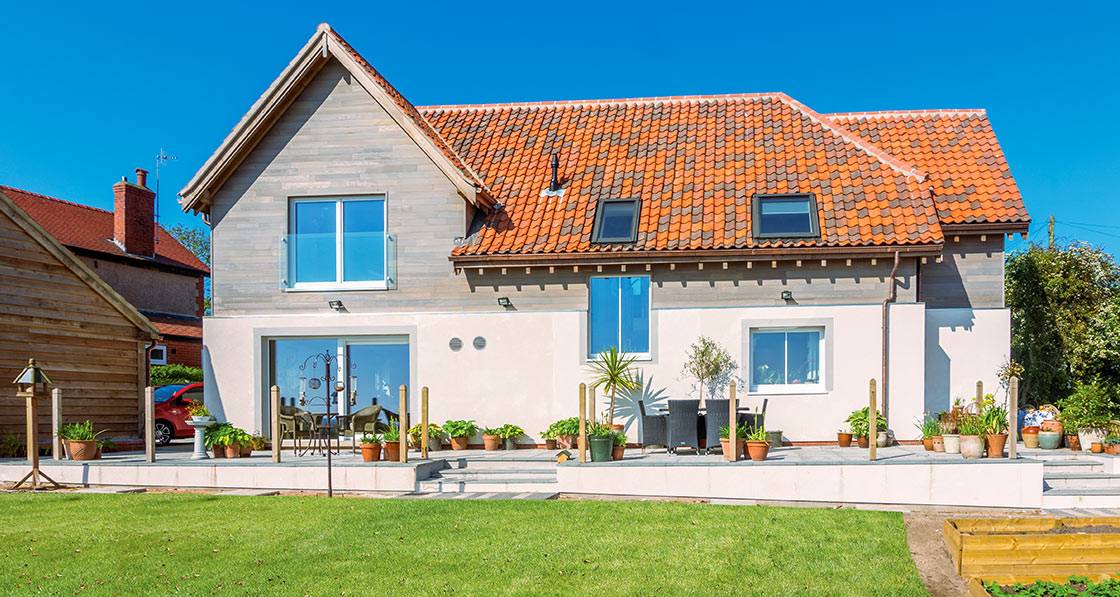
- New build
- Posted
The UK's first green oak passive house
Choosing newly-harvested green oak — which shrinks and moves as it dries — for the millimetre-precise demands of passive house construction was a bold move by Phil Garnett and his wife Yvonne, but one that ultimately gave them one of the most unique and ground-breaking passive homes in the UK.
Click here for project specs and suppliers
Building type: 188 square metre detached green oak house
Location: Hunmanby, Yorkshire
Completed: March 2017
Standard: Certified passive house
£305 gas bill per year (heating, hot water & cooking)
When they decided to build a new home in the village of Hunmanby, near the Yorkshire coastline, Dr Phil Garnett and his wife Yvonne intended to create a simple eco-home out of green oak. But somewhere along the way, their plans became much more radical and they ended up constructing the UK’s first certified green oak passive house.
In doing so, they not only disproved the notion that it could not be done technically, but they also set a powerful precedent for future builds.
“It’s been a dream of mine to build a green oak house since I went to a Grand Designs show 20 odd years ago,” Phil Garnett says.
It’s been a dream of mine to build a green oak house since I went to a Grand Designs show 20 years ago.
“But when I approached Andrew Yeats, of Eco Arc architects, in 2014, he suggested going a step further and designing a passive house. It was far more challenging technically, requiring fantastic accuracy in the build and huge amounts of insulation. But we went for it and we love it. I’ve become an absolute zealot to the cause of passive houses.”
From the lounge upstairs at Hilltop House, there are uninterrupted views of 16 miles of coastline, from the high chalk cliffs at Flamborough Head over to Scarborough Castle. “There’s nothing between us and the sea except fields. I can sit for hours as the amazing view changes hourly, so I never get bored.
“But it’s not just the view we love. During the ‘Beast from the East’ cold spell, we were basking in 21 degrees without turning the heating on. The airtightness also makes the house so peaceful, and there’s no dust whatsoever because the mechanical heat recovery system supplies filtered fresh air,” Garnett says.
This article was originally published in issue 26 of Passive House Plus magazine. Want immediate access to all back issues and exclusive extra content? Click here to subscribe for as little as €15, or click here to receive the next issue free of charge
Cumbria-based architect Andrew Yeats of Eco Arc believes Hilltop House will inspire many others to build passive houses using green oak. “In the past, it was thought that green oak and passive houses could not be bedfellows. But Hilltop House shows you can have your cake and eat it. You can enjoy the beauty of exposed oak frames and also get the thermal qualities required to reach passive house standard,” he says.
Yeats believes the British, in particular, will relish the opportunity to bridge the gap between a traditional arts-and-crafts style timber frame aesthetic and the passive house standard.
“Offsite pre-fabricated passive houses can be quite clinical and a bit Germanic. There can be acres of plasterboard and it’s all fairly stripped back, which suits a modern aesthetic, but a lot of British people like a more traditional house,” he says.
From the outset, Yeats was aware of how ground-breaking his design would be. He had to take a metaphorical deep breath, he says, knowing how green oak twists and moves — causing a potential conflict with the need for airtightness in a passive house.
Most homes with green oak frames place the oak columns within the insulation layer. But that wouldn’t work for a passive house, because it would displace insulation and create a big thermal bridge.
The solution was to create an internal frame of green oak — with the oak columns standing within the rooms of the house — and then have the cellulose-insulated timber wall panels wrap around the outside of the oak frame, with a gap for movement tolerances between the two. The frame now takes the main structural load of the roof and upper floor; the timber-panel walls sit on the insulated foundation and are self-supporting.
-
The ground floor features a 300mm thick Isoquick insulated foundation system, plus 250mm wide insulated upstand to edge of concrete slab The ground floor features a 300mm thick Isoquick insulated foundation system, plus 250mm wide insulated upstand to edge of concrete slab
-
The internal frame of green oak which takes the main structural load of the roof and upper floor The internal frame of green oak which takes the main structural load of the roof and upper floor
-
A crane lifting into place the cellulose-insulated timber wall panels, which wrap around the outside of the oak frame A crane lifting into place the cellulose-insulated timber wall panels, which wrap around the outside of the oak frame
-
More panels being lifted into place with metal web joists for services visible In the intermediate floor More panels being lifted into place with metal web joists for services visible In the intermediate floor
-
The oak frame roof structure which is internally exposed The oak frame roof structure which is internally exposed
-
A pre made window ope in insulated panels, with Pro Clima Solitex wind-tight membrane to the outside of the build-up A pre made window ope in insulated panels, with Pro Clima Solitex wind-tight membrane to the outside of the build-up
-
Airtightness taping around the installed Internorm timber-aluminium windows Airtightness taping around the installed Internorm timber-aluminium windows
-
The oak columns stand within the rooms of the house, with the timber wall panels wrapping around the outside, and a gap for between the two — the gap ensured builders could access the walls internally for airtightness taping, and that any movement of the oak frame over time would not impact on airtightness The oak columns stand within the rooms of the house, with the timber wall panels wrapping around the outside, and a gap for between the two — the gap ensured builders could access the walls internally for airtightness taping, and that any movement of the oak frame over time would not impact on airtightness
-
MVHR ducting over oak frame MVHR ducting over oak frame
https://mail.passive.ie/magazine/new-build/the-uk-s-first-green-oak-passive-house#sigProId63f8dc78c3
Yeats had to be careful to maintain the airtightness layers in the insulated panels behind the oak frame. Inaccessible joints would be hard to tape up, he says.
As a result, the builders fabricated every section so that all the joints between the insulated shell components were visible, and not colliding with the green oak frame.
“Instead of having one flat panel meeting another flat panel in a corner, we made an L-shaped panel which was then all pre-taped prior to insulation. So, when we had a butt joint, it was off-centre to a column,” he says. This made access for taping easier. “Having expected it all to be difficult, once we established the principle and knew the ground rules, it was straightforward.”
It was thought that green oak and passive houses could not be bedfellows. But Hilltop House shows you can have your cake and eat it.
The Hereford company Oakwrights was responsible for the construction of the house. Although they build regularly with green oak, they had never worked on a passive house before. “I asked them to switch priorities,” says Yeats. “I said ‘the oak frame is what it is, and it does what it does. I’m much more interested in the continuity of insulation and protecting the airtightness’. They learned fast and followed our instructions to the letter.”
Work began on the house in March 2016 and was completed a year later. Yeats visited the site regularly to make sure the butt joints in the insulated panels were thermal bridge free. “I inspected and photographed each one to make sure we had continuity of insulation throughout,” he says.
“The measurements all prove without doubt that green oak houses can be delivered to a very high passive house quality assurance standard.”
Aside from the oak frame and timber-panel walls, the house features a typical checklist of passive house features: south-facing orientation for solar gain, triple-glazed Internorm windows, an insulated foundation system from Isoquick, and a Paul mechanical ventilation heat recovery (MVHR) unit.
Phil Garnett says that even during the ‘Beast from the East’ earlier this year, the house maintained an indoor temperature of 21C without the gas boiler kicking in. But his wife Yvonne likes to keep it at 23C in the evenings generally, and the couple spent £305 on gas for space heating, hot water and cooking in their first 12 months.
“Now we are living in a home that is maintained at a constant optimal temperature with a continual supply of filtered fresh air from the MVHR,” Phil Garnett says. “Combine with this the subtle smell of wood, the visual appeal of the exposed oak frame, and the peace and quiet created by the exceptional soundproofing of the passive house construction, and you have an environment that is perfect for all the senses, generating a fantastic feeling of wellbeing.”
Selected project details
Clients: Phil & Yvonne Garnett
Architect & passive house designer: Eco Arc
M&E engineer: Alan Clarke
Civil & structural engineer: Richard Renier Associates
PHPP & thermal bridging analysis: Alan Clarke / Eco Arc
Main contractor: David Warnett
Airtightness tester: Paul Jennings
Timber frame system: Oakwrights
Cellulose insulation: Thermofloc
Wood fibre insulation & airtightness products: Ecological Building Systems
Insulation foundation system: Isoquick
Windows & doors: Ecohaus Internorm
Roof window: Fakro
Heating system: Worcester Bosch
Radiators: Quinn
MVHR: Green Building Store
Clay roof tiles: William Blythe
In detail
Building type: 188 sqm green oak framed passive house (+ 36 sqm garage)
Location: Hunmanby, Yorkshire
Completion date: March 2017
Cost: £450,000 (£2,008 per sqm)
Passive house certification: Passive house certified
Space heating demand (PHPP): 17 kWh/m2/yr
Heat load (PHPP): 10 W/m2
Primary energy demand (PHPP): 88 kWh/m2/yr
Heat loss form factor (PHPP): 3.16
Overheating (PHPP): 4% (of time above 25C)
Airtightness (at 50 Pascals): 0.3 air changes per hour
Energy performance certificate (EPC): A (92)
Thermal bridging: Bespoke cold bridge free junction detail design by Eco Arc certified passive house designers with input from Alan Clarke & Nick Grant.
Energy bills (measured or estimated): £305 annual gas bill for space heating, hot water and gas cooker.
Ground floor: 20mm Engineered Oak floor boards with Poly-Onx oil matt finish, on 250mm thick reinforced concrete floor slab, on Visqueen radon membrane, on 300mm thick Isoquick proprietary interlocking insulation (plus 250mm wide insulated upstand to edge of concrete slab), on 50mm small, clean, angular, free-draining stone, on formation and layering of Type 1 hard core layers back to solid substrate, proof rolled sub-grade. U-value: 0.012 W/m2K
Ground floor walls: 10mm thin coat silicone render finish by K Rend externally, followed inside by 100mm dense recycled aggregate concrete block, 50mm wide drained & vented cavity, Solitex Fronta Humida breather membrane, 100mm Gutex Multitherm wood fibre insulation, 245mm I-beam studs at 600mm c/c insulated with full-fill Thermofloc cellulose insulation, 9mm OSB board, Novia VC6 vapour control membrane, 50 x 50mm battens to form 50mm service void insulated with Knauf glass wool insulation, 12.5mm Gyproc plasterboard internal lining with plaster skim, 1 mist coast & 2 coats emulsion paint, internal exposed oak frame structure. U-value: 0.106 W/m2K.
First floor walls: Western red cedar timber cladding boards externally on 50 x 50mm cladding battens forming wide drained & vented cavity, followed inside by Solitex Fronta Humida breather membrane, 100mm Gutex Multitherm wood fibre insulation, 245mm I-beam studs at 600mm c/c insulated with full-fill Thermofloc cellulose insulation, 9mm OSB board, Novia VC6 vapour control membrane, 50 x 50mm battens to form 50mm service void insulated with Knauf glass wool insulation, 12.5mm Gyproc plasterboard internal lining with plaster skim, 1 mist coast & 2 coats emulsion paint, internal exposed oak frame structure. U-value: 0.106 W/m2K.
Flat roof: Clay tile roofing on battens and counter battens, breather membrane on soft wood apex sub frame. Flat ceiling consisting of 100mm Gutex thermal board on 2 x 300m I-beam studs at 600mm c/c with 600mm full-fill Thermofloc cellulose insulation, 9mm OSB, Novia VC6 Foil vapour control membrane, 100 x 100mm ceiling joists between oak purlins to form service void with 12.5mm Gyproc plasterboard with plaster skim, 1 mist coat & 2 coats emulsion paint. Roof U-value: 0.061 W/m2K Pitched roof: Clay tile roofing on battens and counter battens on breather roof membrane, 100mm Gutex thermal board on 300m I-beam studs at 600mm c/c with 300mm full-fill Thermofloc cellulose insulation, 9mm OSB, Novia VC6 foil vapour control membrane, 50 x 50mm battens to form service void with 50mm Knauf glass wool insulation, 12.5mm Gyproc plasterboard with plaster skim, 1 mist coat & 2 coats emulsion paint, internal exposed oak frame structure. Roof U-value: 0.097 W/m2K
Windows: Internorm HF310 timber-aluminium triple glazed windows & HS330 sliding doors. Featuring ISO glazing spacers and glazing U-value of 0.6 W/m2K. Overall window U-value: 0.76 W/m2K.
Roof window: Fakro FTT U8 Thermo. Passive quadruple glazed unit roof lights with fivefoldsealed airtight construction, supplied complete with thermal flashing and XDK insulation kit. Overall U-value: 0.58 W/m2K
Heating system: Worcester Bosch Greenstar 12i condensing gas boiler & Worcester Bosch Greenstore TC250 twin coil cylinder total volume 190 litres, distributing heat via small radiators (generally one per room) and towel rails to wet rooms.
Ventilation: Passive House Institute certified Paul Novus 300 MVHR system. Passive house certified efficiency 93%. Electrical consumption 0.30 Wh/m3.
Green materials: Natural clay tile roofing, natural timber flooring, recycled newspaper cellulose insulation, FSC timber.
Image gallery
-
Ground floor plan Ground floor plan
-
Panel junction detail section Panel junction detail section
-
Section AA Section AA
-
Section BB Section BB
-
First floor plan First floor plan
-
Site floor plan Site floor plan
https://mail.passive.ie/magazine/new-build/the-uk-s-first-green-oak-passive-house#sigProId918ac23215