Seasonal coefficient of performance for Compact P and Air9 (variable speed compressor output power) Ecodesign A+++ SCOP 511% efficiency.
Water: N/A
Electricity: 19 m2 Trina Mono solar photovoltaic array with 3.48 kWh installed capacity. Battery storage 4.8 kWh. Solis Hybrid inverter.
Green materials: Cellulose insulation, timber frame.
Image gallery
-
Plan-ground-floor-5 Plan-ground-floor-5
-
Plan-high-level-windows-10 Plan-high-level-windows-10
-
Plan-roof-31 Plan-roof-31
-
Elevations-front-and-RHS Elevations-front-and-RHS
-
Elevations-LHS Elevations-LHS
-
Sections-parapet-details Sections-parapet-details
-
Detail-pitched-roof-make-u Detail-pitched-roof-make-u
-
Detail-fascia-to-courtyard-8 Detail-fascia-to-courtyard-8
https://mail.passive.ie/magazine/new-build/above-the-curve-limerick-passive-house-showcases-precision-timber-engineering#sigProId3f6404a1c6