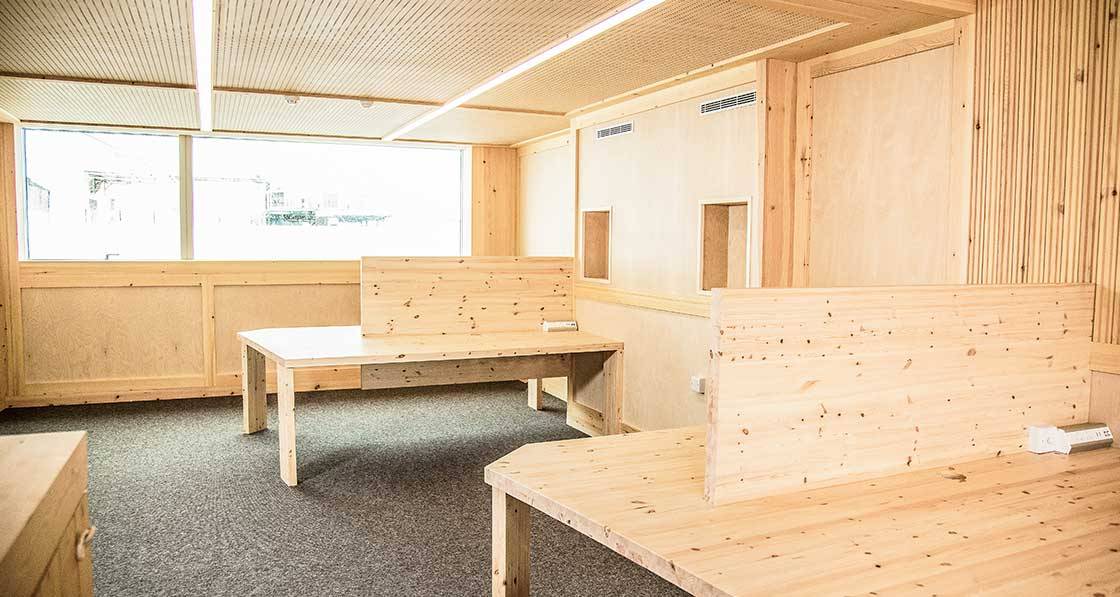
- Upgrade
- Posted
Form and function
Run-down terraces are an all-too-common sight in towns and villages across Ireland, but an ambitious deep retrofit project in Tralee provides an inspiring blueprint for regeneration, taking a cold 19th century terraced office and turning it into a beautifully designed space with tiny energy bills, fit for the 21st century.
Click here for project specs and suppliers
Building: 129 m2 mid-terrace, 19th century office building
Method: Deep retrofit with internal insulation, plus extension
Location: Tralee, County Kerry
Standard: Enerphit Classic (passive retrofit standard)
Energy bills: €14 per month for spacing heating & ventilation. Estimate. See ‘in detail’ for more.
€14 per month
A 19th century two-storey, mid-terraced commercial building with decidedly wonky party walls might not strike you as the most natural choice for a passive house retrofit, not least because external insulation was not an option, and access to the site was poor.
However, as the offices for a company that specialises in high-quality building fabric design and project management, it is not surprising that owner Jeremy Walsh — along with his architect Douglas Carson — successfully deployed a fabric-first approach to transform this exceptionally hard-to-treat building into one that meets the Enerphit standard for retrofit.
Bought in 2016 by Jeremy Walsh Project Management, number 10 Gas Terrace in Tralee did have at least a few things going for it: it was structurally sound, there was space to extend out the back, and it is located right in the commercial heart of Kerry’s bustling capital town.
Mid-terraced buildings are usually not the worst offenders when it comes to retaining heat, but this building was “freezing, absolutely freezing” for its occupants for the three odd years they had used it, Walsh says.
However, his intention was always to renovate and having overseen a major renovation and extension to his own home, also to the Enerphit standard, this project finally commenced in 2019. Walsh was first exposed to the passive house concept as far back as 2011 by a client for a project that never got off the ground, but “it kind of stuck with me ever since then”, he says, particularly for its close adherence to the science of building physics.
In 2013 Walsh went on a two-week passive house course in Germany with an eye to implementing the standard on his home, a job which he completed in 2015. Living day-to-day with high levels of comfort and low energy bills, and the monitoring of two Netatmo sensors that confirm the excellent indoor air quality, swept away any lingering doubts he had about the passive house concept, and in particular mechanical ventilation.
“Conceptually, I got it as an engineer, but it was living in it that really drove it home.”
It’s kind of everything I could have hoped for.
With his feet firmly in the passive house standard and all the detailing that it entails, it was a much shorter hop and skip to doing the same again with 10 Gas Terrace. The project was also intended to be something of a shopfront for Walsh’s business. “Essentially I wanted an office that I’d be proud of and that our company and all the staff will be proud to work in, and a by-product of that is that it would be a nice place to show off to our clients,” he says.
More specifically, he wanted a light-filled space that would allow his team to collaborate as much as possible. “I wanted a space that was going to be open plan, a space that we could collaborate, work together well and produce a good team atmosphere in the place.”
For the renovation of his own home, Walsh had worked with Douglas Carson, a family friend who runs a Dublin-based practice with his wife, Rosaleen Crushell, and opted to hire him again for Gas Terrace. Walsh naturally assumed the role of project manager and main contractor, which included looking after the civil and structural engineering, and fabric design and detailing.
You design it thinking about the person who’s coming up the street.
Carson has worked on low-energy building projects before, but appears to have relished working for Walsh because there was no large team of consultants to engage with, and because their working relationship in terms of responsibility for the passive house design was fairly fluid, although Walsh took the lead. “That’s the best way to work, I think, when you’re working with somebody; that things are blurry in terms of who is what and who does what,” Carson says.
He liked the fact that the building was in the centre of Tralee town, but not on a busy street, so access to the front was easier.
Furthermore, a co-operative neighbour facilitated access to the rear, enabling the team to crane-lift in large items like the glulam beams. But with restrictions on what could be done with the front and the very back, as the footprint of the building took up the entire site, most of the focus of the project works had to be on the “in-between stuff”.
https://mail.passive.ie/magazine/upgrade/form-and-function#sigProId5cca0977ea
That said, the design of the facade is intriguing and something that Carson is quite proud of. Gas Terrace is a narrow lane that used to face onto the former Denny sausage factory in the town and, while this has now been demolished - a new commercial development is on the way - the front of the building will still only ever be approached from its left or right side. This inspired what Carson terms an oblique design approach for the facade. “That means you design it thinking about the person who’s coming up the street, as opposed to somebody who’s approaching it from the front.”
The result is achieved by sills that are incredibly deep, and an expanse of Velfac aluclad windows that are set well back into the openings. “That’s not always necessarily the optimum place to put [the windows] in terms of thermal performance, but it was kind of our response to designing it obliquely,” explains Carson. “So, when you approach the building, you don’t see any glass; it appears more like a monolithic mass of render and paint. The joinery of the doors and windows also gets to be protected from the rain.”
With no room to use external insulation on the front walls or at the rear, it had to be internal. So having the windows flush with the internal insulation also facilitated the desire not to have internal wooden sills at the upper floor level, which Carson insists “would just gather dust and never be cleaned”.
The biggest challenge with the building fabric was dealing with a hodgepodge of boundary conditions. The original stone walls made up the front facade and extended about a third of the way back, but there were other party walls and neighbouring extensions of various construction types. “Each boundary condition required a slightly different treatment but faithful to the overall insulation strategy,” Walsh says.
“Most of the existing rear walls had to be demolished as either they did not follow the boundary or were not structurally sound.” These were rebuilt with thermal blocks at ground level, and timber frame at the rear of the first floor. The original stone walls were preserved, however, and insulated internally with Isover Metac mineral wool.
The measured performance is testament to the fact that the building simply works.
Insulating internally always carries a risk of condensation, particularly against older solid wall structures, because of the risk of creating a dew point — a sudden drop in temperature where water vapour condenses to liquid — between the new insulation and the old wall. In this case, there is an air gap behind the insulation to drain away any moisture that might collect. A dynamic condensation analysis by passive house certifier Earth Cycle Technologies, using the WUFI software, also confirmed that the build-up was safe.
As a two-storey office with a long footprint, getting sufficient light was always going to be a priority, and this was achieved partly using generous roof lights. But the issue of creating sufficient ventilation for the downstairs toilet was a challenge that called for an inventive solution. “In our mind, it’s not really acceptable that you’d have a toilet and you can’t open a window to get fresh air,” says Carson. There was also no lobby to separate the WC or the adjoining shower room from the corridor outside, which extends into the kitchen.
And even though the building would be mechanically ventilated, the team still wanted to be able to get fresh air into the bathroom quickly.
The clever solution was to create a tiny courtyard, with large doors making up three of the four sides of its rectangular shape: one leading into the shower room, one into the toilet and one into the meeting room. “The challenge was to keep that in as a kind of a device to get indirect sunlight into those three spaces but, more importantly, to get fresh air very quickly when it needs to be despite the [MVHR] machines doing a lot of the ventilation work,” Carson says.
This article was originally published in issue 39 of Passive House Plus magazine. Want immediate access to all back issues and exclusive extra content? Click here to subscribe for as little as €10, or click here to receive the next issue free of charge
Being an open-plan office with space for eight staff, but also fairly small at 140 square metres, acoustic design was another element that informed the choice of materials for the finishes, while also creating its distinctly warm northern European interior.
“What I was looking to create was a great atmosphere that people can work well together and collaborate and yet not put each other off, and so acoustics are a major part of that,” says Walsh. Previous experience of working with Brian Johnston of CLV Consulting on an office building in Killorglin reinforced the value of making this a priority.
“Even before the finishes were chosen, there were acoustic treatments on the ceilings and you could really tell the difference between something that had considered acoustics and something that hadn’t.”
Johnston performed a desktop analysis of the two open-plan floors and the meeting room (complete with polished concrete floors downstairs) and recommended the correct amount and spacing of holes in the birch plywood on the walls and ceilings as a Class C absorber. The design and the spacing of the holes had been chosen especially to achieve this effect. “There’s 50 mm mineral wool behind the perforated plywood which acts as both thermal and acoustic insulation within the service cavity, and so it is an overall neat solution,” says Walsh.
Both Carson and Walsh are delighted with the finished result, with Carson especially pleased with the exposed tongue and groove timber on some of the walls and the balustrades, creating a nice textual corduroy effect, one that is likely to remain a permanent part of the décor.
The measured performance is also testament to the fact the building simply works as it is designed to. The building’s energy demand is so small, Walsh estimates that during 2021, its solar PV array and battery will have supplied 64 per cent of its total energy needs. Indoor environmental monitoring also indicates that carbon dioxide, humidity and temperature rarely exceed comfortable levels (see ‘In detail’ for a breakdown of the figures).
Walsh says: “It’s a very calming place to work actually, and I think that’s a combination of the wood and the acoustics, so it’s just a nice place to work… it’s kind of everything I could have hoped for really.”
He struggles to pick out one favourite feature “but it’s probably the curved plywood beams on the meeting room ceiling, which is an example of what is achievable by combining great architecture, structural design and onsite workmanship”.
“We may add more splashes of colour over time, with bits and pieces of art or something like that, but for the moment, I’m just happy to be here.”
Embodied carbon
An embodied carbon calculation was conducted by Tim Martel using PHribbon. The analysis assumed a 50-year design life for the building, as per the EU’s Level(s) scope, as this is required in assessments against the RIAI 2030 Climate Challenge. The calculation assumed one replacement of the building’s heating and ventilation system – a perhaps optimistic decision, given the reference to 17-year design life in Product Environmental Passports for heat pumps and ventilation systems, but one which takes account of previous research on the performance of a 25-year-old heat recovery ventilation system in the first passive house. The building’s large PV array was also assumed to be replaced once, as was the building’s cement render, the asphalt roof system, the carpet and vinyl flooring, with bathroom fittings assumed to require two replacements. CEM I was assumed for the concrete floor – when in reality 30 per cent GGBS substitution occurred, which would have reduced the figure for this element.
The building posted a score of 374.1 kg CO2e/m2 – 111 kg of which was solely related to the building’s large solar PV array. While this does not take account of the substantial contribution the array will make to displace emissions from grid electricity, this remarkable finding places the PV array as by far the biggest single source of embodied CO2 in the building –- higher than the entirety of the substructure, or the walls, the roof, the windows, or all other building services combined.
Selected project details
Clients, passive house design, civil & structural engineering: Jeremy Walsh
Project Management Architect: Carson and Crushell
Main contractor: O’Mahony Builders
Passive house certification & dynamic condensation analysis: Earth Cycle Technologies
Plumbing contractor: Diarmuid Walsh
Electrical contractor: Garrett Walsh Electrical
Airtightness test: Air Matters
Carpentry: Dan O’Keefe
Airtightness products: South West Radon
Windows and doors: Velfac, via Teroco Windows & Doors
Roof windows: Reynaers, via the Folding Door Company
Fit out: Harris Carpentry
Flooring: Concrete Creations
Carpets: Lovett Carpets
Roofing: Gleasure Roofing
Space heating & ventilation system: Nilan Ireland
Solar PV: Gilroy Solar
Lighting: Thorn Lighting
Acoustic consultants: CLV Consulting

In detail
Building type: 145 m2 mid terrace 1800s stone building (129 m2). Enerphit retrofit with a new extension to the rear.
Location: 10 Gas Terrace, Tralee, Co Kerry
Completion date: December 2020
Enerphit certification: Certified
(All below figures post-retrofit)
Before: Not available
After: B1 BER (126.59 kWh/m2/yr)
Space heating demand: 9 kWh/m2/yr
Heat load: 8 W/m2
Primary energy demand (PHPP): 73 kWh/m2/yr
Heat loss form factor (PHPP): 2.67
Overheating (PHPP): 8 per cent
Number of occupants: 6-7
Energy performance coefficient (EPC): 0.61
Carbon performance coefficient (CPC): 0.63
Measured energy consumption: Before: Assumed annual electric consumption
based on full occupancy, the pre-existing condition is 13,900 kWh (107 kWh/m2/yr) however this is probably an overestimate.
After: Estimated delivered annual electric use is 4,300 kWh (from PHPP). Based on the data available for 2021 as of 16 November and extrapolating to the end of the year, Jeremy Walsh Project Management estimates the following energy use: Total expected electrical use: 4,654 kWh; expected imported electricity from the grid: 1,670 kWh (approx. 35 per cent). This indicates the on-site solar photovoltaic system and battery supplied approximately 64 per cent of energy use during 2021. Projected total electricity use is broken down as follows. Lighting: 945 kWh; heating and ventilation: 1,317 kWh; general plug points and other: 2,392 kWh. However, the solar system had software issues in early 2021 and the occupants were still getting used to heating settings, so these figures may improve further in 2022.
Energy bills: Using the above projected energy consumption figures for 2021, and the 35c per kWh rate (including VAT) that JWPM is paying for electricity, the total cost of imported grid electricity for 2021 is estimated at €585. If it is assumed that the same proportion of grid electricity is used for heating and ventilation as for all energy use in the building (e.g., 36 per cent), then this could be expected to require just 474 kWh of imported electricity all year, at a cost of just €166, or approximately €14 per month. These figures include VAT but not standing charges or PSO levy.
Airtightness (at 50 Pascals): 0.8 air changes per hour
Thermal Bridging: Thermal bridges calculated using Dartwin Mold Pro v5 software. 37 details modelled. See images.
Ground floor:
Before: Uninsulated concrete floor. U-value: 0.6 W/m2K
After: 125 mm concrete floor on 150 mm Xtratherm XT/UF Polysio insulation. U-value: 0.150 W/m2K
Original stone walls:
Before: Approx 600 mm stone walls. U-value: 0.9 W/m2K
After: 600 mm stone wall, followed inside by 40 mm air cavity, 125 mm timber studs at 400 mm c/c filled with 125 mm Isover Metac insulation (lambda=0.034 W/mK), Siga Majpell vapour control & airtight membrane, 50 x 50 softwood horizontal battens at 600 mm centres with 50 mm Isover Metac, 18 mm birch plywood sheeting. U-value: 0.188 W/m2K
Rear extension walls (party walls):
Before: Neighbour’s block wall, air cavity, 215 mm concrete block. U-value: 0.4 W/m2K
After: Neighbour’s block wall, 50 mm air cavity, 150 mm Roadstone Thermalite block, 150 mm timber stud walls with 150 mm Isover Metac between the studs, Siga Majpell vapour control & airtight membrane, 50 x 50 timber battens with 50 mm Isover Metac between the studs, 18 mm birch plywood sheeting. U-value: 0.166 W/m2K
Rear first floor wall: 10 mm cement board on 50 x 32 treated timber battens and counter-battens, breathable membrane, 75 mm Polyiso sarking insulation, 18 mm plywood sheeting, 175 mm timber studs at 400 mm centres with 180 mm Isover Metac between the studs, Siga Majpell vapour control & airtight membrane, 50 x 50 timber battens at 600 mm centres with 50 mm Isover Metac between the battens, 18 mm plywood sheeting. U-value: 0.130 W/m2K
Pitched roof (over original building): New roof slates on treated timber battens, followed underneath by breathable roofing felt, timber roof rafters, ventilated air space, with lower timber ceiling rafters with a combined thickness of 220 mm with Isover Metac insulation between the rafters, Siga Majpell vapour control & airtight membrane, 50 x 50 timber battens at 600 mm centres filled with 50 mm Isover Metac, 18 mm birch plywood sheeting. U-value: 0.134 W/m2K
Extension roof: 2-ply mineral felt cap sheet and underlay, on 150 mm Polyiso insulation, vapour control layer, on 38 mm solid timber decking. U-value: 0.143 W/m2K
Windows & doors: Velfac triple glazed, argon-filled, Ribo alu 2 windows and doors to front façade. Velfac 200 Energy aluclad windows and doors to the rear. Overall U-value of 0.80 W/m2K
Roof windows: Reynaers CS/CP fixed rooflight system with triple glazing (argon-filled). Overall U-value: 0.50 W/m2K
Heating system:
Before: Direct electric heating and electric storage heater.
After: Nilan Combi 302 Polar provides ventilation with highly efficient heat recovery and comfort heating and cooling. Combi 302 Polar combines two heat recovery techniques, where the unit first recovers 85 per cent of the heat via the highly efficient counter flow exchanger. The residual energy is recovered via the unit’s heat pump, which is able to both heat and cool the supply air. Ventilation: See heating system above. NilAir ducting system used.
Hot Water: Joule 300 L hot water cylinder is heated by excess electricity generated from the solar PV array, particularly over the weekend when the office is unoccupied. This provides most of the hot water needs for the week. A back-up electric boost option is available if required.
Green materials: All timber furniture, structural timber, birch plywood, timber decking from PEFC certified sources; concrete floor has GGBS content of 30 per cent. Flat roof to the rear is designed to take sedum roof (to be installed later).
Electricity: 6 kWp Solax solar photovoltaic array c/w inverter and 6.3 kWh battery with expected annual output of 5,302 kW. Once the battery is full the solar array next heats the hot water cylinder before discharging to the grid.
Lighting: Thorn Equiline and Katona LED lighting controlled by occupancy sensors and daylight dimming sensors.
IAQ monitoring: Nuwave CaDi sensor recently installed. For the 2.5 months for which data is available the CO2 levels exceed 999 parts per million for just 23 seconds and the humidity was outside the recommended range (45-65 per cent) for 1,194 seconds (19.9 minutes).
Image gallery
https://mail.passive.ie/magazine/upgrade/form-and-function#sigProIdfadb19d926