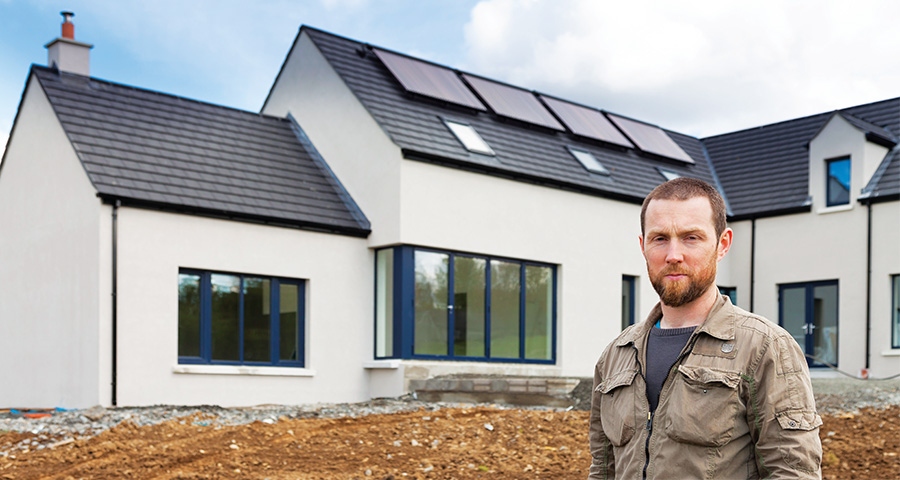
- New build
- Posted
The builder's view - why passive house doesn't cost extra
With this passive house in Co Kildare, father-and-son building team Pat and Paul Doran of Pat Doran Construction Ltd prove that meeting the strict low energy standard can be done for even less than a ‘normal’ build – to the tune of a €20,000 reduction in build costs compared to the Department of the Environment’s suggested compliance approach.
In 2013 I built my own low energy home with my father, Pat Doran, a builder with over 30 years of experience. Since then we’d completed a number of low energy projects, but we were eager for the ultimate challenge — building to the passive house standard.
But it’s rare to get the opportunity to build a passive house. There are a number of reasons for this, but perhaps the most significant one is cost. The general perception is that the standard is simply one many people cannot afford. As the recent Irish Building Control Act has driven up the costs of construction, this would seem to be more the case than ever. I would argue however that this is flawed logic, and that the opposite is actually the case. Due to the Building Control Act, Part L (conservation of fuel and energy) of the 2011 building regulations is now being more strictly enforced. All new dwellings built today have to be 60% more energy efficient than they were in 2005. In effect this means every new house built today has to achieve an A3 energy rating.
The front facade of the house incorporates a fairly traditional design, though the rear is more contemporary in appearance
To me this means there is now little or no difference in the cost of building a passive house and one that complies with regulations. If people are stuck with the cost of an A3 house, why not just build a passive house? In the latter half of 2014 we were presented with an opportunity to do just that. We were engaged to take on the building of a new 290 square metre detached house near Naas, Co Kildare. This was our first house on which the new Building Control Act would apply. It was also to be our first passive house.
During the tendering stage the client accepted this approach with one very important caveat — the house could not cost more than building a dwelling that was merely compliant with Part L. If there was to be extra cost, it would have to be marginal. We were about to find out what the real differences were between the highest energy standard in the world and our current building regs, both in terms of cost and the unique building challenges we would face on site.
The house features a Viking House passive slab insulated foundation system
To identify exactly what the differences were between a Part L compliant house and a passive house, I referred to a regulatory impact analysis published by the Department of the Environment in 2010, when Part L was being revised. This document included a table of nine dwellings modelled in Deap (Dwelling Energy Assessment Procedure) to meet the new demand for a 60% reduction in energy use over the 2005 regs. One of these dwellings, a 280 square metre detached house, very closely matched our project. During the pricing stage I used it as a benchmark to investigate the difference in cost between building to passive house and just building to Part L.
Whereas a Part L compliant house is evaluated by Deap, the compliance of a passive house is governed by another software program, PHPP. The Passive House Institute promotes PHPP as a tool for designers to ensure that a house will comply with the standard. From a builders’ point of view however I also found PHPP to be an excellent costing tool. I could evaluate different build-ups to determine which one was the most cost-effective solution to achieve the required U-value. It could also show me how far we would have to go beyond what Deap would deem sufficient for compliance. This in turn would allow me to identify the difference in cost between the two standards.
Metal web joists create smooth and neat runs for services
The first surprise was that when modelled in Deap the house required a passive level U-value for the floor of 0.15. The table suggested 110mm of PIR insulation under the slab to achieve this. My sense of vindication was short lived however, as this still wasn’t low enough for PHPP. It appeared PHPP was pushing me to spend more money on insulation in the floor beyond department guidelines for Part L compliance.
But then I began to investigate further. As PIR under the slab was looking to be an expensive option, I explored the possibility of an insulated raft foundation system. I received a quote for the Viking House passive slab from Airpacks which appeared to be very reasonable. It gave a U-value as low as .09, which was more than sufficient for PHPP. It also eliminated all cold bridges at the floor-to-wall junction.
This was vital for the passive house standard, which is unequivocal in accepting no thermal bridges. Yet how important was it for Part L which specifies thermal bridging should be reduced, ‘“insofar as reasonably practical”. To me this appeared to be a ‘get out of jail free card’ for having to eliminate cold bridges.
Thermal bridge free sills from Passive Sills with windows installed proud of blockwork
Yet when I went back to the department’s guide it required a Y-value of 0.08 and suggested that its acceptable construction details (ACDs) be followed to achieve compliance. When we priced the floor with the PIR board and the ACDs against the Viking House passive slab system, the results were startling. The Viking House foundation was over €5000 cheaper to get to finished floor level.
When it came to the construction stage, however, my father Pat was reluctant. He argued that strip footing was tried and tested, and if anything went wrong it would come back on us. The lower cost of this unconventional approach however wouldn’t allow him to discount the idea completely. So I asked Seamus O’Loughlin of Viking House to phone him, and somehow he managed to put Pat’s fears at ease.
During construction, however, nobody except Pat was allowed to compact the filling to the structural engineers’ specifications. He insisted that carpenters rather than general labour be brought in to assemble the foundation system. As a carpenter by trade himself, he worked with them closely to ensure everything was done right. Throughout the years I had always noticed he took special care with foundations, but on this project it was even more so. To his surprise things went much more smoothly than he had ever seen strip footings work, and it came in on budget.
Airtightness detailing with Siga tapes and membranes around the Velux roof window
The next challenge was the walls. The reference house in Deap called for a passive-level U-Value here of 0.14 to achieve compliance with the regs. It suggested 100mm PIR in the cavity and 50mm PIR dry lining to achieve compliance. In our opinion dry lining a new build is not a good idea for a variety of reasons, not least potential problems with mould.
Our preferred option was 150mm of Xtratherm’s PIR board in the cavity, which we had used in my own house — with fantastic results in terms of low heating bills. However PHPP told us this was — by a tiny fraction — insufficient for meeting the passive house standard in this case.
Zehnder Comfoair 350 MVHR system
We then considered external insulation, as it would work very well with the Viking House passive slab. In our experience external insulation was expensive, but Steven Magee of Airpacks made us a pitch on their EPS system, and suggested we also use specially rendered sills from Passive Sills in Cork. We priced it all up, and the results again defied the assumption that passive house is too expensive.
An external insulation system with 250mm EPS and U-value of 0.12 was marginally more expensive than the 150mm board in the cavity, with a difference of only a few hundred euro. However the guideline of 100mm in the Cavity and 50mm dry lining was €3000 more expensive.
The external insulation also worked very well during construction. The numerous cold bridging issues from junctions with steel, lintels and sills were eliminated with a continuous wrap from floor to eaves.
When it came to the roof the department guidelines required a U-value of 0.12 for compliance, well within the passive house range. The suggestion to achieve compliance was 150mm PIR between the rafters and 60mm PIR dry-lining below the rafters.
The block-built house was insulated externally with Kore EPS
PIR in the roof however was not our preferred option. Instead we preferred to full-fill the rafters on the slope with 300mm of Isover Metac high performance mineral wool. The rafters could then be counter battened for services and the void insulated with another 50mm of Metac. This boosted the U-value on the slope to 0.10. We also put 600mm of standard mineral wool between and over joists on all flat ceilings, bringing the U-Value here down to 0.08. This build-up easily satisfied the requirements of PHPP. There was also no competition in terms of cost. The cost of the materials alone, if we had used PIR in the roof, would have been €1,000 more than it cost us for supply and fit of all the mineral wool. On top of that we estimated you could easily spend another €3000 on labour as cutting and fitting rigid boards between rafters is extremely time consuming, and you will never get the full-fit possible with mineral wool.
At this stage our passive house was working out nearly €11,000 cheaper than the department’s reference Part L compliant 280 square metre detached house. There were still the windows to go however, and passive house insists on triple glazing, which hasn’t come cheap in the past. Yet the detached house modelled by the department in Deap required triple glazing to comply with Part L anyway. The client opted for Munster Joinery and their windows and doors had the added bonus of coming with Passive House Institute certification.
When it came to ventilation, however, there was a significant difference between the department’s reference house and our passive house. Part L accepts natural ventilation as compliant. Passive house does not accept natural ventilation; mechanical ventilation with heat recovery (MVHR) is required.
If you consider that the cost of installing three extract fans and wall vents came in at less than €1000, and MVHR came in at €6500, this represents a significant extra cost. So how was I able to justify this expense given our brief that any extra expense to the client should only be marginal.
The argument I used was that the extra expense could be offset against the reduced cost of the central heating system. This house is a 290 square metre dormer with four bedrooms, two living rooms, kitchen, utility and office. A standard house of this size would usually require anything in the region of 15 to 20 radiators. With our passive house spec, PHPP calculated that we needed 2550 watts to heat the house to 20C on the coldest day of the year. This could be roughly calculated as three radiators, two big and one small.
Reynaer’s aluminium bi-fold doors, triple-glazed with argon filling and an overall U-value of 1.0 W/m2K
I wasn’t brave enough, however, to suggest such a small heating system. What if we got a really cold winter? What if the clients felt 20C was cold? Satisfying the parameters of PHPP is one thing, satisfying client preference is quite another. Especially as the perception of temperature in a house is often a subjective experience.
I decided to build some redundancy into the system and asked PHPP how many watts the house would need to reach 25C inside if it was -15C outside. It came back with 7000 watts — or roughly seven radiators — which still represented a saving of €1300 euros in the cost of the rads alone without even taking into account the fittings, piping and labour of installation. From this perspective we were roughly able to half the extra expense of MVHR to €2500, which the client was willing to accept, especially when the added benefits of MVHR in terms of increased ventilation, comfort and health were explained.
There are far cheaper MVHR systems on the market, but there are also horror stories of poor installations and homeowner comfort being severely impaired as a result. This is why we pushed the client to go with a Zehnder system from Flynn Heat Recovery Systems. The owner Maurice Flynn has installed a number of systems for us, including in my own house, and we haven’t had a problem yet, which is great reassurance to us as builders. When it came to design we also had the benefit of the services of Darren O’Gorman of Target Zero who managed to keep the whole MVHR system within the thermal envelope — not an easy thing to do on a dormer house.
Airtightness was the other significant difference between our passive house and the detached house modelled by the department. The Part L compliant house accepted an air permeability of 5m3/hr/m2. This roughly translates to an N50 of 5 air changes per hour (ACH). By contrast the passive house standard requires an onerous maximum air leakage of 0.6 ACH.
Mark Baker of Baker & Co is the only person we will work with when it comes to airtightness. In addition to working with Pat for over twenty years, we have found Mark’s advice and experience crucial in getting down below 1.0 ACH on several projects now, while his supply-andfit price is always the same as it would cost us to buy the materials. On this project Mark’s tender price worked out at one per cent of the total build cost, which the client accepted as a marginal extra expense.
Still, we found that during construction achieving the required levels of airtightness was not easy, and the cost of works was harder to quantify beyond the cost of the airtight barriers. Any good builder practices attention to detail, but getting down to 0.6 requires you to take this to a whole new level. Pat spent an inordinate amount of time with trades discussing the details required for complex junctions. Every service penetration to the house had to be identified and planned for. It was harder to timetable the trades at first fix while preserving the integrity of the airtight layer. The trades required far more supervision and support than normal. This ensured that when we came to the final test, there was no problem in reaching 0.6 ACH.
Still all of this represents a cost to the client that many could argue is not there when the air permeability allowed is 5m3/hr/m2. It should be borne in mind, however, that there is a consequence for this level of air permeability. When I entered 5m3/hr/m2 into PHPP the projected heating bills of the client more than tripled, going from €400 a year in oil to €1,400. So the counter-argument could be made that by sticking to 5m3/hr/m2, you’re paying for an Arated house but in reality you’re getting mediocre energy performance.
Another extra expense we incurred related to the requirement for renewables under Part L of the building regulations. Under the new Building Control Act, the local authority requires a Part L compliance report at commencement stage. This involved Mark Shirley of 2eva.ie modelling the house in Deap to evaluate it for compliance. As this was a passive house which worked in PHPP, I didn’t foresee any problems in Deap. I was wrong.
Mark’s evaluation showed that while it passed the energy reduction requirement with ease, comfortably achieving an A2 rating, it failed to comply with the carbon reduction requirement. The house did have an oil boiler but it also had 40 solar tubes, which we assumed was enough to meet the 10kwh/m2/yr target for renewables. The reason for this failure, Mark explained to me, was that the house was simply too energy efficient. Due to this, there wasn’t enough demand for the solar to satisfy the 10kwh/m2/yr target.
Mark presented us with three options: make the house less energy efficient to increasing heating demand, add solar photovoltaic panels, or ask Kildare County Council to use their discretion in the matter. We went for the third option at first, but got no response.
It certainly didn’t make sense to us, the client, or Mark Shirley to make a house less energy efficient in order to achieve Part L compliance. Did this not go against everything Part L was put there to achieve? PV came in too expensive, but working closely with Mark we found that an additional 80 solar thermal tubes (a total of 120 solar tubes) was the most costeffective solution for compliance.
It was still an extra unnecessary expense of approximately €2000. Other clients could easily have opted for higher fuel bills to save that few thousand during construction. My fear is that this is exactly what will happen if this issue is not addressed.
In the end, the house we built fulfilled passive house requirements without any significant difference in costs to one that was merely Part L compliant. In fact, I estimate a house built to the department’s Part L spec would have cost €310,000, whereas built to the passive house standard, this house came in at €290,000. And in terms of running costs, health and comfort levels it is worlds apart from a house that has only ticked the appropriate boxes in Deap. The biggest obstacle to building a passive house is no longer cost – our own building regulations now put standard building costs around the same as passive house – but lack of awareness.
We were aware of the cost-effectiveness of using alternative building methods to those suggested by the department’s guidelines, and of the value of the passive house approach as better building practice. The problem is we’re in the minority. My big fear as we move forward is that unquestioning conformity to common practice and Part L requirements will lead to a major lost opportunity — where houses are built for the same budget as a passive house, but without any of the benefits.
Selected project details
Architect: DH Architectural
Contractor: Pat Doran Construction
M&E engineer: Target Zero
Civil & structural engineer: Tanner Structural Designs
Energy consultant & airtightness testing: 2eva.ie
Mechanical contractor: Seamus Byrne Heating & Plumbing
EPS insulation & passive slab supply: Airpacks
Insulated sills: Passive Sills
Roof insulation: Baker & Co
Electrical contractor: Erne Electrical
Airtightness products: Siga
Passive slab design: Viking House
Windows & doors: Munster Joinery
Bi-fold doors: Lakeside Windows
Roof window: Velux, via Chadwicks
Oil boiler: Grant Engineering, via Chadwicks
Solar collectors: Joule, via Chadwicks
MVHR system: Versatile
MVHR contractor: Flynn Heat Recovery
First fix carpentry & roofing: Christy McMahon Carpentry
Second fix carpentry & stairs: David McDonnell Carpentry
Additional info
Building type: 250 square metre detached dormer masonry built house
Location: Ballymore Eustace, Co. Kildare
Completion date: April, 2015
Budget: €290,000
Passive house certification: not certified
Space heating demand (PHPP): 18 kWh/m2/yr
Heat load (PHPP): 10 W/m2
Primary energy demand (PHPP): 75 kWh/m2/yr
Airtightness: 0.61 ACH at 50 Pa
Energy performance coefficient (EPC): 0.334
Carbon performance coefficient (CPC): 0.355
BER: A2 (47.27 kWh/m2/yr)
Thermal bridging: Viking Passive Slab L-shaped profile connecting 300mm EPS beneath the floor with 250mm EPS on the walls externally, windows fitted externally to the face of block and sitting on EPS Passive sills, 90mm window frames wrapped in EPS, 180mm Metac at wall plate connecting 250mm EPS on walls to 320mm Metac between rafters. Y-value based on PHPP defaults.
Ground floor: Viking House passive slab insulated foundation with 300mm EPS. U-value: 0.9 W/m2K
Walls: Acrylic render externally on 250mm Kore External EPS insulation, on 215mm block on the flat, on sand & cement render internally with skim coat finish. U-value: 0.12 W/m2K
Sloped ceiling: Quinn roof tiles externally on 50x35 battens/counter battens, followed underneath by Pro Clima Solitex breathable roofing underlay, 320mm rafters fully filled with Isover Ireland Metac mineral wool, Siga Majpell airtightness membrane stapled to underside of rafters internally, 50mm service cavity insulated with Metac, 12.5mm plasterboard ceiling. U-value: 0.11 W/m2K
Flat Ceiling: Quinn Rooftiles externally on 50x35 battens/counter battens, followed underneath by Solitex breathable roofing underlay, 400mm fibreglass above the ceiling joists, 200mm fibreglass between the joists, Siga Majpell airtight membrane stapled to underside of joists internally, uninsulated 25mm service cavity, 12.5mm plasterboard ceiling. U-value: 0.08 W/m2K
Windows: Munster Joinery Passiv uPVC Passive House Institute Certified triple-glazed windows, with argon filling and an overall U-value of 0.85 W/m2K. Reynaer’s Aluminium bi-fold door, triple-glazed with argon filling and an overall U-value of 1.0 W/m2K.
Roof window: Velux MK06 triple-glazed roof window. U-value: 1.0 Wm2K
Heating system: 92% efficient Grant Vortex condensing oil boiler supplying seven radiators and 850 litre Viessmann buffer tank, plus 120 Joule Acapella solar vacuum tubes supplying separate buffer tank
Ventilation: Zehnder Comfoair 350 heat recovery ventilation system — Passive House Institute certified to have heat recovery rate of 84%
Image gallery
https://mail.passive.ie/magazine/new-build/the-builder-s-view-why-passive-house-doesn-t-cost-extra#sigProId793f5858ca