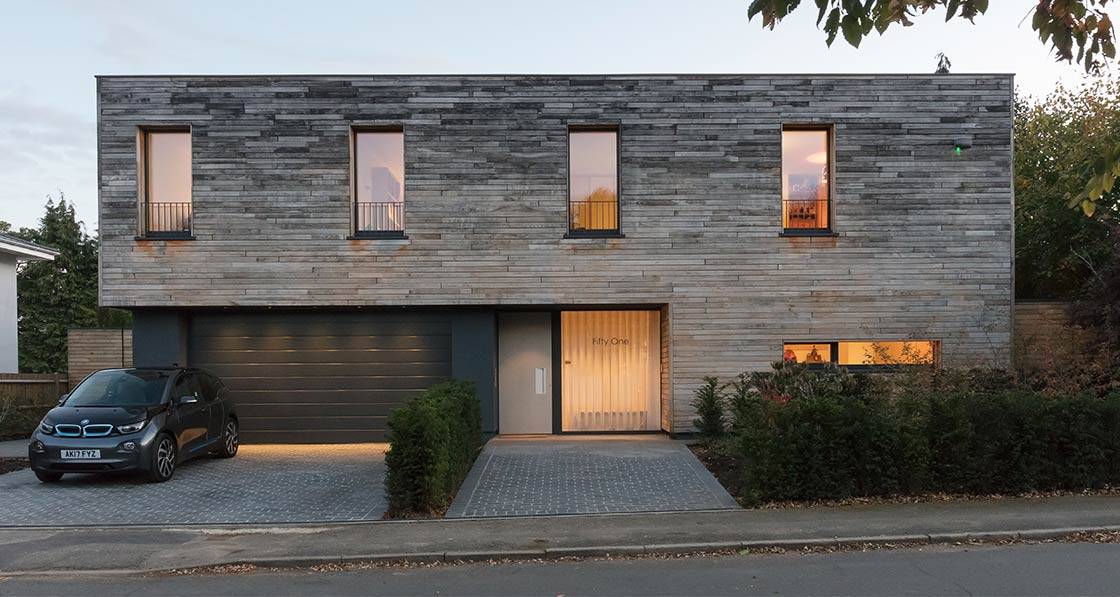
- New build
- Posted
Wood works - Sleek but large Herts passive house goes heavy on timber
The Deerings, a large new certified passive house in the Hertfordshire village of Harpenden, is the stunning result of meticulous attention to design, energy efficiency and ecological materials by its architects, builders and a homeowner so taken by the experience that it led to an investment in an innovative passive house start-up.
Click here for project specs and suppliers
Building: 400 sqm timber frame passive house
Location: Harpenden, Hertfordshire
Completed: October 2017
Standard: Passive house certified
£ for space heating (see ‘In detail’ panel for more)
Originally from North Wales, Danny Luhde-Thompson had initially intended to move back there and build a new home, but when circumstances changed so did his plans.
Rather than retreating to the country life, Luhde-Thompson and his wife ended up staying in their current home town of Harpenden in Hertfordshire, electing to demolish their bungalow in favour of a new, modernist-inspired five-bedroom house.
His childhood in Wales did mean one thing, though: Luhde-Thompson was sure that he wanted a house that took energy use and comfort into consideration. “As a child I lived in a long cold stone house with ice on the windows in the mornings,” he says.
Wishing to avoid this ever again, Luhde-Thompson wanted a house that had the best possible thermal performance.
Perhaps inevitably, it became a passive house. “Once you start looking into it, it’s about more than just insulation; it’s about airtightness and thermal bridging. When you keep going you end up with a passive house.”
When Luhde-Thompson moved into the original building on the site —as he puts it, a typical 1970s bungalow—he attempted remedial work, and while this improved the dwelling it was also part of what inexorably drove his desire to build a passive house.
“I added insulation, and that definitely made a difference, but you come to realise there are problems you can’t solve: cold bridges, damp patches and so on. It got kind of annoying, frankly.”
This article was originally published in issue 27 of Passive House Plus magazine. Want immediate access to all back issues and exclusive extra content? Click here to subscribe for as little as €10, or click here to receive the next issue free of charge
Over the years Luhde-Thompson spent a lot of time researching the best way to achieve an energy efficient dwelling, and by the time he started to plan his build in Harpenden, passive house had become a realistic goal, with more expertise and know-how available.
Luhde-Thompson says that the process was not a particularly challenging one. “Because we knew we wanted it to be a passive house right from the start and because we had a south facing plot it was relatively easy. We were able to minimise north facing glass,” he says.
He has already felt the benefits, saying that aside from having spent essentially nothing on space heating, the house is simply more comfortable than the norm.
The blistering summer of 2018 did throw up potential difficulties, however. How would a passive house deal with weather that saw all of Europe baking?
“The hot summer was much more of a challenge, it’s true,” he says. ““You have to have a strategy. Basically, you need to move the blinds and remember to open the windows in the evening [but] if you can get the house down to 23 or 24 [degrees] overnight you only gain a degree or two during the day.”
Other difficulties were the result of conscious design choices. “We wanted a contemporary style, which was fine [but] some of the detailing work was pretty hard for the architect. Log-burning stoves in a passive house are pretty weird, but we liked the feel of sitting around one in the winter. Some of the routing through the chimney was pretty complicated,” he says.
For architect Tom Gresford. this was his second fully certified passive house, and for his practice, Gresford Architects, marrying energy performance with good design is a central goal. Sometimes it is met with resistance, though.
You’re not just getting something that performs well, you’re also getting a beautifully-designed building.
“I don’t think people take global warming seriously enough. This is me getting on my high horse, but [most] people want something sexy more [than they want a low energy home],” he says.
“We always try to get our clients to go to passive house; we’re not always successful, but we always try. We like to marry that with a real concern for aesthetics.”
Selling clients the idea of a house with lower running costs doesn’t necessarily work, he says. “The problem with the cost issues is that people who are building the houses are relatively wealthy anyway.”
Nonetheless, Gresford intends to keep banging the drum. “For us, we’re saying to people that part of our unique selling point is that we are very design-conscious. You’re not just getting something that performs well, you’re also getting a beautifully-designed building.”
1 One-wire sensors installed throughout the house, like this one in the KORE insulated foundation system, monitor temperature and in some cases humidity;
2 construction of internal partitions in the timber-frame house underway;
3 I-Beam timber joists were fully insulated with Warmcel insulation with some mineral wool below, as seen here, followed beneath by a Pro Clima Intello Plus vapour control layer;
4 Solitex Fronta WA wind tight breather membrane to the outside of the timber-frame construction;
5 construction of the chimney for the wood-burning stove;
6 timber battens forming the rainscreen cavity to the outside of the wall build-up, onto which sweet chestnut cladding was fitted externally;
7 a boxed-off section of extra insulation installed due to the proximity of this area to the roof terrace;
8 timber battens forming a services void in the ceiling through which the rigid MVHR ductwork runs;
9 another one-wire temperature sensor installed within the timber-frame.
Gresford says that an element of compromise is to be expected, but that does not mean the passive house standard cannot be achieved.
“If you’re willing to engage [then] you can get there. That’s one of the things I like about passive house: you’re either getting it or you’re not. There’s no fudge in the certification.”
The Deerings, a timber-frame construction, adopted a ‘fabric-first’ design approach while aiming to meet the client’s aspirations in terms of space and lifestyle.
The super-insulated timber frame was constructed off-site by passive house veterans MBC Timber Frame Ltd, supplied with insulation and an airtight membrane, and erected in three weeks on a KORE passive slab, also provided by MBC.
It’s about more than just insulation; it’s about airtightness and thermal bridging.
“The MBC airtightness guarantee does remove a lot of the pain, because they absorb that headache,” says Mike Jacob of Trunk Low Energy Building, who project managed the build.
This is the fourth passive house Jacob has worked on with Gresford Architects, and he says that preserving airtightness while installing the flue for the stove, after MBC had finished on site, was the biggest challenge on the job.
“In terms of thermal bridging that was really dealt with at the design stage. The garage was tricky, the roof terrace was tricky, but those problems were ironed out before it came to site,” he says. “So, it was more about the service penetrations, particularly the flue.”
Gresford agrees: “Wood-burning stoves have issues with airtightness and cold bridging,” he says. “The average one is about as airtight as a sieve. The other [airtightness issue] was the cat flap. We went for an automatic cat flap, with a chip to open it.”
As a child I lived in a long cold stone house with ice on the windows.
Meanwhile cellulose insulation and external sweet chestnut cladding was chosen to help reduce the carbon footprint of the project, which minimised the use of concrete and steel to less than ten per cent of the total volume of the building.
Attention to the embodied energy in the materials was not only of interest to an environmentally-conscious client, but something that Gresford generally works into his designs. “Our previous passive house went completely without steel,” he says.
“It was purely timber frame, but in this one, because of some of the design features, it does have some steel in it. That doesn’t affect the energy performance. but it is a question of embodied energy, and some of the detailing becomes harder. You have to work a little bit harder on cold bridging and so on.”
An open plan ground floor sits below a five-bedroom first floor, with an orientation toward the garden, affording views intended to make the house a special place to be. The first floor has a reading area, taking advantage of the natural light that fills the space. Back on the ground floor, a utility room complements the open plan kitchen.
For heating, the wood-burning stove is one of three systems that feeds into a 500-litre heat store; there’s also a huge (90 tube) solar thermal array and a gas boiler. The heat store feeds underfloor heating pipes downstairs, while upstairs it supplies towel rails in the bathrooms and a duct heater in the supply air of the heat recovery ventilation system.
To some, this might seem like a lot of equipment for a passive house. “I would have been happy with a very minimal heating system,” says Luhde-Thompson, “but when I was originally considering a passive house there were very few of them. I could just imagine the complaints I would have had from my family if they had been cold, with no backup heating.”
The underfloor heating pipework was cheap to add anyway, he says, and he was keen for a stove for its look and feel in winter. “A normal 6 to 8kW stove would overheat a passive house, so we had to have the heat store to take heat away — and that works perfectly.”
The stove does the bulk of the (minimal) heating workload, complimented by the solar, and because he has wood from hedging and trees taken down during siteworks, he’s spent almost nothing so far for heating. The gas boiler is a backup but has been little used.
So far, he’s barely used the underfloor heating either, except in his wife’s study. With a year’s experience under his belt, he says they probably could have managed with just having underfloor heating in his wife’s office and a duct heater for downstairs, like upstairs.
For Luhde-Thompson, the project was also somewhat serendipitous. While it was on site, project manager Mike Jacob was getting ready to seek funding for Kiss House, a new enterprise that delivers architect-designed, turnkey timber-frame houses built to the passive house standard.
Luhde-Thompson, who was quickly becoming a passive house evangelist, looked over the business plan and ended up becoming one of the primary investors in the new company. “I’m passionate about building more passive houses, and Kiss House seems a great way of achieving that,” he says.
And at the Deerings, the end result now is exactly what was planned: a contemporary home, yes, but also one that makes a positive environmental statement, that sets an example for others to follow — one of Luhde-Thompson’s motivations for building a passive house in the first place.
As he says: “I also wanted to build one so that other people would be inspired to do so.”
Graphing the Deerings
A data obsessive, homeowner Danny Luhde-Thompson has installed 67 one-wire temperature sensors throughout his house, monitoring everything from conditions inside his walls and floor to how hot or cold every element of his heating and ventilation system are. Some of these sensors also record humidity. Here, we present graphs of some of his most interesting data.
(above) Performance of the house during a week of very cold weather between 21 and 28 February 2018. MIN shows the temperature of air being drawn in from outside by the ventilation system (MVHR) — essentially ambient outdoor temperature. MSUP is the temperature of pre-heated warm air the MVHR is supplying to the house. MEXT shows the temperature of air the MVHR is extracting from ‘wet’ rooms. Bed1 shows the temperature in one bedroom wall, while Study is the temperature in the floor of the study — with spikes when the underfloor heating is turned on. The sensors show consistent, comfortable temperatures during an intense cold spell. MOUT, the red line, shows the temperature of air the MVHR is dumping outside after heating is extracted.
(above) Performance during a remarkably hot summer afternoon, when the temperature of air drawn in by the MVHR (MIN), ie ambient outdoor air, peaked over 32C. MOUT, the temperature of air being dumped outside by the MVHR, tracks this closely, because the heat recovery function is turned off so no heat is being extracted from outgoing air. Temperatures in the study floor (Study) remain below 24C here, but in the bedroom wall (Bed1) they peak slightly over 25C — the passive house definition of overheating. MEXT shows the temperature of air the ventilation system is extracting from wet rooms — again showing signs of some overheating, though temperatures may be warmer in the ventilation duct. MSUP is the temperature of air the MVHR, in bypass mode, is supplying to the house.
(above) This graph shows temperature and humidity in one external wall between 16 January and 16 March. MIN show the temperature of outdoor air drawn in by the MVHR. WNHO-t is ‘wall north high outside temperature’, the temperature of an in-wall sensor high on the outside of a north-facing wall, so it closely tracks ambient temperature. WNHI-t is towards the inside of the same wall, with a temperature consistently around or just under 20C. WNHI-h shows humidity on the same sensor, consistently between the 40% and 60% recommended for good indoor air quality. WNHO-h shows humidity towards the outside of this wall, typically around 80%, while OUT-h shows ambient outdoor humidity. Overall the graph reveals a healthy, consistent indoor humidity in spite of humid conditions outside. TB1 is the bedroom temperature, consistently at or just above 20C.
Selected project details
Client: Danny Luhde-Thompson
Primary architect: Gresford Architects
Passive house consultant: Gresford Architects
Initial architect (planning): Nicholas Tye Architects
Project manager: Mike Jacob
Timber frame manufacturer: MBC Timber Frame
Passive house certifier: WARM Low Energy Building Practice
Structural engineering: Tanner Structural Design Ltd (sub-structure); Peter de Lacy Staunton (super structure); Cubic Building Surveying Ltd (additional structure)
Plumbing & heating: Solinvictus
MVHR design: Williams Energy Design
MVHR supply & install: Touchwood
Electrical contractor: Nightingale Electrical
Window supplier & installer: Ecohaus Internorm
Roof windows: LAMILUX UK Ltd
Insulated foundation system: KORE
Blown cellulose insulation: Warmcel, via PYC
Airtightness products: Ecological Building Systems / Partel / Medite Smartply
Solar evacuated tubes: The Small Solar Company
Rainwater harvesting: Rainwater Harvesting
Solar PV inverter: Solinvictus
Wood burning stove: Kamdi24.de
Airtight cat flap: Petwalk
Low VOC paint: Eico
Cladding: Husker Ltd
Drainage: Crofton Design Ltd
Flooring: Sutton Timber
Landscaping: Armstrong Landscapes
In detail
Building type: Detached 5-bedroom timber frame house. Gross internal area 400 sqm.
Location: Harpenden, Hertfordshire
Completion date: October 2017
Budget: Private
Passive house certification: Certified
Space heating demand (PHPP): 12.0 kWh/m2/yr
Heat load (PHPP): 9 W/m2
Primary energy demand (non-renewable, PHPP): 45 kWh/m2/yr
Primary energy renewable demand (PER, PHPP): 37 kWh/m2/yr
Heat loss form factor (PHPP): 2.81
Overheating (PHPP): 2%
Airtightness (at 50 Pascals): 0.51 ACH
Energy performance certificate (EPC): A (97)
Measured energy consumption: In first 12 months, an estimated 2m3 of wood and 82m3 of gas (914kWh) consumed for space & water heating.
Thermal bridging: MBC timber frame system with accredited detail Psi-values; average Psi-value produced by structural steel within superstructure: 0.068 W/mK; chimney Psi-value 0.370 W/mK; stove sporadic operation Psi-value 2.645 W/mK; SVP Psi-value 0.303 W/mK. Total Thermal Bridges account: for 2.7 kWh/m2
Energy bills (measured or estimated): During his first 12 months in the house, Danny Luhde Thompson paid £38 for 82m3 of gas, plus £94 in standing charges. However, from his monitoring he estimates that almost all of this spend was for hot water. He says: “All the [space] heating was really from solar gain, people, four cats and the stove. As well as heating the heat store (6kW), the stove gives some heat (2kW) to the room, and the general ventilation seemed to propagate this around the house nicely.” All wood used for the stove was left over from siteworks. Ground floor: 400mm KORE Floor EPS100 white insulation (EPS300 to perimeter) under 100mm reinforced concrete slab, 4mm concrete screed and 18mm timber floor finish. U-value: 0.092 W/m2K
Walls: 20mm sweet chestnut timber cladding externally, followed inside by 150mm rainscreen cavity formed with timber battens, Solitex Fronta WA monolithic wind tight breather membrane, 12mm Medite vent MDF sheathing panel, 400mm twin timber stud wall formed with 38x89mm studs at 400 c/c fulfilled with Warmcel insulation (thermal conductivity at 0.038 W/m2K), 12.5mm SmartPly ProPassiv board, 45x45mm battens to form service void, 12.5mm Plasterboard, 3mm painted skim. U-value: 0.107 W/m2K
Sarnafil G 410-18EL felt (1.8mm) externally fully bonded to 18mm plywood, followed underneath by 50x50mm ventilated timber battens and timber firrings fixed through to joists, Ampatop Protecta Plus roof membrane, 15mm Smartply OSB, 400mm I-Beam timber joists at 400mm c/c fully insulated with Warmcel insulation (thermal conductivity at 0.038 W/m2K), ProClima Intello Plus vapour control layer, 200x50mm timber battens to form ceiling void, 12.5mm plasterboard, 3mm painted skim. U-value: 0.096 W/m2K
Terrace: 20mm external floor finish, followed underneath by plastic pedestal, Sarnafil protection sheet, Sarnafil G 410-18EL Felt (1.8mm) fully bonded to 18mm plywood, 95x50mm ventilated timber battens and timber firrings fixed through to joists, Solitex Weldano roof membrane, 15mm Smartply OSB, 300mm I-Beam timber joists at 400mm c/c fully insulated with Warmcel insulation (thermal conductivity at 0.038 W/m2K), ProClima Intello Plus vapour control layer, 100x45mm timber battens to form ceiling void, 12.5mm plasterboard, 3mm painted skim. U-value 0.130 W/m2K
Windows, external doors, patio doors: Internorm HF310 passive house certified timber-aluminium window. Average window U-value 0.83 Wm2K. Average g-value 0.45. Internorm HF310 Door, HS330 sliding door and AT410 front door.
Roof window: Lamilux FE Energysave. Passive House Institute certified. Overall U-value: 0.84 W/m2K
Heating system: Rokossa IG2 RLU log boiler stove. 90 tube solar evacuated tube array with Resol differential controller. Worcester Greenstar 24Ri gas boiler (24kW), All supplying 500 litre Energystore Biosolar heat store which in turn supplies underfloor heating, towel rails to upstairs bathrooms, a duct heater in in the supply of fresh air upstairs. Heatstore also supplying domestic hot water
Ventilation: Paul Novus 450 with summer bypass and electric defroster. Lindab ductwork. Roof window motorised, Lindab ductwork. Motorised roof window for extra ventilation.
Water: F Line 7,500 litre tank collecting rainwater used for toilets and garden watering. External blinds: Roma Quadro 130 S Motorised External blind system. Reduction factor for temporary sun protection at 24%.
Green materials: FSC certified sweet chestnut cladding, ash floor & ceiling, Warmcel cellulose insulation, EICO paints, timber frame structure.
Image gallery
-
Proposed window jambs and external blind detail Proposed window jambs and external blind detail
-
Proposed slab - wall detail Proposed slab - wall detail
-
Proposed wall intermediate floor detail Proposed wall intermediate floor detail
-
Proposed flat roof - eaves detail Proposed flat roof - eaves detail
-
Proposed intermediate floor - floor above garage junction Proposed intermediate floor - floor above garage junction
-
Proposed eaves details Proposed eaves details
-
Proposed terrace floor to side wall junction detail Proposed terrace floor to side wall junction detail
-
Proposed terrace floor to wall junction detail Proposed terrace floor to wall junction detail
-
East elevation East elevation
-
First floor ground plan First floor ground plan
-
Ground floor plan Ground floor plan
-
Roof plan Roof plan
-
Section AA Section AA
-
Section BB Section BB
-
Section CC Section CC
-
Section DD Section DD
-
Section EE Section EE
-
West elevation West elevation
-
Cold snap Cold snap
-
Heat wave Heat wave
-
Wall temp humidity Wall temp humidity
https://mail.passive.ie/magazine/new-build/wood-works-sleek-but-large-herts-passive-house-goes-heavy-on-timber#sigProIdf06bf9dfea