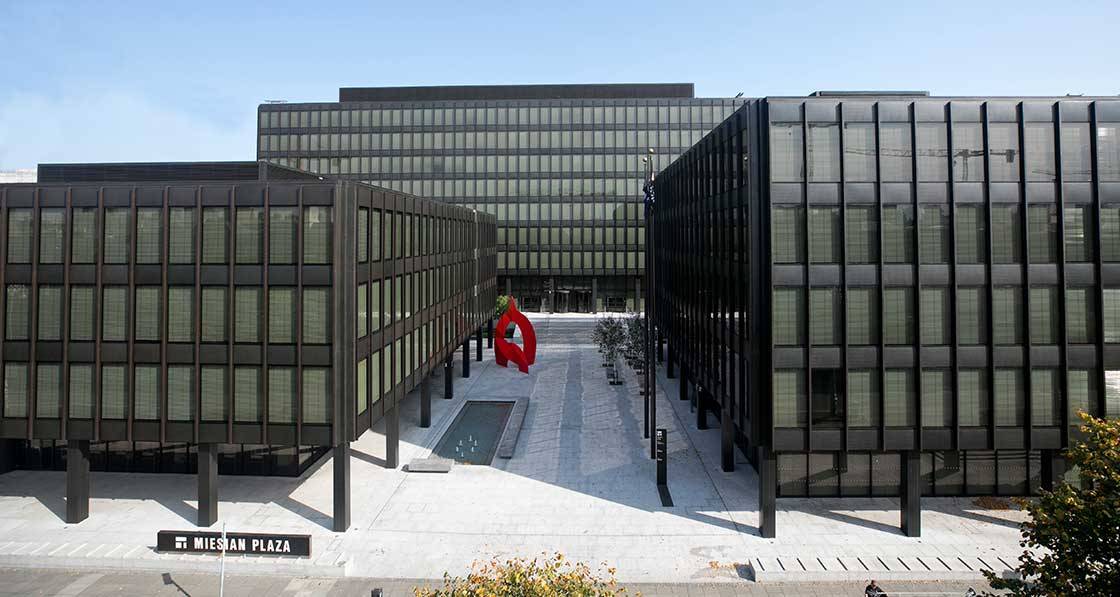
- New build
- Posted
Mies en Scéne - Iconic Dublin offices get deep green treatment
The deep and comprehensive refurbishment of the Miesian Plaza complex on Dublin’s Baggot Street provides a radical blueprint for how to transform mid-20th century city office buildings into comfortable, healthy and super low energy spaces that support sustainable transport and working patterns.
Building: Deep retrofit of 21,800 m2 office building
Completed: December 2016
Location: Baggot Street, Dublin
Budget: €100m
Standard: LEED Platinum V4
When New York City published a list of the energy performance scores of the city’s buildings in 2012, one essential piece of the city’s architectural heritage was shown in a particularly poor light: Ludwig Mies van der Rohe’s modernist classic Seagram building on Park Avenue scored just 3 out of 100. So, what on earth is a Seagram-inspired 1960s office building doing in the pages of a magazine on ultra-low energy buildings? What separates Dublin’s Miesian Plaza from its forebear in this regard, is a hugely impressive effort to renovate and upgrade the office complex from the bottom to the top of the scale.
The developers have taken what would be described in industry parlance as a very ‘hard to treat’ commercial building and overseen its complete transformation into what is now one arguably of the greenest office spaces in the world.
What made the project even trickier from this perspective was the complex’s status as a protected structure. Nonetheless, it’s the first and only development in Ireland to date to be awarded LEED (Leadership in Energy and Environmental Design) Platinum status – LEED’s highest possible rating for environmental performance and sustainability. It joins an exclusive club of 180 other buildings worldwide that have achieved the same certification.
But it is also ground-breaking because it demonstrates the degree to which developers of commercial buildings are responding to increasingly strident client demands for vastly better energy performance, sustainability and comfort.
Miesian Plaza is a complex of three office buildings first designed and built in the 1960s and 1970s as the headquarters for the Bank of Ireland. It’s well known for being one of the first modernist office buildings in the country, with its iconic fronted glazed facade and bronze cladding. It was also one of the first US-style ‘central core’ style buildings to be developed here, sitting on podiums above an underground car park.
In 2006, at the height of Ireland’s property boom, Bank of Ireland sold the centre for €212m to a consortium of investors led by Derek Quinlan and Paddy Shovlin, but their plans for the centre were disrupted by a combination of Dublin City Council’s decision to designate it as a protected structure and the property crash (according to the Irish Times). Receivers took control and sold it to businessman Larry Goodman in 2012 for just over €40 million.
This article was originally published in issue 32 of Passive House Plus magazine. Want immediate access to all back issues and exclusive extra content? Click here to subscribe for as little as €10, or click here to receive the next issue free of charge
Goodman’s Remley Developments then assembled an international design team led by Miesian Plaza’s original architects, Scott Tallon Walker, to devise a €100 million plan to bring the 1960s and 1970s offices up to the highest standards, which included an extension to the rear of the largest block to create an overall floor space of almost 220,000 ft2 of lettable space.
Block one is now out on long-term lease to three government departments —Finance, Health, and Children & Youth Affairs — while blocks two and three are occupied by Asian pharmaceutical giant Takeda.
Passive House Plus was given an exclusive tour of the facility by David Torpey, development director of Remley Developments.
Standing in the slightly revised public space outside the buildings alongside the distinctive sculptures and water features, it’s clear that things are different, but the plaza’s essential character, particularly the bronze facade and curtain wall cladding, is still very much evident.
You might say it was fitting that Scott Tallon Walker were very happy to step in again on this project, given that its celebrated co-founder, Ronnie Tallon, was Miesian Plaza’s original architect. Indeed, it turns out Ronnie Tallon himself took a close interest in the project when the plans were being drawn up before he sadly passed away in 2014.
It would be easy to be intimidated at the prospect of upgrading such a hard-to-heat building, built during an era when energy was cheap, but according to Paul Hadfield, one of the lead architects on the redevelopment, the building’s good floor-to-ceiling height, its relatively modernity, and the quality of the materials used in the original construction lent itself well to being adapted and extended.
It was a very deep retrofit of the building and we had to dismantle it, really, and put it back together.
“From the outset originally, it was conceived as something that could be maintained over time,” he says. “Now, obviously, it was a very deep retrofit of the building and we had to dismantle it, really, and put it back together in its entirety and demolish cores and rebuild them and re-introduce structure to get it to work. But the bones of the building, if you look at the building before it was renovated and then look at it again, it’s the same.”
Certainly, a hallmark of the original design was its symmetry, and the effort that the team made to preserve this is a striking measure of the attention to detail that went into the project. As an example, Torpey points out how the ceiling grid from Senior Architectural Systems and the location of the ceiling lights were set out to be gridded off against the facade so that there were no awkward juxtapositions that could be spotted by the naked eye, inside or out. This was a tricky enough challenge because the 1960s-era building was designed on an imperial structural grid.
“They were all great fans of symmetry,” says Torpey. “Mr Ronnie Tallon, a great fan of symmetry. Mr Larry Goodman loves things to be symmetrical. All these things, they didn’t happen by accident. There was a huge amount of effort put into the ceiling coordination and getting all of these set out in accordance with the primary grid.”
The inside layout was subjected to extensive remodelling, including removing all the non-structural screed, which enabled the team to put in raised access floors – a pretty much standard requirement for modern offices to ensure easy access to data cabling and other services.
Heating is provided by gas-fired fan coil systems, with additional Kampmann trench heaters along the perimeter of each floor – adding up to 2,000 metres worth - mainly to improve comfort levels for those sitting near the glazing. “All that’s there to do, is on extremely cold winter days, is to make sure that there’s no chill factor at the interface point there where the floor meets the wall,” says Torpey.
The complex is beautifully finished throughout, with no hint of drafts or stuffiness, and was eerily quiet despite every floor being almost fully occupied. The same attention to detail is to be found in every part of the buildings, including the toilets, which are more akin to what you would find in a very posh hotel, with large, full-height cubicles, flattering lighting and super-efficient ventilation providing 20 air changes per hour. All toilet cisterns and urinals are fed by a rainwater harvesting system as well.
So, while the buildings have been significantly upgraded inside and out, how important was sustainability for potential clients? “It was huge”, says Torpey. “You could say it was very much client-driven; the direction given from day one was to make this the most energy-efficient building it could be because that was seen by the owner as being an ever-increasing demand of tenants. And it’s not going to go away. That was recognised.”
Certainly, what becomes clear early on is that Remley’s decision to aim for LEED Platinum (version four) status from the outset had a huge influence on the scope of the building’s sustainability credentials.
LEED is a rating system devised by the US Green Building Council, and it rates projects across six key categories: site sustainability, water efficiency, energy and atmosphere, materials and resources, indoor environmental quality, and innovation and regional priority (the latter covering any strategies not included in the other categories, or any particular concern in the building’s locality).
According to Torpey and others involved in this project, LEED has more global recognition than BREEAM, (Building Research Establishment Environmental Assessment Methodology), which has a greater foothold in the UK and Europe.
Experts say there are pros and cons to both approaches, but LEED has more international recognition and certainly appears to be gathering more steam and challenging BREEAM in Europe. So, this, in tandem with the degree of US investment in Ireland, made the decision to go for LEED over BREEAM perhaps more of a marketing decision than anything else.
It’s the first and only development in Ireland to be awarded LEED Platinum.
Mark Deverall, design co-ordinator at contractor John Paul Construction, says that setting LEED Platinum status as a target right from the beginning “was immensely beneficial and allowed us to plan accordingly to ensure the building would meet the determined targets”.
“Our early involvement also meant we were able to explore the attributes of the various building materials to suit the targets and address any potential waste management issues.”
Stringent energy performance targets are harder to achieve with a retrofit than with a new build, of course, but retrofitting an existing building can be beneficial in LEED. “It can take more than 80 years to make up for the environmental impact of demolishing an old building and constructing a new one, even if the resulting building is extremely energy efficient,” says US Green Building Council senior vice president Brendan Owens, who attended the certification presentation for the project.
“This is why LEED prioritises re-use of existing buildings as they are a critical part of making cities and communities healthier and more sustainable for residents… The work Miesian Plaza did to achieve LEED Platinum is a model for policy makers, design teams and developers to study and emulate.” On the other hand, the fact that all three of the buildings are protected structures presented a conundrum of tricky challenges in order to meet demanding energy use targets while still preserving their essential appearance and character.
According to Hadfield, the biggest challenge from the outset was the facade; given its protected status, there were restrictions on what could be done to it. Nonetheless, airtightness tests undertaken before works started showed that the facade leaked very badly, so there was considerable scope for improvement.
The curtain wall cladding, and double-glazed windows all had to be stripped and refurbished and fitted with new deeper CareyGlass glazed units. The new unit comprises an outer layer of bronze body tinted glass laminated to a pane of solar refl ective glass, while the inner layer comprises two panes of extra clear glass so as not to alter the bronze hue (making four panes in total). The double lamination also provides redundancy should any of the panes break.
One of the best indications of quality of workmanship comes with the scrutiny of a blower door test. The three buildings posted impressive q50 results of 2.07, 4.53 and 4.62 m3/hr/m2 @ 50 Pa. According to David Torpey, these results – and the attention to detail evident throughout the project – owe a lot to the approach the team took to meeting the Building Control Amendment Regulations (BCAR), working hand-in-hand with leading independent assigned certification firm i3PT, who use a range of measures to track and record quality and compliance of construction projects. “Every piece of the façade, every piece of the EDPM that were put in was inspected and photographed.”
i3PT’s environmental manager Archie O’Donnell says the project’s success didn’t happen by accident. “The culture on a project happens top down from the owners, the project manager, the contractor. That permeates through the project to the guys on the tools. David Torpey set a very clear objective that everyone could roll in behind.”
Meanwhile the corners of the south, east and west elevations of the buildings are fitted with a second, inner double-glazed skin, with a 600 mm ventilated cavity between this and the outer glazing. Ventilation slots at the base and head of the outer glazing are designed to allow for passive ventilation of the cavity, to help prevent thermal build up, while there are also motorised solar reflective blinds governed by roof-mounted weather stations.
As well as giving excellent heat and sound insulation, Torpey says these twin walls will also give clients greater flexibility with regards to remodelling without needing expensive alterations to the base infrastructure at a later stage. “So, the decision was made, and it cost a lot of money both in terms of putting it in and losing some floor area, but we made that decision. We were either going to say that these buildings were of a particular standard or they weren’t.”
The upgraded façade was crucial in reducing heating and cooling requirements and was a significant boost to the energy efficiency, accounting for almost half of the 77% reduction in energy demand. To put this further into perspective, the overall energy demand today of 144 kWh/m2/yr – simulated in the IES Virtual Environment software – is a far cry from the 457 kWh/m2/yr the pre-retrofit building was scoring in LEED.
As well as the bronze in the facade, there was also bronze in the inside of the building, but it was in a much worse state than on the facade, so the decision was taken to replace it with new aluminium capping but anodized in bronze. Working with Dublin City Council, Scott Tallon Walker produced no less than nine different sample panels to find the best match of tinted glass to the original bronze tinting.
The original bronze blinds were replaced with white blinds which have a bronze coating at the bottom to preserve some of the original aesthetic and which are, unusually, concave rather than convex.
Given that this was a five-year project that started in 2013 in earnest, it’s worth noting that Remley went out of their way to source materials with EPDs (Environmental Product Declarations) at a time when practically nobody else in the country was looking for them – a full three years before the Irish Green Building Council launched the EPD Ireland register of audited construction products.
Complying with LEED also requires proper documentary evidence. “We had to show them, in terms of the disposal strategy that 95%, both by volume and weight, did not go to landfill, it was recycled,” says Torpey. “So, for instance, all of the original carpets that we had here, they all went for recycling.”
The development is heated by a combination of modulating condensing gas boilers, along with a gas-fired CHP in block one, which collectively provide low temperature hot water to fan coil units and trench heaters in the offices.
Meanwhile the energy load for cooling is significantly reduced by a thermal energy store from Crystal Air PCM, using phase change materials (PCM) which change from liquid to solid state using Pluss OM11, an organic PCM with a melting point of 9.5C, to operate with standard chilled water flow and return temperatures (6/12C) and enable the next day’s cooling load to be generated efficiently and economically at off peak electricity rates – and stored till required. The operation of all the heating and cooling kit for the buildings is watched over like a hawk by building manager Sarah Burns – the tour for Passive House Plus included a building management nerve centre with a multitude of live and logged data available on the building’s performance.
Another impressive feature at the ground floor basement level is the separate bicycle hall with its own dedicated entrance and space for 225 bikes – full of bicycles on the day Passive House Plus visited – plus a super-ventilated, underfloor-heated drying room (for wet and sweaty gear) and even a couple of fully equipped service stations for fixing bicycles, and a rainfall radar display to keep staff ahead of the weather. There’s also a well-equipped gym and showers. The underground car park spaces are a bit wider than standard and include six charging stations for electric vehicles.
The provision of these facilities goes well above and beyond what was required by the LEED certifiers, but Torpey says the certifiers were “gobsmacked” when they saw them.
“But what they were most gobsmacked about was the use [of the cycling facilities] ...you can see the use and how popular it is. I would say that if you do give the correct level of infrastructure, people will use it.”
The heating system has been also been broken up into multiple zones for greater flexibility, which means being able to localise usage at quieter times, such as at the weekends.
But from the perspective of working with tenants to ensure that the building’s energy performance is optimised, securing leases of 20-25 years is key. “The benefit of that is, is that we cannot quite dictate, but most certainly direct and encourage tenant compliance with our preferences with regards to that environment,” says Torpey.
Whereas other landlords might “cut the ribbon and walk away”, Remley believes it can assist tenants to get the most out of the building. “It doesn’t come from a single meeting. It doesn’t come from a statement. It comes from working together, analysing the core data.”
As a finished product, Hadfield says the project has revitalized not just the buildings but the space around it. “It feels like part of the city again; before it felt like it was slightly being pulled away from the city because it hadn’t been used as much in the last, say, 10, 15 years.”
“But I think the biggest takeaway, really, is that you can achieve so much with an existing structure providing the quality is there in the first place.”
According to Archie O’Donnell of i3PT, it shouldn’t be surprising that a rigorous approach to meeting BCAR – in this case with an independent, scrupulous assigned certifier implementing a systematic approach to compliance, and maintaining an evidence trail – should help to achieve a high-performance building.
“BCAR interfaces with energy efficiency and passive house because the objectives are the same – the BCAR process is synonymous with quality. If you hadn’t a regime you should still be delivering those quality objectives. Where construction quality and passive house overlap is in that outcome-focused approach – where designs are reviewed and co-ordinated, materials and methodologies are checked, installation works are inspected and supervised and performance at completion is verifi ed with detailed records collated as evidence of the good work done.”
But will such a strong focus on quality and sustainability become a more common feature in commercial building designs?
David Torpey sees a strong demand for sustainability among his client base, including the kinds of multinational corporations looking for high-end European office accommodation. “The market expectation in Washington at the moment is that if it’s not LEED Platinum, then it’s not for us,” he says. “There should be no fear within the sustainability community that there isn’t an understanding and an acceptance from the commercial side. We accept that this is absolutely a base requirement from our tenants. Not just for sustainability but in terms of occupancy costs, staff comfort, and their staff enjoying working in the building.”
Selected project details
Client: Remley Developments
Architect: Scott Tallon Walker Architects
Main contractor: John Paul Construction
Assigned certifi er: i3PT
Civil & structural/M&E engineer/ environmental consultant: Arup
LEED consultant: JAE Engineering
LEED assessment: Longfields
Quantity surveyor: Kerrigan Sheanon Newman
Fire consultant: Michael Slattery Associates
Planning consultant: Stephen Ward Town Planning & Development
Airtightness testers: Building Envelope Technologies
MEP installation: Designer Group/Winthrop
Glazing & cladding contractor: Architectural Aluminium Ltd
Glazing system: CareyGlass
Air handling units: FläktGroup
Fan coil units & trench heaters: Keane Environmental
Condensing boilers: Hevac
CHP: Temp Technology
Building management system: Ashdown Controls
Facade management system: Crossflow
Thermal energy store: Crystal Air PCM
Rainwater system: Capcon
Internal paints: Keim/Dulux
Render system: Sto
Wool insulations: Rockwool/Isover/Knauf
Gypsum boards: Gyproc
Flooring: Interface/Forbo
In detail
Building: 21,800 m2 office building (Grade A)
Location: Miesian Plaza, Baggot Street, Dublin 2
Completed: November/December 2016 (tenant fit-out followed this)
BER: Not required (listed property)
Environmental assessment method: LEED Platinum Version 4 certified
LEED Energy Model for proposed building: 144 KWh/m2/yr (net delivered energy, including regulated (space heating, hot water, ventilation, cooling, lighting and unregulated loads (plug loads, lifts, etc). Based on standardised occupancy profile.
LEED Energy Model for original building: 457 KWh/m2/yr (used for comparison to determine LEED energy cost savings)
Calculated primary energy demand: (iSBEM, primary energy, regulated loads) Before: 400 kWh/m2/yr After: 100 kWh/m2/yr
Energy bills: Not available
AIRTIGHTNESS
Before: Not available though it was known the façade leaked badly
After (at 50 Pascals): Block 1 q50: 4.62 m3/hr/m2; n50: 0.89 ACH Block 2 q50: 4.53 m3/hr/m2; n50: 1.27 ACH Block 3 q50: 2.07 m3/hr/m2; n50: 0.61 ACH (Note q50 results are as per airtightness test, n50 results were calculated by Greenbuild for Passive House Plus based on q50 results and gross building volumes and are estimates only).
Ground floor: Upgraded to U-value: 0.20 W/m2K
Roof: New extensive green roof with tapered rigid insulation board with minimum U-value of 0.20 W/m2K
CURTAIN WALLING (before)
- Non-thermally broken semi-unitized bronze curtain walling system, incorporating floor-toceiling bronze body tinted double glazed units, and bronze clad spandrel panels between the first-floor level and roof.
- Non-thermally broken stick bronze curtain walling system, incorporating an upper and lower row of double glazed units between the ground floor level and the soffit of the first-floor level.
U-value (centre pane glass only): 2.9 W/m2K U-value (glass + spandrel + framing): 3.8 W/m2KM
CURTAIN WALLING (after)
Cladding upgrade works comprised the following:
- asbestos removal from the existing spandrel panels
- insulated backing panel to the existing spandrel panels
- floor edge thermal insulation infill
- new fire break detail
- new CareyGlass double glazed units, comprising four panes of glass (outer laminated bronze tinted/solar reflective panes, argon filled cavity, inner laminated extra clear/extra clear panes)
- new thermally broken and insulated inner bronze anodized aluminium capping and framing
- new outer weather seals
- new inner seals and membranes to provide second line of defence from a weathering prospective
- new weep holes to the existing carrier frame to allow for drainage, pressure equalisation and ventilation of the double glazed units
U-value (centre pane glass only): 1.0 W/m2K U-value (glass + spandrel + farming): 1.65 W/m2K
Note: An extension to block one was constructed using a structural steel frame and the same facade system as outlined above.
HEATING SYSTEM (after): The buildings are provided with a four-pipe fan coil system for heating throughout (developer standard fit-out). Natural gas fired boiler plant is used to generate low temperature hot water (LTHW). Gas plant comprised of 3 x De Dietrich boilers in Block 1 (1 x C330-650 ECO; 2 x C630-1300 ECO); 2 x boilers in Block 2 (De Dietrich C330-280 ECO) and 2 in Block 3 (2 x De Dietrich C330-430 ECO).
Low temperature hot water is pumped to each floor of the three buildings and valved and capped on each floor shafts and provided with heat meters for use in above ceiling fan coil units (developer standard fit-out) which provides heating to the floor plates. Perimeter Kampmann trench heaters are provided throughout all three blocks. All connections are metered.
Ventilation: Series of FläktGroup air handling units (AHUs) to each block. All AHUs treat and distribute fresh air at a rate of 14 l/s/ person (one person per 8 m2 net floor area), to all office areas (to two separate locations on each floor, in all three blocks). Vertical ducts carry fresh air to and extract air from all floors. The AHUs are fitted with chilled water and hot water coils to temper the incoming, filtered, outside air. AHUs incorporate thermal flywheels for heat transfer.
Thermal energy store: A 1,000 kW thermal store contained in 5 insulated vertical tanks filled with savE phase change material (PCM), manufactured for Crystal Air by Pluss Advanced Technologies, encapsulated in hermetically sealed HDPE crystal spheres for the storage and transfer of the buildings’ thermal requirements – with cooling generated at night making use of off-peak grid electricity, for both fan coil units and air handling units.
Electricity: Block 1 features a gas-fired 75 kW ENER-G combined heat & power (CHP) plant.
Water: Rainwater collection tanks are located at basement level of each block. Booster pumps distribute filtered rainwater for WC flushing.
Green materials: A broad range of products with EPDs were specified from brands including Besam, Dorma, Dulux, Forbo, Gerberit, Gyproc, Hilti, Interface, Isover, Kiem, Knauf, Mosa, Norament, Promat, Rockwool, Senior Architectural Systems, Sto, Uzin, Ventec, Wavin, etc.
Image gallery
-
13184-PLA-0533-A1-20191119 13184-PLA-0533-A1-20191119
-
Miesian-Plaza-Site-Plan Miesian-Plaza-Site-Plan
https://mail.passive.ie/magazine/new-build/mies-en-scene-iconic-dublin-offices-get-deep-green-treatment#sigProId06da3d5bfa