- Design Approaches
- Posted
Navan Credit Union
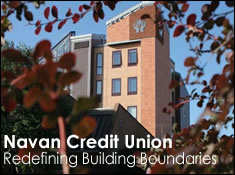
The growing ambition of sustainable building in Ireland has never been more thoroughly embodied than in the recently completed St Mary’s Credit Union, Navan, Co. Meath.
Central to the building’s design, engineering and construction is an approach that is holistic in the truest sense, driven by architects Gaia Ecotecture’s belief that the building—linked to the original credit union built by the firm in the late 1980s—should act as a living structure; its elements interacting dependant on the needs of the building’s users and the challenges and benefits thrown up by shifting weather conditions and natural resources.
The attention to detail inherent in this holism has created a building that is innovative in so many regards that focusing on any one aspect of the building—such as the fact that this is Ireland’s first 5-storey timber frame building—would do the building as a whole an injustice. In recognition of this fact, the building has been selected amongst a handful of cutting edge projects around the world for presentation at the World Sustainable Building Conference in Tokyo.
Embodied Energy and Lifecycle Analysis
We’re blessed with an excellent client—an articulate and careful management team from the board, to the executive, to the building committee, to the general manager. They had put their trust in us in the late 80s, and we’re very pleased that they came back to us. As an owner-occupier to the building, they were open to the persuasive argument of prolonging life to first replacement, keeping down the use of external energy sources such as grid electricity and gas, and investing in energy producing devices such as double wall and box windows, photovoltaics and solar thermal. The payback period on these devices is fully justified commercially speaking through lifecycle analysis when you have an owner-occupier. A pernicious problem is that developers, who “lash the thing up”, sell it quickly, and turn their money over, couldn’t care less, and the unfortunate tenant is left with low performance fabric, which if they have a repairing lease, rapidly becomes an ‘albatross’ that they have to pay for. We were in the position here that the owner-occupier is responsible for the maintenance costs, and there are excellent studies by our own cost managers Gardiner and Theobold, et al which show that the life cycle running cost of a building greatly exceeds its first capital cost, with conventional building. The cost to the organisation is minimised by intelligent investment in quality.
The fact that we now apparently need four planets to maintain our profligate life style means that if you’re conscientised about your children or your children’s children, you have got to move towards making buildings on the Factor 10 principle—that we use less of everything, much more efficiently. Factor 10 is by no means out of the question. If you look in ‘Green Design; Sustainable Building for Ireland’ you’ll see that locally produced air dried softwood has embodied energy of about 110, on a scale where aluminium is in the region of 75,600, KwHrs / cubic metre and concrete products based on conventional Ordinary Portland Cement and steel (103,000) are up there in the mega numbers. We’re dealing here with step changes in building culture. If we accept the word of the UN Environmental Programme team in their annually updated GEO 2000 reports we need to change. This Credit Union building goes as far as possible, in a streetwise and alchemically alert way to bring down embodied energy. It’s not fundamentalist—where we need steel we use steel. We’ve used a ‘filigree’ of galvanised steel, with zinc cladding elsewhere in the building with flashings and so forth where it is appropriate. Those relatively small volume materials carry an embodied energy burden, but they’re applied intelligently, to do the task for which they are best suited. The vast bulk and mass of the building is timber, and this timber is in fact protected by the high embodied energy materials on its external face.
View of the clay and steel clad south west facade of Navan Credit Union—a high embodied energy cladding specified with durability in Irish weather conditions in mind
5 Storey + Roof Timber Frame
Years of research have gone into this timber structure. We trawled Europe and North America for the most advanced timber technology. We’ve gone to see the leading people in Austria , Germany , Switzerland , and Scandinavia , and to cut a very long story short, Projekt-Holzbau Merkle in South Germany had previously earned their credentials with a colleague of ours in GAIA International, Joachim Eble. With their engineers, Pirmin Jung, we worked through a design process within the terms of Eurocode 5, BS 5268 and the German DIN standards amongst others to develop the design. The key point of the structure over five stories, of course, turns on the connections. The delightful engineering involves tiny amounts of steel used to form the connections, but this steel is totally submerged within timber, so that the timber itself is acting as an insulant to the thermally vulnerable steel, in terms of fire protection. The building is being presented at the Garmisch conference later this year by Pirmin Jung, and there is great interest in the building. We devised the basic structural scheme but great credit must go to Pirmin Jung’s team for detailed analysis and shop drawings.
The lift shaft itself is engineered in timber. There was a proposal to use concrete which we discounted. In other projects where concrete and timber have been used together with less than total success because they are two disparate materials. They behave entirely differently, and if they’re used in conjunction it can cause great problems with settlement, expansion and contraction.
The staircases have been attractively designed to encourage use in lieu of lift for healthy exercise and reduced energy use
The timber engineering aspects need to be treated with great caution. Every building of this kind must be closely engineered. The fire safety aspects, moisture content, density and stress grading required engineering of a very high calibre from Jurg Stauffer of Pirmin Jung’s office, working in close collaboration with the architects. Readers of this article cannot take it that they can, in cavalier fashion, build to five stories. This building is a hybrid between a frame structure and a skin or panellised structure. The wall panels came complete with sealed insulation, preformed windows and so forth to infill around a skeletal frame. It’s a hybrid interaction between frame and skin, rather like the bones, cartilage and ligature of our own bodies. We’re not just skeletons—we work with a tenuity of skin and tissue, and this building is rather similar in its concept to that. An additional key point is racking (lateral) stability and strength. In certain very extreme weather conditions—the ‘Clonee tornado’ or the recent ‘Katrina’ hurricane, are cases in point—there can be negative uplift forces on the substructure. So there are holding down bolts at certain points to literally hold the building onto the substructure. The dead load of course is much lighter than a conventional concrete structure, thereby significantly reducing substructure, which in this case consists of continuous fluidised augered piles.
This article was originally published in Vol 2, Issue 11 of Construct Ireland magazine. Want immediate access to all back issues of Passive House Plus and exclusive extra content? Click here to subscribe for as little as €10, or click here to receive the next issue free of charge
Projeckt Holzbau- Merkle used the Brettstapel system, with beech dowels at 8% moisture content being inserted, under pressure, through slightly smaller drillings, in the pine laminae, typically at 12% moisture content. In this system, as the moisture contents equalise, the hardwood dowel expands and the softwood shrinks, becoming an integral solid timber construction, with attractive fire safety characteristics, while retaining very low embodied energy. This component is manufactured to a quality control level which allows it to be used directly as a finish, eliminating other materials.
A Kerto stressed skin was also used, a highly engineered timber product that uses minimal amounts of glues but in a very strategic way. It’s basically what the North Americans call laminated veneer lumber (LVL). This is such a huge subject that we’re skimming over here. The use of OSB plywoods, Glulam, Kerto, Steicoflex wood-fibre insulation rather than petrochemical derived insulation—It’s all of a piece.
We would recommend the use of Pirmin Jung’s office. We’ve found them to be among the best consulting engineers we’ve ever had contact with. I say that based on my own experience as an engineer. When I come across really subtle, nuanced engineering I recognise it and the degree of detail they went into was astounding. Every single junction in this structure was modelled in 3 dimensions. The statics and detail stress analysis were of a very high order, and the interlock between Pirmin Jung’s office and Projekt Holzbau Merkle was exemplary. It’s something that has been lost in the building industry. There’s too much of a divide between consultant and ‘on the shop floor’ know-how. In this case, literally, the CAD drawings became the automated cutting software for the components. Due to the fact that Projekt Holzbau Merkle and Pirmin Jung have built up a rapport, we reaped the harvest of a collegiate approach between them. There’s two much of a schism between consulting engineering and actual fabrication. It’s not a culture as it was in the past- Peter Rice comes to mind as a wonderful example.
Fire safety
The building is a 20 metre cubic building, but we previously managed to prove that a 30 metre timber building was structurally feasible and fire safe. We base that assertion on the authority of Professor Mario Fontana at ETH University in Zurich whom we visited and consulted; if we were using a misting sprinkler system and the same technology we used in the current building, with further enhanced fire safety measures, it would be safe and technically possible to make such a building. We have all been appalled by the detail of the twin tower collapse, where the floor detail in fire proved so perniciously dangerous, causing progressive collapses to the towers.
Workers fit timber floor panels on the building’s 3rd floor
Scaffolding on the timber structure lends perspective to the sheer scale of Ireland’s tallest timber frame building
Timber needs to be respected. The great square riggers took people around the world through hurricanes, and didn’t break up for the greater part. Our own intuitive guideline is that if the building is no higher than trees, then nature has already proven the integrity of tree structures! The fire aspect in particular here is a credit to the fire officers concerned. Meath County Council have engineers in their fire department and we found on the earliest consultations, on the superceded 30 metre tower scheme, down to the final fire certificate for this building that we relied on their engineering approach and professionalism of the fire service. They did not ‘throw a rule book’ at us but of course were fully cognisant of the legislation and best practice. We examined the whole building from first principles and in this respect we were very well served by Howard Morgan of International Fire Consultants (ex BRE). He provided a crucial study for the whole building, in terms of the smoke reservoir.
The use of a two staircase approach, the use of smoke venting in a very controlled way in the hands of the fire chief are key . The caveat here is that readers may not take it without question that a five-storey timber building is fire safe. There are many cautionary tales within the literature, from Julius Natterer’s work and others, where the greatest caution must be applied to timber. The size of cross section of timbers available to flame is a key matter. Small scantling sizes are highly vulnerable. Dense timber, designed with appropriate charring rates and with strategic application of spread of flame, non-toxic coatings—all these are key to ensuring a robust fire-safe building. The building uses layers of sacrificial timber, which is a commonplace of timber engineering. Most structural engineers in Ireland don’t like timber because the calculations are much more difficult. The material you’re working with is highly variable, from heartwood to sapwood, and various elaborate stress gradings. There are only one or two engineers in the country who would really have close expertise. It takes time and dedication to become really committed and skilful in this area. Ozelton and Baird’s Timber Designer’s Manual is a key reference for engineers who would like to bring this further.
In Enterprise Ireland there is a very good engineer, Bill Robinson, who was involved in the testing of connections for round-pole structures; give place name here. Bill helped us in early research and contacts on this project. The expertise is in the country, but the cultural confidence to use it generally is not yet there. We are hoping that this middle Europe import will help to stimulate interest in displacing very high embodied energy concrete and steel structures, despite the intimidating concrete lobby in this country. Entrenched commercial interest and entrenched professions are militating against innovation and against widespread uptake of environmentally sound techniques. Unless we break through these barriers and show the way in terms of there being good business opportunities in innovation, we will forever be luddite, and trailing the field in this area, internationally.
The stainless steel structure of the Venturi roof ventilator being lifted onto the building
The exterior
It irks me to see Irish architects using softwood cladding in a new ‘green wash’ or gift wrapping public relations exercise around very conventional structures. The concrete or steel is on the inside and it comes wrapped in a softwood cladding that will rot in very short order, because the detailing of most of these claddings is appallingly bad, which may falsely discredit timber building. We know enough about the driving rain index in Ireland and the very high relative humidity, coupled with at other times punishing extremes of intense sunlight and several weeks of drought in summer, to know that the external skin of this building was avowedly to be long-lived to first replacement, and mineral in nature to protect the softer organic material within. So The substance of this building is organic in nature but the skin is a high embodied energy, very thin, with high quality-assurance cladding, which is where the egg analogy comes in. Every hen produces a superb defence to its egg , as Brunelleschi intuited at his breakfast table for his dome! In this case the Moeding tile, which was in fact invented by Thomas Herzog architect is 30mm in overall thickness, with a cavity. The amount of highly fired clay in the tile is very small. We used this rain screen cladding technology, and all credit to SJW facades’ Shay Wheelock and Brendan Doris for understanding and applying the technology well . We went to the Moeding works: we had an excellent visit with them. They rose to the challenge of this building, particularly in terms of multiple colours and textures. They were very design sensitive. We have really enjoyed working with this highly fired, clay based material.
This interlinks with zinc cladding and the hydroelectrically derived aluminium, as much as possible. Then you come to what we see as highly technical glazing that will stand up to storm from Pensher-Skytech who do a lot of work in the middle east for blast resistance and so forth. Their heavy duty glazing bars with several lines of defence, high end glazing specification and so forth, does carry a high embodied energy burden, but it is appropriate because we want the Venturi, the solar chimney, the passive solar east stair ‘prism’ and the link to the existing building, which are all of that nature, to last. By contrast the banking hall screens and box windows are much more protected, and we used a lower embodied energy technology there.
We hope the whole external skin will be there well past our lifetimes, rather than seeing timber cladding being removed after a decade or so, or sixties buildings being taken down in their entirety. That is a scandal, considering that we’ve inherited buildings that are now a quarter of a millennium old and still going strong.
The view looking into the atrium of the completed building reveals timber levels complimented with extensive planting
Glazing strategy
Glass is a very high embodied energy material. It should be used sparingly. The crude but useful rule of thumb is 50% aperture to the south, 30% to the east/west, 10% to the north. Excessive south glazing creates as many problems as it may solve from time to time. With that broad rule of thumb, the south facing glazing is for energy pick-up but it is also for chi flows into the peace garden. The banking hall is a double height space with a timber mezzanine ‘floating’ in the centre of that space, which actually hangs from the floor above. The aesthetic and architectural qualities of glass are exploited fully, we hope, and the use of timber as framing to the glazing is crucially important to keep the embodied energy down. But at the same time we’ve used Scandinavian derived aluminium which is largely from hydropower sources to protect the timber on the external skin, because it would take a punishing from the intense sunlight on the southern facades.
There’s detail on the glass spec including impact resistance over the glazed link, fire control glass within range of vulnerable apertures in the event of fire. There is quite a subtle range of glass types used in the building for energy, safety and aesthetic reasons—not least in the Venturi glazing, which is carefully designed to maximise daylight into the core of the building down through the atrium.
Passive heating measures
The main passive heating measure is to look at the whole building as a passively heated device, through the use of orientation, shading, and percentage aperture for different elevations. Good uptake of solar heat gain in the morning is delivered into the building for the hours of occupation, or in the alternative, shaded or vented if the gains are unwanted.
The major passive solar heating device is the double façade to the banking hall. The orientation is basically square on diagonal—that is one corner of the building is effectively due south. So you have a southeast and southwest banking-hall glazed timber double wall, and then you have a northwest wall. This is tied into the double ‘box’ windows. The winds in this location are predominantly from the southeast or southwest, with virtually no winds of significance from due south north. So there tends to be suction or lower pressure from the northwest façade and positive pressure on SE and SW ; this helps cross ventilation.
The mezzanine floor meeting at the edge of the Banking Hall glazed wall
The passive devices are carried forward into what we call the ‘box’ windows, which are twin skins of window with an interstitial space of about 400mm. Both windows are double-glazed with a high glazing specification, and as with the banking hall walls which are 6 meters high, these ‘box’ windows have a subtle system of trickle ventilation. So in deep winter it’s a ‘lockdown’, using trickle ventilation only. By creating a suction effect within the building of so many Pascals you draw air from the warmed cavity into the building. The ventilation air arrives into the occupied zone pre-heated. Conversely in high summer, the outer glazing is opened at the top, so that all unwanted gains are vented off. The cavity must be purged once you pass the acute cold season and part of the shoulder season, because the passive gain device can become your enemy in high summer. The use of external shading and external purging is crucial to the way these work. Afternoon overheating on southern facades would be a huge problem if these design measures weren’t incorporated, including mechanical external shading doubling with overnight security shutters and deciduous shading of what we call the ‘Abraham screen’ to the Peace Garden—a brise soleil screen with Wisteria climbers. In a short time, this will provide shade in summer, and with loss of leaf, will provide light and heat access in deep winter
Solar water heating
We have a range of Thermomax panels, and here Mark O’Brien of Energy 365 provided services to the consulting engineer, Brian McPhillips with expert subcontractors Eirbyte and Glas. The basic device is evacuated tube which picks up from the steep south-oriented plant room roof, into a calorifier for hot water to lavatories, wash hand basins and the kitchen. Any excess to that requirement goes into the space heating system as a minor pre heat, so that the temperature difference—or Delta T —for the boilers is somewhat reduced.
A close up view reveals the texture of the Moeding clay tiles
Active and auxillary heating measures
We live in an oceanic temperate climate. In a way you can say that in Ireland we have weather rather than climate. I’ve walked in my shirtsleeves in Dublin at Christmas, and I’ve been very cold in mid-summer. We see auxiliary heating and cooling as being exceptional events that are needed to deal with peaks in the weather, of heat or cold. We see the whole technological approach to this building as hybrid in nature rather than fundamentalist. The passive building idea, where there’s no heating or cooling whatever is a counsel of perfection that can sometimes leave clients physically uncomfortable, while the professionals involved may be feeling smug. So the active heating and cooling systems employed both use state of the art technology. We believe in subtle science. In the case of the cooling system, we’re using gas-fired heat pumps of extremely high efficiency. The Coefficient Of Performance in the heat pumps means that the net efficiency in the whole system is 131%.
The heating system is in a banked series of modulating condensing boilers, which are efficient whatever the load, to take full advantage of the load/ efficiency curve. It’s a commonplace, that if you use a boiler at the low end of its load capacity, it is inherently inefficient. So by having three boilers in tandem, as and when you need to service varying demand, you bring them in, in series. The first boiler is brought as quickly as possible to the peak of its efficiency curve, which is up around 93%, and so on. In a clever, controlled regime you keep these three boilers as close to their peak of efficiency as possible. This is a completely natural-gas based system in both cases, which means the primary energy use is highly efficient rather than having road haulage of LPG or electrical grid losses.
We have found from experience that low temperature hot water systems are the best outcome. We’ve tried various different solutions but we believe in oversized radiator surface with lower circulating water temperature and lower water content. We would like to see the same plant and equipment doing both jobs of heating and cooling, but after careful study it was found that it was more appropriate to have separate heating and cooling circuits in this case. For the future, to keep down installed cost, we believe there’s a very great scope for the same plant within the rooms performing both functions, especially using heat pump technology.
There is natural gas available, at a considerable infra-structural cost brought to the town. We see the building, in urbanism terms, as tied into the organism that is the town, and it is sensible to use the grid supply while it is available.
Both the Banking Hall Wall of twin-skinned glazing space at right of view from the West Stairs and the twin skinned 'box' windows are central to the building's intelligent passive heating and ventilation approaches
Electricity
Our mains electricity approach is of course to go to Airtricity for wind energy, from the Arklow bank and so forth. The primary energy consumption from ESB is a multiple of Airtricity current. With Airtricity there is a 90% efficiency, as the only inefficiency you have is from the grid losses. In the case of the ESB plant and equipment, overall it would be of the order of 40% efficient production, which is extremely low, and deteriorating further when you apply the 10% grid loss to that. The sad fact is that you must multiply your grid electricity kilowatt from the ESB by a factor of circa 2.775 to get the real primary energy use. The obvious choice is to use wind if you want to keep your primary energy use down.
We took the decision that we wanted to use the sun to operate devices including the automatic actuators, dampers, fans; in other words, the assisted ventilation and heating requires quite a number of devices, and these could become a demand on grid supply otherwise. With the assistance of Eirbyte, Glas and Energy 365 we have an excellent system of Photovoltaic panels which are coupled into low energy fans, actuators, dampers and vent controls, which significantly reduce the demand on the grid supply and the solar availability is in phase with periods of greatest ventilation need. By having 5-day storage, we have so far managed to have no grid top up whatever to the battery bank in the plant room. We are nuancing and refining the balance between the charge to the batteries and the demand from these actuators, vents and so forth. The back up trickle charge from the grid kicks in at 20% and tops up to 80%.
Photovoltaics(PV) is an evolving technology, the prices are coming down, and the economies of scale are increasing. Both BP—now called Beyond Petroleum—and Shell have invested significantly in PV. At the current state of the art, you can be satisfied that the PV plant and equipment will at least pay for itself over the lifetime of the equipment. In the case of solar thermal, the payback is much shorter. For an owner occupier the life cycle on PV stands up, at current prices, just about, and improving.
The entrenched professions, and the entrenched business world will not change until it is seen to be advantageous to do so, so Beyond Petroleum, having been British Petroleum, is an exemplar. The entreched oil industry has commercially prevented the development of renewable energy until the intellectual echelon within that industry has convinced management that it is the only way to go. Then they want to be ahead of the posse. Their R & D has to anticipate the demise of the Neanderthal (and suggested changes?) technology they’re pushing. The “infernal” combustion engine is one of the least efficient things ever invented. A model-T Ford gave just as many miles per gallon as the current SUVs.
The twin skinned ‘box’ windows are central to the building’s intelligent passive heating and ventilation approaches
BMS system
The Building Management System is by Standard Controls Ltd. We’d like to credit Declan McDonnell and Linda Healy as being extremely helpful, and John Roe, the commissioning engineer. In continuing dialogue with us, they devised a subtly interactive control regime from deep winter, to shoulder, to high summer, which is being empirically refined during the commissioning and test period. It works essentially from a weather station at the apex of the plant room, free and clear of all turbulence and disturbance. From that we get the wind direction and force, shade temperature, humidity, and this informs the ‘brain’ so to speak—the programmable controller—of the whole system. In a ranked series of acts, the banking hall walls inner, outer, upper and lower windows are controlled in a particular way which maximises the solar gain, and avoids overheating. During the course of the day, these various actuators, like fish gills, admit more or less air through the double wall.
The key ventilation devices are the Venturi ventilator and the solar chimney. An interesting result of this project is that the commission and test phase was, if you like, an iteritive ratification of the computational fluid dynamics modelling which Strathclyde University carried out. There were some significant surprises in the way that the actual building needed to be nuanced in control, based on the way these devices actually behave. We believe in a highly empirical commission and test phase, iteritively. This all goes back to one PC, which is controlled by the building superintendent, Michael Cahill and everyone’s going through a learning curve right now. He can literally, in live time, monitor what’s happening and tweak the system accordingly. It’s also monitored/ controlled by modem back at Standard Controls’ headquarters. The control regime has gone through several iterations already and is still in refinement. It’s not until the building has been through all seasons that that control regime will settle down.
It’s crucial that through the commission and test period of not less than one year, the intellectual attention to the system is maintained. We have had good cooperation from Standard Controls and Tim King of King Environmental, where we have actually physically measured velocities, humidity and temperatures through a series of five different test days to augment the probes that are in the BMS. There are probes throughout the building measuring the various parameters, with the data taken back to the programmable controller for an appropriate response. We’re measuring all the active and auxiliary passive devices in kilowatt hours and our target is to know at the end of the monitoring period the precise kilowatt hours per square metre per annum, whether active or passive—whether coming from PV or solar thermal or from the two grid supplies of wind electricity or natural gas. The target is 50kwh per m2 per annum, and we’ve been through high summer auxiliary cooling, staying within our target. Old fashioned energy guzzlers use up to 600 KwHrs / sq M /annum! Thats factor 10 in action! The test will be deep winter, and we’re currently nuancing the system so that we do our utmost to stay within our target. We believe it will be achieved—based on the evidence to date.
Lighting
The intention was that as much as possible, the building would be naturally lit. The Lux on the work plane has recently been measured and we’re very pleased with the outcome. The use of south-facing but shaded glazing with a high lintel gives deep penetration of daylight into the plan. The main cube building is circa 15 metres square, so to the centre of the plan it’s 7.5 metres and our modelling showed that we needed auxiliary daylight in the core of the plan. That supported a concept that is now something of a cliché—the atrium. The variation on the cliché is that the atrium does not come down vertically, but actually drops from south to north to enhance the southerly penetration of light, as a shaft of light down into the building. The atrium void on each floor shifts to the north with each descending floor and is architecturally enriching.
The auxiliary lighting is banked so that the range of fittings nearest to the window wall stay off unless absolutely required. However deep within the plan in winter, or in dull days, the inner bank of lighting in the offices comes on first, and only if the lux on the work plane remains low do the bank of fittings nearest to the window wall switch on. This is helping to reduce auxiliary electricity for lighting the offices. All the electrical lighting is geared to movement sensors and lux meters, so that if circulation areas don’t have traffic or if an office is empty, the lights simply go off. However, It’s a crucial fact based on psychological research that if the user of a room is in control, their perceived comfort band widens considerably. If they feel that Big Brother is going to open the window or turn the lights on or off, it creates a stress. So it’s crucially important that in this building the users can walk over to the window and open or close it at their pleasure, no matter what the BMS is doing. Essentially, the user can override Big Brother.
Positioned on the Solar Chimney, solar evacuated tubes provide hot water and supplementary space heating, and photovoltaic panels are used to power the BMS
The east stair ‘prism’ takes advantage of passive solar gains
Ventilation
A key aspect of the ventilation relates to the undercroft space in the building, created using concrete made with Ecocem’s environmentally-friendly cement, which is a fraction of the embodied energy of standard OPC based concrete. That slab is on Volclay,Voltek which is a bentonite clay waterproofing layer, rather than a petrochemical based tanking. The slab is 220mm thick, which is essentially a ballast to hold down the volclay, because if water meets the volclay it expands into a gel. There is a synergy there, as the heavier Ecocem-based concrete slab acts as a thermal flywheel, so in summer the air is admitted into the undercroft, there’s a pre-cool of that air from the thermal coolth in the slab which is night purged. Overnight-air passes through this undercroft, reducing the temperature of the slab. During the working day, incoming air is drawn into the undercroft through an aperture in the floor of the banking hall, and admitted into the space. The converse is true in winter. Night purging is then not used, and thermal mass retains some heat from the building and earth . During the day there is a preheat by passage over the thermal mass of the undercroft slab. The undercroft is a small space, about 1.4metres high, and The ground beams which support the timber structure above are also constructed using Ecocem based concrete. The downstand depth of the beams occurs within this zone. It also means, like in Palladian villas, the service space is used to raise the more organic timber volume up from the ground to protect it from any rogue dampness that may get into the structure. The coolth and heat from the undercroft is drawn into the main volume. We then use all the bathrooms which need a high number of air changes per hour, with an under-pressure in the north duct, to draw air from the habitable rooms, offices and circulation space through the ‘loos’ and out through the north duct. This is the first way in which extracted air occurs. The winter air change target is 0.7 to 1 air changes per hour within the offices, but in the loos, for instance, we need something like 6 or 7 air changes. They being smaller volume spaces, you get this through-put naturally, you keep the bathrooms fresh, while keeping fresh air coming into the office spaces. This is done with a series of louvres and dampers in the doors and lobbies., with a back-draft protection so that foul odours don’t come back to the habitable rooms.
The next ventilation device is the trickle venting. Low velocity is essential to get the preheat effect from the solar cavity as air is admitted below outer and allowed into the building at upper inner. At the top of the building, we have two innovative devices. The ‘Venturi’ ventilator is a success. It basically traps cross-flowing air with a V shaped section to inward. The air comes down to a ‘throat’ narrowing, rather like a chimney gathering, where you have accelerated flow through the Venturi, just above some horizontal louver blades. The under-pressure created, rather like an aircraft wing, as this air rushes across the horizontal blades, draws the air in a subtle way from the atrium. It can create significant Pascals of under-pressure in the total space of the building. This assists the trickle venting to work, drawing the air through the solar cavity of the box windows and the banking hall wall.
Exterior view of the solar chimney combining solar evacuated tubes, high-spec glass and photovoltaic panels
The building is like a living organism in a way; highly responsive to wind, sunlight, humidity and so on.
The second major ventilation device, the outcome of which we’re very pleased with, is the solar chimney. This runs at a steep angle up the centre line of the solar plant room roof. It’s oriented due south. There’s an insulated black plate solar collector in a parabolic cross section on the floor of the solar duct, so as the sun tracks through the sky, there is an excellent pick up of solar energy within the duct, and there’s a huge change in temperature from the bottom to the top of the duct which creates a huge updraft, especially in intense sunlight, which is when you want accelerated ventilation into the building—especially an office building from noon onwards.
The top of the duct, as seen from the outside, is a flat top, high-spec glass, and the floor of the duct (REFER TO PHOTOGRAPH) is curved, so that some of the surface is always facing approximately at right angles to the solar angle. If it were box-shaped, you wouldn’t get the same effect. This came out of the consultation with Strathclyde University . Dechau Tang pointed out the merits of the parabolic section and this is working. We have probes in the solar chimney at bottom, middle and top and we’re getting velocities of 1 metre per second across the whole cross section—which is equivalent to a huge piece of mechanical air handling equipment—with no auxiliary primary energy input whatever, apart from the little actuators which are powered by the sun anyway.
The suppliers of goods and equipment have been astonished by the velocities achieved—they would have had to put in a ‘humungous’ piece of conventional air handling equipment before. Velocities in the Venturi exit, where we have probes, can be up to 7 or 8 metres per second, which is an astonishingly high figure at the horizontal louver blades where the forced flow through the Venturi, above the blades, is occurring.
The Venturi and solar chimney are both controlled by the BMS, and they’re ranked. In deep winter, the solar chimney alone will be working, with the Venturi fully closed. Coming into shoulder season, the solar chimney would be brought up to fully open, starting to bring in the Venturi. In high summer, where you have the ‘spikes’ of overheating in the afternoon, the Venturi would be fully functional flat out ventilating and the solar chimney would be fully throttled open.
A close up view of the horizontal louver blades below the Venturi
Air quality and the selection of materials
In BauBiologie principles any internal room should have a balance between clays, silicates and lime. If you have too much lime it can cause sclerosis; too little clay leads to very dry or very humid air, and silicates have a balancing effect to do with ionisation. We have a largely timber building, which has a delightful effect on air quality—it’s an abstract effect, but building physics come into it as well. It’s slightly aromatic. It is hygroscopic, so it has an affect of smoothing peaks of humidity. Very significantly, the clay walls have a huge impact on air humidity, and we’ve actually measured this with a humidity metre. As you approach the clay wall, you can actually see air humidity dropping on a humid day. That has a lovely aesthetic affect as well in those spaces.
Otherwise, there are more well-known measures such as avoiding persistent organic poisons. The caveats have been observed to do with avoiding POPS (persistent organic poisons) from formaldehyde, chipboards, VOCs, PVC, dieldren, PCPs and so on. We’re using natural wool carpet, organic paints, particular species of planting like Spider plants which deal with particulates ions and toxins in the air. Computers and the paraphernalia of the modern office generate quite a lot of problems in terms of air quality, with for instance particulates from photocopiers, and ionised air from computer cooling etc. Planting has a restorative effect on this air, so we have intensive internal planting to improve air quality within the building. This becomes particularly important when you bring the ventilation rate down to about 0.7 to 1 air change per hour. You wouldn’t dare do this unless you were paying great attention to air quality. Many offices would be ventilated to between 4 and 7 air changes per hour on the rather tired and very wasteful engineering principle that the answer to pollution is dilution. The trouble with gross air dilution is that you’re consuming huge amounts of primary energy to achieve that effect.
Modelling
Based on intuitive design, we basically designed the solar chimney and the Venturi in particular ourselves. We were happy to go to the University of Strathclyde where Clarke’s work has been pioneering and we were happy to work with Jeremy Cockroft and Dechau Tang. Dechau Tang did the computational fluid dynamic modelling. We had a daylong workshop with them to make sure that the “rubbish in / rubbish out” syndrome didn’t catch us. As a result of that they produced some excellent modelling which encouraged us to continue with our design approach and to nuance it in a variety of ways. Dechau Tang put his finger on the need for a parabolic floor to the solar chimney.
Clay walls finished in organic paints in the building help humidity levels to drop on humid days and help maintain air quality levels
Thermal and Acoustic Insulation
The thermal insulation is largely timber derived. Homatherm and Steicoflex are the key products. Ecological Building Systems have access to these materials ex stock. The acoustic insulation is an interesting issue. Our target was 55dba between floors. The acoustic insulation between cellular offices is a careful balance between natural ventilation to get through-flow of air from the atrium through individual offices. There has been a gradual refinement of the acoustic panels over the doors.
Airtightness
Airtightness is crucial and we found that we had hard work trying to get subcontractors to really appreciate that you cannot have an energy efficient building unless it is ‘tight’. The tightness is to do with severe energy loss, but also crucially in terms of vapour management. If you have interstitial vapour trapped within fabric of a timber building of this nature it is a recipe for rampant Serpulius Lacrymans and so on by way of wood feeding biota. So the management of the vapour barrier and the breathing membrane and whether these two skins meet the framing to aperture is crucial. A grave problem in the Irish Construction industry exists in a lack of realisation of the implications of vapour track into the fabric. Once a timber building starts rotting, and there’s unseen propagation of fungi, you have a huge problem on your hands. A caveat here is that you dare not embark on multi-storey timber construction of this kind unless air-tightness and vapour-tightness is fully understood. We need to build on German and Scandinavian know-how here. Griffner Coillte is a potentially promising exemplar. It is a recipe for disaster to continue with some of the ‘wood butchery’ that goes on in Ireland , masquerading as good timber frame.
External Shading
As part of the Peace Garden concept around the building, the Judaic, Islamic and Christian patriarch Abraham was an inspiration. His sons Ishmael and Isaac exemplify these different religious traditions. There’s a building in Hebron where all three religions honour Abraham in the same building, where he is buried. So the ‘Abraham’ screen is the armature, (in these very troubled times from Gaza to Iraq ), for the very beautiful shading plant Wisteria, which will take a couple of seasons to fully colonise the Abraham screen and brise soleil at the top. This gives natural shading when you need it, and with deciduous leaf fall you get back to maximised daylight in deep winter. I’d like to compliment the work of Marta Lam of the University of Brighton who has done some hard science, post graduate research in this area, showing that you can have drops in temperature of up to 5 and 6 degrees C in the vicinity of this shading, removal of particulates and humidity balancing. There is mechanical shading in the interim, while we’re waiting for this planting to develop. We’re using the security shutters partially closed on a daily basis, which are perforate screens, and these are being used strategically in the morning, afternoon and evening on the appropriate façade, and the building superintendent understands how to use them. They’re very simple to use to avoid excessive incident of sunlight onto the banking hall walls in particular.
Roofing
You get some thermal mass and insulation using the intensive roof in particular. With the existing boardroom which was from the 80s—a relatively low budget roof of composite cladding—rain noise was an issue and this earth roof has dealt with that problem. The thermal insulation value of saturated roof is not very high, but it brings a thermal flywheel effect into play. The main reason for this roof is to re-oxygenate the ground plane which you have turned from a green landscape into a hard landscape. Simply lifting the green landscape up gives a restoration of air quality, reducing urban air particulates and so forth. Use of the green roof restores a natural balance. Crucially, everyone knows in Ireland the way that ultraviolet light breaks up flat roofing materials. A living roof deals with that problem. It actually protects the fabric of the building from direct sunlight.
img src="/images/stories/magimages/Vol02-Iss11/0211navan17.jpg" alt="" width="330" height="362" />
An extensive sedum green roof which was added to the original building and has solved the problem of rain-noise in the existing boardroom
Water
We’re 90% water ourselves. In Ireland water is all around us. Water is the kind of through-flowing reality of life. In approaching the water management on the site we started with the falling rain. Our target was to keep it out. Vigilance in that respect is crucial. As an addition to the existing building from the late 80s we’ve put an extensive Bauder roof using Sedum. For the new build, we’ve put an intensive deep earth roof, about 350mm of humus. On this roof we have grasses and bamboo. The intention is three fold: to harvest water and irrigate this planting; to reduce sound impact of extreme rains particularly on the existing building; and to then harvest the water from the roofs to recycle within the building for irrigation of the extensive internal and external landscaping of the building and for toilet flushing. The loos are dual flush, with a mini and major flush. We have deliberately eschewed using this water for showers. There are some showers within the building for cyclists, but because of bird guano and organic matter in the landscaped roofs we avoided using it for potable or ablution uses. With different types of roof you can do this. We have a large reservoir sunken tank within the gardens , with filtering of this water. We then have internal and external water gardens to compliment the art works, and quite a lot of trouble in this has been taken by Linda Fitzsimmons, who’s done a beautiful job. The aesthetic, elemental calming effect of water is used as much as possible.
Wastewater
We reduced the outputs to the mains system as much as possible. We’re using SUDS (sustainable drainage systems) for all the roads, paths and paving. After downpour this water does not instantly run off to flood the drains. In fact there’s a catchment below the paving, and a slow release of the water back into the groundwater, filtering down into the aquifers. There’s a certain capacity that the SUDS system takes, and it is only the excess water which would ever go to storm-water drains. Regarding blackwater treatment, we made a decision to use the infrastructure provided through the municipality. The building is on a confined urban site. It did not make sense to go for onsite sewage treatment here as we have on other projects.
Access Issues
Universal access is now a legislative requirement as well as being a human right. We recently finished a project in the Four Courts complex where historic accommodation had to be made accessible to all including ambulant disabled, partially-sighted people with severly impaired mobility and so on. Disability is a universal experience for those of us who live to any age: as we grow old we all become less able or challenged in some way. It was a client requirement that this building be fully accessible for employees, members, visitors or whatever. The entire building is designed on universal access principles. The lift plant and equipment is Kone Eco-Disk, with in-shaft mechanism, which uses less than 50% of the electrical energy used by conventional systems. Full credit to Kone for leading the field on this. They also do a beautiful job—the quality assurance is high-end. We insist on using evacuation standard lifts, which means that there’s an independent energy supply, even during grid failure or loss of grid in fire. There are protected power circuits to the lift and the fire chief has control of the lift in the event of fire, so that if elderly or people with disabilities are trapped at upper levels the fire chief only will direct evacuation of the building using the lift. This calls for some additional expenditure but it is a significant safety feature in the building, particularly a timber building.
Existing Building
The existing building was built in the late 1980s, I would now consider it a “light green” building. It used passive solar, and high thermal mass techniques for instance. I would now in retrospect see it as quite dated but am still pleased with it as a design. A key component here is the social and community dimension to these buildings. These buildings are owned by 25,000 members of the community—almost every member of the community in Navan is a member of the Credit Union. The buildings speak to a certain degree of social solidarity and economic well being. The Irish expression “Trí neart a chéile, a mhaireann na ndaoine” is appropriate. The use of landscaping, art, water, natural materials, and inviting form-language rather than the rictus of ‘modernism’ which can be extremely antipathetic and anti community in demeanour—a banal cloned private language of architect to architect, in a sterile and reductive way, which is a travesty of the conceptual basis of true modernists masters such as Johanes Itten. Devising such a large volume beside the little building from the 80s was quite confronting. We have worked as hard as we can to make the forms sympathetic. There’s a scale issue of how you step from a building which is effectively storey and a half, to a 6 storey building with some rather high service volumes around it. The architectonic inter-relationship comes from a lot of study and is hopefully successful.
Overcoming Planning
The planning history is somewhat vexed. I take a dim view of the general development-control planning ethos in Ireland . We lack a forward planning culture, we lack a progressive planning input—which is exemplified by a minority of planners in Ireland . There is a culture of “knee jerk” development control planners, who if something dares to put its head above the parapet, whether in nature or in height, the immediate reaction is to prevent it. This leads to a series of zero sum outcomes, and the banality of our general building culture is something of a disgrace. We Irish people are famous worldwide for being builders, yet our output across this beautiful island in the landscape and in towns and cities is way below our potential. There needs to be a root and branch review of how we perceive design, forward planning, with development control simply being a matrix of regulation for a forward vision of how we want settlement to be. We were eventually granted planning for this building. In some respects it was somewhat controversial. We hope that the trust that has been placed in the building is vindicated by the outturn.
The Project Team’s Response to the Challenge
It’s been particularly gratifying as the job went on to see perplexity change to interest to joy at the out turn, and that’s not a bad progression. We’d like to compliment PJ Hegarty Ltd for adopting right from the start a partnership approach. We’ve managed to come to the final accounts stage of this job on cordial terms with the director level and management of PJ Hegartyand Sons. They have an appetite for innovation. They wanted to be associated with a project of this type. The profit margins are considerably less than in conventional large volume rapid throughput build, and Every subcontractor who came to the job had to make an extra effort and we compliment everyone, who took the time and trouble to go through the process with us. Each nominated subcontractor had to go through quite a detailed design phase on a C B A status of approval protocol. This has worked out. Hopefully, some of the subcontractors involved will go on to replicate what they’ve provided in this contract with greater ease than was possible at this level of innovation. Nordan, for instance, who were extremely good value, went on in design development to deliver in terms of good engineering. We would compliment Frank O’Toole and his team of Erik De Vos and John McMenamy for staying with us and for seeing the thing through. We believe they’ve produced something that they can be justifiably proud of.
A message to the Construction Industry
I hope this project sends out a constructive message to the Irish construction industry. Hard science know-how, supply-side expertise, materials which are readily available for sourcing with the goodwill to find the source are far too little used, and we’re surrounded from our housing to our commercial and institutional buildings with banality, through the repetition of hackneyed ways of doing things. This turns very significantly on the degree of manipulation in the market. The sooner, as is the case with this building that it becomes a buyer’s market, where the purchaser calls the shots, gets good advice, and decide what they’re going to purchase. It’s been a sellers market for far too long. The interest rate has driven the “fizz” in the market and something of a feeding frenzy where, by and large everyone from domestic mortgage holder to commercial building tenant is getting extremely bad value for money. Beware the risen people in the rip off Republic. Nobody likes to be stuck with a shoddy product for which they have paid out of their precious resources. They feel cheated and let down. That anger is beginning to emerge I believe into the building culture. Irish people are entitled to better, and hopefully this little building—it’s only 1,300 square metres all together—can act as a waypoint or fingerpost towards what is possible. The building is far form perfect, and it has been a learning experience for everybody, but that is life. People learn by doing, and in this country we do far too much talking instead of learning by doing. The blood, sweat and tears that have gone into this building have been put in with a view to the building being a multiplier within the Irish building sector. It’s rather pointless on its own unless it’s highly replicated, right across the board in an open and generous way, whether through intellectual property, commercial secrets or whatever. It’s time that Ireland made really good progress in this area and it can only happen if people are generous with know-how.
Selected project details
Client: St. Mary’s Credit Union
Architects: Gaia Ecotecture
Consulting M&E Engineer: Derham McPhillips
Main Contractor: PJ Hegarty
Quantity Surveyor: Gardiner & Theobald
Structural timber Subcontracter: Projekt-Holzbau Merkle
Structural engineer ‘in-house’ to Merkle: Pirmin Jung
Piling sub contractors/substructure: PJ Edwards
M&E contractor: Mercury Engineering
Electrical subcontractor: HTE
ACU supplier: Crystal Air
Solar contractor: Energy 365
Solar Subcontractors: Eirbyte & Glas
Radiators & Sanitaryware: Versatile
Light fittings: Project Lighting
BMS: Standard Control Systems
Ventilation Testing: King Testing
Venturi, Solar Chimney & Aluminium/steel windows: Pensher-Skytech
Timber /aluminium windows: Nordan
Moeding clay tile cladding agent: SJW Facades
Sedum roofing: Bauder
‘Kone’ Passenger Lift: Industrial Logistics
West stairs: Joseph McNally Joinery
Fit-out & furniture Subcontractor: Walls to workstations
Banking hall counter: Charles O’Toole Furniture
Blinds- BH & partitions: Paddy Rogers Blinds
Tambour suppliers in “Bubble” Reveal Windows: Wood Partners A/S
Atrium handrail: Metalcraft
Zinc roofing & RWPs: Robert A. Copeland & Sons
R&D: ESRU Strathclyde University
Landscape: Tom Flynn
Internal planting: Linda Fitzsimmons
Artists: Cormac Boydell & Rachel Parry
- sustainable design
- Navan Credit Union
- Gaia Ecotecture
- photovoltaics
- solar energy
- timber frame
- timber
- venturi
- heat pumps
- building management system
Related items
-
Grant integrated heating packages installed for 61 homes in Rathdrum
-
Timber in construction group holds first meeting
-
Up to 11
-
Passive Power
-
It's a lovely house to live in now
-
Offaly new build installs Grant integrated heating package
-
Is it okay to retrofit heat pumps before building fabric?
-
Mass timber consultation: have your say by 21 April to change the rules
-
We Build Eco flat pack timber frame partnership gathers pace
-
Mass timber masterwork
-
Hevac launches hot water heat pump with green refrigerant
-
Viessmann launch two new compact heat pumps