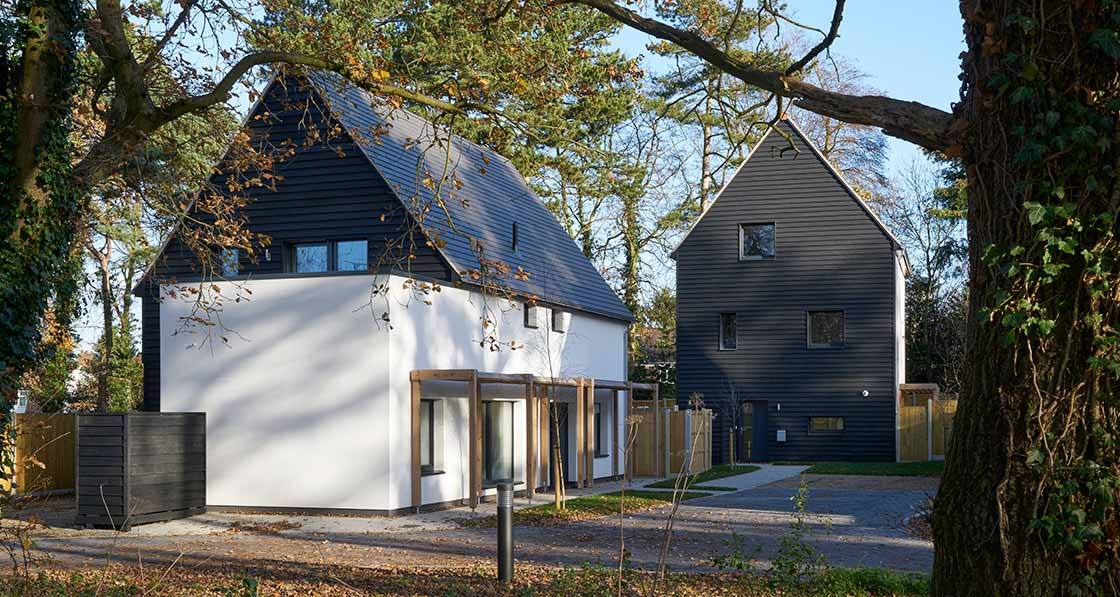

- New build
- Posted
Affordable homes scheme reflects rise of Norwich as a passive hub
A new development of passive housing on the outskirts of Norwich shows how to combine energy efficiency, ecology and affordability on one exemplary site — and why the city continues to be an unlikely leader in pushing passive house construction in the UK.
Click here for project specs and suppliers
Building type: 8 detached & 6 semi-d passive houses, from 72 to 133 sqm
Location: Hellesdon, Norwich
Build method: Externally insulated poroton block
Standard: Passive house certified
EPC: B
Heating: Gas boilers
Heating bills: £27 - £55 per year
When architects Hamson Barron Smith won top prize at the Norfolk Constructing Excellence Awards in April for their £2.8m Carrowbreck Meadow passive house scheme, it was confirmation that Norwich has become the heartland of passive house development in the UK.
Norfolk’s capital city will see around 300 passive house units built over the next few years. Hamson Barron Smith is designing more than 120 of these homes and Mikhail Riches Architects are delivering a further 100 homes from their office in London.
Local authorities in Norwich have played a crucial role in pushing the local development of passive housing. Six of the 14 Carrowbreck units, for example, will be affordable homes built for Broadland District Council.
In 2015, Norwich City Council introduced the ‘Fabric First’ framework, a collaboration between contractors with expertise in passive house construction, to assist the development of passive house projects.
This article was originally published in issue 21 of Passive House Plus magazine. Want immediate access to all back issues and exclusive extra content? Click here to subscribe for as little as €10, or click here to receive the next issue free of charge
The framework is open to all local authorities and housing associations. At this year’s Norfolk Constructing Excellence Awards, the Fabric First Institute — which runs training courses in passive house design and construction — was the overall runner-up to Carrowbreck.
Now, Norwich City Council’s ambition is to see 1,000 passive houses built locally in the next 10 years.
Sarah Lewis, project architect with Hamson Barron Smith at Carrowbreck, says: “These are exciting times for passive houses in Norwich, which is leading the way in the delivery of fabric first projects. The local authorities in Norwich are pushing the standard partly because it addresses issues of fuel poverty and environmental regulations. The message is getting out that councils can think on a grand scale. A lot of councils around the UK are looking at passive house as a benchmark because it provides more quality than the marketplace.”
Lewis is an influential figure in the world of passive house development and a valuable asset for the city of Norwich, where she moved from London in 2014.
Lewis qualified as a passive house designer after completing London’s first passive house in 2010, in Camden, for bere:architects.
She also created the PHPP modules for the east of England’s first passive house designer course and has spoken three times at the International Passive House Conference.
Carrowbreck is set in woodland and designed in the traditional Norfolk style, defined by references to the historic barn vernacular.
All of the homes have electric car charging points, rainwater butts and connection points for solar PV.
The positioning and orientation of the homes is designed to maximise access to solar gain in winter and prevent over-heating in summer, according to the architects, with brise soleil and venetian blinds providing solar shading.
Carrowbreck was also one of the first UK projects to use 300mm Porotherm poroton blocks, which require 95% less water than traditional blockwork to manufacture.
The blocks have achieved an A+ BRE Green Guide rating, with 30% of materials from alternative, recycled, or secondary sources.
At Carrowbreck, the blocks were insulated externally with Baumit OpenTherm EPS, which is new to the UK market (see architect’s comment for more details).
The timber roof elements are from Metsa Wood, who use “100% traceable wood from sustainable northern forests”.
Other low carbon materials were incorporated wherever possible, such as Warmcel cellulose insulation, which is made from recycled newspapers. Most materials came from local suppliers too.
Hamson Barron Smith is now conducting a full post-occupancy evaluation of the project as part of the ‘soft landings’ process with residents, including interviews with occupants, analysis of energy bills from all homes, and data collection from an advanced monitoring system in one home that gathers info on gas and electricity consumption as well as indoor temperatures, relative humidity and carbon dioxide levels.
Local contractors and sub-contractors were also crucial to the project. The main contractor was RG Carter, which has two bases in eastern England. Although RG Carter had never worked on a passive house project before, all of the homes here passed the stringent passive house air pressure test requirements of 0.6 air changes per hour at 50 Pascals on their first attempt.
Before beginning the project, RG Carter put its tradespeople and sub-contractors through the Fabric First framework training programmes.
Jackie Richards, director of Whole House Energy, which is responsible for the Fabric First training, says passive house training schemes for tradespeople normally take three days to complete and cost upwards of £1,000 per person. But here, the information has been condensed into a one-day course to supply the essentials.
“It’s a long day from 8am to 6pm which is enough to teach the fundamentals about airtightness, insulation, thermal bridging and ventilation,” Richards says. “It’s a practical course as there’s not enough time to go into a lot of theory and do a lot of maths and calculations. So we don’t outline the details about ventilation, for example, but just teach them how to install it. But they find it’s enough information for them to get the job done and very few know anything about passive house before they start.”
For senior tradespeople who want to take their knowledge to the next level, there is a certified tradesperson training which lasts three days.
The passive house designer course, meanwhile, is even more detailed, offering nine days of instruction. “All the courses are about more than passive house,” Richards says. “It’s really a case of educating tradespeople about how to construct quality buildings. They learn how to eradicate the energy performance scam, which is what we are up against. On average we use 16% more energy in our buildings than they’ve been designed for. Sometimes it can be 10 times more.”
Richards agrees that Norwich has become one of the boldest and most forward-thinking regions for sustainable development in the UK.
She believes the original inspirational for the change in approach came from the construction of the Enterprise Centre, at the University of East Anglia.
(from top) this sequence shows the construction of the ground floor and external walls, with the installation of the 300mm Dow Floormate EPS insulated foundation system, with 200mm of reinforced concrete above this, and the rising 300m Porotherm clay block walls forming the external walls for the properties.
Designed to showcase passive house development, it opened in June 2015, and is now recognised as one of the UK’s greenest buildings. Professor John French, CEO of the Adapt Low Carbon Group, which commissioned the building and shepherded its construction, told the Guardian newspaper: “We wanted to create the ultimate sustainable building.”
The team working on the passive certified Enterprise Centre sourced 70% of the building’s wood from Suffolk’s Thetford Forest.
The building is wrapped in prefabricated, vertically hung thatch panel cassettes. Although vertical thatching has been used in places like Holland, prefabricating the thatch panels off site had never been done before. The panels were built in local thatchers’ barns across Norfolk, and each timber cassette module was filled with tightly bound, locallysourced straw.
Since it opened, specially designed software has continually monitored the building’s carbon footprint. “The Enterprise Centre has created a lot of interest in passive houses in Norwich and the team that worked on it has moved on and disseminated their ideas,” says Richards.
Despite the inspirational presence of the Enterprise Centre in Norwich, it still takes an enlightened approach from a local council to build houses to passive house levels in an era of drastic budget cuts.
At Broadland District Council, chief executive Phil Kirby says the authority was determined to lead by example.
“We did compare the cost of meeting passive house standards at Carrowbreck with more traditional methods and, of course, it was more expensive. But one of our key ambitions is environmental excellence and we took the view that we wanted to pilot the production method, rather than simply maximising profit. It was also an element in attracting purchasers.”
Broadland District Council went into partnership with NPS Group, the parent company of Hamson Barron Smith, to create a joint venture company, Broadland Growth Limited, which focuses on small, high-quality developments with excellent energy efficiency. For Carrowbreck, Broadland District Council provided the land and part-funded the development, but the council has been paid back with a profit. “Broadland is a big growth area and we have shown how it’s possible to build an energy-efficient development and make a profit,” Kirby says.
There are two much larger passive house developments in the pipeline now.
(above, clockwise from top left) Airtightness detailing in preparation for floor joists; and at the wall-roof junction, ready for internal lime parge coat to complete the line of airtightness; penetrations through the airtight layer kept to a minimum and where necessary carefully sealed; the Baumit OpenTherm EPS external insulation being applied to the Porotherm walls; the OpenTherm EPS installed with fixings and trim; external render applied to the EPS.
The Regeneration Company, which was established by Norwich City Council to deliver new homes, is behind a 172-unit development at Three Score, in Bowthorpe, Norwich.
Some 112 of the properties will be built to the passive house standard and one third of the homes will be affordable housing. RG Carter is again the contractor, having acquired a good understanding of passive house construction on Carrowbreck. A further 105 passive houses are planned at Goldsmith Street, off Dereham Road. “There’s been a sea change of attitudes in Norwich,” says Jackie Richards. “With all the upskilling of local tradespeople, there’s an opportunity for the region to do it again and again now.”
Architect’s comment
The sustainability ambitions at Carrowbreck permeate the project at every level, from the overprovision of affordable homes to the new woodland path and animal haven, through to the choice of natural and low carbon materials across the site.
A fully sustainable drainage strategy has been delivered and all homes have electric car charging points, rainwater butts, connection points for PV, and are compliant with the recommendations of the National Housing Standards Review.
Sustainable transport choices have been supported through the new path to the closest bus stop and the shared surface access road through the development.
Carrowbreck was one of the first UK projects to use 300mm precision-engineered Porotherm blocks, a fast, virtually dry construction. With its rapid daily output, this brought cost and timesaving benefits, while its thermal and acoustic efficiencies will bring further advantages for decades to come with a design life of over 150 years.
The blocks were combined with a brand new external wall insulation to the UK market, Baumit OpenTherm, the only EPS insulation system to be truly permeable, allowing the walls to breath. Paired with lime plasters and MVHR it ensures perfect indoor humidity. The external render, also vapour open, is microscopically smooth, creating a self-cleaning surface –important on this wooded site.
Although no longer a regulatory requirement, the RG Carter project management team produced a site waste management plan for the project to reduce, reuse and recycle wherever possible.
Meanwhile 11 local apprentices were employed in a range of trades to further their education and in particular the skills required to build passive house dwellings.
Carrowbreck Meadow demonstrates that in a period where affordable housing requirements are being challenged due to the introduction of the community infrastructure levy and viability issues, the council can deliver its own high quality housing developments which exceed affordable housing requirements and deliver sustainable buildings while still delivering profit.
(above, left to right) a layer of Foamglas Perinsul blocks in the Porotherm clay-block walls, acting as a thermal break where the balcony will meet the external walls; low thermal conductivity fixings for the external insulation; external insulation lapping over the window frames to minimise thermal bridging psi values (all windows and doors open inward).
Selected project details
Client: Broadland Growth Limited
Architect: Hamson Barron Smith
Contractor: RG Carter
Poroton blocks: Porotherm
Airtightness products: Pro Clima / Ecological Building Systems
External wall insulation: Baumit
Additional wall insulation: Kingspan Insulation UK
Cellulose insulation: Warmcel / Payne Insulation
Additional roof insulation: Rockwool
MVHR designer: Greenwood
MVHR systems: Edmunson Electrical
Windows & doors: Ecohaus Internorm
Slab insulation: Dow
Thermal breaks: Foamglas
Roof structural components: Metsa Wood
External blinds: Hallmark
Monitoring system: Tensor
Wall ties: Ancon
MVHR duct insulation: Armaflex
In detail
Building type: 8 detached and 6 semi-detached homes. Sizes range from 72 sqm to 133 sqm.
Location: Hellesdon, Norwich
Completion date: October 2016
Budget: £2.8m including all construction and landscaping
Passive house certification: Certified
Space heating demand (PHPP): 13.86 kWh/m2/yr (avg over 14 homes)
Heat load (PHPP): 10.36 W/m2 (avg over 14 homes)
Primary energy demand (PHPP): 110 kWh/m2/yr (avg over 14 homes)
Environmental assessment method: Code for Sustainable Homes – level 4 for water
Airtightness (at 50 Pascals): 0.45ACH (avg of pressurisation and depressurisation over the 14 homes)
Energy performance certificate (EPC): Exact figure varies by plot but all have an EPC of B.
Heating bills: Estimated at £27-55 per year, subject to house type and size, based on PHPP calculated space heating demand ranging from 832-1663 kWh/yr, and gas price of 3.68p from the Gas Collective Fix December 2016 tariff (British Gas).
Thermal bridging: Foamglas Perinsul blocks used, one course at terrace to separate parapet walls up to first floor, and under all of the ground floor door thresholds
Form factor: Averages 3.7 across the site, but varies from 3.1 to 4.3. Although larger than the market would typically provide in Britrain, the homes are relatively small compared to German homes, meaning they have a higher surface area to volume ratio than would be ideal from a PHPP perspective.
Overheating: 0-1% above 25C, based on Peter Warm’s overheating stress testing.
Ground floor: 150mm compacted base followed above by 25mm sand blinding, 1mm DPM, 300mm Dow Floormate 500-A EPS insulated foundation system, separating layer, 200mm reinforced concrete (450mm wide x 935mm deep ring beam at perimeter), power-floated finish. U-value: 0.113 W/m2K
Rendered walls: 220mm Baumit EWI OpenTherm Contact EPS system fixed to 300mm Wienerberger clay Porotherm block single leaf system (supplied via Ridgeon’s) using Ejot fixings (Ejotherm STR U2G). Porotherm blocks laid on a mortar bed. Taped on inside with pro clima tapes to floor slab and to all junctions, roof to wall plate etc. Wet plastered internally with 20mm Baumit KP36W spray applied airtight layer, top coat of Baumit Fino Bello finishing plaster coat, sanded to finish. U-value: 0.104 W/m2K
Timber clad walls: 32 x 175 sawn feather edge Siberian Larch cladding with Celcure ACT brown treatment to UC3 and one coat of black priming from Ridgeon’s. Timber clad elevations feature 140mm Kingspan Kooltherm (2 layers of 70mm insulation adhered on, battened on to the Porotherm blocks. Fischer SXRL 10 x 260mm long fixing the battens to the Porotherm blocks). U-value: 0.110 W/m2K
Roof: Metsawood thin joist system. 400mm I joist roof rafters, pumped full with Warmcel insulation. On the underside, 18mm 0SB3 as airtight layer. Service void with 25mm battens and Rockwool RWA45 insulation. Top layer of the rafter was 15mm OSB (not as airtight later). Wall plates were a Metsawood Kerto 75mm bonded timber bedded on top of Porotherm blocks. Gyproc plasterboard finishes to ceilings. Breathable roofing felt, 38mm counter batten vertically, 25mm tile batten. Forticrete Gemini tiles externally. U-value: 0.091 W/m2K
Windows & doors: Internorm KF410 passive house certified uPVC/alu units by Ecohaus Internorm. Window glazing Ug Value: 0.51-0.54, g-Value – 59-62%. Window frame Uf Value – 0.85 W/m2K. Window spacer Psi – 0.031. Internorm front doors U-value 0.58 W/ m2K. Window installation Psi range from 0.011 to 0.109 depending on whether there are external blinds and by facade cladding.
Heating system: Vaillant Ecotec 412 system gas boiler with Santon Premier Plus PP210B cylinder in larger houses and Vaillant Ecotec Plus 32 kW combi boilers in smaller houses. Stelrad radiators in landing, kitchen/dining rooms, lounges, and heated towel rails in bathrooms.
Ventilation: Paul Novus 300 MVHR in larger houses, Zehnder ComfoAir 200 Luxe in smaller houses. With Comfotube distribution systems. Both units Passive House Insittute certified.
Water: Restricted waterflow showerheads. Water butts in gardens.
Brise soleil: Bespoke timber brise soleil designed by the architects. 150mm x 50mm C24 graded redwood spruce with chain of custody certification, with clear Protim 3A treatment and Sikens sealant stain.
Image gallery
-
Elevations drawings 1 Elevations drawings 1
-
Full technical dimension front door detail Full technical dimension front door detail
-
Full technical dimensional roof detail Full technical dimensional roof detail
-
Location drawing 1 Location drawing 1
-
Site plan Site plan
https://mail.passive.ie/magazine/new-build/affordable-homes-scheme-reflects-rise-of-norwich-as-a-passive-hub#sigProId3c9b996e5e