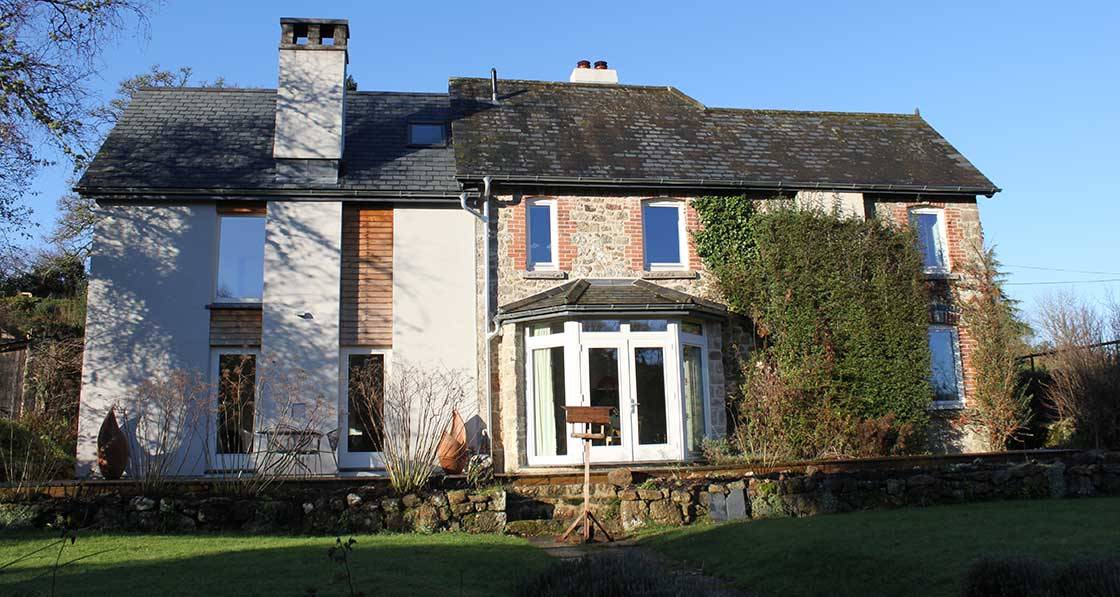
- Upgrade
- Posted
Granite-hewn Victorian home upgraded to PHI low energy standard
Built in 1850, this home in Dartmoor national park would have relied on local timber supplies for heating until the advent of widely-available central heating. One passive house-flavoured retrofit later, it’s back to its wood-burning roots – only this time with much less wood use, and much higher comfort.
Click here for project specs and suppliers
Building type: 246 sqm Victorian detached house
Location: Dartmoor, Devon
Budget: £200,000
Standard: PHI low energy building
£200/yr Estimated heating costs – though the house is mainly heated by client’s own free timber
So you’ve got an irregular-shaped stone-walled Victorian house, subject to the strict planning criteria of a national park – with the added complication of a protected bat colony in the roof.
Sited on the north-facing side of a frosty and often-foggy valley, with a client who does not want to be bothered with certification – and a builder who had never tackled a passive house contract before.
If you wanted to end up with a passive house certified home, perhaps you wouldn’t start from here? Well, the beauty of passive house is you can start from anywhere, and still end up with a warm, comfortable home with dramatically reduced energy consumption.
And so it has proved with the retrofit of this large detached house taken on by architects Gale & Snowden and contractor Building Devon, with the brief to completely overhaul the fabric and services and add a two-storey extension. And the house is now certified as a ‘PHI low energy building’ (in fact it was the first to be certified to this standard in the UK).
Located near Chagford on the edge of Dartmoor, with spectacular views towards Castle Drogo and the rolling hills of Devon, the main part of the house dates back to the 1800s, complete with 500mm solid granite exterior walls. There was also a 1990s extension, built with the standard block cavity construction of the time.
The house was one of a long line of retrofits the client had carried out. He had always been interested in the sustainability of these projects, and in 2010, for this retrofit, he enlisted the help of Gale & Snowden Architects.
At that point Gale & Snowden themselves were relatively new to passive house, but one of their first passive house projects, the 18-flat development at Knights Place in Exeter, was on site, so the architects took the client for a visit.
As project architect Tomas Gartner recalls: “We explained the principles of what we were doing there and the client was very interested in achieving the building and comfort standards, though at that stage he did not want to go for certification.”
Gale & Snowden carried out the design as you would for a certified retrofit – modelling the fabric heat loss in PHPP, prioritising airtightness, carrying out thermal bridge analysis, and specifying heat recovery ventilation.
“The client was on board with how passive house works, that it is all based on physics, and he was really comfortable with numbers, so PHPP was useful to communicate about the implications of different choices and decisions, and we were able to keep him in the loop where we were moving towards or away from the Enerphit level performance, so he could be involved easily in all the decisions.”
1 The existing walls before the upgrade work — the depth of the eaves allowed for external wall insulation over the existing rendered walls; 2 new Viking 3E triple-glazed aluclad windows; 3 600mm EPS insulation over joists at ceiling level, and airtight taping around attic hatch; 4 An existing load bearing wall was clad with 100mm EPS on both sides to reduce thermal bridging; 5 solid stone wall externally followed inside by mineral fibre insulation and vapour control layer; 6 the existing rendered walls were externally insulated, but this was not permitted on the visible granite walls.
Design
The house was not in bad condition structurally, but with its uninsulated stone walls and 20-year-old oil-fired heating system, it was ripe for an upgrade.
The location in the Dartmoor National Park – with a 100-page design guide to follow – obviously added constraints to the project.
Luckily the team were able to find triple glazed timber windows that the national park planners were happy with, and that weren’t too expensive. Unsurprisingly, external insulation was not permitted on the visible granite walls, meaning internal insulation had to be used quite extensively.
“For the internal insulation we used mostly mineral fibre insulation (150mm packed into timber studwork). Upstairs, where the rooms are quite small, the client opted to use Aerogel in order not to lose space – the Aerogel saved around 100mm,” Gartner says.
There were in theory two options for wall airtightness, outside and inside. One possibility was to repair the granite walls, and make the masonry and the rendered sections continuous with the slab and the airtight layer in the roof. The alternative was to go inside. Although this second option might appear more disruptive, as the team needed to cut back floors and ceilings to ensure continuity, “it meant that the airtightness and vapour control layers are the same, so no warm moist air can get behind the insulation to meet the cold masonry, which with internal insulation I think is very important,” Gartner says. He also notes that achieving airtightness in a rubblecored traditional stone wall might have been quite tricky.
The new extension and the existing rendered walls were externally insulated with EPS. This delivered lower U-values than the internal insulation (around 0.13 W/m2K, as opposed to 0.2 W/m2K), thus improving the overall energy performance.
Build
When contractor Building Devon were taken on for this project, they had never worked on a passive house project before. But Tomas Gartner says they did “an incredible job, really meticulous.” Gale & Snowden have since worked with them on two more builds.
Barry Webb from Building Devon found the passive house approach made sense immediately.
“What we liked about passive house was the attention to detail when it comes to making a building airtight and thermally efficient. Once you understand the concept you forever see ways air can get into the building, and stopping it almost becomes an obsession. This level of construction is well above the current building regs and just makes sense if you want to conserve energy.”
They also appreciated the sound basis in science and mathematics: “We found it very interesting that the knowledge and computer modelling is able to determine the building’s efficiency, and if insulation is reduced in one area it can be increased in another to offset. This is especially important on a retrofit where space can be limited.”
In turn, Building Devon used their practical understanding of what works in construction to make a number of valuable suggestions, Tomas Gartner says. “What I particularly like about Building Devon is their intelligent approach to sequencing.”
“They are always looking ahead to the next step. For example, we had proposed a taped membrane for the ceiling airtightness layer, but they pointed out that by using OSB instead, this could be taped from above – the site crew would have a platform to work straight onto, making it much easier to deliver excellent airtightness.
“It’s always worth being open to contractors’ suggestions: the contractor will always have something to bring.”
Services
Hot water comes from a large thermal store heated primarily by solar thermal collectors, with back-up from an immersion heater.
The client was a great fan of wood stoves, and wanted to install not one but three, to make use of their own timber supply. One stove was installed as the main source of space heat in the central open hallway. A second stove went into the living room, then a wood-fired range cooker in the kitchen diner.
“A stove in the kitchen is potentially tricky because the room is under extract, so you have to be extremely careful that there is no chance of CO contamination,” Gartner says.
“However we found an Austrian model that is airtight enough to use in a passive house, and of course also installed carbon monoxide alarms as required in the regs.”
The wood stoves are supplemented by three electric towel rails. For the purposes of primary energy calculations the team and certifier between them settled on the prediction of an 80:20 split in favour of wood. The client estimates that the electric heating gets used less than this – although as the wood isn’t purchased, there aren’t records as such.
Heat load & climate
Chagford’s nearest weather station is only 30 miles away in Exeter. However Exeter’s climate is very different from Chagford’s: it is close to the sea in a sheltered south-facing valley, where it rarely drops below 5C.
Chagford by contrast is on the north-facing side of the high Teign valley, prone to frost and, not infrequently, fog. “The house is in a spectacular location, the views are amazing – however, the orientation of the site means the daily window for solar gain is shorter,” Gartner says.
“In order to get the best possible predictions, we did try to get more local weather data to input into the calculations, but nothing was available in the right format. Instead we used the Exeter data, adjusted for elevation.
“In these kind of locations we always exercise caution, and oversize the heating system a bit compared to the predicted load in PHPP: we’ve completed a number of passive houses in Devon now, and so far they’ve all been comfortable and the energy use has been within predictions.”
WUFI
Although the client was not interested in certification at the time, around five years later, when they decided to sell, they decided a third-party-accredited standard offering quality assurance would be useful to demonstrate to prospective buyers the quality of what they were buying – so Gale & Snowden went back to the project to organise certification.
This article was originally published in issue 24 of Passive House Plus magazine. Want immediate access to all back issues and exclusive extra content? Click here to subscribe for as little as €10, or click here to receive the next issue free of charge
The certification process flagged up the need for dynamic moisture analysis.
As Tomas Gartner explains: “When I did my passive house training in 2009 – not long before we began this project – there was no mention of hygrothermal calculations.” There is also no statutory requirement to carry out dynamic hygrothermal calculations when specifying internal wall insulation, though the current standards are under review.
Instead, the team looked at the moisture safety of the build-ups using Glaser steady state condensation risk analysis, trying to be as rigorous as possible – including asking the manufacturers of the insulation and membranes to supply their calculations.
“As certification didn’t happen until after the build was complete, we couldn’t really go back to the manufacturers and ask them to supply Wufi calculations for us,” Gartner points out. “But as the client was keen to go ahead with certification, he employed Joseph Little at Building Life Consultancy to do it.”
The biggest issue when carrying out Wufi calculations is often getting the right material property data to input. While some materials are quite well characterised and consistent – fired blocks for example, the specific hygrothermal properties of the materials in a traditional building using natural stone from a local quarry are a lot less clear. Yet relatively small differences can make a significant difference to the predicted performance.
The Dartmoor granite this house was built from turned out to be quite unlike the hard, impermeable type of granite that you would find in northern Britain and Scandinavia; called “Chagford gold”, it is softer and more porous with a relatively high lime content.
Once you understand the concept of airtightness you forever see ways air can get into the building, and stopping it almost becomes an obsession.
Building Life Consultancy reviewed the available technical literature and compared it with materials from the Wufi database, in order to arrive at the closest possible data match to input for the calculations.
The porous nature of the stone means that driving rain will penetrate more deeply, but it also makes the wall more forgiving of temporary condensation, Gartner says, so in the end it turns out to be beneficial as the masonry is better able to regulate moisture.
Happily, all the build-ups passed the assessment. Although of the materials used internally the mineral wool is the more vapour open, perhaps counter-intuitively in the dynamic calculations the Aerogel – which is quite hydrophobic but still vapouropen – was the further into the safe zone of the two (of course mineral wool is a great deal cheaper).
Bats
Early investigations of the roof revealed a very thick layer of bat droppings – and as bats are a protected species, this determined the decision to insulate and make the roof airtight at ceiling level, leaving the bats free to come and go as before – though now through dedicated bat access points rather than just cracks and gaps.
As Barry Webb recalls, they had to allow the bats to come and go through their original entry points under the eaves by creating slots in the wall and roof insulation, which they lined with roofing felt. “Essentially, there are built in cold bridges to satisfy and preserve the bat colony!” he says.
None of this could be done while the bats were at home; as it is a winter roost, work on the roof had to wait until the colony had moved out for the summer. Webb adds that: “the client was concerned about the bat effluent, which is very smelly, permanently soiling the insulation, so a layer of plastic sheeting was laid over the top and large plastic containers with cat litter placed under their roosts.” An airtight loft access hatch was installed, which gives access to the roof space for any maintenance requirements, and to clean up after the co-residents!
Certification
Gale & Snowden’s design had originally aimed for the Enerphit target. However between the build and the decision to certify, south-west England was reclassified from a ‘cold temperate’ to ‘warm temperate’ climate by the Passive House Institute, making the energy target for Enerphit more demanding (requiring a maximum annual heat demand of 20, not 25 kWh/m2/yr, to qualify).
Because Enerphit was no longer an option, the house became the first in the UK to be certified to the then-new PHI low energy building standard.
To qualify, a building must achieve a high level of energy efficiency and a high degree of user satisfaction, as well as protection against condensation damage, as with the passive house and Enerphit standards, with an annual space heat demand at or below 30 kWh/m2/yr, airtightness at or below one air change per hour, and a primary energy demand (renewable) of below 75 kWh/m2/yr.
Since this early passive house project Gale & Snowden have gone on to embrace the standard and they now specialise in passive house, and Building Devon too have gone on to carry out new builds and conversions to passive house standards. Barry Webb says they learned a lot from this first project – not least about the inferior way almost all other houses are built and refurbished.
“When building to passive house standards you learn a lot, and realise there is a whole other way of building and with the numerous advances in materials a building can be so much more than a leaky, cold, inefficient dwelling. It makes you realise that the building industry is years behind in this country and needs a serious shake up.
“We have gained an enormous amount of knowledge on how to improve the work we do, and are able to put that knowledge into action on all our projects, and hopefully help the future of our planet and the environment around us.”
Selected project details
Architect: Gale & Snowden
Civil & structural engineer: Barry Honeysett
Main contractor: Building Devon
Airtightness testing: JSD Air & Acoustic Testing
External insulation: SAS
Internal wall insulation: Rockwool
Additional wall insulation: Aerogel
Roof insulation: Jablite / Knauf
Airtightness products: Ecological Building Systems
Windows & doors: Viking, via Ecomerchant
Solar thermal: Megaflo
Heat recovery ventilation: Zehnder, via Aereco
Chimney system: Schiedel
In detail
Building type: 1850 Victorian detached house. 246 sqm treated floor area.
Location: Dartmoor, Devon
Budget: £225,000
Space heating demand (PHPP): 30 kWh/m2/yr (certified PHI low energy building)
Heat load (PHPP): 15 W/m2
Overheating (PHPP): 0%
Primary energy demand (PHPP): 104 kWh/m2/yr
Energy performance certificate (EPC): A 93
Heating costs: Estimated at under £200 per year. Based on 20% (6 kWh/m2/yr) of the building’s calculated space heating demand provided by three electric towel rails, assuming a price per unit of £0.13p. The client’s own free wood supply provides the balance.
Airtightness (at 50 Pascals): 0.7 air changes per hour
ORIGINAL WALLS
Before:
Solid granite stone wall. 1960’s concrete cavity wall with 50mm EPS insulation.
After:
Wall type A: Solid stone wall externally followed inside by 100mm mineral fibre insulation, vapour control layer, service void with 50mm mineral fibre insulation, plasterboard and skim. U-value: 0.224 W/m2K
Wall type B: Solid stone wall followed inside by 54mm aerogel insulation, VCL, OSB board, plasterboard and skim. U-value: 0.215 W/m2K Wall type C: 6mm render externally followed inside by 250mm Neopor insulation, concrete cavity wall with 50mm EPS insulation, plaster. U-value: 0.109 W/m2K
EXTENSION WALLS
Wall Type E: 6mm render externally, followed inside by 250mm Neopor insulation, concrete blocks laid on flat, plaster. U-value: 0.130 W/m2K
Wall Type F: 22mm cedar cladding externally, followed inside by 38mm ventilated void, weather membrane, 250mm mineral fibre insulation, 100mm concrete block, plaster. U-value: 0.137 W/m2K
EXISTING ROOF
Before:
Uninsulated cold roof with slate finish. After:
Insulation at ceiling level: 600mm EPS, OSB board, mineral fibre between existing joists, plasterboard and skim/plaster and lath.
Extension roof: I-joist timber roof with mineral fibre insulation: local slates externally on 38/25 battens/counter battens, followed underneath by breathable roofing underlay, 365mm timber I-joists fully filled with mineral fibre insulation, 12mm taped & sealed Medite Smartply OSB, 38mm insulated service cavity, 12.5mm plasterboard and skim ceiling. U-value: 0.11 W/m2K
WINDOWS & DOORS
Before:
Single glazed, timber windows and doors. Overall approximate U-value: 3.50 W/m2K
After and extension:
New Viking 3E triple glazed, aluclad windows and doors: Average overall U-value of 0.95 W/m2K
Roof windows: Velux triple glazed roof windows. Overall U-value: 1.0 W/m2K
HEATING SYSTEM
Before:
20 year old oil boiler & radiators throughout entire building. After:
RIKA Vitra (with externally insulated Schiedel Isokern pumice chimney system in extension), Nester Martin, and Lohberger woodburning stoves, MEGAflo solar thermal system including 2.34 sqm flat plate array and thermal store.
VENTILATION
Before:
No ventilation system. Reliant on infiltration, chimney and opening of windows for air changes. After:
Zehnder ComfoAir 350 — Passive House Institute certified to have heat recovery rate of 83%.
Green materials: Local slate and timber, natural paints and pure solid hard oils, no PVC, all timber furniture from FSC certified sources.
Image gallery
-
Extenstion window cill Extenstion window cill
-
Extension window jamb Extension window jamb
-
Cavity wall GF junction Cavity wall GF junction
-
Ceiling junction at gable Ceiling junction at gable
-
Existing EWI window cill junction Existing EWI window cill junction
-
Existing intermediate floor detail Existing intermediate floor detail
-
Existing 1st floor EWI eaves junction Existing 1st floor EWI eaves junction
-
Existing 1st floor IWI ceiling junction Existing 1st floor IWI ceiling junction
-
Existing 1st floor eaves junction Existing 1st floor eaves junction
-
Existing EWI eaves details Existing EWI eaves details
-
Existing EWI window head detail Existing EWI window head detail
-
Existing IWI GF junction Existing IWI GF junction
-
Existing IWI window head and intermediate floor junction Existing IWI window head and intermediate floor junction
-
Existing IWI window cill junction Existing IWI window cill junction
-
Existing IWI window jamb Existing IWI window jamb
-
Existing internal wall GF junction Existing internal wall GF junction
-
Existing internal wall roof junction Existing internal wall roof junction
-
Existing junction between EWI and IWI at internal wall Existing junction between EWI and IWI at internal wall
-
Existing floor to new floor insulation Existing floor to new floor insulation
-
Exension abutment detail Exension abutment detail
-
Extension base of timber cladding on 140mm block Extension base of timber cladding on 140mm block
-
Extension door threshold detail Extension door threshold detail
-
Extension EWI and timber cladding junction Extension EWI and timber cladding junction
-
Extension eaves detail Extension eaves detail
-
Extension ground floor junction Extension ground floor junction
-
Extension ridge detail Extension ridge detail
-
Extension roof light Extension roof light
-
Extension roof trussed penetration detail Extension roof trussed penetration detail
-
Extension verge detail Extension verge detail
-
Extension window head FF Extension window head FF
-
Extension electric boxes Extension electric boxes
-
Extension timver cladding window head and threshold Extension timver cladding window head and threshold
-
First floor wall types First floor wall types
-
Ground floor plan wall types Ground floor plan wall types
-
Lean to eaves junction Lean to eaves junction
-
Lean to ridge detail Lean to ridge detail
-
Proposal Proposal
https://mail.passive.ie/magazine/upgrade/granite-hewn-victorian-home-upgraded-to-phi-low-energy-standard#sigProIdb4e99330cf