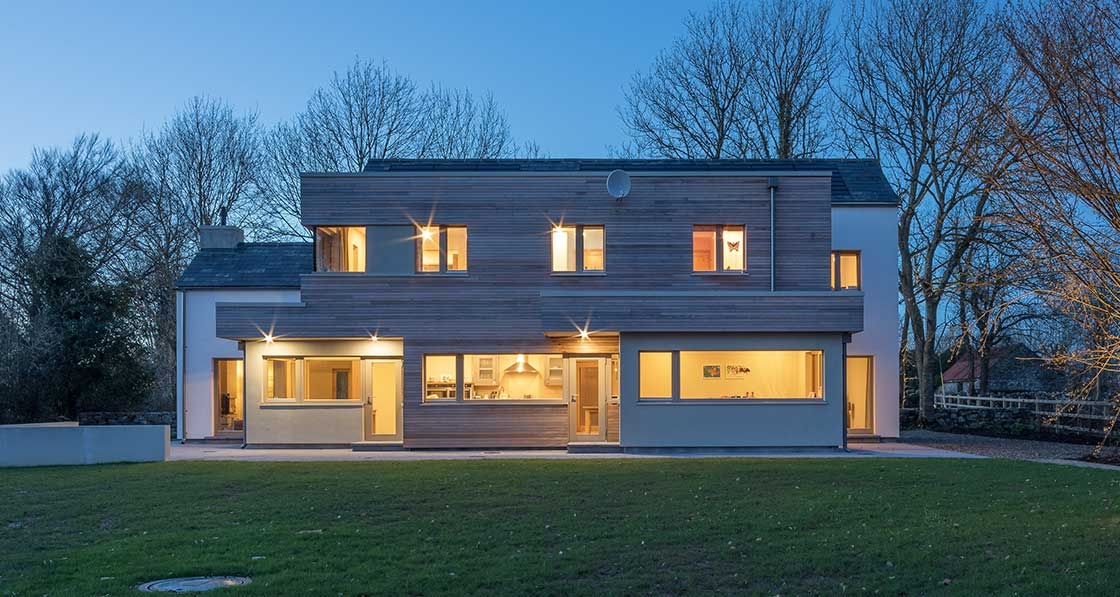
- New build
- Posted
A green builder's dream green home
This is what you get when one of Ireland’s most experienced low energy builders creates a home for his own family, with help from one of the country’s foremost ecological architects — a modern and elegant passive house that pays detailed attention to sustainability at every turn.
Click here for project specs and suppliers
This article was originally published in issue 20 of Passive House Plus magazine. Want immediate access to all back issues and exclusive extra content? Click here to subscribe for as little as €10, or click here to receive the next issue free of charge
When Niall Dolan set out to build his own house, the results were always going to be interesting. Dolan set up GreenTec Ecological Homes Ltd in 2002, and ever since then, he’s been at the forefront of sustainable building in Ireland. Based in Craughwell in south county Galway, the home Dolan built for himself, his wife Mary and his two children is a showcase of everything he has learned over the past 15 years.
One of the fundamental aims of the build was to create an exemplar project in sustainable building for one-off rural houses. And what the Dolans have ended up with is a passive, nearly zero energy building that makes abundant use of sustainable, healthy materials.
It’s also a beautifully designed home, and indeed, Dolan and his architect Miles Sampson put lots of time into making sure the finished house was both traditional yet contemporary. “I knew that Niall would be building the house to the highest standards in sustainability and construction quality,” says Sampson.
The layout of the timber frame house takes its inspiration from the traditional farmhouse cluster, where home and outbuildings enclose a central courtyard. It also respects the site’s traditional boundaries of dry limestone walls and mature trees, all of which were retained.
But just because the project had such an experienced contractor and client didn’t make it easy. For Niall Dolan, the central challenge of the project lay in simply getting the time to build the house in the first place. He explains that he struggled continually to find time between his clients’ projects to get the work done.
“This wasn’t a speedy build,” he says. “I did the foundation, then the frame the following year...and so on. It was very stressful because the other houses I was building took priority over mine. I was always on the back foot.”
Spreading the work out over such a long period caused quite a few complications. Take the wood fibre external insulation, a product that neatly represents the material choice across the project. The Dolans were keen to make sure that almost everything they used was natural. But by specifying wood fibre external insulation, the project took on a certain level of risk.
Niall explains that you need nearly five weeks of dry weather, first to fit the insulation, then for rendering. That would be challenging in any circumstances, but to find that block of time in between his other commitments was especially difficult.
“It was tough,” he says. “We just managed to get those five weeks in September 2015. If I’d missed that slot, I’d be a full year behind – there’s no way I’d be in the house now. When I’m building houses for clients and there’s wood fibre specified, I know I could lose my shirt on it because if the house starts at the wrong time, if there’s a delay on widows and you run over, the project is suddenly months behind.”
There were no such issues with the cellulose insulation specified for the walls. Over 11,000 recycled newspapers were used to create the insulation, which he chose not alone because it was a natural material, but because it compacts well and fills the entire wall void easily. But in order to deliver passive standard thermal performance, a deeper build up is necessary than would be required with a synthetic insulant.
Niall was also keen to find windows which did not use petrochemical-based insulation in the frames, and sourced a passive certified unit from M-Sora. The frames are made entirely of wood, and feature a patented technology which gives a passive standard U-value using air alone as an insulator in the frame. It’s interesting to note that specifying all timber, instead of aluminium-clad windows, reduced the spend on what is one of the biggest cost elements of any passive build by a full €10,000. By going with all timber units, Dolan was able to both maintain the traditional aesthetic he wanted for his house, and to keep faith with natural materials. The downside of course is the need to maintain the timber.
The use of external insulation actually helps out quite a bit here however. The wood fibre extends over the frames of the windows, reducing the surface area exposed to the elements. Moreover, Dolan explains that in his last house, the choice of an all-timber unit worked out really well.
“I got seven years out of them before I had to repaint, and it cost about €700 to do the job. So I did the maths. If you need to repaint every seven years, it’s a long time before you get up to ten grand.”
He had anticipated that a rooflight, which Sampson specified for the entrance area, would have to be specially made to meet passive house standard. But at a trade show in Germany, Dolan came across a passive certified quadruple-glazed unit from Velux that fitted the bill perfectly. The first of its kind in Ireland, it’s solar powered, and can be opened remotely.
Staying with solar power, Sampson was able to position the house to make maximum use of passive solar gains, while still retaining the mature trees. The back of the house faces south, and features a stepped profile to ensure that kitchen, dining room, sitting room and playroom all get equal sun. This elevation has a modern feel, with lots of glazing, while the north-facing front of the house has a far more traditional design, with small, dispersed windows looking onto the public road.
“The design challenge was to create a home that reflected the different aspirations of both Mary and Niall,” says Sampson. “The solution of using a more traditional architectural language facing the public road also tied in nicely with passive house certification allowing for smaller windows on the north side of the house.”
The flat sections of the roof will be planted with sedum, while the pitched roof has been fitted with a 4kW integrated PV array. The sedum area was sized by the architect to offset the amount of carbon used in the making of concrete for the foundations, thereby delivering a zero carbon build. In addition, the roof is wired to take a further 6kW of PV if required.
Dolan is also planning to source a battery to allow him to store power and thereby reduce his reliance on the grid at times when the PV is not producing. He also plans to have enough energy left to charge an electric car.
The house is primarily heated by a Nibe air source heat pump, supplying underfloor heating on both floors. There’s also a gas-fire in the sitting room, where Dolan didn’t specify underfloor heating, to avoid any risk of overheating in a room with façades facing south, west and north.
With so much sustainable building experience under his belt, you would think airtightness would not have been a problem on the build. Under normal circumstances, it wouldn’t have been. Again however, the fact that the Dolans had to stagger the project threw up unforeseen issues. Typically, Niall says, airtightness is done in one fell swoop over a two week period.
“I was bringing lads in for a day here and a day there. They’d do one room, then I’d have them off on another job, and to be honest, that just doesn’t work. You need your head in the job, and if you leave it for two months then come back to it, it’s going to take you a while to pick up where you left off.”
Frequently, the build team found themselves having to redo work just to make sure that the passive target would be achieved. “They might have primer put on the floor, then a month later, they’d have to reapply it because there was dust in it.”
Dolan adds that Emmet Nee, who helped erect the timber frame – manufactured by Advanced Timber Craft, who have since rebranded as Kudos – helped keep the building’s airtightness on track. “Emmet always ensured the first fix airtightness was under control,” he says.
Dolan was also keen to ensure that any of the structural and performance elements of the build would not hinder architect Miles Sampson’s design flair. That meant, however, that a canopy extending from the back elevation created a particular challenge as far as airtightness was concerned, where it met the thermal envelope.
The preliminary result measured by airtightness specialists 2eva.ie – 0.58 ACH – is just inside the 0.6 ACH passive threshold. Dolan expects this to improve further when the final test is completed, as much more sealing work has been done since.
One thing Dolan allowed additional time and budget for was slabbing the interior walls.
Instead of conventional plasterboard, he sourced magnesium oxide board.This has the advantage of having a much better racking strength compared to conventional gypsum slabs. You can hang everything from kitchen units to TVs directly from the boards – which again are natural materials – without the usual need in timber-frame construction to incorporate a timber filler behind the wall.
Ampak’s Variano membrane, fitted to walls and roof, provides airtightness and vapour control for the timber frame structure
Metal web joisting in the ceiling to contain services such as ventilation ducting
Raft foundation insulated with 250mm Kore Insulation, and 215mm Quinn Lite blocks to perimeter and rising walls
The pitched roof has been fitted with a 4kW integrated PV array and also features a Velux quadruple-glazed solar powered roof window
The house is finished with carefully detailed sustainable timber cladding
The wood fibre external insulation extends over the frames of the timber windows, reducing the surface area of window frame exposed to the elements.
But is it possible to quantify the impact of such an ecologically-minded spec? In the absence of a full life cycle assessment, there are some positive indicators. In very rough terms the use of the insulated raft foundation likely reduced concrete use by 40 to 50%. What’s more, an extremely low carbon alternative to Portland cement – ground granulated blast-furnace slag (GGBS) from Ecocem – was used, including 50% of the 50m3 or so of concrete used in the foundations, and 25% of the 17m3 in the floor screeds. According to Ecocem’s environmental calculator, the net effect is that seven tonnes of CO2 were prevented from being emitted into the atmosphere – which is equivalent to over 56,000 km worth of driving by a typical family car. That figure would almost double if the concrete-reducing effect of the foundations were added, even before considering the buildings other low carbon materials, and the amount of sequestered carbon in the building’s wide palette of timber materials.
The family moved in last September, and so far, all is great. “The heat is so consistent,” says Mary Dolan. “You don’t have to worry about closing doors or drafts. You’re not worrying about the kids being cold, even when you bathe them. I remember as a child shivering for an hour after a bath, but here it’s always warm,” she says.
But the real proof of the pudding is in the energy bills. “We checked the running costs of the heat pump from the 22nd of August 2016 to the 7th of Feb 2017. It’s €190 in total for heat and hot water, with hot water taking €110 of that.” The Dolans also spent €75 for one barrel of gas — that makes for a total of just €155 for space heating through most of autumn and winter.
Selected project details
Client: Niall & Mary Dolan
Architect: Miles Sampson Architects
Contractor & project management: GreenTec Ecological Homes
Timber frame: Kudos (erected by Emmet Nee)
Energy consultant: MosArt
Mechanical contractor: Western Energy Systems
Electrical contractor: F&H Electrical
Airtightness tester: 2eva.ie
Heat pump & underfloor heating: Unipipe
Cellulose insulation: Sustainable Insulation Products
Wood fibre insulation & airtightness products: Partel
Thermal breaks (Foamglas blocks): TIDL
Thermal blocks: Quinn Building Products
Floor insulation: Kore
Windows: DBP Fenestration Ltd
Roof window: Velux
Entrance doors: Geraghty Joinery
Cladding: Machined Timber Specialists Ltd
Screeds: Esker Readymix
GGBS: Ecocem, via Esker Readymix
Solar PV: Solar Century
Gas stove: JP Distributors
Timber flooring: Bearfoot
Flat roof membrane: Newell Roofing Products
Acoustic flooring underlays: Sheepwool Insulation
Additional info
Building type: 200 square metre detached two-storey timber frame house
Completion date: August 2016
Budget: €380,000
Passive house certification: pre-submission
Space heating demand (PHPP): 15.56 kWh/m2
Heat load: 9.57 W/m2/yr
Primary energy demand (PHPP): 73 kWh/m2
BER: Pending
Energy bills: €110 for hot water and €80 for heating from 22 Aug 2016 to 7 Feb 2017 (heat pump); €75 for gas stove in same period. Airtightness: 0.58 ACH at 50 Pa (final test yet to be completed)
Ground floor: Raft foundation insulated with 250mm Kore Insulation and 215mm Quinn Lite blocks to perimeter. U-value: 0.119 W/m2K
Walls: Factory-built timber frame with 22mm larch cedar & render externally, followed inside by 50 x 50mm treated battens and counter-batten, Ampack UV façade membrane, 80mm wood fibre board, 235 x 38mm cellulose-filled timber stud, Ampack membrane taped and sealed, 50mm service cavity insulated with Rockwool insulation, and 12mm MGO board internally. U-value: 0.126 W/m2K
Roof: Salvaged Blue Bangor slates externally on 50 x 35mm battens/counter battens, followed underneath by breathable Ampack roofing underlay, 100mm wood fibre, 235mm timber joists/rafters fully filled with cellulose insulation, Ampack airtight membrane, 50 mm uninsulated service cavity, 12mm MGO plasterboard ceiling
Windows: M-Sora Natura E112 passive certified triple-glazed timber windows. Overall U-value: 0.77 W/2K
Roof window: Velux quadruple-glazed, passive house certified, solar powered roof windows. Overall U-value: 0.70 W/m2K Heating system: Nibe VVM 320 air source heat pump with underfloor heating everywhere apart from sitting room. 200 litre hot water tank. DRU Global 60 gas fire with balanced flue to sitting room.
Ventilation: Brink 400 MVHR unit, Passive House Institute certified heat recovery efficiency of 84%.
Electricity: 4kW solar PV to roof slates
Green materials: Timber frame, MGO dry lining board, salvaged slate, cellulose insulation, wood fibre insulation, salvaged stone, GGBS cement (50% in slab, 25% in screeds), sheep wool carpets, cedar cladding, all-timber windows, sedum roof still to be fitted.
Image gallery
-
-
02 Site analysis 02 Site analysis
-
04 Design concept 04 Design concept
-
05 Sustainable design 05 Sustainable design
-
Ground floor plan Ground floor plan
-
First floor plan First floor plan
-
North south elevations North south elevations
-
West east elevations West east elevations
-
Sections Sections
-
https://mail.passive.ie/magazine/new-build/a-green-builder-s-dream-green-home#sigProIdece45b9dd4